- お役立ち記事
- Unlocking Japanese Manufacturing Excellence: A Deep Dive into Overall Equipment Effectiveness
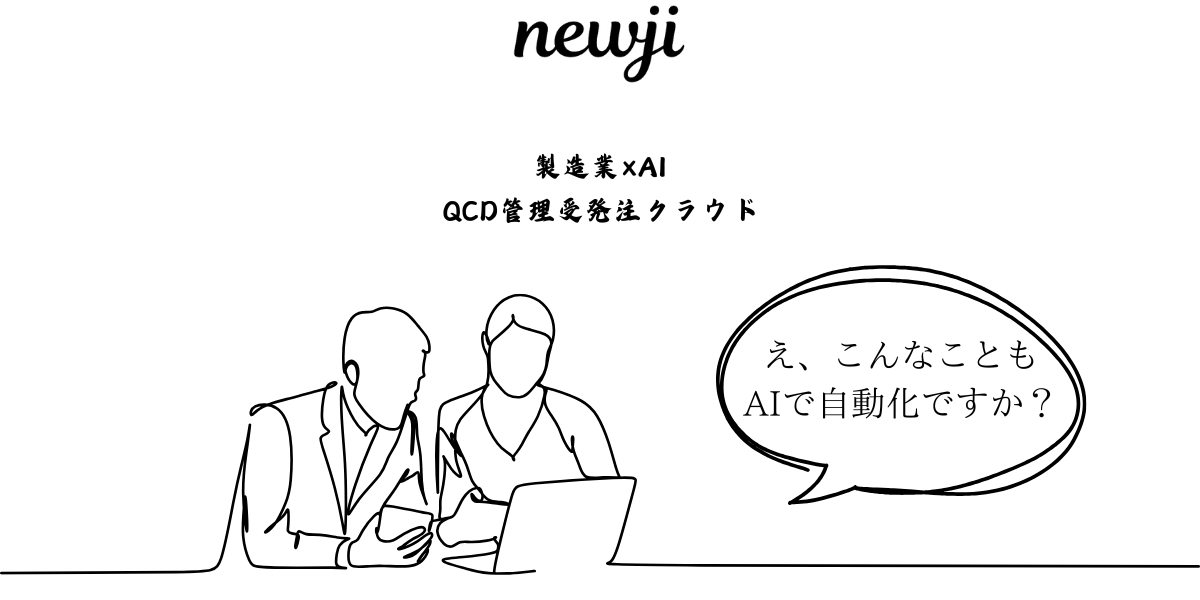
Unlocking Japanese Manufacturing Excellence: A Deep Dive into Overall Equipment Effectiveness
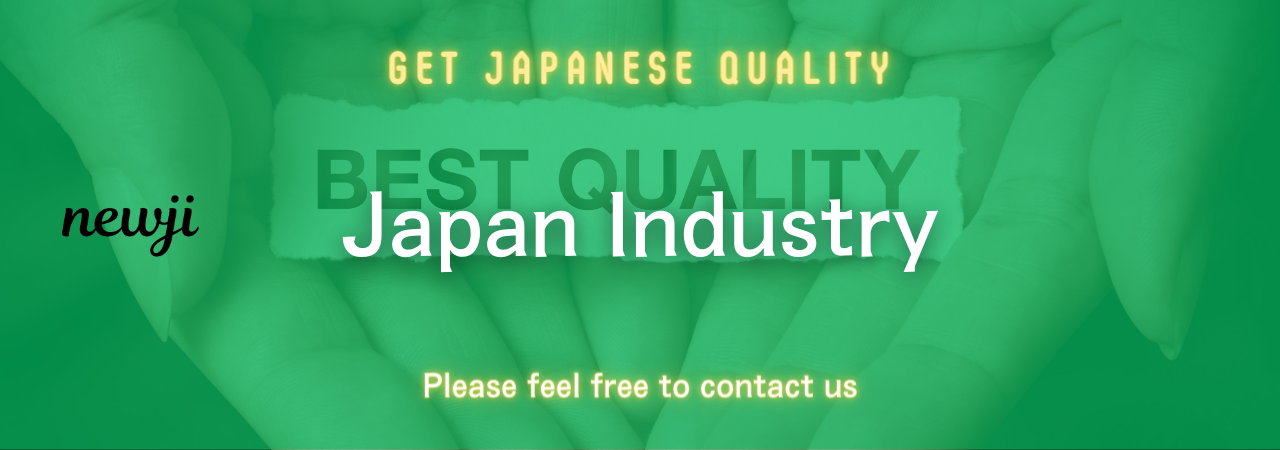
目次
Introduction to Overall Equipment Effectiveness (OEE)
Overall Equipment Effectiveness, commonly known as OEE, is a crucial metric in the manufacturing industry. It provides a comprehensive overview of how effectively a manufacturing operation is utilized. OEE measures the percentage of planned production time that is truly productive. This metric helps companies identify losses, benchmark progress, and improve the efficiency of their manufacturing processes.
