- お役立ち記事
- The difference between Wire Cutting and Electrical Discharge Machining (EDM)
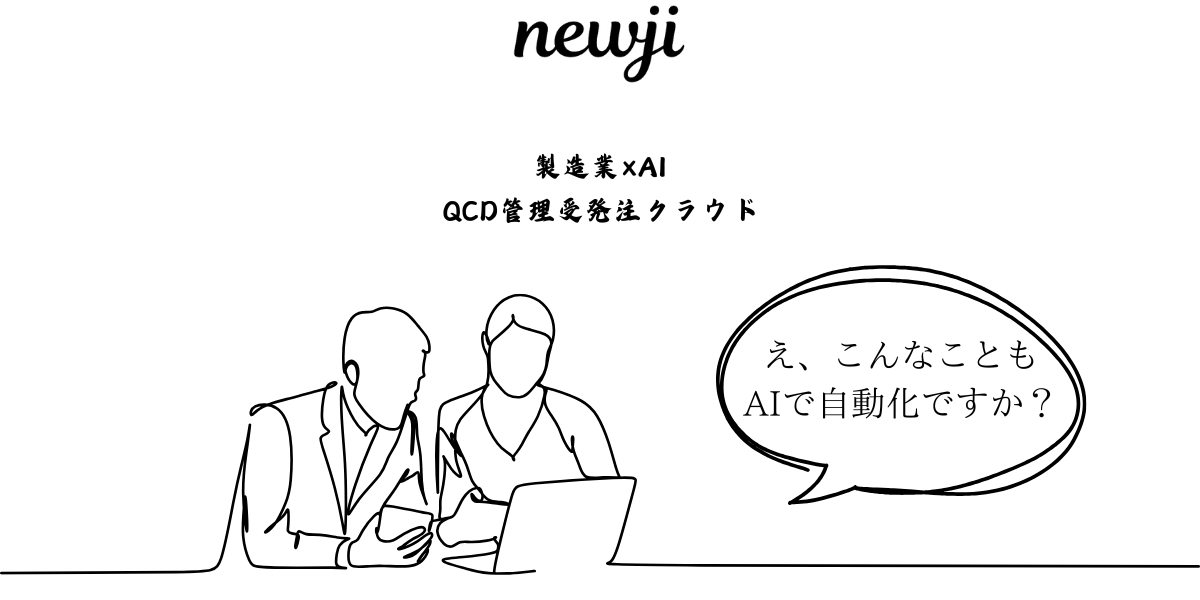
The difference between Wire Cutting and Electrical Discharge Machining (EDM)
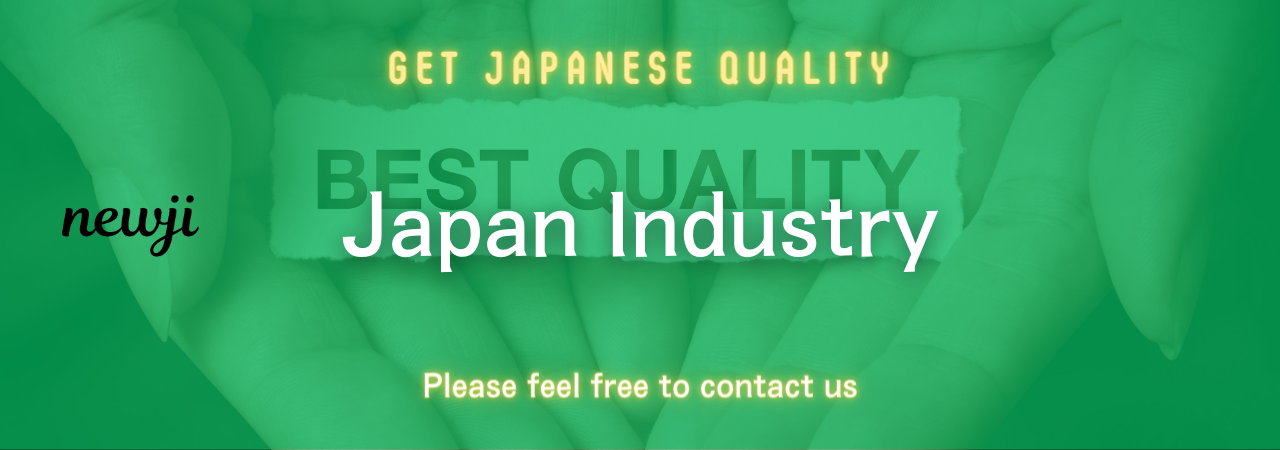
When it comes to precision machining, industries are always on the lookout for tools and techniques that can deliver fine results.
Wire cutting and Electrical Discharge Machining (EDM) are two such methods that often come up in discussions about high-accuracy cutting processes.
Even though they both serve similar purposes, these methods are distinct in their approaches, applications, and outcomes.
Understanding the key differences between wire cutting and EDM can help you decide which technique is most suitable for your specific needs.
目次
What is Wire Cutting?
Wire cutting, also known as wire electrical discharge machining (Wire EDM), is a method that uses a wire to cut through materials.
The wire itself doesn’t actually touch the material being cut; instead, it discharges electrical sparks that erode the material.
This allows for high precision and is particularly useful for cutting hard metals that traditional machining methods might struggle with.
