- お役立ち記事
- Visualizing Production Lines with Advanced Sensor Networks
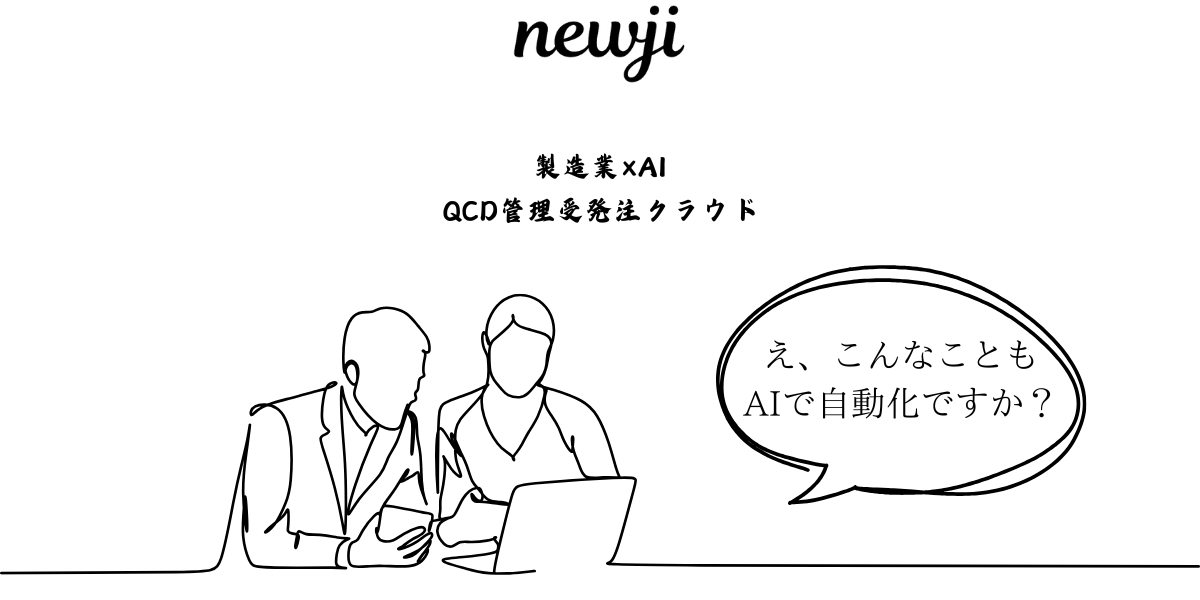
Visualizing Production Lines with Advanced Sensor Networks
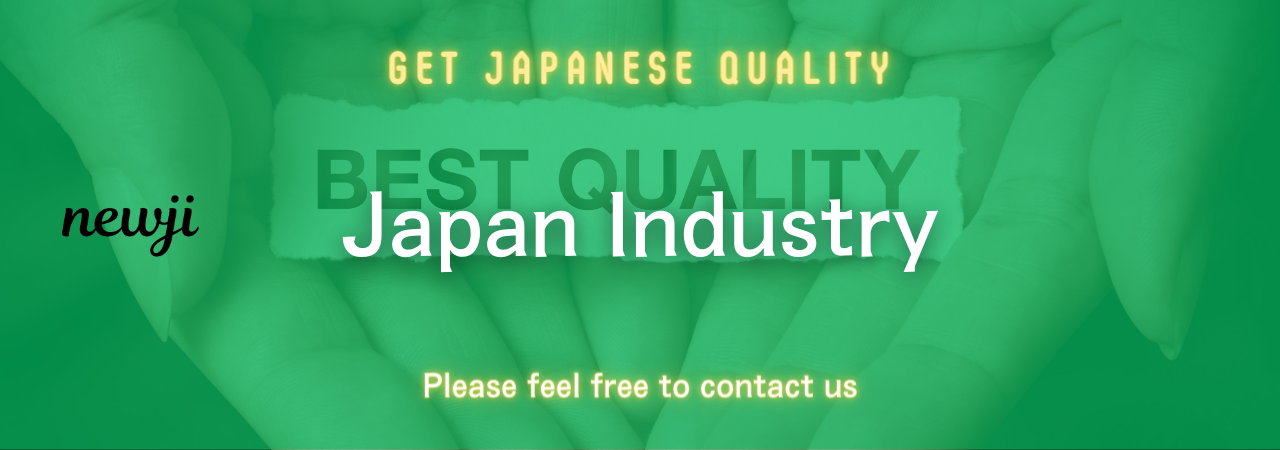
In today’s ever-evolving manufacturing landscape, the integration of advanced sensor networks for visualizing production lines has become pivotal. By harnessing these cutting-edge technologies, industries can not only streamline operations but also enhance productivity and safety. Understanding how these sensor networks work and their benefits is essential for anyone looking to stay ahead in the manufacturing arena.
目次
What Are Advanced Sensor Networks?
Advanced sensor networks are systems comprised of multiple sensor nodes, each capable of collecting, processing, and transmitting data. These sensors monitor various parameters like temperature, pressure, humidity, and vibration. When implemented in a manufacturing setting, they provide real-time data about production processes.
