- お役立ち記事
- TPMの原則と実践: 製造業サプライチェーンにおける設備保全と生産能力維持のための方法論
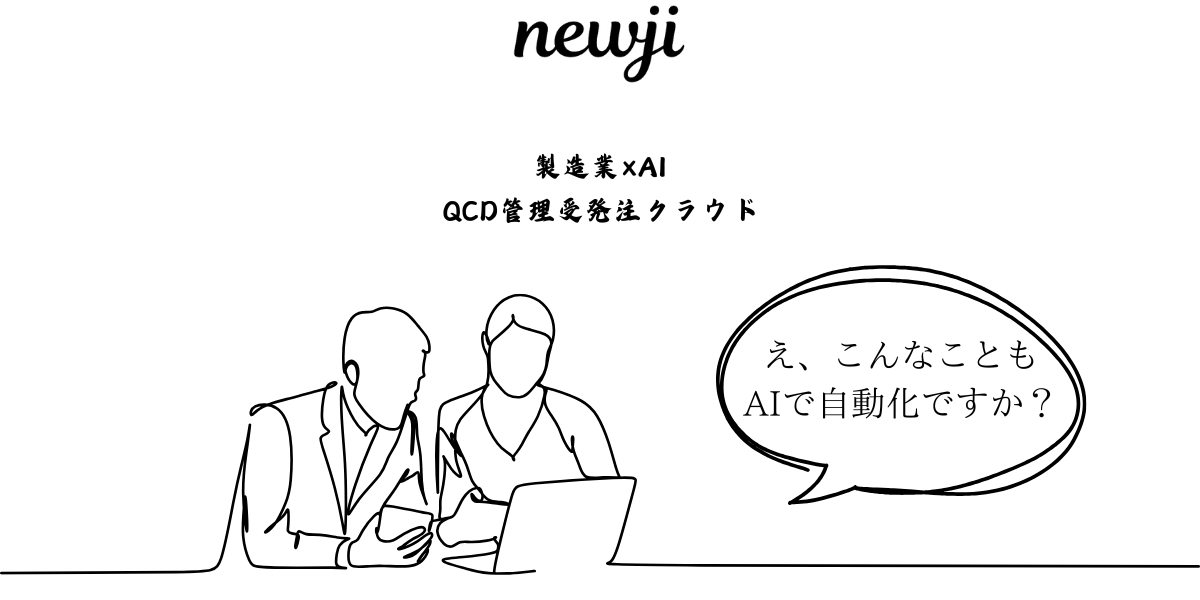
TPMの原則と実践: 製造業サプライチェーンにおける設備保全と生産能力維持のための方法論
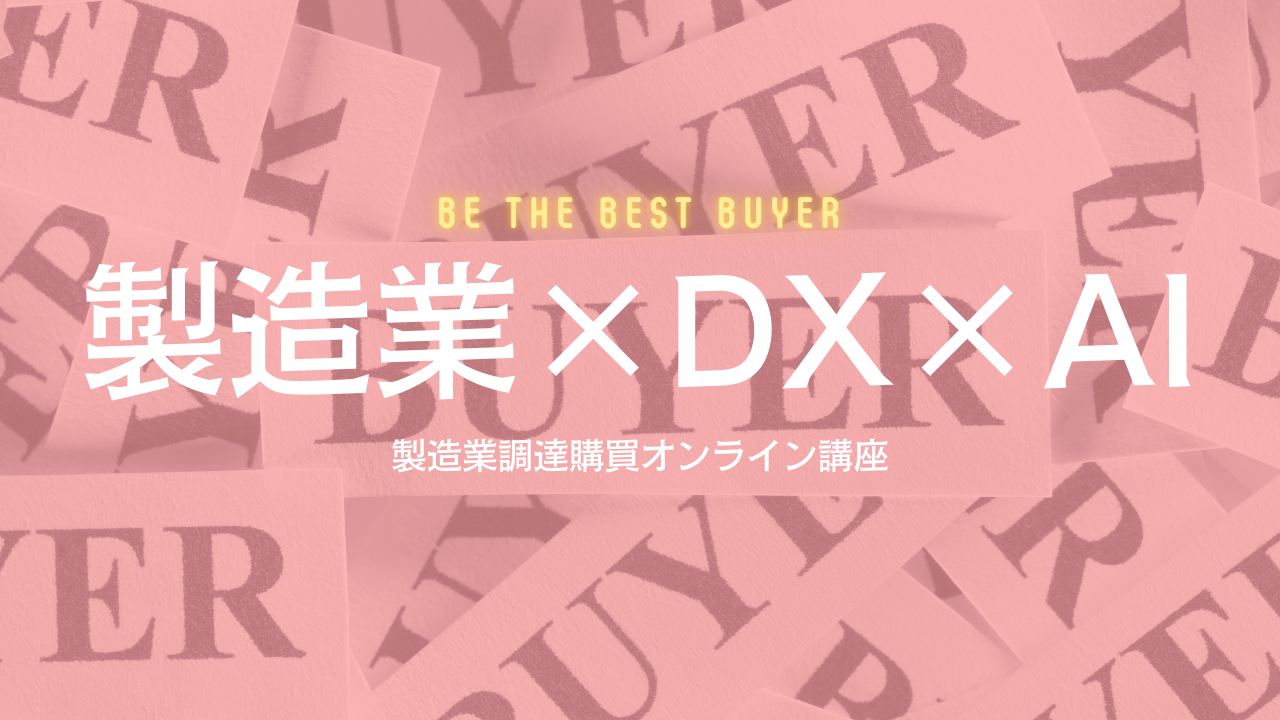
目次
TPMとは何か?その基本的な原則と目的
TPM(Total Productive Maintenance:全員参加の生産保全)とは、設備の生産性を最大限に発揮させるために、現場の全員が主体的に保全活動に取り組む手法です。
TPMの目的は、設備の故障やロスを徹底的に排除し、設備総合効率(OEE)を向上させることにあります。
そのために、「個別改善」「自主保全」「計画保全」「教育訓練」「初期流動管理」「品質保全」「安全衛生」「事務間接部門」の8本の柱で活動を進めていきます。
TPMの8本の柱とその実践方法
1. 個別改善:設備の弱点を見つけ出し、改善を図る活動です。
ロスの見える化、改善提案の実施、改善効果の確認などを行います。
2. 自主保全:オペレーターによる日常的な点検・清掃・給油などの保全活動です。
異常の早期発見・早期対応、設備の劣化防止を目的としています。
3. 計画保全:設備の故障を未然に防ぐための予防保全活動です。
保全計画の立案、予防保全の実施、保全履歴の管理などを行います。
4. 教育訓練:保全技能の向上と多能工化を目指した人材育成活動です。
保全スキルマップの作成、教育訓練計画の立案・実施、スキル認定などを行います。
5. 初期流動管理:新規設備の立ち上げロスを最小化する活動です。
設備導入前の検討、導入時の支援、立ち上げ後のフォローなどを行います。
6. 品質保全:不良や品質トラブルを未然に防止する活動です。
品質管理工程図の作成、品質監査の実施、品質改善活動などを行います。
7. 安全衛生:労働災害のリスクを排除し、安全で快適な職場環境を実現する活動です。
リスクアセスメントの実施、安全教育の徹底、5Sの推進などを行います。
8. 事務間接部門:生産部門を支援し、業務の効率化を図る間接部門の活動です。
情報システムの整備、業務プロセスの改善、サプライチェーンの最適化などを行います。
TPMの推進体制と PDCAサイクル
TPMを成功させるためには、トップダウンとボトムアップのバランスが重要です。
経営層のリーダーシップのもと、現場の自主性を尊重した推進体制を構築する必要があります。
