- お役立ち記事
- 成功企業に学ぶQFDの導入と効果:製造業のケーススタディ
月間76,176名の
製造業ご担当者様が閲覧しています*
*2025年3月31日現在のGoogle Analyticsのデータより
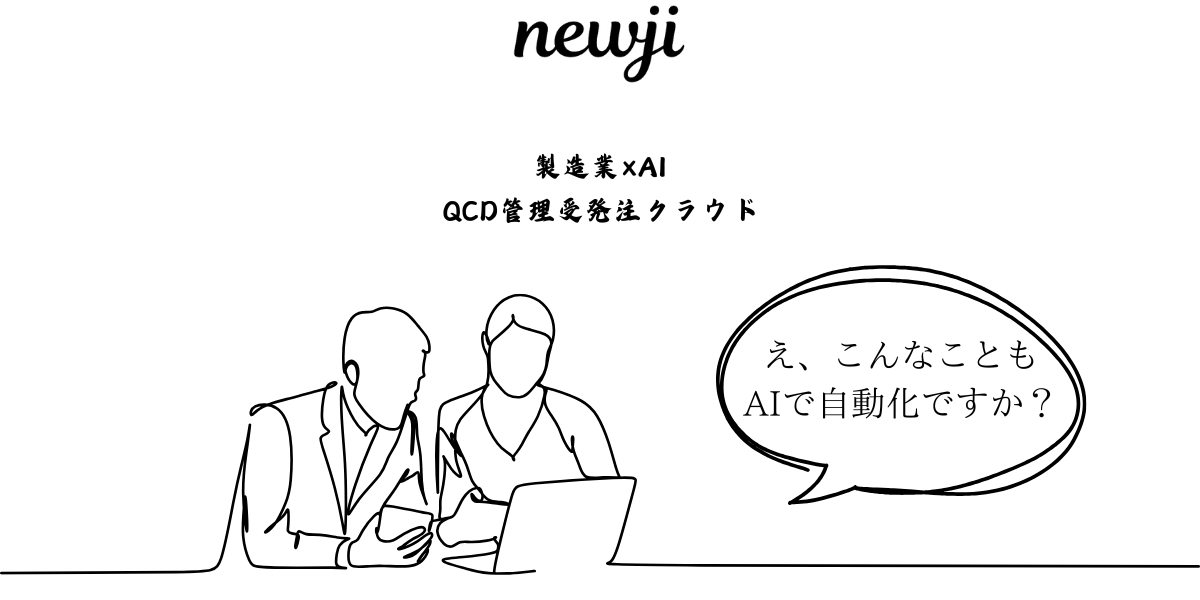
成功企業に学ぶQFDの導入と効果:製造業のケーススタディ

製造業において、製品の品質と顧客満足は企業の競争力を高める重要な要素です。
多くの企業がこれを実現するためにさまざまな品質管理手法を取り入れていますが、その中でもQFD(Quality Function Deployment)は特に効果的な方法の一つです。
この記事では、QFDの基本概念とその適用方法、さらに成功企業のケーススタディを通して、その効果について考察します。
目次
QFDとは何か?
QFDの基本概念
QFDとは、製品やサービスの設計において顧客の要求を明確に反映させる手法で、日本語では「品質機能展開」と訳されます。
この手法は、1966年に日産自動車で開発され、その後多くの企業に導入されました。
QFDの目的は、顧客のニーズを的確に理解し、そのニーズを設計や製造工程に反映させることです。
QFDの4ステップ
QFDは通常、以下の4つのステップで展開されます。
これらのステップを通じて、製品機能がシステム、サブシステム、コンポーネントといった各レベルに分解されるため、精度の高い製品設計が可能になります。
1. 製品計画(HOQ: House of Quality)
2. 部品展開
3. 製造工程計画
4. 生産計画
成功企業のQFD導入例
ここでは、いくつかの成功企業のQFD導入事例を紹介します。これらのケーススタディは、QFDの導入がどのような効果をもたらすかを具体的に示しています。
トヨタ自動車
トヨタ自動車は、QFDを製品開発プロセスに取り入れることで、市場での競争力を劇的に向上させました。
特に「HOUSE OF QUALITY」の手法を用いて、顧客の声を詳細に解析し、それを設計と製造工程に反映しました。
これにより、トヨタは「品質が高い車」のイメージを確立し、顧客満足度を大幅に向上させました。
ソニー
ソニーもまた、QFDを積極的に活用している企業の一つです。
例えば、新しいモデルのテレビを開発する際、QFDを用いて顧客が求める映像品質や音質、デザインなどを詳細に分析しました。
その結果、他社製品との差別化に成功し、市場での売上げを大幅に伸ばしました。
ホンダ
ホンダもQFDの効果を実感している企業の一例です。
バイクの新モデル開発において、QFDを用いて顧客が求める性能やデザインを反映させました。
この取り組みが奏功し、新製品は市場で高評価を受け、売上げが大幅に増加しました。
QFD導入による具体的な効果
QFDを導入することで得られる具体的な効果には以下のようなものがあります。
顧客満足度の向上
QFDは顧客の要求を直接取り入れる手法ですので、製品開発段階から顧客の期待に応えることが可能になります。
例えば、新しい製品が市場に出たときに、顧客からのフィードバックが「こんな機能が欲しかった」というポジティブなものだった場合、それはQFDがうまく機能している証拠です。
設計ミスの減少
QFDを用いることで、開発初期段階から詳しい設計仕様を確定することができ、後からの設計変更が少なくなります。
これにより、設計ミスや再設計によるコスト増加を抑えることができます。
開発期間の短縮
顧客のニーズを詳細に把握し、それを最初から製品設計に反映させることで、試行錯誤の期間を大幅に短縮することが可能です。
これにより、開発期間全体を短縮でき、市場投入までの時間を短くすることができます。
コスト削減
設計ミスの減少や再設計の必要性が少なくなることで、トータルの開発コストが削減されます。
さらに、顧客満足度が向上することで、販売数量が増加し、スケールメリットによるコスト削減も期待できます。
QFD導入のためのステップ
QFDの導入は一見難しいように感じられますが、以下のステップを踏むことでスムーズに進めることができます。
