- お役立ち記事
- Cost Reduction Through Lane Manufacturing
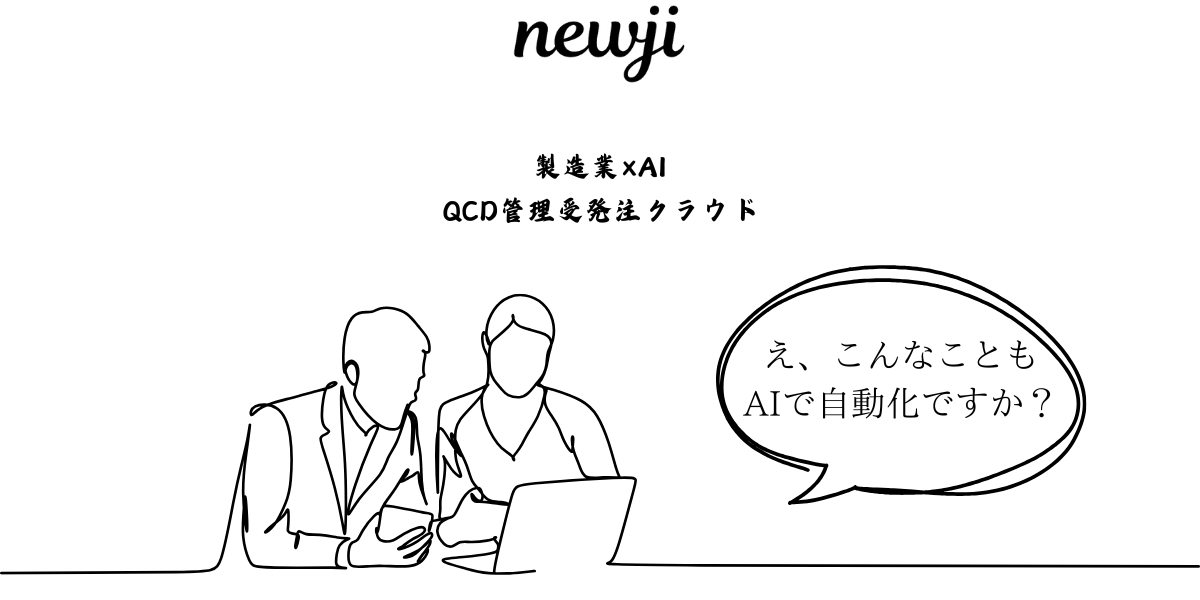
Cost Reduction Through Lane Manufacturing
In the highly competitive landscape of the manufacturing industry, companies are constantly seeking ways to optimize their operations and maximize cost savings. One approach that has gained significant popularity is Lean Manufacturing. By adopting Lean principles and practices, companies can streamline their processes, eliminate waste, and achieve substantial cost reductions.
Lean Manufacturing is based on the concept of continuous improvement, where every aspect of the production process is evaluated and refined to eliminate non-value-added activities and optimize efficiency. It focuses on minimizing waste in various forms, such as overproduction, excess inventory, defects, unnecessary motion, waiting time, and overprocessing.
By implementing Lean Manufacturing principles, companies can achieve significant cost reductions in the following ways:
1. Inventory Reduction: Lean Manufacturing emphasizes the concept of Just-in-Time (JIT) production, where inventory is minimized through tight control and synchronization of material flow. By reducing excess inventory, companies can lower carrying costs, minimize storage space requirements, and decrease the risk of obsolete goods.
2. Waste Elimination: Lean Manufacturing identifies various forms of waste, such as transportation waste, defects, and overproduction. By eliminating waste, companies can reduce unnecessary expenses and allocate resources more effectively.
3. Improved Quality: Lean Manufacturing places a strong emphasis on quality control by implementing error-proofing techniques and continuous process improvement. By minimizing defects and rework, companies can reduce costs associated with scrap, rejections, and customer complaints.
4. Streamlined Processes: Lean Manufacturing aims to simplify and streamline processes by eliminating non-value-added activities and optimizing workflow. By reducing motion waste and creating more efficient processes, companies can save time and resources, ultimately leading to cost savings.
5. Employee Engagement: Lean Manufacturing promotes a culture of employee engagement and empowerment. By involving employees in problem-solving and process improvement initiatives, companies can tap into their knowledge and expertise, leading to increased efficiency and reduced costs.
6. Supplier Collaboration: Lean Manufacturing encourages strong relationships with suppliers and emphasizes collaboration throughout the supply chain. By working closely with suppliers to improve lead times, quality, and cost-effectiveness, companies can achieve significant cost savings.
In conclusion, Lean Manufacturing provides a systematic approach to achieving cost reductions in the manufacturing industry. By implementing Lean principles and practices, companies can streamline their processes, eliminate waste, improve quality, and enhance overall efficiency. Through inventory reduction, waste elimination, improved quality, streamlined processes, employee engagement, and supplier collaboration, companies can optimize their operations and achieve substantial cost savings. Embracing Lean Manufacturing is a powerful strategy for companies looking to stay competitive and thrive in today’s challenging business environment.
資料ダウンロード
QCD調達購買管理クラウド「newji」は、調達購買部門で必要なQCD管理全てを備えた、現場特化型兼クラウド型の今世紀最高の購買管理システムとなります。
ユーザー登録
調達購買業務の効率化だけでなく、システムを導入することで、コスト削減や製品・資材のステータス可視化のほか、属人化していた購買情報の共有化による内部不正防止や統制にも役立ちます。
NEWJI DX
製造業に特化したデジタルトランスフォーメーション(DX)の実現を目指す請負開発型のコンサルティングサービスです。AI、iPaaS、および先端の技術を駆使して、製造プロセスの効率化、業務効率化、チームワーク強化、コスト削減、品質向上を実現します。このサービスは、製造業の課題を深く理解し、それに対する最適なデジタルソリューションを提供することで、企業が持続的な成長とイノベーションを達成できるようサポートします。
オンライン講座
製造業、主に購買・調達部門にお勤めの方々に向けた情報を配信しております。
新任の方やベテランの方、管理職を対象とした幅広いコンテンツをご用意しております。
お問い合わせ
コストダウンが利益に直結する術だと理解していても、なかなか前に進めることができない状況。そんな時は、newjiのコストダウン自動化機能で大きく利益貢献しよう!
(Β版非公開)