- お役立ち記事
- The Manufacturing Process for Band-Aids and Strengthening Adhesion
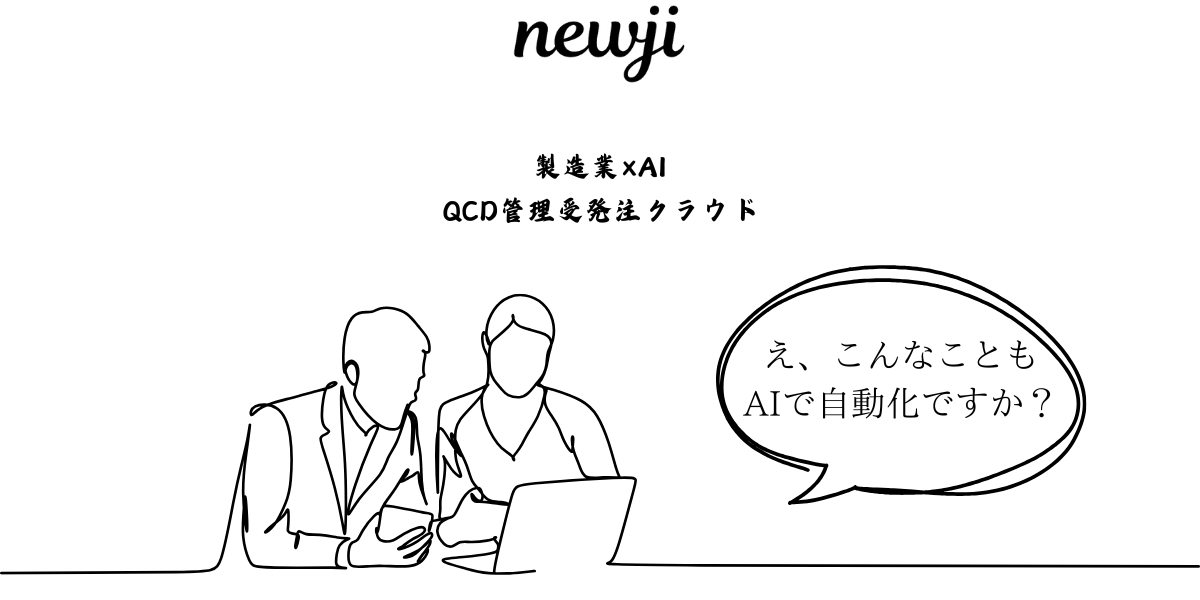
The Manufacturing Process for Band-Aids and Strengthening Adhesion
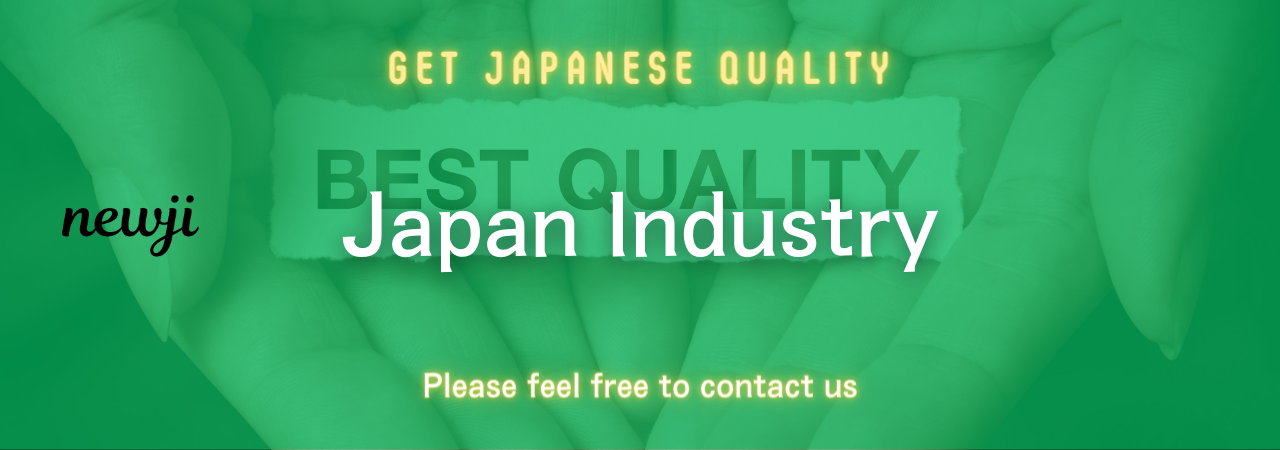
The Band-Aid is one of those everyday items we often take for granted but play a crucial role in our lives.
When you get a small cut or scrape, a Band-Aid can cover and protect it from dirt and germs.
Let’s dive into the fascinating process of how Band-Aids are made and how manufacturers ensure they stick well to the skin.
目次
Materials Needed to Make Band-Aids
Before diving into the manufacturing process, it’s essential to know the materials used in making Band-Aids.
