- お役立ち記事
- 技術者に必要な原価計算の基礎知識とコストダウンへの応用
技術者に必要な原価計算の基礎知識とコストダウンへの応用
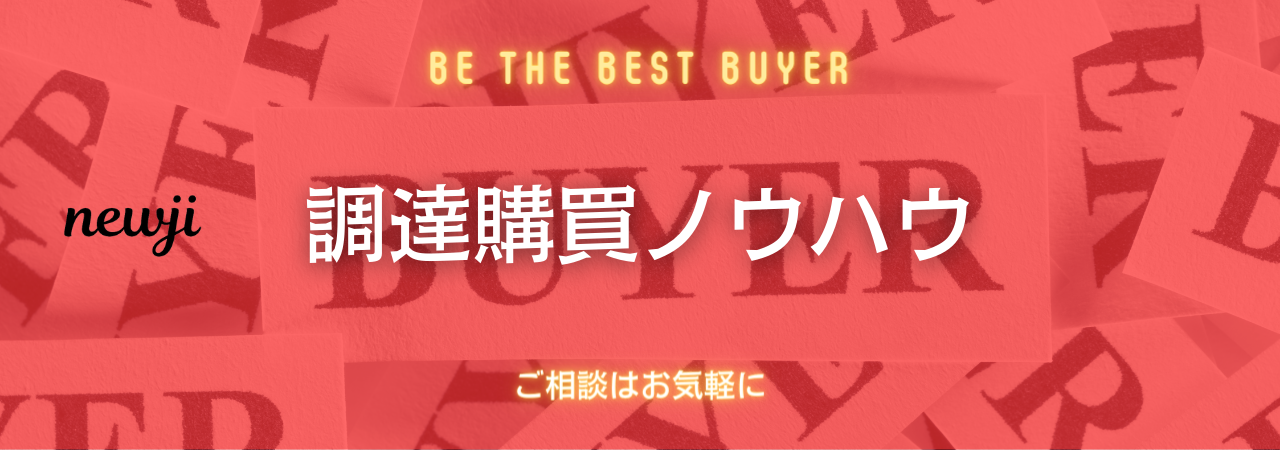
目次
技術者に必要な原価計算の基礎知識とは
製造業における技術者にとって、原価計算は非常に重要なスキルの一つです。
原価計算は製品開発から生産、出荷に至るまでの全プロセスにおいて、コストを明確化し、利益を最適化するための基盤となります。
原価は製造業において売上高と同じくらいの重要度があり、それを理解することでコストダウンや効率化に貢献できます。
では、技術者に欠かせない原価計算の基礎知識について詳しく見ていきましょう。
原価の基本構成
原価は大きく分けると製造原価と非製造原価に分類されます。
製造原価には材料費、労務費、経費が含まれます。
材料費とは、製品を製造するために必要な原材料や部品のコストです。
労務費は製造工程に携わる作業者の給与や賃金などを指します。
経費は製造に関わる設備の維持費や間接費を含みます。
非製造原価は販売管理費や一般管理費を指し、販売活動や会社の管理活動にかかるコストです。
これらの原価を正確に把握することが、製品の価格設定やコストダウンの施策において重要となります。
直接原価計算と全製造原価計算
製造原価の計算方法として代表的なのが、直接原価計算と全製造原価計算です。
直接原価計算では、製品やプロジェクトごとに直接的に関連する変動費のみを原価として捉え、固定費は管理費として別途管理します。
これにより、製品単位での利益貢献度を評価しやすくなり、新規製品の採算性を迅速に検討できるメリットがあります。
一方、全製造原価計算は、すべての製造コストを製品に割り当てる方法です。
変動費だけでなく固定費も含めて製品原価を算出するため、製品別の正確な原価管理が可能です。
標準原価計算と実際原価計算
標準原価計算は、あらかじめ設定された標準の原価を基準にして、それに基づき実際の生産活動を評価していく手法です。
標準原価は、材料費や労務費、時間当たりの生産量などの設定に基づき決定されます。
設定された標準に対して実際の数値を比較し、差異分析を行うことで、生産現場の問題点や改善点を特定できます。
実際原価計算は、実際に発生したすべてのコストを集計し原価を算出します。
現場でのリアルタイムな原価情報を提供し、詳細な原価分析に適していますが、コスト管理に時間と労力がかかるという課題もあります。
原価計算を用いたコストダウンの手法
原価計算を効果的に活用することで、製造現場におけるコストダウンを推進することが可能です。
次に、具体的なコストダウンの手法をご紹介します。
製品設計の見直し
原価計算を通じて製品のコスト構造を明確にし、高いコストを占める要因を特定することができます。
これを元に、製品設計の段階で部品数の削減や材料の見直しを行うことで、製造コストを低減する設計変更を行います。
設計段階での見直しは、後工程の見直しと比べて大幅なコスト削減が期待できるため、非常に効果的です。
生産プロセスの効率化
生産現場における効率化は、製造原価の削減に直結します。
原価計算を基にした工程別のコスト分析を行い、無駄を省いたレイアウトの改善や生産ラインの統合を行います。
また、作業の標準化や自動化を進めることで、労務費や間接費を削減し、製造効率を向上させることができます。
サプライチェーンの最適化
原価計算は、調達購買においても活用できます。
供給先の見直しや複数サプライヤーからの見積もり比較により、購入価格の削減を実現します。
