- お役立ち記事
- The difference between Surface Grinding and Internal Grinding
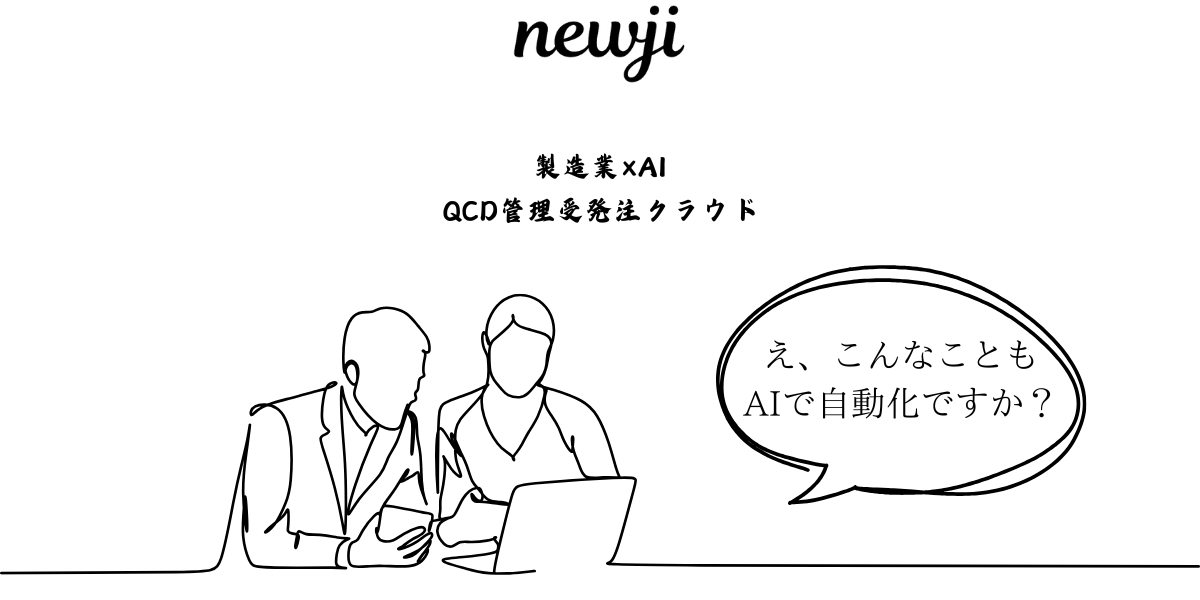
The difference between Surface Grinding and Internal Grinding
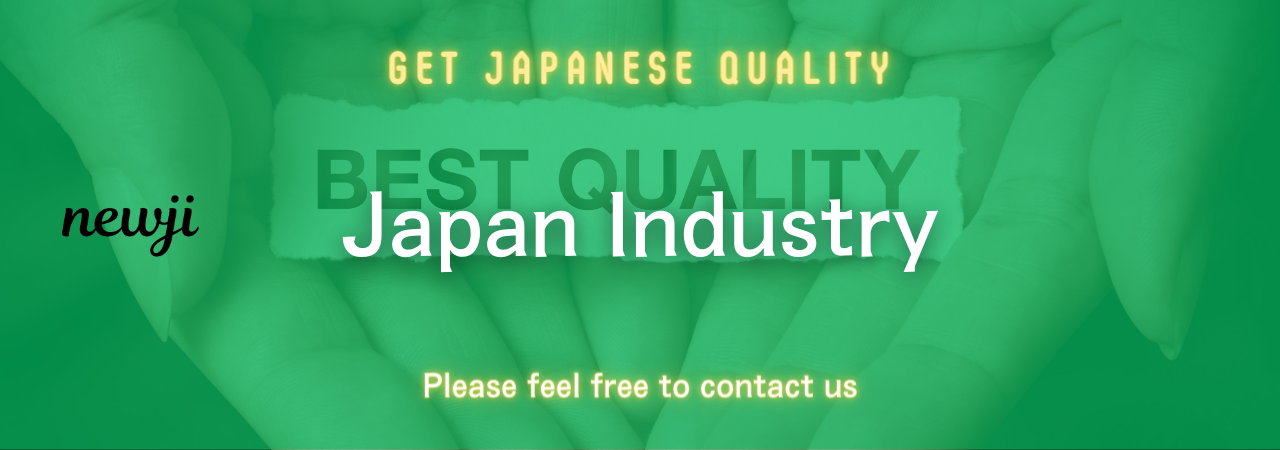
When it comes to precision machining, grinding techniques play a crucial role in ensuring that materials meet specific design requirements.
Among the many grinding methods available, surface grinding and internal grinding stand out due to their distinct processes and applications.
Understanding the differences between these two techniques can help manufacturers and engineers select the most suitable method for their projects.
目次
What is Surface Grinding?
Surface grinding is a process that involves grinding the surface of a workpiece to make it smooth and flat.
This technique utilizes a spinning abrasive wheel to remove small chips of material from the surface, ensuring a high level of precision.
The workpiece is typically held in place by a magnetic chuck or a special fixture.
The grinding wheel rotates at high speed, and as it moves across the surface, it removes tiny amounts of material to achieve the desired finish.
