- お役立ち記事
- なぜなぜ分析の基礎と効果的な問題解決への活かし方
月間77,185名の
製造業ご担当者様が閲覧しています*
*2025年2月28日現在のGoogle Analyticsのデータより
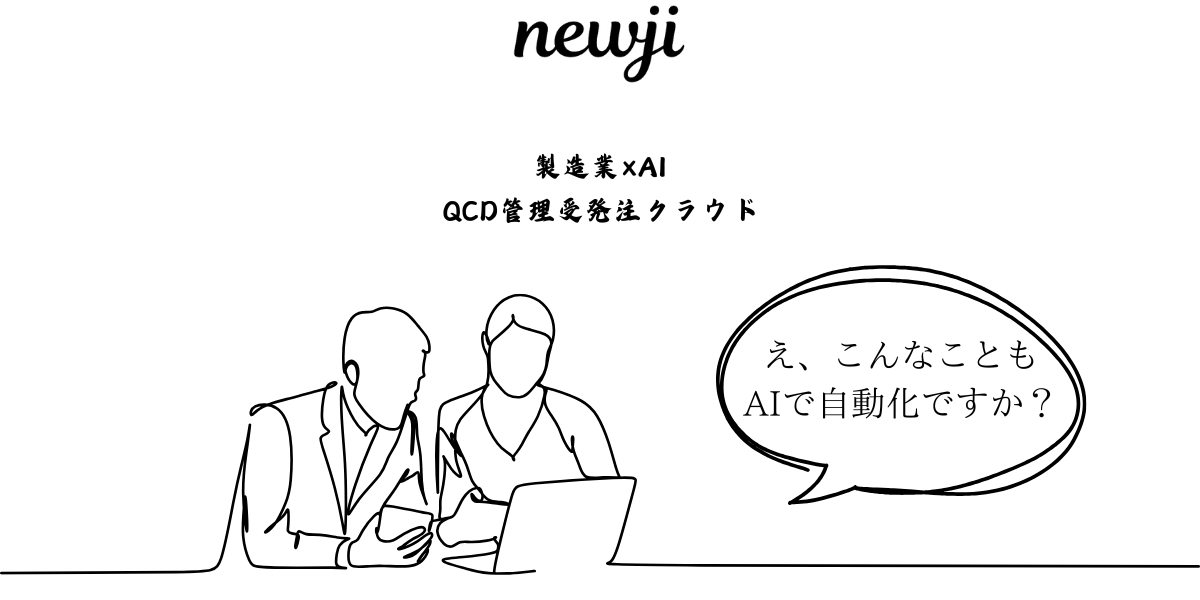
なぜなぜ分析の基礎と効果的な問題解決への活かし方
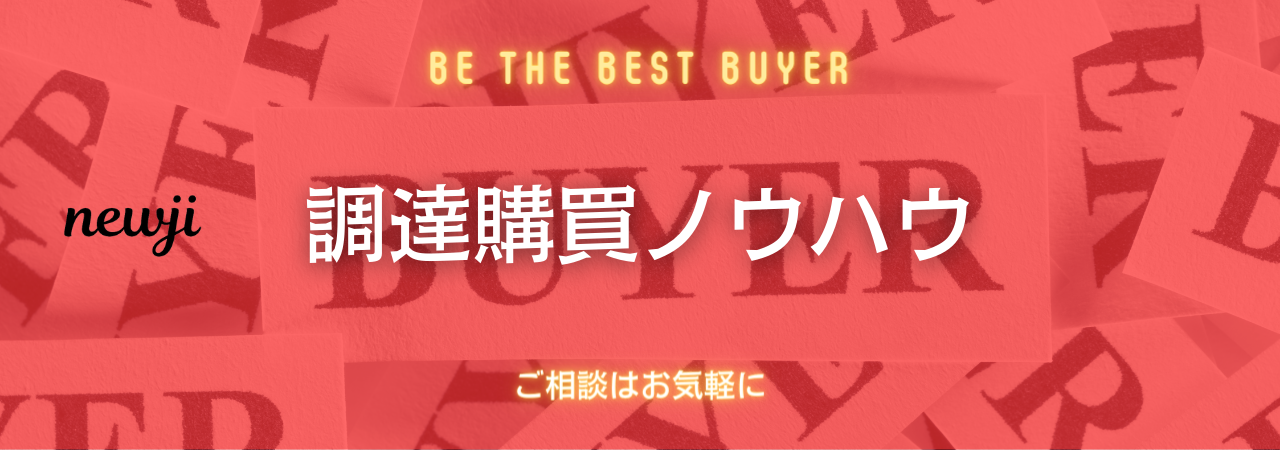
目次
なぜなぜ分析とは何か
なぜなぜ分析とは、製造業における問題解決手法の一つであり、問題の根本原因を特定するためのプロセスです。
生じた問題に対して「なぜ?」と繰り返し問いかけることで、その原因を追求していきます。
一般には5回程度の「なぜ?」を繰り返すことで、根本原因にたどり着くと考えられていますが、実際の現場では必要に応じて回数を増減することもあります。
この手法は、問題が発生した際に原因を表面的に片付けるのではなく、根本的な部分にアプローチすることによって再発防止を図ることを目的としています。
なぜなぜ分析の進め方
ステップ1:問題の明確化
まずは問題を具体的に明らかにすることが重要です。
曖昧な問題の定義で進めてしまうと、根本原因の特定が不確かになり、効果的な対策を講じることができません。
製品の不良率が上がった、納期遅れが発生したなど、現状をしっかり把握しましょう。
ステップ2:「なぜ?」を繰り返す
次に、明確にされた問題に対して「なぜ?」という問いかけを繰り返します。
例えば、「製品が不良品として出荷された」という問題であれば、「なぜ不良品が発生したのか?」という疑問からスタートします。
一つの原因を特定したら、その原因に対してさらに「なぜ?」を問いかけるプロセスを繰り返して、自分たちの知識の限界まで深掘りを続けます。
ステップ3:根本原因の特定
何度も「なぜ?」と問い続けて、これ以上問いかけても新しい原因が出てこなかったり、自分たちで直接制御できない一つの根本原因にたどり着いたら、その時点で「なぜなぜ分析」は完了とみなされます。
ただし、たどり着いた根本原因が見えてきたところで、改善可能な対策を講じてリスクの低減を図っていくことが必要です。
ステップ4:対策の実行と効果の確認
根本原因が特定されたら、具体的な対策を立てて実行します。
この時に重要なのが「対策を実施した結果として、どういった効果を期待するか」を事前に定義しておくことです。
そのためには、予想される効果を数値化できる形で設定しておくことが望ましいです。
実施後は、初期に設定した数値目標が達成されたかどうかを確認し、再度なぜなぜ分析が必要な場合もあります。
なぜなぜ分析が製造現場に与える効果
なぜなぜ分析を効果的に行うことで、製造現場には以下のような効果が期待できます。
再発防止によるコスト削減
根本原因に目を向け、問題が再び起こる前に適切な対策を講じることで、同様の問題が再発することを防ぎます。
これにより、不良品などに関連するコストを削減することができます。
プロセス改善による生産性向上
なぜなぜ分析を通じてプロセスの問題点が見つかると、それに対する改善の余地が明確になります。
結果として、製造プロセス全体の効率を上げ、生産性を向上させることが可能です。