In the context of Japanese manufacturing excellence, OEE plays a significant role. Japanese manufacturers have long been recognized for their efficiency and quality. By implementing OEE, these companies can maintain their competitive edge and continuously strive for improvement.
The Pillars of OEE
OEE is calculated based on three main components: Availability, Performance, and Quality. Each of these pillars provides insights into different aspects of the manufacturing process.
Availability
Availability measures the proportion of scheduled time that the equipment is available for production. It accounts for both planned and unplanned downtime. Planned downtime includes scheduled maintenance and breaks, whereas unplanned downtime includes unexpected equipment failures or other disruptions.
Improving availability involves minimizing both planned and unplanned downtime. This can be achieved through effective maintenance strategies, such as preventive and predictive maintenance, and by ensuring that equipment is quickly repaired when breakdowns occur.
Performance
Performance measures how quickly the equipment operates compared to its maximum possible speed. It considers factors like minor stops and slow cycles that prevent the machine from running at its full capacity.
Enhancing performance involves optimizing production processes to reduce cycle times and minimize minor stoppages. Techniques such as lean manufacturing and continuous improvement can help achieve higher performance levels.
Quality
Quality assesses the proportion of good parts produced compared to the total number of parts started. It reflects the effectiveness of the production process in producing defect-free products.
Improving quality involves implementing quality control measures, such as Six Sigma and Total Quality Management (TQM), to reduce defects and ensure consistent product standards.
Advantages of Implementing OEE in Japanese Manufacturing
Japanese manufacturing is renowned for its efficiency and quality. Implementing OEE further enhances these strengths by providing a structured approach to identifying and eliminating inefficiencies.
Enhanced Productivity
OEE helps manufacturers identify and eliminate bottlenecks in their production processes. By addressing issues related to availability, performance, and quality, companies can significantly increase their overall productivity.
Data-Driven Decision Making
OEE provides valuable data that can be used to make informed decisions. Manufacturers can analyze OEE metrics to identify trends, predict future performance, and implement strategic improvements.
Continuous Improvement
OEE fosters a culture of continuous improvement. By regularly monitoring and analyzing OEE, companies can implement incremental changes that lead to sustained improvements in manufacturing efficiency.
Cost Reduction
Improving OEE can lead to significant cost savings. By reducing downtime, increasing production speed, and minimizing defects, companies can lower operational costs and enhance profitability.
Challenges and Disadvantages of OEE
While OEE offers numerous benefits, its implementation is not without challenges. Understanding these challenges is essential for successful OEE adoption.
Complexity in Measurement
Accurately measuring OEE can be complex. It requires precise data collection and analysis, which can be time-consuming and resource-intensive. Without accurate measurements, the insights provided by OEE may be unreliable.
Resistance to Change
Implementing OEE often involves significant changes to existing processes. Employees and management may resist these changes, making it challenging to implement OEE effectively.
