- お役立ち記事
- 設計変更と設計改善の違い
月間76,176名の
製造業ご担当者様が閲覧しています*
*2025年3月31日現在のGoogle Analyticsのデータより
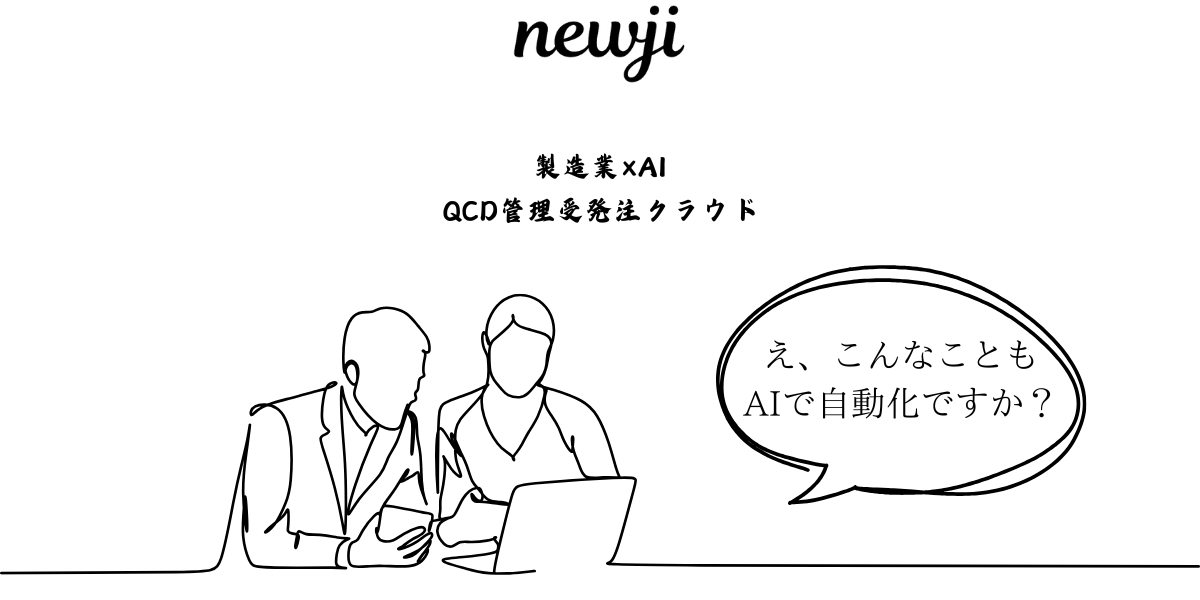
設計変更と設計改善の違い
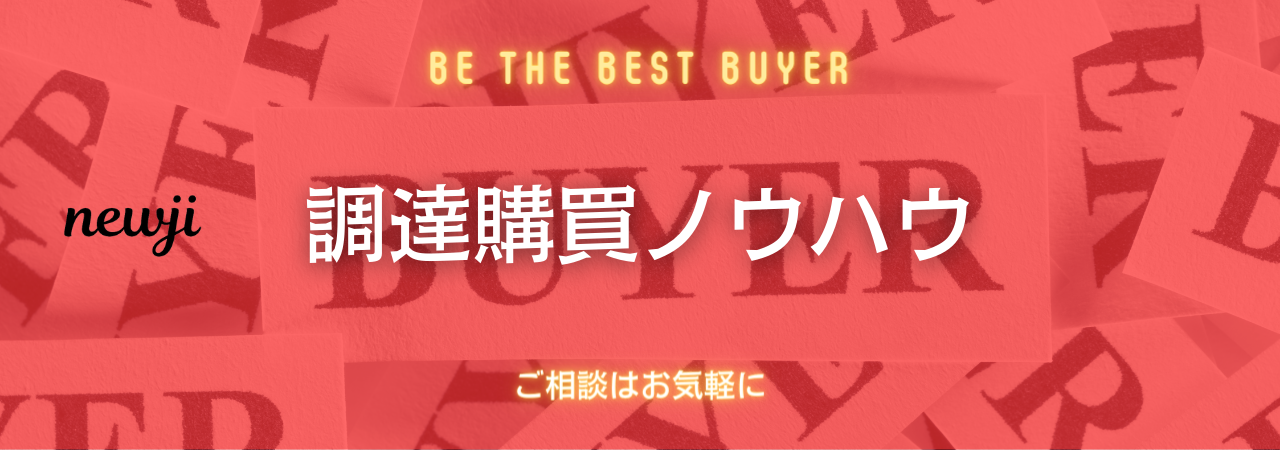
目次
設計変更と設計改善の定義
設計変更と設計改善は、製造業の現場において頻繁に使用される用語ですが、それぞれ異なる目的とプロセスを持っています。
まずは、それぞれの定義について詳しく見ていきましょう。
設計変更とは
設計変更は、既存の設計を改訂することを指します。
これは、製品または製造プロセスに対して何らかの技術的な変更が必要とされる場合に行われるものです。
設計変更の目的は多岐に渡りますが、主に以下のような理由が含まれます。
– 規格や法律の変更
– 市場のフィードバック
– コスト削減
– 部材の供給停止
– 製品の性能向上
例えば、法的な理由で特定の材料の使用が禁止された場合、それに代わる材料を選定し、設計を変更する必要があります。
また、消費者のフィードバックで製品の使い勝手が悪いとされる場合、その部分を改良するための設計変更が求められることもあります。
設計改善とは
一方、設計改善は、既存の設計をベースに性能や品質を向上させるためのプロセスを指します。
設計改善は、製品の寿命を延ばしたり、効率を向上させたりするために施されることが一般的です。
目的としては以下のようなことが挙げられます。
– 品質向上
– 生産効率の向上
– 完成品の性能向上
– コスト削減
– 環境負荷の削減
例えば、製造過程での不良品が多発している場合、その原因を突き止め、改善策を講じます。
また、生産効率が低いと感じた場合、製造プロセスや使用する機械を見直すことで改善を図ります。
設計変更と設計改善のプロセス
次に、具体的なプロセスについて見ていきましょう。
設計変更のプロセス
1. **問題の特定**
まず初めに、設計変更を必要とする問題や課題を明確に特定します。
これは、製品の欠陥、法規制の変更、または消費者からのフィードバックなどが該当します。
2. **変更の計画**
次に、その問題を解決するための変更計画を立てます。
新しい設計案を作成し、それが既存の設計とどのように異なるかを明確にします。
3. **検証とテスト**
新しい設計が計画通りに動作するか確認するために、プロトタイプの作成やシミュレーションを行います。
必要に応じて、厳密なテストを行い、性能や品質に問題がないか確認します。
4. **実行とフォローアップ**
問題がないことが確認されれば、設計変更を実際の生産ラインに適用します。
その後、状況をフォローアップして新しい設計に問題が発生しないか監視します。
設計改善のプロセス
1. **現状評価**
まずは、現行の設計や製造プロセスを評価します。
データを収集し、どこに改善の余地があるかを見極めます。
2. **改善点の特定**
