- お役立ち記事
- The importance of “quality evaluation standards”—Standards set by management and how to apply them in the field
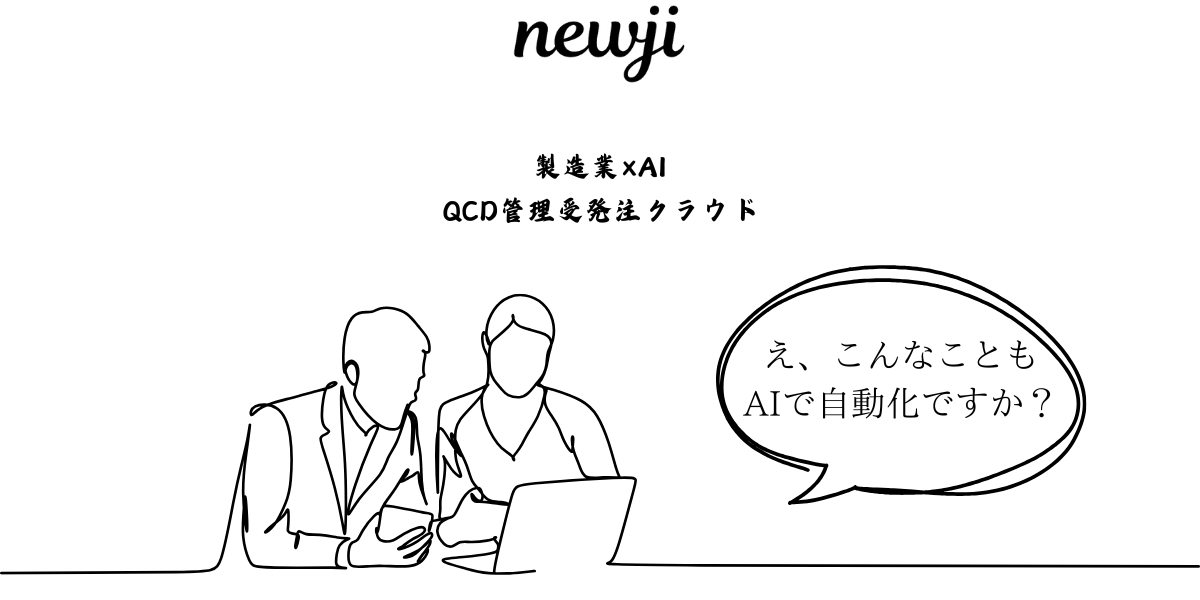
The importance of “quality evaluation standards”—Standards set by management and how to apply them in the field
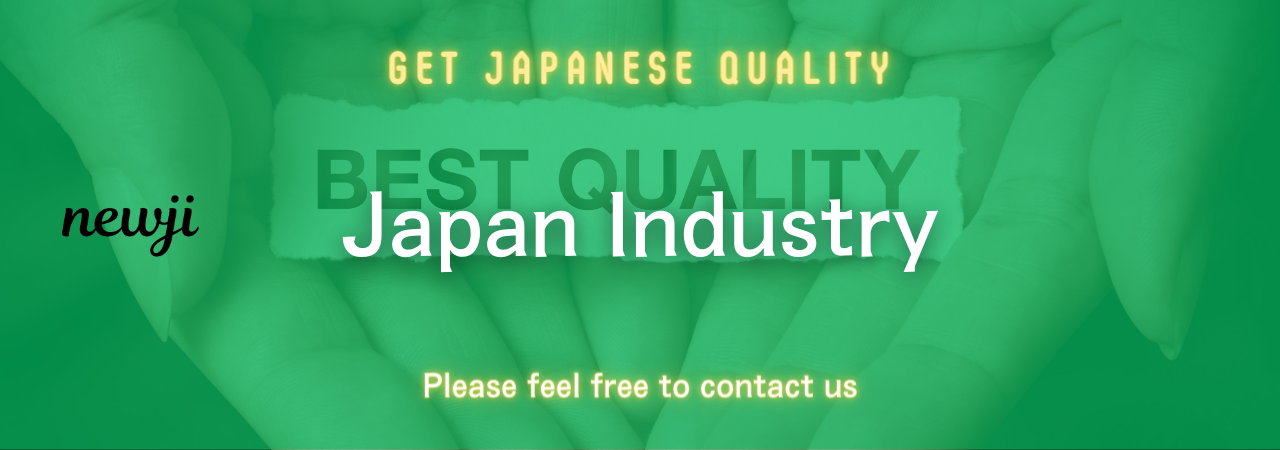
目次
Introduction to Quality Evaluation Standards
Quality evaluation standards are essential benchmarks set by management to ensure products and services meet desired expectations.
These standards serve as a guideline for assessing the quality of a company’s output, ensuring customer satisfaction, and maintaining a competitive edge.
They range from customer feedback to internal processes designed to monitor and improve service delivery.
Understanding and implementing these standards in the field is crucial for any organization aiming to achieve excellence.
Why Quality Evaluation Standards Matter
Quality evaluation standards play a pivotal role in enhancing the overall performance of an organization.