また、TPMの活動はPDCAサイクルを回しながら継続的に改善していくことが求められます。
計画(Plan)、実行(Do)、評価(Check)、改善(Act)のサイクルを繰り返し、活動のレベルアップを図っていきます。
スマートファクトリー時代におけるTPMの進化
IoTやAIなどの新しい技術の登場により、製造業のあり方は大きく変化しつつあります。
スマートファクトリーの実現に向けて、設備保全の分野でもデジタル化が進んでいます。
設備のセンシング技術の高度化、予知保全システムの導入、保全業務の自動化・省人化など、TPMの手法もこれらの技術を取り入れながら進化しています。
ただし、技術だけでなく、現場の知恵と経験を活かすことが重要であることに変わりはありません。
まとめ: TPMの本質は現場力の強化
TPMの本質は、現場の全員が設備を大切にし、設備の生産性を高めていくことにあります。
そのためには、一人ひとりが主体的に考え、行動することが求められます。
TPMの活動を通じて、現場の自主性と改善力を高めていくことが、製造業の競争力強化につながります。
新しい技術を取り入れながらも、現場力を大切にするTPMの考え方は、これからも製造業の発展に貢献していくでしょう。
資料ダウンロード
QCD調達購買管理クラウド「newji」は、調達購買部門で必要なQCD管理全てを備えた、現場特化型兼クラウド型の今世紀最高の購買管理システムとなります。
ユーザー登録
調達購買業務の効率化だけでなく、システムを導入することで、コスト削減や製品・資材のステータス可視化のほか、属人化していた購買情報の共有化による内部不正防止や統制にも役立ちます。
NEWJI DX
製造業に特化したデジタルトランスフォーメーション(DX)の実現を目指す請負開発型のコンサルティングサービスです。AI、iPaaS、および先端の技術を駆使して、製造プロセスの効率化、業務効率化、チームワーク強化、コスト削減、品質向上を実現します。このサービスは、製造業の課題を深く理解し、それに対する最適なデジタルソリューションを提供することで、企業が持続的な成長とイノベーションを達成できるようサポートします。
オンライン講座
製造業、主に購買・調達部門にお勤めの方々に向けた情報を配信しております。
新任の方やベテランの方、管理職を対象とした幅広いコンテンツをご用意しております。
お問い合わせ
コストダウンが利益に直結する術だと理解していても、なかなか前に進めることができない状況。そんな時は、newjiのコストダウン自動化機能で大きく利益貢献しよう!
(Β版非公開)