These sensors are interconnected, often wirelessly, to create a network. This network continuously feeds data back to a central system where it is analyzed and visualized. The visualization aspect makes it easy for plant managers and operators to understand what’s happening on the production line at any given moment.
How Do Sensor Networks Work in Production Lines?
To grasp how sensor networks function in production lines, it’s essential to understand both the hardware and software components involved.
Hardware Components
The hardware includes a variety of sensors strategically placed throughout the production line. For instance, temperature sensors might be installed near machinery that generates heat. Pressure sensors might be located where fluids are transported. Each sensor collects data pertinent to its environment and sends this data to a central receiver.
Software Components
On the software side, advanced algorithms and machine learning models analyze the incoming data. This analysis helps identify patterns, detect anomalies, and predict potential issues before they escalate. Visualization software then turns this analyzed data into easy-to-understand charts, graphs, and dashboards.
Benefits of Visualizing Production Lines
Integrating advanced sensor networks in production lines offers a multitude of benefits. These range from operational efficiencies to enhanced safety measures.
Improved Operational Efficiency
Sensor networks enable real-time monitoring, which means any issues can be detected and addressed immediately. This reduces downtime and ensures that the production line operates smoothly. For example, if a machine begins to overheat, the system can alert maintenance teams to take corrective action before a breakdown occurs.
Enhanced Quality Control
The precise data collected by sensors allows for better quality control. Any variations from the standard can be quickly identified and corrected. This ensures that the final product meets quality standards consistently. Additionally, historical data can be analyzed to improve production processes over time.
Increased Safety
Safety is a critical concern in any manufacturing environment. Sensor networks help monitor conditions that could be hazardous. For example, sensors can detect gas leaks or identify malfunctioning equipment that could pose safety risks. Immediate alerts can be sent to ensure that necessary actions are taken to protect workers.
Challenges and Solutions
While the advantages are clear, implementing advanced sensor networks isn’t without challenges. Understanding these obstacles and how to overcome them is crucial for successful integration.
Cost of Implementation
One of the primary challenges is the cost associated with installing and maintaining these networks. While the initial investment can be high, the long-term benefits, such as reduced downtime and improved product quality, often outweigh the costs. Opting for scalable and modular sensor solutions can also help manage expenses.
Data Management
The sheer volume of data generated by sensor networks can be overwhelming. Efficient data management systems are necessary to handle this influx. Investing in cloud storage solutions and robust data analytics platforms can help streamline data processing and ensure valuable insights aren’t lost in the noise.
Integration with Existing Systems
Another challenge is integrating sensor networks with existing manufacturing systems. Compatibility issues can arise, making it difficult to achieve a seamless integration. Working with experienced vendors who offer customizable solutions can alleviate these concerns. Conducting thorough testing before full-scale implementation ensures that any integration issues are identified and resolved early.
The Future of Sensor Networks in Manufacturing
The future looks promising for the use of advanced sensor networks in manufacturing. As technology continues to evolve, we can expect these networks to become even more sophisticated and integrated.
Advancements in AI and Machine Learning
With the ongoing advancements in artificial intelligence (AI) and machine learning, sensor networks will become smarter. They’ll be able to make more accurate predictions and provide actionable insights, taking automation and efficiency to new levels.
Expansion of IoT
The Internet of Things (IoT) will also play a significant role. More devices will be connected, leading to even more comprehensive data collection. This interconnectedness will enable more detailed monitoring and control of production lines.
Sustainability Initiatives
As industries increasingly focus on sustainability, sensor networks will help monitor and reduce energy consumption, waste, and emissions. This will not only help companies comply with environmental regulations but also contribute to broader sustainability goals.
Integrating advanced sensor networks for visualizing production lines is a transformative step for modern manufacturing. It brings a host of benefits, from operational efficiency and quality control to enhanced safety. While challenges exist, they can be overcome with the right strategies and solutions. As technology progresses, the capabilities of these networks will continue to expand, heralding a future of even greater innovation and efficiency in manufacturing.
資料ダウンロード
QCD調達購買管理クラウド「newji」は、調達購買部門で必要なQCD管理全てを備えた、現場特化型兼クラウド型の今世紀最高の購買管理システムとなります。
ユーザー登録
調達購買業務の効率化だけでなく、システムを導入することで、コスト削減や製品・資材のステータス可視化のほか、属人化していた購買情報の共有化による内部不正防止や統制にも役立ちます。
NEWJI DX
製造業に特化したデジタルトランスフォーメーション(DX)の実現を目指す請負開発型のコンサルティングサービスです。AI、iPaaS、および先端の技術を駆使して、製造プロセスの効率化、業務効率化、チームワーク強化、コスト削減、品質向上を実現します。このサービスは、製造業の課題を深く理解し、それに対する最適なデジタルソリューションを提供することで、企業が持続的な成長とイノベーションを達成できるようサポートします。
オンライン講座
製造業、主に購買・調達部門にお勤めの方々に向けた情報を配信しております。
新任の方やベテランの方、管理職を対象とした幅広いコンテンツをご用意しております。
お問い合わせ
コストダウンが利益に直結する術だと理解していても、なかなか前に進めることができない状況。そんな時は、newjiのコストダウン自動化機能で大きく利益貢献しよう!
(Β版非公開)