- お役立ち記事
- Unlocking Excellence: The Role of Supplier Certification in Japanese Manufacturing Success
Unlocking Excellence: The Role of Supplier Certification in Japanese Manufacturing Success
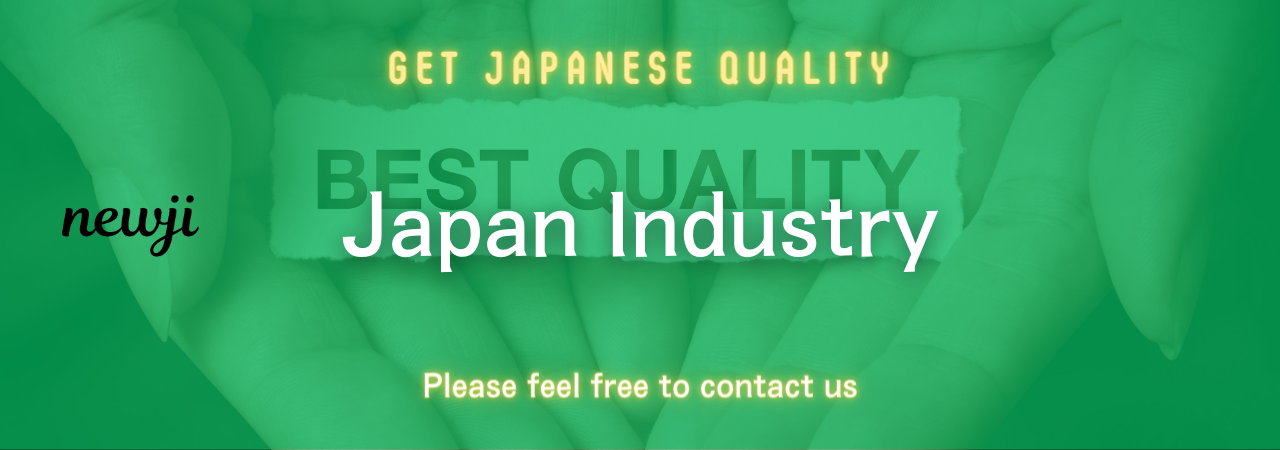
目次
Understanding Supplier Certification in Japanese Manufacturing
Supplier certification plays a pivotal role in the success of Japanese manufacturing companies. It serves as a benchmark for quality, reliability, and efficiency among suppliers. By implementing rigorous certification processes, Japanese manufacturers ensure that their supply chain upholds the highest standards necessary for producing world-class products.
The Importance of Supplier Certification
Supplier certification is essential for maintaining consistent product quality and operational efficiency. It provides a structured framework for evaluating and selecting suppliers based on predefined criteria. This process minimizes the risk of defects, delays, and other issues that can adversely affect production. Additionally, certification fosters a culture of continuous improvement among suppliers, encouraging them to adopt best practices and innovate in their processes.
Types of Supplier Certifications in Japan
Japanese manufacturers utilize various certification standards to assess their suppliers. Some of the most common certifications include ISO 9001 for quality management, ISO 14001 for environmental management, and IATF 16949 for automotive quality management. These certifications ensure that suppliers meet international and industry-specific standards, facilitating seamless integration into the manufacturing process.
Advantages of Supplier Certification
Implementing a supplier certification program offers numerous benefits to Japanese manufacturing companies. These advantages span across quality assurance, reliability, competitive positioning, and more.
Quality Assurance
One of the primary advantages of supplier certification is enhanced quality assurance. Certified suppliers are required to adhere to strict quality standards, reducing the likelihood of defects and ensuring that materials and components meet the necessary specifications. This leads to higher overall product quality and customer satisfaction.
Enhanced Reliability and Consistency
Certification processes evaluate a supplier’s ability to deliver consistently high-quality products. This reliability is crucial for maintaining steady production schedules and meeting delivery deadlines. Consistent performance also builds trust between manufacturers and suppliers, fostering long-term partnerships.
Competitive Advantage
Working with certified suppliers can provide a significant competitive advantage. It signals to customers and stakeholders that the company is committed to quality and excellence. This reputation can differentiate a manufacturer in a crowded marketplace, attracting more business and fostering customer loyalty.
Disadvantages of Supplier Certification
While supplier certification offers many benefits, it also comes with certain drawbacks that companies must consider.
High Costs
Achieving and maintaining certification can be costly for suppliers. The expenses associated with compliance, audits, and process improvements may be substantial, particularly for smaller suppliers. These costs can strain supplier relationships and impact their willingness to engage with larger manufacturers.
Lengthy Certification Process
The certification process can be time-consuming, potentially delaying the onboarding of new suppliers. Extended timelines may hinder a company’s ability to respond quickly to market demands or production needs, affecting overall agility and responsiveness.
Potential for Supplier Reduction
Strict certification criteria may lead to a reduction in the pool of available suppliers. While this ensures higher quality, it can also limit options and increase dependency on a smaller number of suppliers. In cases of supplier disruption, this dependency can pose significant risks to the manufacturing process.
