- お役立ち記事
- Thorough Silicon Valley leak testing techniques that mid-level employees in the quality assurance department of the medical device manufacturing industry should know
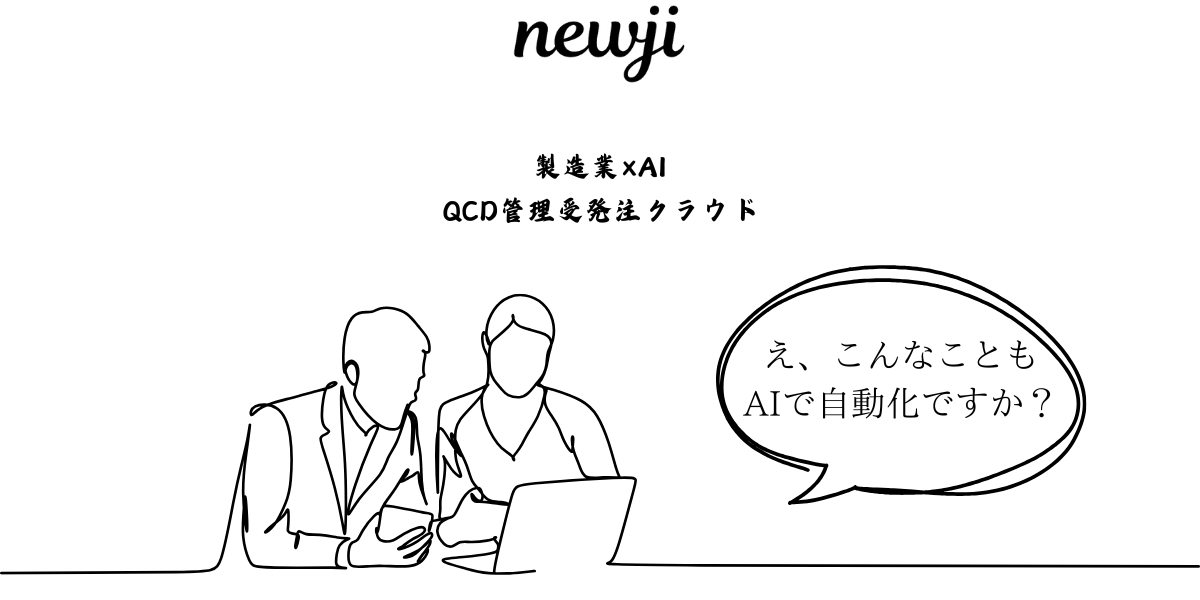
Thorough Silicon Valley leak testing techniques that mid-level employees in the quality assurance department of the medical device manufacturing industry should know
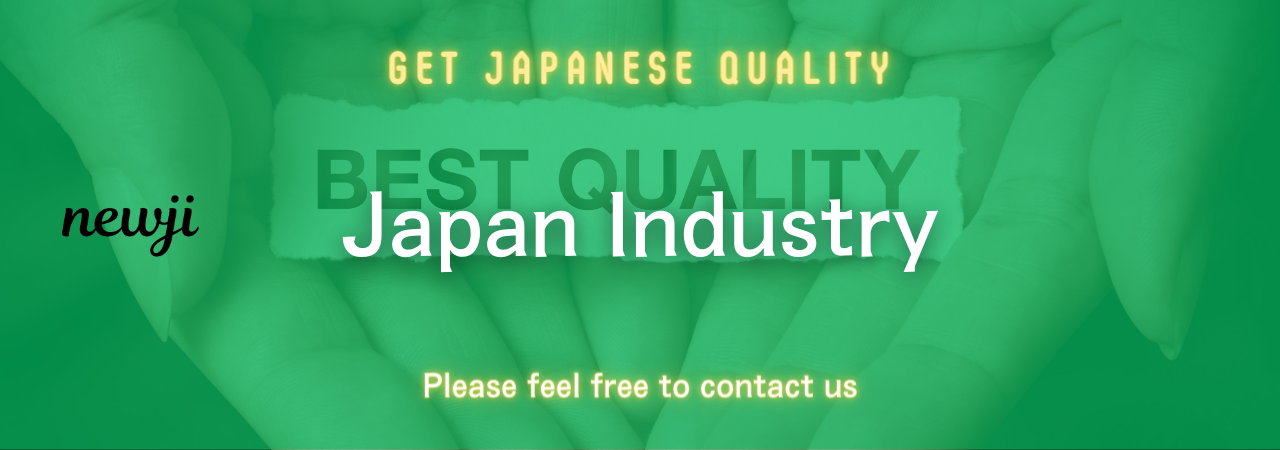
Understanding Leak Testing in Silicon Valley
Leak testing is a critical process, especially in high-stakes industries like medical device manufacturing.
In Silicon Valley, where innovation and precision go hand in hand, understanding advanced leak testing methods is essential.
Mid-level employees in the quality assurance department need to be well-versed in these testing techniques to ensure product integrity and safety.