Every Band-Aid consists of three primary components: the adhesive, the backing, and the pad.
Adhesive
The adhesive is the sticky part of the Band-Aid that ensures it stays in place on your skin.
It’s usually made from a combination of rubber-based or acrylic adhesives.
These adhesives are chosen for their excellent stickiness and durability.
Backing
The backing is the material that holds the adhesive and the pad.
It can be made from fabric, plastic, or a flexible material like polyurethane.
The type of backing used can affect the Band-Aid’s flexibility and comfort.
Pad
The pad is the soft, absorbent part that goes directly over the wound.
It’s usually made from a sterile gauze or cotton.
Some pads are treated with an antiseptic to help prevent infection.
The Manufacturing Process
Now that we know what Band-Aids are made of, let’s look at how they are manufactured.
The process involves multiple steps to ensure that each Band-Aid is safe, effective, and high-quality.
Step 1: Preparing the Adhesive
The first step involves preparing the adhesive.
Manufacturers mix the raw materials, such as rubber or acrylic, with other ingredients to make a sticky solution.
This mixture is then heated to ensure all components are thoroughly blended.
Step 2: Coating the Backing
Next, the adhesive is applied to the backing material.
This is done using large rollers that evenly coat the backing with the adhesive solution.
Once coated, the backing goes through a drying tunnel to ensure the adhesive is set and ready for the next steps.
Step 3: Adding the Pad
A machine then places small, pre-cut pads onto the adhesive-coated backing.
These pads are carefully positioned to ensure they are centered and securely attached.
The pads are often treated with antiseptics if required.
Step 4: Cutting and Shaping
Once the pads are in place, the backing material is cut into individual Band-Aids of various shapes and sizes.
Manufacturers often use a die-cutting machine for this purpose.
The precise cutting ensures that each Band-Aid is the right size and shape.
Step 5: Sterilization
After cutting, the Band-Aids undergo a sterilization process.
This is crucial for ensuring that the Band-Aids are free from any bacteria or germs.
Many manufacturers use heat or radiation to sterilize the Band-Aids effectively.
Step 6: Packaging
Finally, the Band-Aids are individually wrapped and packaged.
This is usually done in a sterile environment to maintain their cleanliness.
The wrapped Band-Aids are then placed in boxes or other packaging materials, ready for shipment to stores.
Strengthening Adhesion
One of the most important features of a Band-Aid is its ability to stick well to the skin.
Manufacturers use several techniques to ensure strong adhesion.
Improving Adhesive Formulation
Adhesive formulation is a critical factor.
Manufacturers continually research and test different combinations of materials to find the most effective adhesive.
Some adhesives are designed to be more sticky, while others are made to be more skin-friendly.
Patterned Adhesive Application
Instead of applying the adhesive as a solid layer, some manufacturers use a patterned application.
This helps the Band-Aid adhere better by creating a more effective bond with the skin.
The patterns allow for flexibility, which helps the Band-Aid stay on even if you are moving around.
Testing for Durability
Before reaching consumers, Band-Aids go through rigorous testing to ensure they meet high standards.
Manufacturers test for factors like how well the Band-Aid sticks, how long it stays in place, and how it reacts to different skin types.
This helps them create a product that is reliable and effective.
Conclusion
The manufacturing process for Band-Aids is complex and involves many steps.
From preparing the adhesive to cutting and sterilizing, each step is essential for creating a high-quality product.
Manufacturers constantly strive to improve the adhesion and overall effectiveness of Band-Aids, ensuring they provide the best care for minor injuries.
So the next time you reach for a Band-Aid, you’ll know just how much effort goes into making this simple yet vital item.
資料ダウンロード
QCD調達購買管理クラウド「newji」は、調達購買部門で必要なQCD管理全てを備えた、現場特化型兼クラウド型の今世紀最高の購買管理システムとなります。
ユーザー登録
調達購買業務の効率化だけでなく、システムを導入することで、コスト削減や製品・資材のステータス可視化のほか、属人化していた購買情報の共有化による内部不正防止や統制にも役立ちます。
NEWJI DX
製造業に特化したデジタルトランスフォーメーション(DX)の実現を目指す請負開発型のコンサルティングサービスです。AI、iPaaS、および先端の技術を駆使して、製造プロセスの効率化、業務効率化、チームワーク強化、コスト削減、品質向上を実現します。このサービスは、製造業の課題を深く理解し、それに対する最適なデジタルソリューションを提供することで、企業が持続的な成長とイノベーションを達成できるようサポートします。
オンライン講座
製造業、主に購買・調達部門にお勤めの方々に向けた情報を配信しております。
新任の方やベテランの方、管理職を対象とした幅広いコンテンツをご用意しております。
お問い合わせ
コストダウンが利益に直結する術だと理解していても、なかなか前に進めることができない状況。そんな時は、newjiのコストダウン自動化機能で大きく利益貢献しよう!
(Β版非公開)