また、JIT(Just-In-Time)生産方式の導入により在庫を最小限に抑え、資金繰りや保管コストを低減します。
サプライヤーとの関係構築も重要です。
長期的なパートナーシップを築くことにより、より良い条件での取引や共同開発によるコスト削減が可能となります。
品質管理の徹底
品質管理の強化は、保証コストや不良品コストの削減に繋がります。
原価計算で得られたデータを活用し、品質向上活動を推進します。
具体的には、PDCAサイクルを回して品質管理の定着を図り、QCサークルなどによる従業員の意識向上を促すことも効果的です。
製造業の原価計算とコストダウンの成功事例
ここでは、製造業における原価計算とコストダウンの成功例を紹介します。
事例1:電子機器メーカーの製品設計改善
ある電子機器メーカーは、原価計算を用いて製品のコスト構造を分析し、特に高コストを占める部品を特定しました。
各部品の代替品や機能集約を進めた結果、部品単価が低減し、製品単価を約15%削減することに成功しました。
事例2:自動車部品メーカーの生産プロセス革新
自動車部品メーカーでは、生産プロセスの各工程を細分化し原価計算を行い、非効率な工程を特定しました。
工程の自動化や作業標準化を導入したことで、生産効率が大幅に向上し、年間10億円のコスト削減を達成しました。
事例3:家電メーカーのサプライチェーン改革
家電メーカーでは、原価計算を基にサプライチェーン全体を再構築しました。
パートナーシップの強化とJIT生産方式の導入により、調達コストと在庫管理コストの削減に成功し、総コストを約20%削減することができました。
製造業における原価計算とコストダウンの未来
製造業における原価計算とコストダウンは、従来の手法にとどまらず、デジタル技術の進化とともに革新が進んでいます。
製造現場はIoTやビッグデータの活用によりリアルタイムでの原価管理が進展し、AIによるデータ分析で更なるコスト削減の可能性を模索しています。
技術者に求められるのは、そこで得られる新しい情報をいかに活用し、実行に移すかという姿勢です。
未来の製造業において、原価計算とコストダウンは企業の競争力を高めるカギとなります。
柔軟な思考で現場の課題に向き合い、価値ある製品を生み出しつづけることが、技術者の使命です。
資料ダウンロード
QCD調達購買管理クラウド「newji」は、調達購買部門で必要なQCD管理全てを備えた、現場特化型兼クラウド型の今世紀最高の購買管理システムとなります。
ユーザー登録
調達購買業務の効率化だけでなく、システムを導入することで、コスト削減や製品・資材のステータス可視化のほか、属人化していた購買情報の共有化による内部不正防止や統制にも役立ちます。
NEWJI DX
製造業に特化したデジタルトランスフォーメーション(DX)の実現を目指す請負開発型のコンサルティングサービスです。AI、iPaaS、および先端の技術を駆使して、製造プロセスの効率化、業務効率化、チームワーク強化、コスト削減、品質向上を実現します。このサービスは、製造業の課題を深く理解し、それに対する最適なデジタルソリューションを提供することで、企業が持続的な成長とイノベーションを達成できるようサポートします。
オンライン講座
製造業、主に購買・調達部門にお勤めの方々に向けた情報を配信しております。
新任の方やベテランの方、管理職を対象とした幅広いコンテンツをご用意しております。
お問い合わせ
コストダウンが利益に直結する術だと理解していても、なかなか前に進めることができない状況。そんな時は、newjiのコストダウン自動化機能で大きく利益貢献しよう!
(Β版非公開)