Overemphasis on Metrics
Focusing too much on OEE metrics can lead to unintended consequences. For example, prioritizing OEE improvement might lead to increased pressure on employees, potentially affecting morale and job satisfaction.
Integration with Existing Systems
Integrating OEE with existing manufacturing systems can be difficult. It requires seamless communication between different systems and processes, which can pose technical and logistical challenges.
Supplier Negotiation Techniques for Enhancing OEE
Effective supplier negotiation is crucial for enhancing OEE, especially when dealing with Japanese suppliers known for their high standards and quality.
Building Strong Relationships
Japanese business culture places a strong emphasis on building long-term relationships. Establishing trust and mutual respect with suppliers can lead to better cooperation and more favorable terms, which can improve OEE.
Clear Communication
Clear and transparent communication is essential in supplier negotiations. Clearly outlining expectations, specifications, and performance standards helps ensure that suppliers understand the requirements, leading to higher quality and more reliable supply chains.
Collaborative Problem Solving
Working collaboratively with suppliers to address issues that affect OEE can lead to more effective solutions. This approach fosters a partnership where both parties are committed to continuous improvement.
Performance-Based Contracts
Implementing performance-based contracts can incentivize suppliers to meet specific OEE targets. This alignment of goals ensures that suppliers are motivated to contribute to the overall efficiency and effectiveness of the manufacturing process.
Market Conditions and Their Impact on OEE
Understanding market conditions is vital for optimizing OEE. External factors such as economic trends, technological advancements, and industry standards can significantly influence OEE performance.
Economic Fluctuations
Economic conditions can affect demand for products, which in turn impacts production schedules and OEE. During periods of high demand, manufacturers may face challenges in maintaining high OEE due to increased pressure on equipment and personnel.
Technological Advancements
Advancements in technology can enhance OEE by providing better tools for measurement, monitoring, and optimization. Implementing new technologies can lead to improved equipment performance and higher OEE scores.
Industry Standards
Adhering to industry standards ensures that production processes meet quality and efficiency benchmarks. Compliance with these standards can positively influence OEE by promoting best practices and minimizing defects.
Best Practices for Maximizing OEE
Implementing best practices is essential for maximizing OEE and achieving manufacturing excellence. These practices help in systematically improving the three pillars of OEE: Availability, Performance, and Quality.
Implementing Preventive Maintenance
Preventive maintenance involves regularly scheduled maintenance activities to prevent equipment failures. By performing maintenance proactively, manufacturers can reduce unplanned downtime and enhance availability.
Adopting Lean Manufacturing Principles
Lean manufacturing focuses on eliminating waste and optimizing processes. By adopting lean principles, manufacturers can improve performance by increasing production speed and reducing cycle times.
Investing in Training and Development
Training employees on OEE principles and best practices is crucial for successful implementation. Well-trained staff can effectively monitor and improve OEE, leading to sustained manufacturing excellence.
Utilizing Real-Time Monitoring Systems
Real-time monitoring systems provide instant access to OEE data, allowing manufacturers to identify and address issues promptly. These systems enable continuous improvement by providing ongoing insights into production performance.
Conducting Regular OEE Audits
Regular OEE audits help in assessing the effectiveness of OEE initiatives. By evaluating performance periodically, manufacturers can identify areas for improvement and implement corrective actions to enhance OEE.
Fostering a Culture of Continuous Improvement
Creating a culture that prioritizes continuous improvement encourages employees to seek out and implement OEE enhancements. This mindset ensures that OEE remains a focal point of the organization’s operational strategy.
Case Studies: Japanese Manufacturers Excelling in OEE
Examining real-world examples of Japanese manufacturers that have successfully implemented OEE provides valuable insights into effective strategies and practices.
Toyota Motor Corporation
Toyota is a global leader in manufacturing excellence, largely due to its implementation of the Toyota Production System (TPS), which integrates OEE principles. By focusing on continuous improvement and waste reduction, Toyota has achieved consistently high OEE scores, resulting in superior product quality and operational efficiency.
