- お役立ち記事
- Utilizing digital twins to realize smart manufacturing
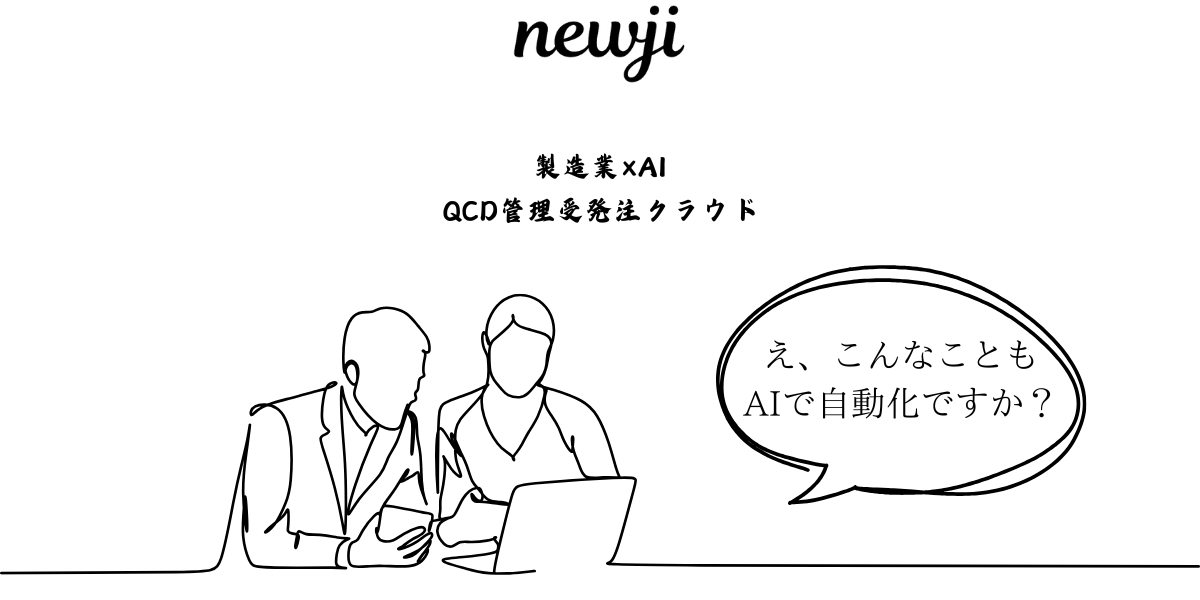
Utilizing digital twins to realize smart manufacturing
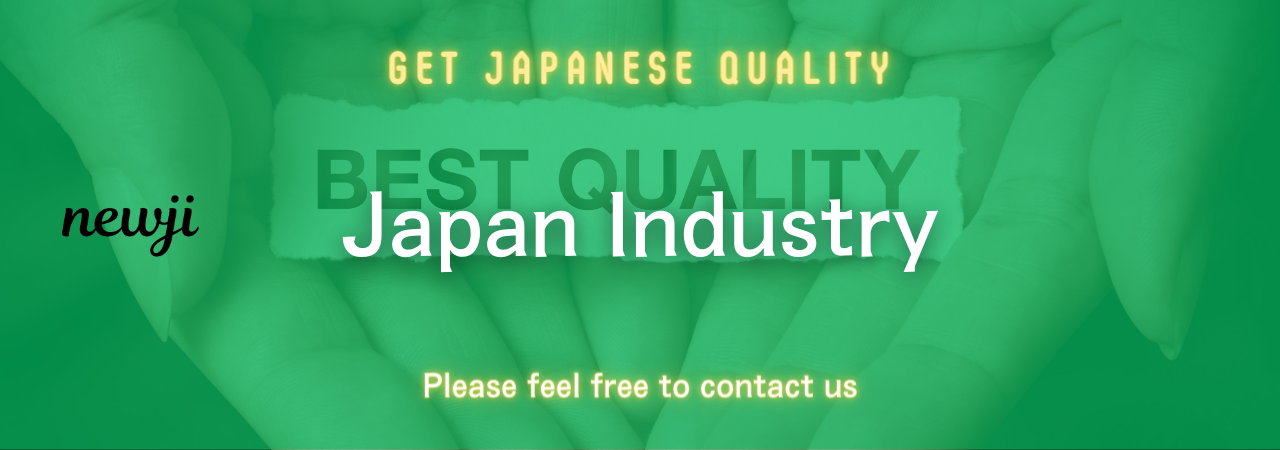
目次
Understanding Digital Twins
Digital twins are virtual replicas of physical systems or products used in various industries to simulate real-world scenarios, providing valuable insights and optimizing processes.
These digital replicas enable the monitoring, analysis, and predictive insights into how a product or system will perform throughout its lifecycle.
