- お役立ち記事
- Troubleshooting Burr Prevention and Effective Countermeasures
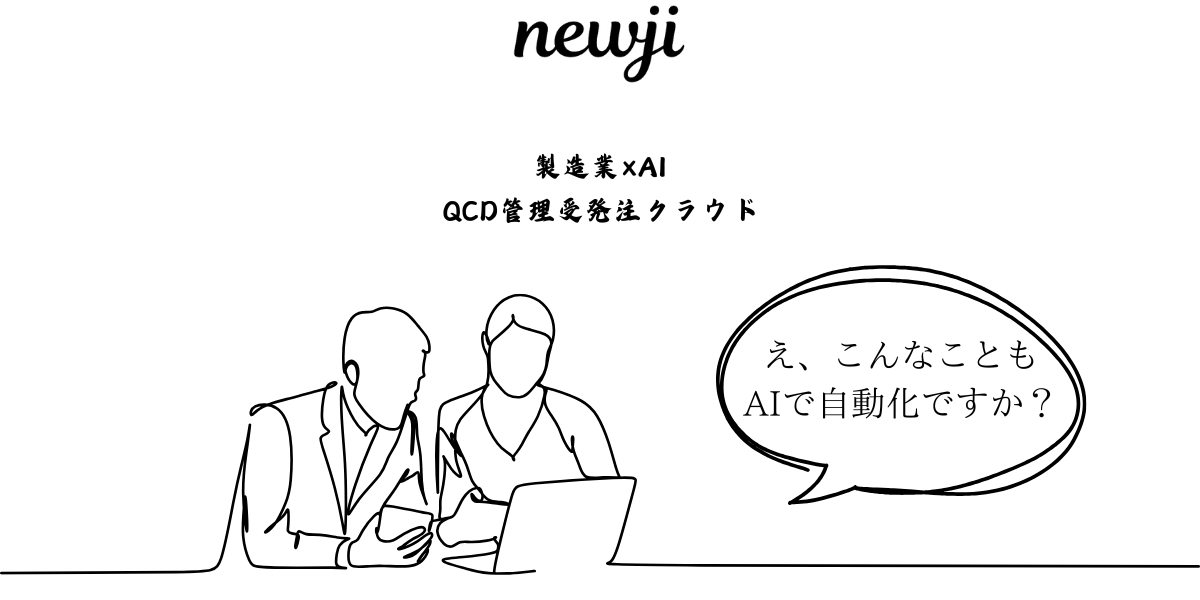
Troubleshooting Burr Prevention and Effective Countermeasures
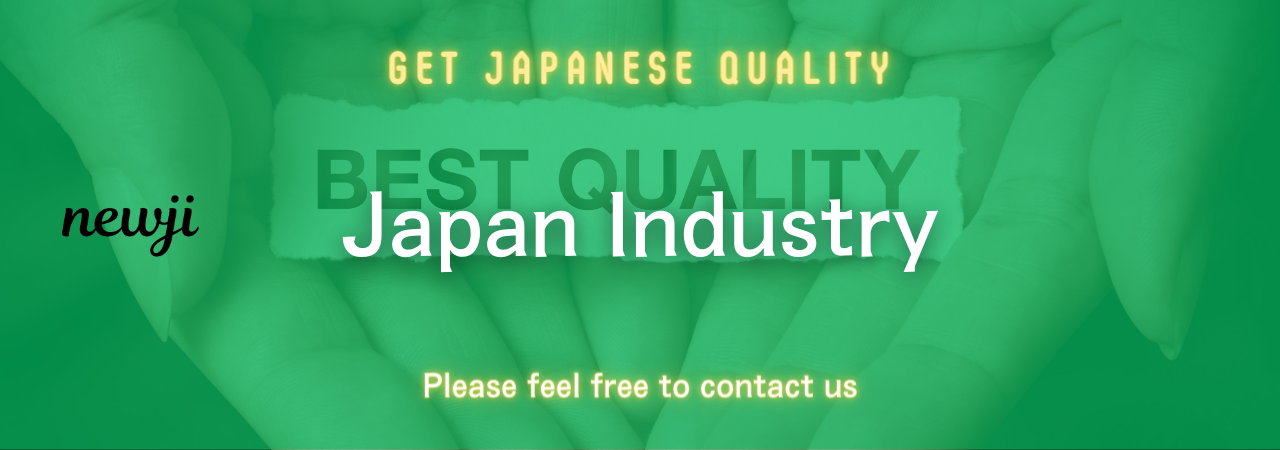
Preventing and addressing burrs on machined parts is an essential aspect of manufacturing that helps ensure product quality, safety, and functionality.
Machined parts with burrs not only present a risk to operators through sharp edges, but they can also lead to improper fitting of parts, affecting the overall performance and durability of finished products.
Understanding the causes, prevention, and removal of burrs can lead to more efficient manufacturing processes and higher quality outcomes.