Panasonic Corporation
Panasonic utilizes OEE to optimize its production lines and enhance equipment performance. Through diligent monitoring and maintenance, Panasonic has minimized downtime and maximized production output, maintaining its reputation for high-quality electronics.
Honda Motor Co., Ltd.
Honda employs OEE to streamline its manufacturing processes and ensure efficient utilization of resources. By focusing on performance and quality improvements, Honda has achieved high levels of productivity and customer satisfaction.
Integrating OEE with Other Manufacturing Metrics
To gain a comprehensive understanding of manufacturing performance, integrating OEE with other metrics is essential. This holistic approach allows for more informed decision-making and effective process optimization.
Lean Manufacturing Metrics
Integrating OEE with lean manufacturing metrics, such as value-added time and waste reduction, provides a deeper insight into process efficiency. This integration helps in identifying non-value-added activities that can be eliminated to enhance overall performance.
Six Sigma Metrics
Combining OEE with Six Sigma metrics, such as Defects Per Million Opportunities (DPMO), allows for a robust analysis of quality and performance. This synergy aids in systematically reducing defects and improving process capabilities.
Supply Chain Metrics
Linking OEE with supply chain metrics, such as lead time and inventory turnover, ensures that production efficiency aligns with supply chain effectiveness. This alignment helps in maintaining optimal inventory levels and meeting customer demand consistently.
The Role of Technology in Enhancing OEE
Technology plays a pivotal role in enhancing OEE by providing tools and solutions that facilitate accurate measurement, data analysis, and process optimization.
Internet of Things (IoT) and OEE
IoT devices enable real-time data collection from manufacturing equipment. This data is essential for calculating OEE accurately and identifying areas for improvement. IoT also facilitates predictive maintenance, reducing unexpected downtime and enhancing availability.
Artificial Intelligence and Machine Learning
AI and machine learning algorithms analyze vast amounts of OEE data to identify patterns and predict potential issues. These technologies can automate decision-making processes, leading to more efficient production and higher OEE scores.
Advanced Data Analytics
Advanced data analytics tools help in processing and visualizing OEE data, making it easier for manufacturers to interpret and act upon the insights. These tools enable deeper analysis, uncovering hidden inefficiencies and opportunities for improvement.
Automation and Robotics
Automation and robotics enhance performance by increasing production speed and consistency. These technologies reduce human error, ensuring higher quality output and contributing to overall OEE improvement.
Implementing OEE: Step-by-Step Guide
Implementing OEE effectively requires a structured approach. The following steps outline a comprehensive guide to successful OEE implementation.
Step 1: Define Objectives
Clearly define the objectives of implementing OEE. Determine what you aim to achieve, such as reducing downtime, increasing production speed, or improving quality. Clear objectives provide a roadmap for the implementation process.
Step 2: Establish Baseline Metrics
Measure the current OEE performance to establish a baseline. This involves calculating the existing availability, performance, and quality metrics. Baseline metrics serve as a reference point for future improvements.
Step 3: Train Employees
Educate employees about OEE principles and their roles in the implementation process. Training ensures that everyone understands the importance of OEE and how to contribute to its improvement.
Step 4: Implement Measurement Systems
Set up reliable measurement systems to track OEE metrics accurately. This may involve installing sensors, implementing software solutions, and establishing data collection protocols.
Step 5: Analyze Data
Regularly analyze OEE data to identify trends and areas for improvement. Use the insights gained to implement targeted strategies that address specific inefficiencies.
Step 6: Implement Improvement Initiatives
Based on the data analysis, implement initiatives aimed at improving availability, performance, and quality. These may include process optimizations, equipment upgrades, or training programs.
Step 7: Monitor Progress
Continuously monitor OEE performance to assess the effectiveness of improvement initiatives. Regular monitoring helps in identifying ongoing issues and ensuring that progress is sustained.