Wire cutting is particularly good for creating intricate shapes and contours.
It is widely used in industries such as aerospace, automotive, and tool manufacturing because it can produce highly accurate parts.
The method is typically used when a high level of detail is required, such as for making molds, dies, and complex components.
What is Electrical Discharge Machining (EDM)?
Electrical Discharge Machining, commonly known as EDM, is a broader category of machining that includes various processes for removing material through electrical discharges.
Wire cutting is actually a type of EDM, but there are other forms such as die-sinking EDM and hole drilling EDM.
Each type has its own specific applications and is suited for different kinds of tasks.
In traditional or die-sinking EDM, an electrode and the workpiece are submerged in a dielectric fluid.
An electrical discharge passes between the electrode and the workpiece, creating a plasma channel and eroding the material.
This method is especially useful for creating complex shapes and fine details in hard materials like titanium and hardened steel.
Key Differences Between Wire Cutting and EDM
Material Considerations
One of the primary differences between wire cutting and other types of EDM is the type of materials they can handle.
Wire cutting is excellent for hard materials and thin components, often dealing with metals like tungsten, titanium, and hardened tool steels.
On the other hand, die-sinking EDM can handle a broader range of materials, including softer metals and alloys.
Precision and Accuracy
Wire cutting excels in precision and accuracy.
The method can achieve extremely tight tolerances, often in the range of a few micrometers.
This makes it ideal for producing intricate components with high-quality finishes.
Die-sinking EDM is also highly accurate but may not achieve the same level of precision as wire cutting.
Speed and Efficiency
When it comes to speed, die-sinking EDM tends to be faster than wire cutting, especially when dealing with large volumes of material.
However, the improved speed often comes at a slight compromise in precision.
Wire cutting, while slower, delivers highly detailed cuts.
Therefore, the choice between the two often depends on whether precision or speed is the priority for the project.
Complexity and Shape
Wire cutting is specialized for producing complex shapes, contours, and fine details.
It’s often chosen for tasks that require intricate geometries or patterns.
Die-sinking EDM, on the other hand, is better suited for more straightforward shapes but can produce deep, intricate cavities in hard materials.
Applications of Wire Cutting and EDM
Wire Cutting Applications
Wire cutting is predominantly used in the tool and die industry for creating molds and templates.
It’s also used in the aerospace industry for making components that require high precision and in the medical industry for parts like surgical instruments and implants.
EDM Applications
Die-sinking EDM is commonly used for making injection molds, die-casting molds, and complex parts in the automotive and aerospace industries.
Its ability to form intricate cavities makes it ideal for manufacturing parts like turbine blades and engine components.
Hole drilling EDM is often employed for creating micro-holes in materials, useful for applications like fuel injector nozzles and cooling holes in turbine blades.
Advantages and Disadvantages
Advantages of Wire Cutting
Wire cutting offers high precision and can cut intricate shapes with tight tolerances.
It also allows for minimal material wastage and produces a smooth surface finish.
Additionally, it can cut hard materials, which might be challenging for other machining methods.
Disadvantages of Wire Cutting
The primary drawback of wire cutting is its slower speed compared to other machining methods.
Moreover, it can be expensive due to the cost of specialized wire and the need for a dielectric fluid to facilitate the cutting process.
Advantages of EDM
EDM can handle a broad range of materials and is highly efficient in producing complex shapes.
It also offers high accuracy and minimal mechanical stress on the workpiece.
Additionally, it can produce excellent surface finishes that often require little to no additional machining.
Disadvantages of EDM
Like wire cutting, EDM can be costly because of the need for specific electrodes and dielectric fluids.
It may also produce a heat-affected zone, though this is generally minimal and can be managed with proper settings and techniques.
Understanding the differences between wire cutting and EDM is crucial for selecting the right machining method for your project.
While both offer high precision and can handle complex shapes, they differ in speed, material capabilities, and specific applications.
By comprehensively evaluating your needs and the pros and cons of each method, you can make an informed decision that will lead to successful and efficient machining outcomes.
資料ダウンロード
QCD調達購買管理クラウド「newji」は、調達購買部門で必要なQCD管理全てを備えた、現場特化型兼クラウド型の今世紀最高の購買管理システムとなります。
ユーザー登録
調達購買業務の効率化だけでなく、システムを導入することで、コスト削減や製品・資材のステータス可視化のほか、属人化していた購買情報の共有化による内部不正防止や統制にも役立ちます。
NEWJI DX
製造業に特化したデジタルトランスフォーメーション(DX)の実現を目指す請負開発型のコンサルティングサービスです。AI、iPaaS、および先端の技術を駆使して、製造プロセスの効率化、業務効率化、チームワーク強化、コスト削減、品質向上を実現します。このサービスは、製造業の課題を深く理解し、それに対する最適なデジタルソリューションを提供することで、企業が持続的な成長とイノベーションを達成できるようサポートします。
オンライン講座
製造業、主に購買・調達部門にお勤めの方々に向けた情報を配信しております。
新任の方やベテランの方、管理職を対象とした幅広いコンテンツをご用意しております。
お問い合わせ
コストダウンが利益に直結する術だと理解していても、なかなか前に進めることができない状況。そんな時は、newjiのコストダウン自動化機能で大きく利益貢献しよう!
(Β版非公開)