目次
Understanding Burrs in Manufacturing
Burrs are unwanted protrusions or rough edges formed on the surface of a material during machining processes such as cutting, grinding, drilling, or milling.
They can be small or large, visible or difficult to detect with the naked eye.
Burrs arise due to the material deformation that occurs at the edges when a cutting tool separates a piece of material.
Types of Burrs
1. **Rollover Burr**: This is the most common type and occurs when material is pushed over the edge as a result of the cutting tool.
2. **Poisson Burr**: Results from the stretching and widening of the metal in a particular direction.
3. **Tear Burr**: Occurs when a part of the material tears away from the body during machining, leaving irregular surface deformations.
Each type requires different handling and removal strategies, making it crucial to identify the type of burr present on a component.
Identifying the Causes of Burrs
Understanding why burrs occur is key to preventing them.
Some common causes include:
Tool Wear and Tooling Errors
Worn-out or improperly maintained tools can lead to the formation of burrs.
Blunt or damaged tools do not cut efficiently and may instead deform the material, causing burrs to form along the edges.
Incorrect Machining Parameters
Incorrect settings such as feed rate, cutter speed, and depth of cut can lead to excessive material stress and result in burr formation.
Using the appropriate parameters for the material and process can significantly reduce burr occurrence.
Metal Properties
The material properties themselves can contribute to burr formation.
Soft materials are more likely to develop burrs due to their tendency to deform, while harder materials may generate less burr but can cause more severe cutting-edge wear.
Preventive Measures to Reduce Burr Formation
Prevention is often the best approach when it comes to dealing with burrs.
Implementing certain measures can help reduce their occurrence and improve product quality.
Optimizing Tool Design
Using tools specifically designed to minimize burr formation can help.
Selecting appropriate geometries and coatings for cutting tools can enhance their performance and help maintain sharp edges longer.
Chamfered edges and appropriate rake angles also play a crucial role in reducing material deformation during the machining process.
Refining Machining Parameters
Ensuring that your machining parameters are optimized for the specific material and process is vital.
Adjusting feed rates, speeds, and cutting depths to suit the material can reduce stress and minimize burr formation.
Conduct regular reviews and testing to determine the ideal settings for each application.
Material Selection
Choosing the right material for your manufacturing process can significantly affect burr production.
Understanding the properties of the materials you work with allows you to anticipate their behavior during machining and select those that are less likely to produce burrs.
Effective Burr Removal Techniques
While preventive measures can drastically reduce burr formation, there will still be cases where burr removal is necessary.
Here are some effective techniques:
Mechanical Deburring
This involves using tools like files, brushes, or abrasive pads to manually remove burrs from a component.
Although labor-intensive and not always suitable for complex geometries, mechanical deburring can be effective for simple parts.
Thermal Deburring
Also known as thermochemically deburring, this process burns away burrs using controlled bursts of combustible gas.
It’s especially effective for parts with intricate designs that are difficult to deburr manually.
Chemical Deburring
Using chemical solutions to dissolve burrs is another method for removing unwanted protrusions.
This approach can be tailored for specific materials but often requires careful handling and additional waste management practices.
Electrochemical Deburring
A process that uses electrical energy to dissolve burrs.
The workpiece acts as an anode, and an electrolyte solution is used to selectively remove burrs, especially effective for small, intricate parts that may be damaged by mechanical methods.
Conclusion
Burrs are a common challenge in manufacturing, but understanding their nature, causes, and how to prevent them can improve product quality and efficiency.
Optimizing tool design and machining parameters, choosing suitable materials, and employing effective removal techniques can aid in minimizing burr impact.
By adopting these strategies, manufacturers can enhance their processes and ensure the delivery of superior, burr-free products to consumers.
資料ダウンロード
QCD調達購買管理クラウド「newji」は、調達購買部門で必要なQCD管理全てを備えた、現場特化型兼クラウド型の今世紀最高の購買管理システムとなります。
ユーザー登録
調達購買業務の効率化だけでなく、システムを導入することで、コスト削減や製品・資材のステータス可視化のほか、属人化していた購買情報の共有化による内部不正防止や統制にも役立ちます。
NEWJI DX
製造業に特化したデジタルトランスフォーメーション(DX)の実現を目指す請負開発型のコンサルティングサービスです。AI、iPaaS、および先端の技術を駆使して、製造プロセスの効率化、業務効率化、チームワーク強化、コスト削減、品質向上を実現します。このサービスは、製造業の課題を深く理解し、それに対する最適なデジタルソリューションを提供することで、企業が持続的な成長とイノベーションを達成できるようサポートします。
オンライン講座
製造業、主に購買・調達部門にお勤めの方々に向けた情報を配信しております。
新任の方やベテランの方、管理職を対象とした幅広いコンテンツをご用意しております。
お問い合わせ
コストダウンが利益に直結する術だと理解していても、なかなか前に進めることができない状況。そんな時は、newjiのコストダウン自動化機能で大きく利益貢献しよう!
(Β版非公開)