Step 8: Foster a Culture of Continuous Improvement
Encourage a culture where continuous improvement is prioritized. Empower employees to contribute ideas and engage in problem-solving, fostering an environment that supports ongoing OEE enhancement.
The Future of OEE in Japanese Manufacturing
As Japanese manufacturers continue to innovate and strive for excellence, the role of OEE is set to become even more significant. Emerging technologies and evolving market demands will shape the future of OEE implementation.
Integration with Industry 4.0
Industry 4.0 initiatives, which focus on digital transformation and smart manufacturing, will further enhance OEE. The integration of advanced technologies like IoT, AI, and robotics will provide deeper insights and more sophisticated tools for OEE optimization.
Sustainability and OEE
Sustainable manufacturing practices are gaining importance. OEE can contribute to sustainability by optimizing resource utilization and reducing waste. Manufacturers can align OEE initiatives with environmental goals to achieve both efficiency and sustainability.
Global Supply Chain Dynamics
Global supply chain complexities necessitate robust OEE strategies. Japanese manufacturers will continue to leverage OEE to manage supply chain disruptions, maintain high standards, and ensure consistent product quality in a dynamic global market.
Enhanced Training and Workforce Development
As technology advances, workforce development will be crucial. Training programs will evolve to equip employees with the skills needed to utilize new technologies and methodologies for OEE improvement, ensuring that the workforce remains capable and adaptable.
Conclusion
Overall Equipment Effectiveness is a vital metric for achieving manufacturing excellence, particularly in the context of Japanese manufacturing. By focusing on availability, performance, and quality, Japanese manufacturers can maintain their reputation for efficiency and high standards. Implementing OEE involves overcoming challenges such as measurement complexity and resistance to change, but the benefits in terms of enhanced productivity, cost reduction, and continuous improvement are substantial.
Supplier negotiation techniques, informed by strong relationships and clear communication, are essential for enhancing OEE. Additionally, understanding market conditions and integrating OEE with other manufacturing metrics provide a comprehensive approach to operational excellence. Leveraging technology plays a critical role in maximizing OEE, enabling real-time monitoring, predictive maintenance, and data-driven decision-making.
Successful implementation of OEE requires a step-by-step approach, including defining objectives, establishing baseline metrics, training employees, and fostering a culture of continuous improvement. As Japanese manufacturers continue to innovate and lead in the global market, OEE will remain a cornerstone of their strategy for sustaining efficiency and delivering high-quality products. Embracing OEE not only unlocks the potential for operational excellence but also ensures that manufacturers remain competitive in an ever-evolving industry landscape.
資料ダウンロード
QCD調達購買管理クラウド「newji」は、調達購買部門で必要なQCD管理全てを備えた、現場特化型兼クラウド型の今世紀最高の購買管理システムとなります。
ユーザー登録
調達購買業務の効率化だけでなく、システムを導入することで、コスト削減や製品・資材のステータス可視化のほか、属人化していた購買情報の共有化による内部不正防止や統制にも役立ちます。
NEWJI DX
製造業に特化したデジタルトランスフォーメーション(DX)の実現を目指す請負開発型のコンサルティングサービスです。AI、iPaaS、および先端の技術を駆使して、製造プロセスの効率化、業務効率化、チームワーク強化、コスト削減、品質向上を実現します。このサービスは、製造業の課題を深く理解し、それに対する最適なデジタルソリューションを提供することで、企業が持続的な成長とイノベーションを達成できるようサポートします。
オンライン講座
製造業、主に購買・調達部門にお勤めの方々に向けた情報を配信しております。
新任の方やベテランの方、管理職を対象とした幅広いコンテンツをご用意しております。
お問い合わせ
コストダウンが利益に直結する術だと理解していても、なかなか前に進めることができない状況。そんな時は、newjiのコストダウン自動化機能で大きく利益貢献しよう!
(Β版非公開)