- お役立ち記事
- なぜなぜ分析の進め方と品質不良再発防止の実践
月間76,176名の
製造業ご担当者様が閲覧しています*
*2025年3月31日現在のGoogle Analyticsのデータより
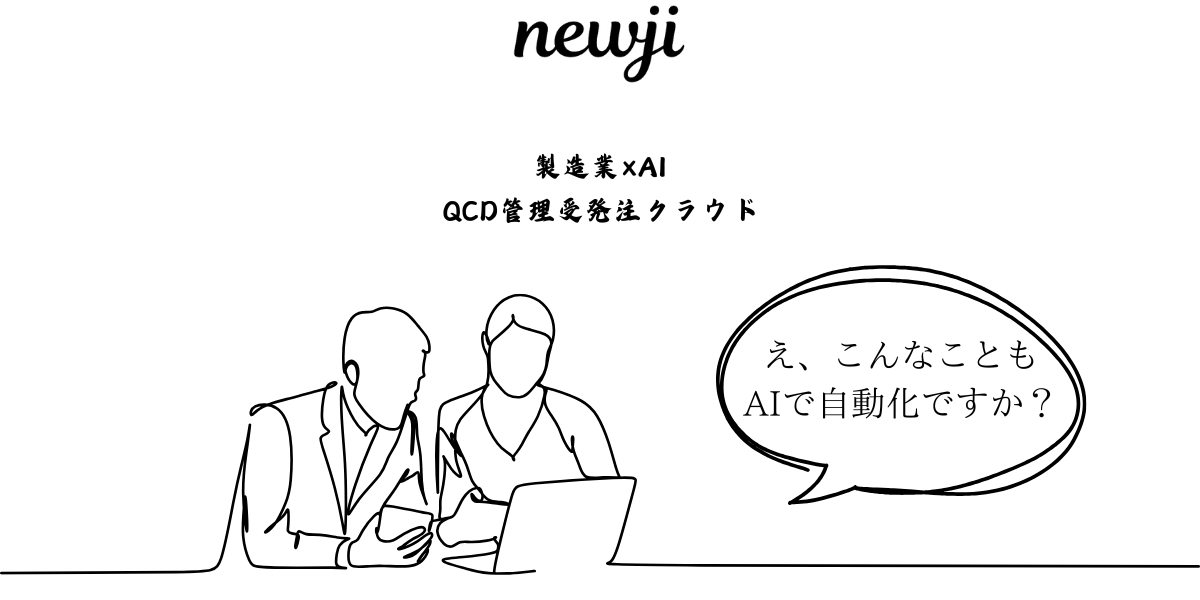
なぜなぜ分析の進め方と品質不良再発防止の実践
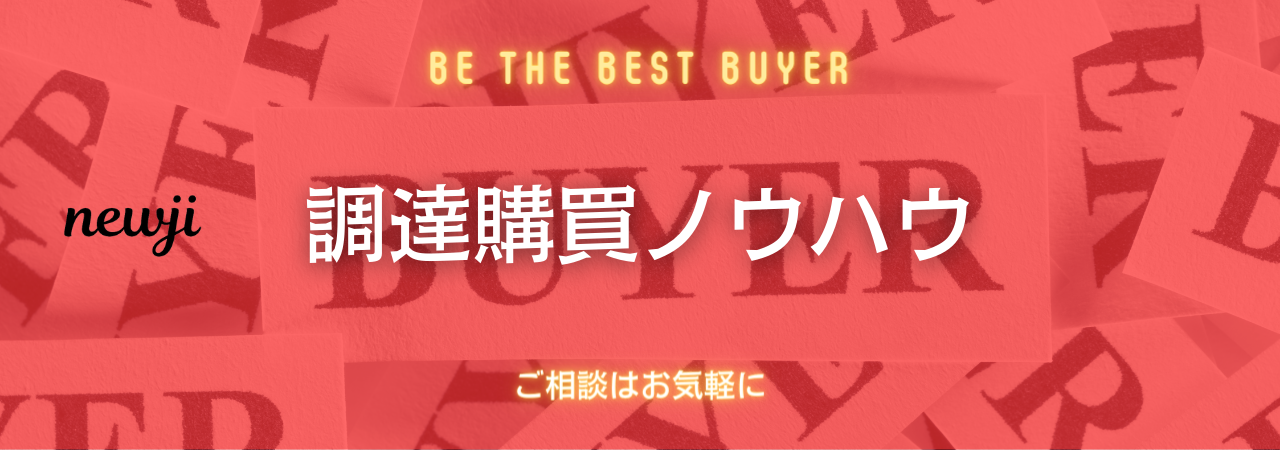
目次
なぜなぜ分析とは何か
「なぜなぜ分析」は、問題の根本原因を特定するための手法です。
製造業では、品質不良や生産トラブルが発生した際に、その原因を追究し、再発を防止するために活用されます。
この手法は、問題が発生した表面的な理由だけでなく、背後に隠された真の原因を見つけ出すのに役立ちます。
なぜなぜ分析は、問題が発生したときに「なぜそうなったのか?」を繰り返し問い続けることで、少なくとも5回程度行うことが一般的です。
これにより、表面からではわからない深層的な問題に迫ることができるのです。
なぜなぜ分析の進め方
ステップ1: 問題の明確化
最初のステップは問題を明確にすることです。
製品の不良、設備の故障、納期の遅れなど、何が問題なのかを具体的に定義します。
問題が明確にならないと、原因を特定することも困難になります。
ここでは、事実に基づき、具体的な事象として問題をとらえます。
ステップ2: 初回の「なぜ?」から始める
問題が明確になったら、なぜその問題が発生したのかを考えます。
最初の「なぜ?」には、表面的な原因が多く含まれます。
ここでしっかりと答えを出すことが重要であり、その答えが曖昧であったり、ただ形式的なものであったりしてはいけません。
具体的で、再現性がある理由を見つけることを目的とします。
ステップ3: 繰り返しの「なぜ?」を問い続ける
初回の「なぜ?」で得た答えについて、さらに「なぜ?」を問いかけます。
このプロセスを繰り返すことで徐々に深層にある真の原因に近づきます。
実際には5回繰り返すとされていますが、問題の性質によっては3回で済む場合も、10回以上かかる場合もあります。
ここでは妥協せず、本来の根本原因を見つけることが大切です。
ステップ4: 原因の仮説を検証する
なぜなぜ分析で突き止めた根本原因が本当に問題を引き起こしているのかを、データや事実に基づいて検証します。
ここでは、仮説として立てた原因が異なる視点でも合致するかどうかを確認します。
例えば、過去の類似事象や他の現場のデータを参考にすることも有効です。
ステップ5: 再発防止策の立案と実行
根本原因が特定できたら、それに対する再発防止策を立案します。
防止策は具体的で実行可能なものでなければ意味がありません。
訓練や設備の改善、プロセスの見直しなど、組織や製造ラインに適合した防止策を実施することが求められます。
なぜなぜ分析で遭遇する課題とその対策
分析の形骸化を防ぐ
なぜなぜ分析が形骸化してしまうと、その効果は大幅に減少します。
上司や関係者からの圧力で形式的に行われる場合、本来の目的である根本原因の究明は難しくなります。
これを防ぐためには、管理職が積極的に関与して分析に取り組む姿勢を見せることが重要です。
また、分析の結果や改善策について現場で継続的に議論し、実行のフィードバックを繋げる仕組みも必要です。
データが不足している問題
データが不足していると、真の原因の特定が難しくなります。