Applications of Surface Grinding
Surface grinding is widely used in various industries for its ability to produce precise and flat surfaces.
It’s commonly employed in the manufacturing of tools and dies, flat panels, gears, piston rings, and many other components that require a high level of accuracy.
This method is particularly useful when a smooth finish and tight tolerances are essential.
What is Internal Grinding?
Internal grinding, on the other hand, focuses on grinding the internal surfaces of a workpiece.
Unlike surface grinding, which targets the exterior, internal grinding aims to improve the interior surfaces to meet specific dimensional and finish requirements.
In this process, a small grinding wheel is used, and it moves inside the workpiece to remove excess material and achieve the desired internal dimensions.
Applications of Internal Grinding
Internal grinding is crucial in applications where internal surfaces must meet exact specifications.
This is often seen in industries like automotive, aerospace, and tooling, where components such as bearings, gears, and bushings require precise internal dimensions.
By employing internal grinding, manufacturers can ensure the components have the right fit and function as intended.
Key Differences Between Surface Grinding and Internal Grinding
1. Workpiece Positioning
In surface grinding, the workpiece is positioned on a table or a magnetic chuck, and the grinding wheel moves across its surface.
This setup is straightforward and ideal for flat surfaces.
In internal grinding, the workpiece is usually clamped in a chuck or mounted on a spindle, and the grinding wheel moves inside the workpiece.
This setup is more complex and is designed for internal surfaces.
2. Grinding Wheel Orientation
In surface grinding, the grinding wheel is positioned above or beside the workpiece, moving horizontally or perpendicularly.
This configuration ensures the surface is ground evenly.
In internal grinding, the grinding wheel is mounted on a spindle that extends into the workpiece.
It operates in a radial motion, targeting only the internal surfaces.
3. Material Removal
Surface grinding aims to remove a thin layer of material from a broad surface to achieve a smooth finish.
This technique is ideal for producing flat surfaces with high accuracy.
Internal grinding, on the other hand, focuses on removing material from the inside of a workpiece.
This process ensures the internal dimensions and finishes meet precise specifications.
4. Complexity and Precision
Surface grinding is generally less complex and can achieve high precision but primarily on flat surfaces.
It’s a versatile technique suitable for many applications.
Internal grinding is more complex due to the intricate setup and the need to grind internal surfaces accurately.
This technique is essential when internal dimensions are critical and requires higher precision machinery.
Choosing the Right Technique
Selecting between surface grinding and internal grinding depends on the specific requirements of the project.
If the goal is to achieve a flat and smooth exterior surface with tight tolerances, surface grinding is the preferred method.
It excels in producing high-precision flat surfaces and is cost-effective for these applications.
However, if the project requires precise internal dimensions and high-quality interior finishes, internal grinding is indispensable.
This technique ensures the internal surfaces comply with strict specifications, a necessity in many high-precision industries.
Advancements in Grinding Technology
With advancements in grinding technology, both surface grinding and internal grinding have seen significant improvements.
Modern grinding machines are equipped with advanced features like CNC controls, automatic wheel dressing, and high-speed spindles.
These enhancements have increased the precision, efficiency, and versatility of grinding processes, allowing manufacturers to achieve better results in less time.
Integration with Other Processes
To further enhance manufacturing capabilities, surface grinding and internal grinding can be integrated with other processes like milling, turning, and EDM.
This integration allows for a more seamless and efficient production flow, saving time and reducing costs.
Conclusion
Understanding the differences between surface grinding and internal grinding is essential for selecting the right machining process.
While surface grinding focuses on achieving smooth and flat exterior surfaces, internal grinding is crucial for precise internal dimensions.
By choosing the appropriate technique, manufacturers can ensure their components meet the desired specifications and function correctly in their applications.
Advancements in grinding technology continue to enhance these processes, offering even greater precision and efficiency in the manufacturing world.
資料ダウンロード
QCD調達購買管理クラウド「newji」は、調達購買部門で必要なQCD管理全てを備えた、現場特化型兼クラウド型の今世紀最高の購買管理システムとなります。
ユーザー登録
調達購買業務の効率化だけでなく、システムを導入することで、コスト削減や製品・資材のステータス可視化のほか、属人化していた購買情報の共有化による内部不正防止や統制にも役立ちます。
NEWJI DX
製造業に特化したデジタルトランスフォーメーション(DX)の実現を目指す請負開発型のコンサルティングサービスです。AI、iPaaS、および先端の技術を駆使して、製造プロセスの効率化、業務効率化、チームワーク強化、コスト削減、品質向上を実現します。このサービスは、製造業の課題を深く理解し、それに対する最適なデジタルソリューションを提供することで、企業が持続的な成長とイノベーションを達成できるようサポートします。
オンライン講座
製造業、主に購買・調達部門にお勤めの方々に向けた情報を配信しております。
新任の方やベテランの方、管理職を対象とした幅広いコンテンツをご用意しております。
お問い合わせ
コストダウンが利益に直結する術だと理解していても、なかなか前に進めることができない状況。そんな時は、newjiのコストダウン自動化機能で大きく利益貢献しよう!
(Β版非公開)