By establishing clear criteria, businesses can consistently measure quality, identify areas of improvement, and drive ongoing innovation.
These standards also act as a communication tool, aligning the mission and vision of the company with day-to-day operations.
Moreover, they help organizations stay compliant with industry regulations, minimizing risks and avoiding costly errors.
Consistency in quality is a significant competitive advantage, and companies that adhere to high-quality evaluation standards often see increased sales, customer loyalty, and market reputation.
Setting Effective Quality Evaluation Standards
It is vital for management to set clear, attainable, and relevant quality evaluation standards.
These should align with the company’s strategic goals and be directly linked to business outcomes.
Key considerations when setting these standards include:
1. **Customer Expectations**: Understanding what customers expect from your products or services is fundamental.
This involves regular market research and feedback collection to tailor quality criteria accordingly.
2. **Regulatory Requirements**: Compliance with local, national, and international regulations is non-negotiable.
Ensure standards are aligned with these legal requirements to avoid potential sanctions.
3. **Resource Availability**: Evaluate existing resources, including technology, manpower, and budget, when setting quality standards.
This ensures that set standards are sustainable.
4. **Continuous Improvement**: The business environment is dynamic.
Thus, quality evaluation standards should be flexible enough to evolve, incorporating lessons from past performances.
5. **Measurable Metrics**: Identify clear metrics that allow you to quantify quality.
This makes it easier to monitor, collect data, and analyze progress.
Application of Quality Evaluation Standards in the Field
The successful application of quality evaluation standards in the field requires a structured approach.
Here are key strategies to effectively implement these standards:
1. **Educating and Training Employees**: Employees should be thoroughly trained on the importance of quality evaluation standards.
This training should cover how to apply these standards in their respective roles.
Regular workshops and refresher courses can reinforce this knowledge.
2. **Integrating Quality into Business Processes**: Quality standards should be an integral part of the organization’s operational framework.
This means embedding them within daily processes, ensuring they are not viewed as an afterthought.
3. **Utilizing Technology**: Leverage automation and advanced analytics tools to monitor and enforce quality standards.
Technology can enhance precision and efficiency in quality assessment.
4. **Regular Auditing and Feedback**: Conduct regular audits to assess compliance with the set standards.
Utilize this information to provide constructive feedback and make necessary adjustments.
5. **Encouraging a Culture of Quality**: Instill a culture that values quality at every level of the organization.
Encourage employees to take ownership and pride in maintaining high standards.
Challenges in Implementing Quality Evaluation Standards
While quality evaluation standards are crucial, implementing them comes with its set of challenges.
These include:
1. **Resistance to Change**: Employees may resist new standards due to a lack of understanding or fear of increased workload.
Management must address these concerns through transparent communication and involvement.
2. **Resource Constraints**: Financial or technological limitations can impede the establishment of stringent quality standards.
It is essential for management to prioritize and gradually integrate standards based on available resources.
3. **Complexity in Measurement**: Some qualitative aspects may be challenging to measure.
Developing comprehensive metrics requires creativity and strategic foresight.
4. **Maintaining Consistency**: Sustaining high-quality standards demands ongoing commitment.
This can be difficult, especially in large organizations with diverse operations.
Conclusion
Quality evaluation standards are a cornerstone of excellence in any organization.
By setting and applying these standards effectively, businesses can ensure consistent quality, enhance customer satisfaction, and maintain regulatory compliance.
While the journey of implementing these standards is not without challenges, the benefits immensely outweigh the efforts involved.
Organizations that prioritize quality are not only well-equipped to respond to market demands but are also poised for long-term success.
It’s vital for management to support and uphold these standards, fostering an environment where each member of the organization contributes to a culture centered on quality.
資料ダウンロード
QCD調達購買管理クラウド「newji」は、調達購買部門で必要なQCD管理全てを備えた、現場特化型兼クラウド型の今世紀最高の購買管理システムとなります。
ユーザー登録
調達購買業務の効率化だけでなく、システムを導入することで、コスト削減や製品・資材のステータス可視化のほか、属人化していた購買情報の共有化による内部不正防止や統制にも役立ちます。
NEWJI DX
製造業に特化したデジタルトランスフォーメーション(DX)の実現を目指す請負開発型のコンサルティングサービスです。AI、iPaaS、および先端の技術を駆使して、製造プロセスの効率化、業務効率化、チームワーク強化、コスト削減、品質向上を実現します。このサービスは、製造業の課題を深く理解し、それに対する最適なデジタルソリューションを提供することで、企業が持続的な成長とイノベーションを達成できるようサポートします。
オンライン講座
製造業、主に購買・調達部門にお勤めの方々に向けた情報を配信しております。
新任の方やベテランの方、管理職を対象とした幅広いコンテンツをご用意しております。
お問い合わせ
コストダウンが利益に直結する術だと理解していても、なかなか前に進めることができない状況。そんな時は、newjiのコストダウン自動化機能で大きく利益貢献しよう!
(Β版非公開)