次に、どの部分に改善が必要かを具体的に特定します。
これは、品質データ、顧客からのフィードバック、または生産の効率データを基に行われます。
3. **改善策の立案**
特定した改善点に対して、具体的な改善策を立案します。
これには、新しい技術の導入や既存のプロセスの改良が含まれます。
4. **テストと評価**
改善策が有効かどうかを確認するためにテストを行います。
必要に応じて、検証データを収集し、改善の効果を評価します。
5. **本格的な導入**
改善策が有効であることが確認されたら、それを全体の生産プロセスに導入します。
その後、定期的にモニタリングしてさらなる改善点がないか確認します。
設計変更と設計改善の課題と解決策
設計変更と設計改善には、それぞれ異なる課題が存在します。しかし、適切な対策を講じることで、それらの課題を克服できる場合があります。
設計変更の課題
1. **コストの増加**
設計変更はしばしばコストの増加を伴います。新しい材料の購入、機械の設定変更、そしてテストや検証の作業が追加されるためです。
2. **納期の遅延**
変更作業が生産ラインに影響を及ぼすため、生産スケジュールが遅れることがあります。
3. **品質保証のリスク**
新しい設計が既存の設計と異なる場合、その品質保証に関するリスクが高まることがあります。
設計変更の解決策
1. **コスト効果の分析**
事前に変更のコスト効果を詳細に分析し、コストと効果のバランスを取る計画を立てる必要があります。
2. **スケジュールの柔軟性確保**
予防的にスケジュールに一定の余裕を持たせ、納期遅延に備えることが重要です。
3. **品質管理プロセスの強化**
詳細なテストとフィードバックループを設定し、品質管理プロセスを強化します。
設計改善の課題
1. **効果の不透明性**
設計改善の効果が明確に見えないことがあり、その結果、効果を実感するまで時間がかかることがあります。
2. **従業員の抵抗**
新しい改善策を導入する際、従業員の抵抗が生じることがあります。
3. **リソースの制約**
改善策を実行するためのリソース(人員、資金、時間など)が不足することがあります。
設計改善の解決策
1. **明確な目標設定**
事前に改善効果を測定するための明確な指標を設定し、進捗を追跡することが重要です。
2. **コミュニケーションの重要性**
従業員に対して新しい改善策の目的と効果を十分に説明し、理解を促すことが必要です。
3. **リソースの適切な配分**
改善策に必要なリソースを事前に計画し、適切に配分することが成功の鍵となります。
最新技術と設計変更・設計改善
技術の進化は日々驚くべき速度で進んでおり、それらの新技術が設計変更および設計改善にどのように影響を与えるかを理解することは重要です。
AIと機械学習
人工知能(AI)と機械学習は、製造プロセスの改善に大いに寄与しています。
– **異常検知**
AIは生産ラインでの異常を迅速に検知し、即座に対応することで品質を維持します。
– **予測メンテナンス**