ステップ1: チームの編成
QFDを導入するための最初のステップは、プロジェクトチームの編成です。
このチームには、設計、製造、品質管理、マーケティングなど、製品開発に関わるすべての部門のメンバーを含めることが重要です。
ステップ2: 顧客の声の収集
次に、顧客からのデータを収集するステップに進みます。
インタビューやアンケート、フォーカスグループなどを通じて、顧客が求める製品の特性や機能を詳細に把握します。
ステップ3: データの分析と整理
収集したデータを用いて、顧客の声を具体的な要求に変換します。
このプロセスでは、「HOUSE OF QUALITY」を用いて要求を整理し、優先順位を付けることが多いです。
ステップ4: 設計への反映
顧客の要求を設計仕様に反映します。
このステップでは、設計チームだけでなく、製造チームとも密接に連携することが重要です。
ステップ5: 継続的なフィードバックと改善
最後に、継続的にフィードバックを得て、製品とプロセスを改善します。
QFDの効果を最大化するためには、常に顧客の声を反映し続けることが必要です。
最新の技術動向とQFD
現代の製造業では、多くの企業がデジタルトランスフォーメーション(DX)を進めており、QFDもその一部です。
AIとQFD
人工知能(AI)技術の進化により、QFDのプロセスにも変革が起きています。
例えば、AIを用いて顧客のフィードバックを自動で解析し、それを設計仕様に反映させることが可能になっています。
これにより、データ分析にかかる時間が大幅に短縮され、より迅速な開発が可能です。
IoTとQFD
IoT(Internet of Things)技術を活用することで、製品の使用状況をリアルタイムで監視し、得られたデータをQFDプロセスに取り入れることができます。
これにより、実際の使用環境に基づいた精度の高い製品改良が可能になります。
クラウド技術とQFD
クラウドベースのソリューションを活用することで、QFDプロセスを効率化することができます。
例えば、クラウド上でデータを一元管理し、関係者がどこからでもアクセス可能にすることで、コラボレーションが容易になります。
QFD(品質機能展開)は、顧客の声を製品設計や製造工程に反映させるための強力な手法です。
トヨタ自動車、ソニー、ホンダなどの成功企業の事例からも明らかなように、QFDを適切に導入することで顧客満足度の向上、設計ミスの減少、開発期間の短縮、コスト削減など、多くのメリットを享受することができます。
また、最新の技術動向を取り入れることで、QFDの効果をさらに高めることが可能です。
製造業における競争力を高めるために、ぜひQFDの導入を検討してみてください。
資料ダウンロード
QCD管理受発注クラウド「newji」は、受発注部門で必要なQCD管理全てを備えた、現場特化型兼クラウド型の今世紀最高の受発注管理システムとなります。
ユーザー登録
受発注業務の効率化だけでなく、システムを導入することで、コスト削減や製品・資材のステータス可視化のほか、属人化していた受発注情報の共有化による内部不正防止や統制にも役立ちます。
NEWJI DX
製造業に特化したデジタルトランスフォーメーション(DX)の実現を目指す請負開発型のコンサルティングサービスです。AI、iPaaS、および先端の技術を駆使して、製造プロセスの効率化、業務効率化、チームワーク強化、コスト削減、品質向上を実現します。このサービスは、製造業の課題を深く理解し、それに対する最適なデジタルソリューションを提供することで、企業が持続的な成長とイノベーションを達成できるようサポートします。
製造業ニュース解説
製造業、主に購買・調達部門にお勤めの方々に向けた情報を配信しております。
新任の方やベテランの方、管理職を対象とした幅広いコンテンツをご用意しております。
お問い合わせ
コストダウンが利益に直結する術だと理解していても、なかなか前に進めることができない状況。そんな時は、newjiのコストダウン自動化機能で大きく利益貢献しよう!
(β版非公開)