- お役立ち記事
- Tips for building a quality management system in the manufacturing industry in response to the revision of ISO 9001
Tips for building a quality management system in the manufacturing industry in response to the revision of ISO 9001
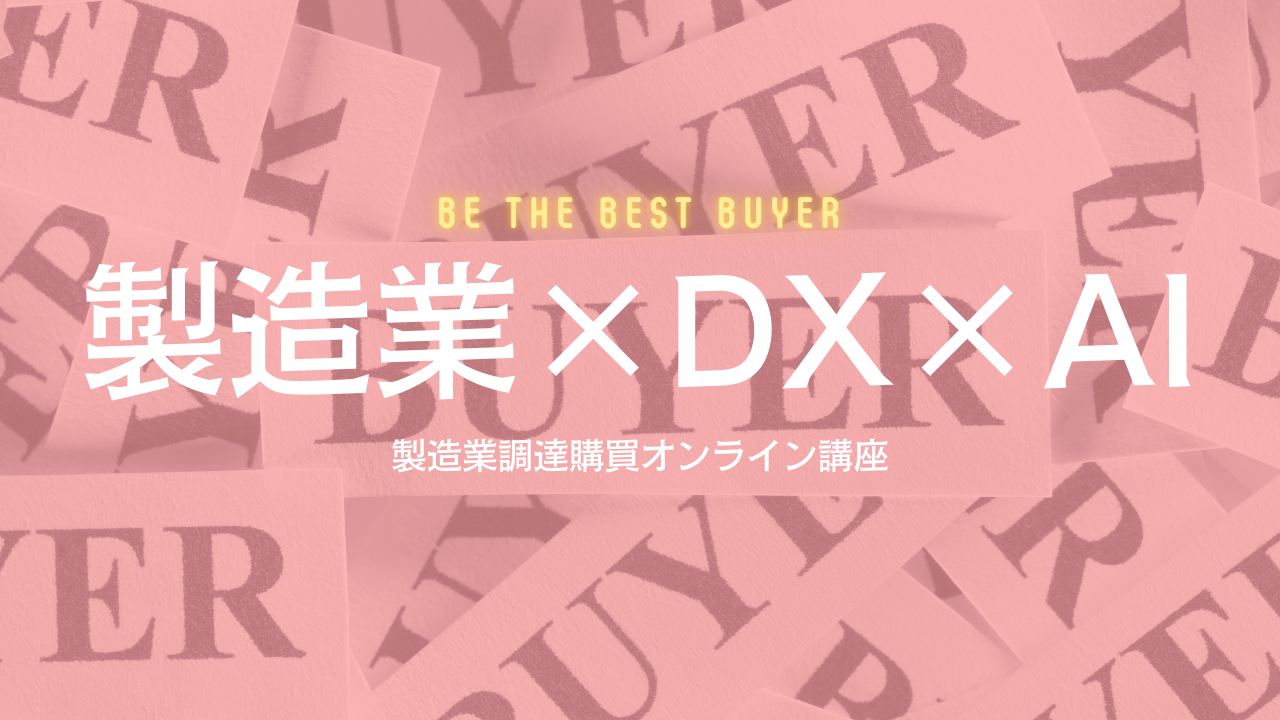
In today’s competitive manufacturing landscape, building a robust quality management system (QMS) is essential for success. With the recent revision of ISO 9001, the international standard for quality management, companies must adapt their processes to meet the new requirements. Implementing a QMS that aligns with the updated standard can help manufacturers improve product quality, enhance customer satisfaction, and streamline operations. Here are some key tips for building a quality management system in the manufacturing industry that complies with the revised ISO 9001.
1. Understand the changes in ISO 9001:2015
The first step in building a QMS is to familiarize yourself with the changes introduced in ISO 9001:2015. The revised standard places greater emphasis on risk-based thinking, leadership involvement, and the context of the organization. It also introduces new terminology and clarifies existing concepts. By understanding these changes, you can ensure that your QMS is designed to meet the new requirements.
