- お役立ち記事
- Transforming Manufacturing with Industry 4.0: The Future of Smart Factories
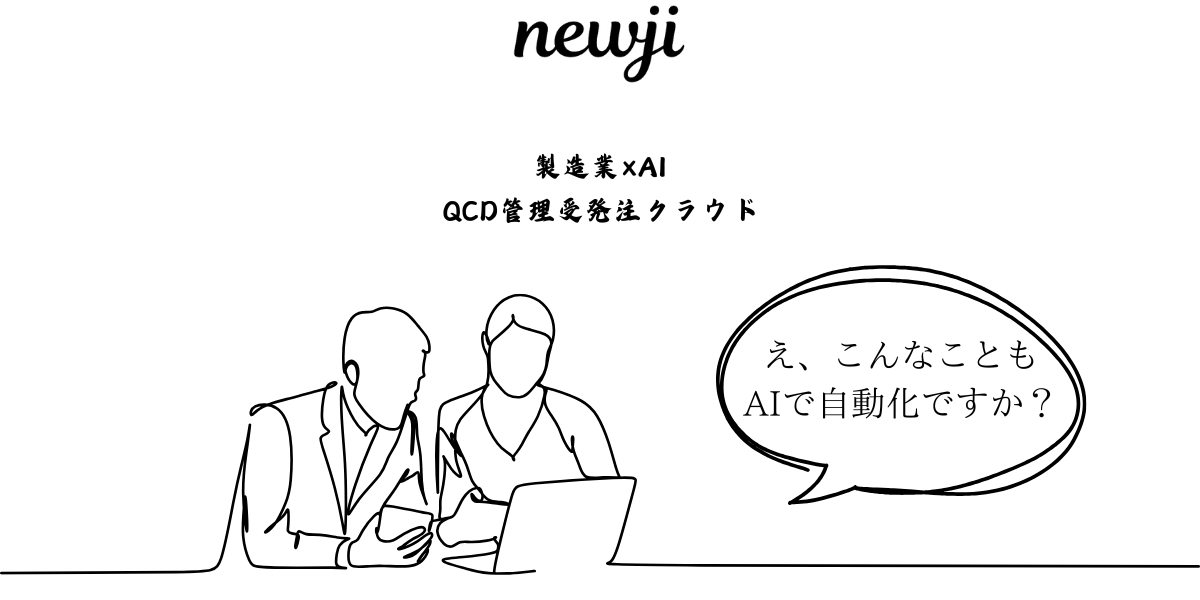
Transforming Manufacturing with Industry 4.0: The Future of Smart Factories
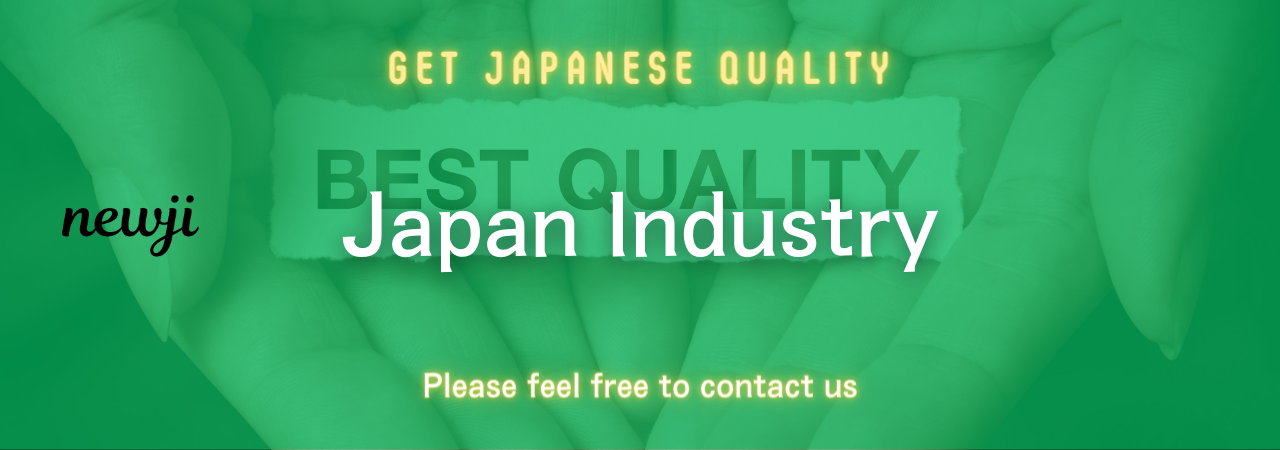
目次
Understanding Industry 4.0
Industry 4.0, also known as the Fourth Industrial Revolution, represents a significant shift in how manufacturing and production are carried out.
This transformation leverages advanced technologies like the Internet of Things (IoT), artificial intelligence (AI), and big data analytics to create smart factories.
By integrating these technologies, manufacturers can achieve higher efficiency, improved quality, and greater flexibility in their production processes.