Supplier Negotiation Techniques in Japanese Manufacturing
Effective negotiation with suppliers is crucial for securing favorable terms and fostering strong partnerships. Japanese manufacturing companies employ specific techniques tailored to their cultural and business practices to achieve successful negotiations.
Cultural Considerations
Understanding and respecting Japanese business culture is essential during negotiations. Emphasis is placed on building trust, showing respect, and maintaining harmony. Negotiators should exhibit patience, listen actively, and demonstrate a willingness to engage in long-term partnerships rather than seeking immediate gains.
Building Long-Term Relationships
Japanese manufacturers prioritize long-term relationships over short-term deals. Negotiations often focus on mutual benefits, collaborative growth, and shared success. Building strong relationships can lead to more favorable terms, better support, and increased flexibility during challenging times.
Effective Communication Strategies
Clear and transparent communication is vital in negotiations. Japanese companies value precision and thoroughness, so providing detailed information and being explicit about expectations can facilitate smoother negotiations. Additionally, non-verbal cues and indirect communication styles are common, requiring negotiators to read between the lines and understand implicit messages.
Market Conditions Affecting Supplier Certification
Several market conditions influence the effectiveness and implementation of supplier certification in Japanese manufacturing. Understanding these factors helps companies adapt their certification strategies to changing environments.
Global Supply Chain Dynamics
Globalization has expanded the reach of manufacturing supply chains, introducing complexity and variability. Supplier certification must account for diverse geographic, economic, and regulatory environments. Japanese manufacturers often emphasize certifications that align with international standards to ensure compatibility across global supply chains.
Technological Advancements
Advancements in technology impact supplier capabilities and certification requirements. Automation, digitalization, and Industry 4.0 technologies require suppliers to adapt and upgrade their processes. Certification programs must evolve to incorporate new technological criteria, ensuring that suppliers remain competitive and capable of meeting modern manufacturing demands.
Economic Factors
Economic fluctuations can affect both manufacturers and suppliers. During economic downturns, maintaining certification standards may become challenging for suppliers facing financial constraints. Conversely, economic growth can provide opportunities for investment in quality improvements and process enhancements, facilitating higher standards of certification.
Best Practices for Implementing Supplier Certification
Adopting best practices in supplier certification enhances its effectiveness and ensures alignment with business objectives. Japanese manufacturing companies employ several strategies to optimize their certification programs.
Comprehensive Vendor Assessment
A thorough evaluation of potential suppliers is critical. This assessment should cover not only quality standards but also financial stability, operational capabilities, and compliance with ethical and environmental practices. Utilizing a multi-faceted evaluation approach ensures that suppliers meet all necessary criteria for certification.
Continuous Monitoring and Evaluation
Supplier certification is not a one-time process. Continuous monitoring and regular evaluations help maintain high standards over time. Implementing performance metrics, conducting periodic audits, and fostering open communication channels enable ongoing assessment and improvement of supplier performance.
Training and Development
Investing in the training and development of suppliers promotes a culture of continuous improvement. Providing resources, workshops, and support for process enhancements can help suppliers achieve and maintain certification standards. This collaborative approach strengthens the overall supply chain and enhances product quality.
Conclusion
Supplier certification is a cornerstone of Japanese manufacturing excellence. It ensures that suppliers adhere to stringent quality and operational standards, fostering reliability and consistency in the supply chain. While the certification process entails significant investments and potential challenges, the advantages in quality assurance, competitive positioning, and long-term partnerships are substantial. By understanding market conditions, employing effective negotiation techniques, and adhering to best practices, Japanese manufacturers can unlock the full potential of supplier certification, driving sustained success and innovation in the global marketplace.
資料ダウンロード
QCD調達購買管理クラウド「newji」は、調達購買部門で必要なQCD管理全てを備えた、現場特化型兼クラウド型の今世紀最高の購買管理システムとなります。
ユーザー登録
調達購買業務の効率化だけでなく、システムを導入することで、コスト削減や製品・資材のステータス可視化のほか、属人化していた購買情報の共有化による内部不正防止や統制にも役立ちます。
NEWJI DX
製造業に特化したデジタルトランスフォーメーション(DX)の実現を目指す請負開発型のコンサルティングサービスです。AI、iPaaS、および先端の技術を駆使して、製造プロセスの効率化、業務効率化、チームワーク強化、コスト削減、品質向上を実現します。このサービスは、製造業の課題を深く理解し、それに対する最適なデジタルソリューションを提供することで、企業が持続的な成長とイノベーションを達成できるようサポートします。
オンライン講座
製造業、主に購買・調達部門にお勤めの方々に向けた情報を配信しております。
新任の方やベテランの方、管理職を対象とした幅広いコンテンツをご用意しております。
お問い合わせ
コストダウンが利益に直結する術だと理解していても、なかなか前に進めることができない状況。そんな時は、newjiのコストダウン自動化機能で大きく利益貢献しよう!
(Β版非公開)