この課題に対処するには、できるだけ詳細なデータを記録し、今後の分析に活用できるようにします。
また、他のプロセスや関連部門の知見を借りることで、仮説の裏付けを行います。
コラボレーション文化を育て、部門を超えた情報共有を促進することで、データ不足の対策が可能です。
バイアスの影響を排除する
分析結果が特定のバイアスによって歪められることがあります。
個々の先入観や組織内の文化が原因で、分析が正確さを失うことも考慮しなければなりません。
客観的な視点を持つことが重要であり、一人で分析に頼るのではなく、多様な視点を取り入れます。
部門を超えたワークショップや研修を実施し、共通認識を持たせることが効果的です。
なぜなぜ分析のメリットと製造業への影響
根本原因の特定による再発防止
なぜなぜ分析により、表面的な解決策にとどまらず、根本原因を明らかにすることで、再発防止策が効果的に機能します。
これにより、同じ問題が繰り返さない仕組みを構築でき、生産効率や品質を向上させることができます。
コスト削減の効果
問題を未然に防ぐことができれば、不良品の廃棄や手直しなどのコストを削減することができます。
また、設備の故障対策や無駄な作業削減は、全体的な生産コストを下げ、企業の競争力を高めることに繋がります。
組織の学習能力の向上
なぜなぜ分析を日常的に行うことで、組織全体が問題解決に対する学習能力を高めることができます。
積極的な問題解決の意識は、職場における持続的な改善活動を促進します。
組織が学習することで、より柔軟で変化に対応できる企業風土が築かれるのです。
結論
なぜなぜ分析は、製造業において品質不良を再発させないための強力な手法です。
5回の「なぜ?」を重ねることで、深層にある問題の根本原因に辿り着くことができ、その解決策を実行することで再発防止が図れます。
また、このプロセスを通じて、組織全体が問題解決への意識を向上させ、生産効率やコスト削減、企業競争力の強化に寄与します。
昭和のアナログ的な考え方から抜け出し、データに基づく根本解決を目指す近代的な手法として、なぜなぜ分析を活用していきましょう。
資料ダウンロード
QCD管理受発注クラウド「newji」は、受発注部門で必要なQCD管理全てを備えた、現場特化型兼クラウド型の今世紀最高の受発注管理システムとなります。
ユーザー登録
受発注業務の効率化だけでなく、システムを導入することで、コスト削減や製品・資材のステータス可視化のほか、属人化していた受発注情報の共有化による内部不正防止や統制にも役立ちます。
NEWJI DX
製造業に特化したデジタルトランスフォーメーション(DX)の実現を目指す請負開発型のコンサルティングサービスです。AI、iPaaS、および先端の技術を駆使して、製造プロセスの効率化、業務効率化、チームワーク強化、コスト削減、品質向上を実現します。このサービスは、製造業の課題を深く理解し、それに対する最適なデジタルソリューションを提供することで、企業が持続的な成長とイノベーションを達成できるようサポートします。
製造業ニュース解説
製造業、主に購買・調達部門にお勤めの方々に向けた情報を配信しております。
新任の方やベテランの方、管理職を対象とした幅広いコンテンツをご用意しております。
お問い合わせ
コストダウンが利益に直結する術だと理解していても、なかなか前に進めることができない状況。そんな時は、newjiのコストダウン自動化機能で大きく利益貢献しよう!
(β版非公開)