The Importance of Leak Testing in Medical Devices
Medical devices must adhere to stringent safety standards.
A small leak can result in device malfunction, leading to severe health implications for patients.
Therefore, having thorough leak testing protocols in place ensures devices are both reliable and safe.
Leak testing helps in identifying potential vulnerabilities in products before they reach the market, safeguarding the manufacturers against recalls and potential lawsuits.
Key Leak Testing Techniques
Silicon Valley boasts a myriad of advanced leak testing techniques.
Understanding these methods allows quality assurance teams to choose the most appropriate one for their specific application.
1. Bubble Emission Testing
One of the simplest and oldest leak testing methods is bubble emission testing.
This process involves submerging a device in water and observing for air bubbles.
While straightforward, it is mostly used for larger leaks and is not suitable for high-precision applications required in medical devices.
2. Pressure Decay Testing
Pressure decay testing is more advanced and involves pressurizing a part and measuring any drop in pressure over time.
This method is popular in Silicon Valley for its accuracy and ability to detect minute leaks.
It is particularly useful for ensuring the integrity of sealed components in medical devices.
3. Vacuum Decay Testing
This technique is similar to pressure decay testing but works in reverse.
A vacuum is applied to the tested component, and any increase in pressure indicates a leak.
This method is highly sensitive and ideal for testing products that need to maintain a sterile or contaminant-free environment.
4. Helium Mass Spectrometry
Helium mass spectrometry is among the most sophisticated leak detection methods available.
It involves the use of helium as a tracer gas and a mass spectrometer to detect leaks.
Given its high sensitivity, it can detect incredibly small leaks, making it an excellent choice for critical components in medical devices.
5. Ultrasonic Leak Detection
This method detects high-frequency sound waves produced by escaping gases or liquids.
Ultrasonic leak detection is non-invasive and can be used to test devices under operational conditions.
This makes it an attractive option for dynamic leak testing in medical devices.
Implementing Leak Testing Protocols
To integrate these methods effectively, it’s crucial to have a structured approach.
Begin by understanding the specific requirements of your medical device.
Consider factors such as the type of material, the expected use of the device, and regulatory standards.
Develop a testing protocol that includes multiple methods to address different types of leaks.
It ensures a comprehensive evaluation, minimizing potential issues post-production.
Continuous Training and Education
Technology in Silicon Valley evolves rapidly, bringing about new testing methods and tools.
Mid-level employees should participate in continuous training to stay updated with the latest leak detection technologies.
Workshops, seminars, and certification courses can be excellent platforms for gaining this knowledge and improving one’s skill set.
Monitoring and Quality Assurance
Effective leak testing doesn’t stop at implementation.
Continuous monitoring and quality adjustments are essential to maintaining high standards.
Use data collected from leak tests to improve processes and address recurring issues.
Collaborate with the manufacturing team to integrate real-time feedback into production processes, ensuring high-quality production runs.
Challenges in Leak Testing
Despite the advanced techniques available, leak testing comes with its challenges.
Identifying leaks in complex, multi-layered devices can be difficult.
Working with small component sizes often requires highly sensitive equipment, increasing costs.
Environmental variables can also affect the accuracy of some leak detection methods.
Conclusion: The Future of Leak Testing in Medical Device Manufacturing
The importance of leak testing in the medical device industry cannot be overstated.
As Silicon Valley continues to drive innovation, these techniques will become even more refined and integral.
For mid-level employees, mastering these techniques not only ensures the safety and reliability of medical devices but also positions them as valuable assets within their companies.
Staying informed and adaptable is key to success in this fast-paced, evolving field.
資料ダウンロード
QCD調達購買管理クラウド「newji」は、調達購買部門で必要なQCD管理全てを備えた、現場特化型兼クラウド型の今世紀最高の購買管理システムとなります。
ユーザー登録
調達購買業務の効率化だけでなく、システムを導入することで、コスト削減や製品・資材のステータス可視化のほか、属人化していた購買情報の共有化による内部不正防止や統制にも役立ちます。
NEWJI DX
製造業に特化したデジタルトランスフォーメーション(DX)の実現を目指す請負開発型のコンサルティングサービスです。AI、iPaaS、および先端の技術を駆使して、製造プロセスの効率化、業務効率化、チームワーク強化、コスト削減、品質向上を実現します。このサービスは、製造業の課題を深く理解し、それに対する最適なデジタルソリューションを提供することで、企業が持続的な成長とイノベーションを達成できるようサポートします。
オンライン講座
製造業、主に購買・調達部門にお勤めの方々に向けた情報を配信しております。
新任の方やベテランの方、管理職を対象とした幅広いコンテンツをご用意しております。
お問い合わせ
コストダウンが利益に直結する術だと理解していても、なかなか前に進めることができない状況。そんな時は、newjiのコストダウン自動化機能で大きく利益貢献しよう!
(Β版非公開)