2. Engage leadership and secure commitment
The revised ISO 9001 standard stresses the importance of leadership involvement in the QMS. Top management must demonstrate their commitment to the system by establishing a quality policy, setting objectives, and allocating resources. Engage your leadership team in the QMS development process and ensure that they understand their roles and responsibilities in maintaining and improving the system.
3. Identify and manage risks
Risk-based thinking is a central theme in ISO 9001:2015. Manufacturers must identify, assess, and manage risks related to their processes, products, and customer requirements. Develop a systematic approach to risk management, including the use of tools such as failure mode and effects analysis (FMEA) and risk matrices. By proactively managing risks, you can prevent quality issues and improve the overall effectiveness of your QMS.
4. Focus on process approach
The process approach is a fundamental concept in ISO 9001. It involves defining, managing, and improving the interrelated processes that make up your QMS. Map out your key processes, including their inputs, outputs, and interactions. Establish process performance indicators and monitor them regularly to identify opportunities for improvement. By adopting a process-oriented mindset, you can enhance the efficiency and effectiveness of your operations.
5. Implement a robust document control system
Documentation is a critical aspect of any QMS. ISO 9001:2015 requires manufacturers to maintain documented information necessary for the effectiveness of the system. Implement a document control system that ensures the creation, approval, distribution, and revision of documents are managed effectively. Use electronic document management systems to streamline the process and ensure that all employees have access to the latest versions of documents.
6. Establish a culture of continuous improvement
Continuous improvement is a core principle of ISO 9001. Manufacturers must establish a culture that encourages the identification and implementation of improvements to the QMS. Engage employees at all levels in the improvement process, and provide them with the necessary training and resources. Use tools such as root cause analysis and corrective action to address quality issues and prevent their recurrence. Regularly review the effectiveness of your QMS and identify opportunities for enhancement.
7. Monitor and measure performance
To ensure the effectiveness of your QMS, you must monitor and measure its performance. Establish key performance indicators (KPIs) that align with your quality objectives and customer requirements. Regularly collect and analyze data related to process performance, product quality, and customer satisfaction. Use this information to make data-driven decisions and drive continuous improvement.
8. Conduct regular internal audits
Internal audits are an essential tool for assessing the conformity and effectiveness of your QMS. Develop an internal audit program that covers all aspects of the system, including processes, products, and documentation. Train a team of internal auditors who can objectively evaluate the QMS and identify areas for improvement. Use the results of internal audits to drive corrective actions and improve the overall performance of the system.
By following these tips, manufacturers can build a quality management system that not only complies with the revised ISO 9001 standard but also drives real business value. A well-designed and implemented QMS can help you improve product quality, reduce costs, enhance customer satisfaction, and gain a competitive edge in the market. As you embark on your QMS journey, remember that building a robust system is an ongoing process that requires commitment, collaboration, and continuous improvement.
資料ダウンロード
QCD調達購買管理クラウド「newji」は、調達購買部門で必要なQCD管理全てを備えた、現場特化型兼クラウド型の今世紀最高の購買管理システムとなります。
ユーザー登録
調達購買業務の効率化だけでなく、システムを導入することで、コスト削減や製品・資材のステータス可視化のほか、属人化していた購買情報の共有化による内部不正防止や統制にも役立ちます。
NEWJI DX
製造業に特化したデジタルトランスフォーメーション(DX)の実現を目指す請負開発型のコンサルティングサービスです。AI、iPaaS、および先端の技術を駆使して、製造プロセスの効率化、業務効率化、チームワーク強化、コスト削減、品質向上を実現します。このサービスは、製造業の課題を深く理解し、それに対する最適なデジタルソリューションを提供することで、企業が持続的な成長とイノベーションを達成できるようサポートします。
オンライン講座
製造業、主に購買・調達部門にお勤めの方々に向けた情報を配信しております。
新任の方やベテランの方、管理職を対象とした幅広いコンテンツをご用意しております。
お問い合わせ
コストダウンが利益に直結する術だと理解していても、なかなか前に進めることができない状況。そんな時は、newjiのコストダウン自動化機能で大きく利益貢献しよう!
(Β版非公開)