The Key Components of Industry 4.0
Internet of Things (IoT)
IoT refers to a network of interconnected devices and machines that communicate with each other through the internet.
In a smart factory, IoT devices can monitor equipment performance, track inventory levels, and even predict maintenance needs.
This connectivity allows for real-time data sharing and decision-making, ultimately leading to more efficient and streamlined operations.
Artificial Intelligence (AI) and Machine Learning
AI and machine learning technologies are crucial for making sense of the massive volumes of data generated in a smart factory.
These technologies can analyze data to identify patterns, optimize processes, and make informed decisions.
For example, AI-powered systems can detect defects in products with greater accuracy than human inspectors, ensuring higher quality and reducing waste.
Big Data Analytics
Big data analytics involves the examination of large datasets to uncover hidden patterns, correlations, and insights.
In the context of Industry 4.0, big data analytics can help manufacturers optimize their supply chains, improve product quality, and enhance customer experiences.
By leveraging data from various sources, manufacturers can make more informed decisions and anticipate changes in demand or production requirements.
The Benefits of Smart Factories
Increased Efficiency
One of the primary benefits of implementing Industry 4.0 technologies in manufacturing is increased efficiency.
Connected devices and systems can automate routine tasks, monitor equipment performance, and identify areas for improvement.
This automation reduces the need for manual intervention, allowing workers to focus on more strategic and value-added activities.
Improved Product Quality
Smart factories leverage advanced technologies to maintain high product quality levels.
AI-powered inspection systems can detect defects in real-time, allowing for immediate corrective action.
Additionally, predictive maintenance tools can identify potential issues before they lead to equipment failure, minimizing downtime and ensuring consistent product quality.
Greater Flexibility
Industry 4.0 enables manufacturers to respond more quickly to changes in customer demand and market conditions.
Smart factories can adjust production schedules, reconfigure assembly lines, and even customize products with ease.
This adaptability allows manufacturers to stay competitive and meet the evolving needs of their customers.
Challenges and Considerations
Data Security and Privacy
With the increased connectivity of devices and systems in a smart factory, data security and privacy become critical concerns.
Manufacturers must implement robust cybersecurity measures to protect sensitive information from cyber threats.
Additionally, clear policies and protocols should be established to ensure data privacy and compliance with relevant regulations.
Integration with Existing Systems
Implementing Industry 4.0 technologies often requires integrating new systems with existing infrastructure.
This integration can be complex and may require significant investment in terms of time and resources.
Manufacturers must carefully plan and execute these integrations to ensure a smooth transition and minimize disruptions to their operations.
Workforce Training and Development
The adoption of Industry 4.0 technologies necessitates a skilled workforce that can operate and maintain advanced systems.
Manufacturers must invest in training and development programs to equip their employees with the necessary skills.
This investment not only ensures the successful implementation of new technologies but also empowers workers to thrive in a rapidly evolving industry.
The Future of Smart Factories
As Industry 4.0 continues to evolve, the future of manufacturing looks increasingly promising.
Emerging technologies such as 5G connectivity, blockchain, and augmented reality (AR) are expected to further enhance the capabilities of smart factories.
For instance, 5G networks will enable faster and more reliable communication between devices, while blockchain can provide greater transparency and security in supply chain management.
AR technologies can support workers with real-time information and guidance, improving productivity and reducing errors.
In conclusion, Industry 4.0 is fundamentally transforming the manufacturing landscape.
By embracing advanced technologies and creating smart factories, manufacturers can achieve unprecedented levels of efficiency, quality, and flexibility.
While challenges exist, the potential benefits make the journey toward Industry 4.0 a worthwhile endeavor.
資料ダウンロード
QCD調達購買管理クラウド「newji」は、調達購買部門で必要なQCD管理全てを備えた、現場特化型兼クラウド型の今世紀最高の購買管理システムとなります。
ユーザー登録
調達購買業務の効率化だけでなく、システムを導入することで、コスト削減や製品・資材のステータス可視化のほか、属人化していた購買情報の共有化による内部不正防止や統制にも役立ちます。
NEWJI DX
製造業に特化したデジタルトランスフォーメーション(DX)の実現を目指す請負開発型のコンサルティングサービスです。AI、iPaaS、および先端の技術を駆使して、製造プロセスの効率化、業務効率化、チームワーク強化、コスト削減、品質向上を実現します。このサービスは、製造業の課題を深く理解し、それに対する最適なデジタルソリューションを提供することで、企業が持続的な成長とイノベーションを達成できるようサポートします。
オンライン講座
製造業、主に購買・調達部門にお勤めの方々に向けた情報を配信しております。
新任の方やベテランの方、管理職を対象とした幅広いコンテンツをご用意しております。
お問い合わせ
コストダウンが利益に直結する術だと理解していても、なかなか前に進めることができない状況。そんな時は、newjiのコストダウン自動化機能で大きく利益貢献しよう!
(Β版非公開)