従業員の意識向上
プロジェクトを進行する中で、従業員全員が「なぜ?」と考える習慣を身につけると、問題への感度が向上し、製品やプロセスの改善意識が高まります。
これにより、自発的に改善点を見つけ出し、提案する風土が育まれるでしょう。
アナログな製造業界でのなぜなぜ分析の活かし方
製造業界では、特にアナログな業界においてデジタル化が進んでいないことが多いですが、なぜなぜ分析はアナログな環境でも活用できる手法です。
問題定義と情報収集に紙とペンを活用
なぜなぜ分析は主に視覚的なツールとして用いられるため、問題定義やその解決プロセスを図示する際には、簡単に紙とペンを使って進行することができます。
アナログ環境下でも手軽に実施できるため、即座に始められるという利点があります。
現場でのコミュニケーションを重視
アナログ環境では、特にコミュニケーションの流れを重要視することが大切です。
なぜなぜ分析は参加者全員の知識と経験を活かすことが肝要であり、会議などの場を設けてお互いに顔を合わせながら進めることで、より深い知見と気づきを得ることができます。
なぜなぜ分析成功のためのコツ
深掘りの精度を意識
「なぜ?」と問い続ける深掘りの過程の中では、無意識に思い込みが影響して、誤った原因に到達することがあります。
そこで、異なる観点やバックグラウンドを持つメンバーがチームを組んでアプローチすることが大切です。
データの重要性を認識
冷静かつ客観的な判断を行うためには、データを根拠として使用することが不可欠です。
可能な限り、定量的なデータをもとに議論を進めることが、効果的な分析を行う鍵となります。
あえて「5回」に固執しない
「なぜなぜ分析」は5回の問いかけが標準とされていますが、状況によっては3回で十分であったり、あるいは10回以上求められることもあります。
固定概念に縛られず、状況に応じて調整する柔軟性を持ちましょう。
資料ダウンロード
QCD管理受発注クラウド「newji」は、受発注部門で必要なQCD管理全てを備えた、現場特化型兼クラウド型の今世紀最高の受発注管理システムとなります。
ユーザー登録
受発注業務の効率化だけでなく、システムを導入することで、コスト削減や製品・資材のステータス可視化のほか、属人化していた受発注情報の共有化による内部不正防止や統制にも役立ちます。
NEWJI DX
製造業に特化したデジタルトランスフォーメーション(DX)の実現を目指す請負開発型のコンサルティングサービスです。AI、iPaaS、および先端の技術を駆使して、製造プロセスの効率化、業務効率化、チームワーク強化、コスト削減、品質向上を実現します。このサービスは、製造業の課題を深く理解し、それに対する最適なデジタルソリューションを提供することで、企業が持続的な成長とイノベーションを達成できるようサポートします。
製造業ニュース解説
製造業、主に購買・調達部門にお勤めの方々に向けた情報を配信しております。
新任の方やベテランの方、管理職を対象とした幅広いコンテンツをご用意しております。
お問い合わせ
コストダウンが利益に直結する術だと理解していても、なかなか前に進めることができない状況。そんな時は、newjiのコストダウン自動化機能で大きく利益貢献しよう!
(β版非公開)