機械学習を用いて機械の故障を予測し、予防的なメンテナンスを行うことでダウンタイムを減少させます。
IoTとリアルタイムモニタリング
インターネット・オブ・シングズ(IoT)は、製造プロセスのリアルタイムモニタリングを可能にし、生産効率の向上に繋がります。
– **リアルタイムデータ収集**
センサーを用いてリアルタイムでデータを収集し、製造プロセスの各ステップをモニタリングします。
– **遠隔操作と管理**
IoT技術を用いて遠隔から製造プロセスを管理し、迅速な対応が可能となります。
3Dプリンティング
3Dプリンティングは、試作や少量生産の分野で特に有効です。
– **試作の迅速化**
試作品を迅速に作成し、設計変更の効果をすぐに確認することができます。
– **コスト削減**
少量生産のためのコストを大幅に削減し、柔軟な対応が可能です。
クラウドコンピューティング
クラウドコンピューティングは、大量のデータを安全かつ効率的に処理するための技術です。
– **データの集約と分析**
製造プロセスに関する大量のデータをクラウドに集約し、分析することで、効率の向上に役立てます。
– **コラボレーションの強化**
クラウドを利用して、異なる場所にいるチーム間で円滑なコラボレーションを促進します。
まとめ
設計変更と設計改善は、それぞれ異なる目的とプロセスを持ちながら、いずれも製造業の品質向上やコスト削減において重要な役割を果たしています。
そのため、これらのプロセスを理解し、適切に実行することは、製造業の競争力を高めるために不可欠です。
また、最新技術を適用することで、設計変更および設計改善の効率と効果をさらに高めることが可能です。
製造業の未来は、こうした技術の応用とともに大きく進化していくことでしょう。
資料ダウンロード
QCD管理受発注クラウド「newji」は、受発注部門で必要なQCD管理全てを備えた、現場特化型兼クラウド型の今世紀最高の受発注管理システムとなります。
ユーザー登録
受発注業務の効率化だけでなく、システムを導入することで、コスト削減や製品・資材のステータス可視化のほか、属人化していた受発注情報の共有化による内部不正防止や統制にも役立ちます。
NEWJI DX
製造業に特化したデジタルトランスフォーメーション(DX)の実現を目指す請負開発型のコンサルティングサービスです。AI、iPaaS、および先端の技術を駆使して、製造プロセスの効率化、業務効率化、チームワーク強化、コスト削減、品質向上を実現します。このサービスは、製造業の課題を深く理解し、それに対する最適なデジタルソリューションを提供することで、企業が持続的な成長とイノベーションを達成できるようサポートします。
製造業ニュース解説
製造業、主に購買・調達部門にお勤めの方々に向けた情報を配信しております。
新任の方やベテランの方、管理職を対象とした幅広いコンテンツをご用意しております。
お問い合わせ
コストダウンが利益に直結する術だと理解していても、なかなか前に進めることができない状況。そんな時は、newjiのコストダウン自動化機能で大きく利益貢献しよう!
(β版非公開)