- お役立ち記事
- Vibration monitoring of rotating equipment that leaders of equipment management departments in the steel industry should know about
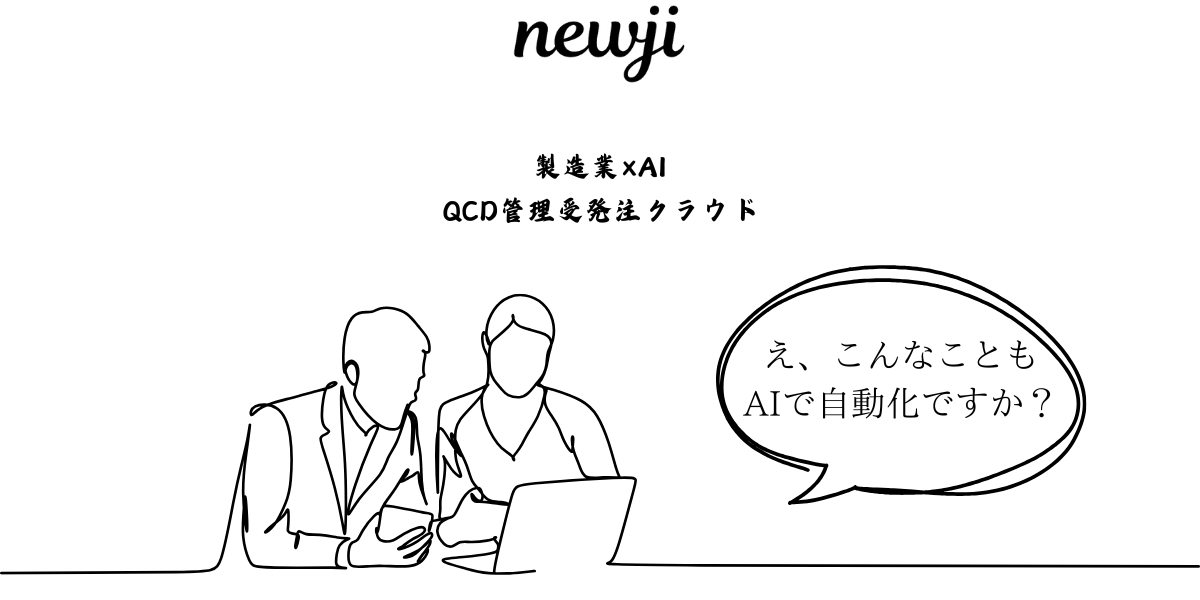
Vibration monitoring of rotating equipment that leaders of equipment management departments in the steel industry should know about
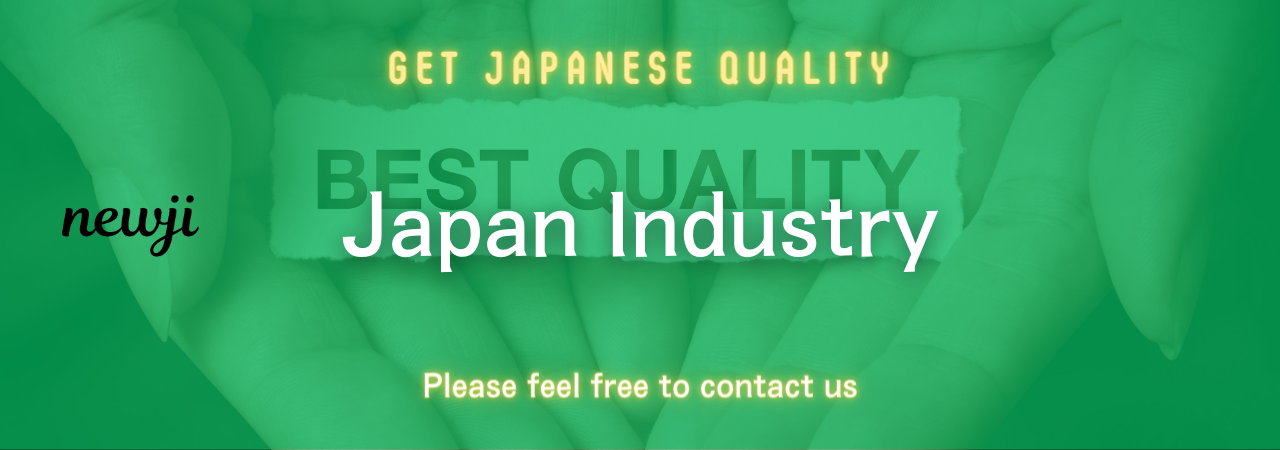
目次
Understanding Vibration Monitoring
Vibration monitoring is an essential technique used in maintenance and equipment management, especially in the steel industry.
It involves measuring the vibrations produced by rotating equipment to assess their condition and performance.
By detecting changes in vibration patterns, maintenance teams can identify potential faults before they lead to equipment failure.
Why Is Vibration Monitoring Important?
In the steel industry, equipment like motors, pumps, and fans are crucial to the production process.
Unexpected breakdowns in these systems can result in significant production delays and financial losses.
Vibration monitoring helps prevent these issues by providing early warnings of machinery problems.
Reducing downtime is one of the main benefits of vibration monitoring.