In smart manufacturing, digital twins are becoming increasingly crucial as they facilitate real-time data exchange and decision-making, enhancing efficiency and productivity.
Traditionally, creating an exact replica of a manufacturing setup for testing and optimization was time-consuming and expensive.
With digital twins, manufacturers can create virtual models to test what-if scenarios without physical changes in the manufacturing plant.
How Digital Twins Work
Digital twins function by leveraging data from various sources, such as IoT sensors and ERP systems, to create a comprehensive model of a product, process, or system.
This model is then used to simulate different conditions and predict outcomes.
The integration of AI and machine learning allows digital twins to evolve and adapt based on new data, providing a continuously improving and accurate depiction of the physical counterpart.
In manufacturing, digital twins typically incorporate data from different phases of production, including design, assembly, and maintenance.
This holistic approach ensures that potential issues are identified early and costs are minimized by optimizing processes before any physical changes are made.
Benefits of Digital Twins in Smart Manufacturing
Enhanced Predictive Maintenance
One of the most significant advantages of using digital twins in manufacturing is enhanced predictive maintenance.
By analyzing the digital twin’s data, manufacturers can predict when machinery needs maintenance, preventing unexpected breakdowns and costly downtime.
This proactive approach not only extends the lifespan of machinery but also improves productivity by keeping all equipment running smoothly.
Increased Efficiency and Productivity
Digital twins allow manufacturers to optimize their operations through real-time monitoring and analysis.
This leads to more efficient use of resources, reduced waste, and improved production processes.
By continuously testing and refining production methods within the digital twin, manufacturers can implement the best strategies in the physical world, significantly boosting productivity.
Improved Product Development
Incorporating digital twins in the product development phase enables manufacturers to test various designs and adjustments without the costly process of physically building prototypes.
The digital twin can simulate how a product will perform under different conditions, allowing for precise refinement and innovation.
This accelerates the product development cycle and helps deliver high-quality products to the market faster.
Challenges in Implementing Digital Twins
Data Integration
Creating a fully functional digital twin requires an extensive integration of diverse data sources.
Manufacturers need to ensure seamless connectivity between IoT devices, cloud computing systems, and operational technologies.
Data integration challenges can arise from incompatible systems and data silos, hindering the effectiveness of a digital twin.
High Initial Investment
Setting up digital twins involves significant initial costs.
This includes investing in advanced technology, software, and the skilled personnel needed to develop and maintain the digital model.
While the long-term benefits often outweigh these costs, the substantial upfront investment may deter smaller manufacturers.
Future of Digital Twins in Manufacturing
Integration with Artificial Intelligence
As technology advances, the integration of AI with digital twins will become more prevalent, enabling even more intelligent and automated systems.
AI can enhance the predictive capabilities of digital twins by providing deeper insights and automating decision-making processes, leading to smarter manufacturing systems.
Expansion Beyond Manufacturing
While digital twins are revolutionizing the manufacturing industry, their potential extends to other sectors like healthcare, transportation, and urban planning.
As digital twins evolve, they will likely play an integral role in shaping a range of industries beyond just manufacturing.
Digital twins represent a transformative approach in the pursuit of smart manufacturing.
By utilizing these virtual models, manufacturers can achieve higher efficiency, enhanced productivity, and better-quality products.
While challenges exist, the ongoing advancements in technology will likely address these hurdles, paving the way for widespread adoption across various industries.
Embracing digital twins may very well be the blueprint for a successful future in manufacturing.
資料ダウンロード
QCD調達購買管理クラウド「newji」は、調達購買部門で必要なQCD管理全てを備えた、現場特化型兼クラウド型の今世紀最高の購買管理システムとなります。
ユーザー登録
調達購買業務の効率化だけでなく、システムを導入することで、コスト削減や製品・資材のステータス可視化のほか、属人化していた購買情報の共有化による内部不正防止や統制にも役立ちます。
NEWJI DX
製造業に特化したデジタルトランスフォーメーション(DX)の実現を目指す請負開発型のコンサルティングサービスです。AI、iPaaS、および先端の技術を駆使して、製造プロセスの効率化、業務効率化、チームワーク強化、コスト削減、品質向上を実現します。このサービスは、製造業の課題を深く理解し、それに対する最適なデジタルソリューションを提供することで、企業が持続的な成長とイノベーションを達成できるようサポートします。
オンライン講座
製造業、主に購買・調達部門にお勤めの方々に向けた情報を配信しております。
新任の方やベテランの方、管理職を対象とした幅広いコンテンツをご用意しております。
お問い合わせ
コストダウンが利益に直結する術だと理解していても、なかなか前に進めることができない状況。そんな時は、newjiのコストダウン自動化機能で大きく利益貢献しよう!
(Β版非公開)