By understanding when and why equipment might fail, managers can schedule maintenance during planned downtimes, minimizing disruptions.
This proactive approach saves both time and money.
Basic Principles of Vibration Monitoring
Vibration occurs in rotating equipment due to imbalances in the moving parts.
When a component is misaligned, worn, or damaged, it causes abnormal vibrations.
Vibration monitoring involves the use of sensors to detect these irregularities.
Sensors measure different parameters such as velocity, acceleration, and displacement.
These measurements are used to create vibration signatures or patterns which are then analyzed for any deviations from the norm.
Even the slightest change in these signatures can indicate potential issues.
Types of Sensors Used in Vibration Monitoring
There are several types of sensors used in vibration monitoring.
Accelerometers are among the most common, as they are capable of measuring the rate of change of velocity.
They are typically mounted directly on the equipment.
Velocity sensors, another useful type, measure the speed of vibration.
They are helpful in detecting moderate-frequency vibrations and are often used alongside accelerometers.
Displacement sensors, on the other hand, are used to measure the distance an object has moved from its normal position.
They are particularly useful in detecting low-frequency vibrations.
Data Analysis in Vibration Monitoring
Once vibration data is collected, it must be carefully analyzed.
This involves comparing the collected data with baseline readings or industry standards.
Tools like Fast Fourier Transform (FFT) are often used in the analysis process.
FFT helps in breaking down complex vibration signals into simpler parts.
This simplification makes it easier to identify specific issues such as unbalance, misalignment, or resonance.
By identifying these problems early, corrective actions can be taken promptly.
Interpreting Vibration Monitoring Results
Identifying the source of abnormal vibrations requires expertise and experience.
It’s important to consider factors like the location of the sensor and the operating conditions of the equipment.
Variations in these factors can affect the vibration readings.
In some cases, vibration monitoring might indicate wear and tear or alignment issues which are easily corrected.
In other situations, it may signal more serious problems such as bearing failures, which would require more intensive intervention.
Regularly reviewing vibration data also aids in predicting future failures.
This analysis enables maintenance teams to prepare appropriately, ensuring replacement parts and resources are available when necessary.
Implementing Vibration Monitoring Systems
Implementing an effective vibration monitoring system requires careful planning.
The first step is to identify the critical equipment in the production process.
These are the machines that would cause the most disruption if they failed.
Next, select the appropriate sensors based on the equipment and the type of measurements needed.
Regular calibration is important to ensure the sensors provide accurate data.
Effective training for maintenance staff is also crucial.
Staff should be knowledgeable about the vibration monitoring techniques and tools, enabling them to make accurate interpretations and timely decisions.
Maintaining a Vibration Monitoring System
Once a system is in place, regular maintenance is necessary to keep it functioning optimally.
This includes periodic sensor checks and recalibration as needed.
Additionally, the systems should be updated to integrate new technologies that improve data collection and analysis.
Invest in advanced software that provides real-time monitoring and automated alerts.
Such features enable quick responses to any vibration abnormalities, further reducing the risk of equipment failure.
Challenges in Vibration Monitoring
While vibration monitoring offers many advantages, it also presents several challenges.
Firstly, it requires an upfront investment in equipment and training which might be costly.
However, these costs are generally offset by the savings from prevented downtimes and maintenance savings.
Another challenge is ensuring accurate interpretation of data.
This requires skilled technicians with experience in diagnostics and equipment maintenance.
Lastly, minimizing false alarms while capturing genuine threats can be difficult.
This is where advanced software analytics and continuous refinement of the monitoring system play key roles.
Conclusion
For leaders in equipment management departments within the steel industry, understanding and implementing vibration monitoring is vital.
It not only helps in preventing costly failures but also optimizes the efficiency and lifespan of critical equipment.
By investing in the right technology and training, leaders can ensure their teams are well-equipped to handle any challenges that arise.
In a competitive industry, staying proactive with maintenance strategies like vibration monitoring can make all the difference.
資料ダウンロード
QCD調達購買管理クラウド「newji」は、調達購買部門で必要なQCD管理全てを備えた、現場特化型兼クラウド型の今世紀最高の購買管理システムとなります。
ユーザー登録
調達購買業務の効率化だけでなく、システムを導入することで、コスト削減や製品・資材のステータス可視化のほか、属人化していた購買情報の共有化による内部不正防止や統制にも役立ちます。
NEWJI DX
製造業に特化したデジタルトランスフォーメーション(DX)の実現を目指す請負開発型のコンサルティングサービスです。AI、iPaaS、および先端の技術を駆使して、製造プロセスの効率化、業務効率化、チームワーク強化、コスト削減、品質向上を実現します。このサービスは、製造業の課題を深く理解し、それに対する最適なデジタルソリューションを提供することで、企業が持続的な成長とイノベーションを達成できるようサポートします。
オンライン講座
製造業、主に購買・調達部門にお勤めの方々に向けた情報を配信しております。
新任の方やベテランの方、管理職を対象とした幅広いコンテンツをご用意しております。
お問い合わせ
コストダウンが利益に直結する術だと理解していても、なかなか前に進めることができない状況。そんな時は、newjiのコストダウン自動化機能で大きく利益貢献しよう!
(Β版非公開)