- お役立ち記事
- カンバンとピッキングリストの違い
月間76,176名の
製造業ご担当者様が閲覧しています*
*2025年3月31日現在のGoogle Analyticsのデータより
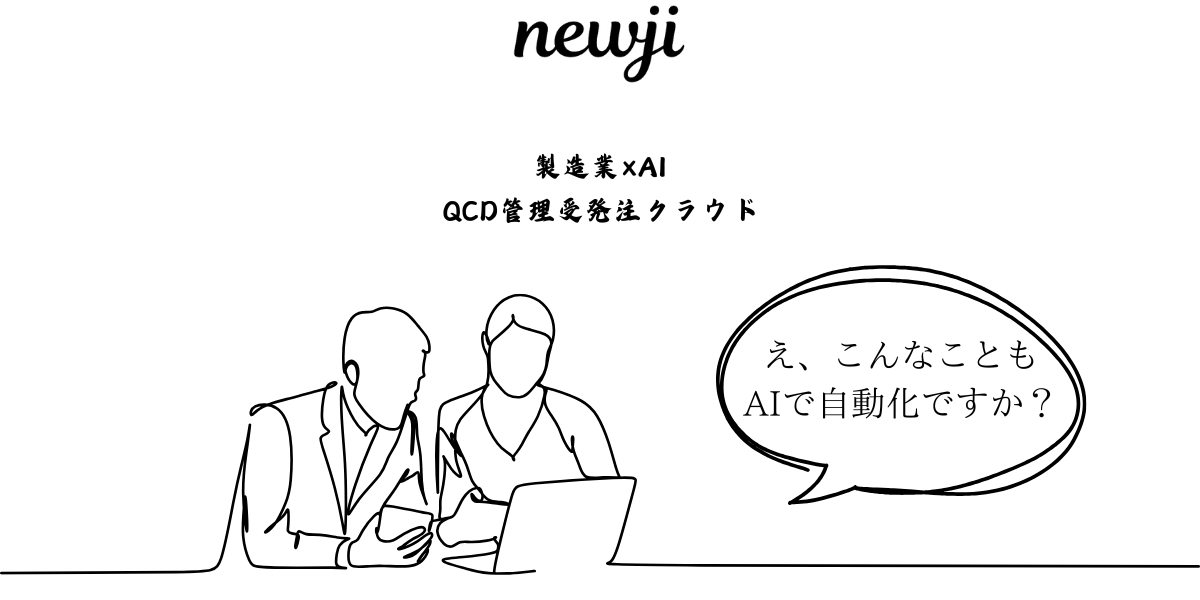
カンバンとピッキングリストの違い
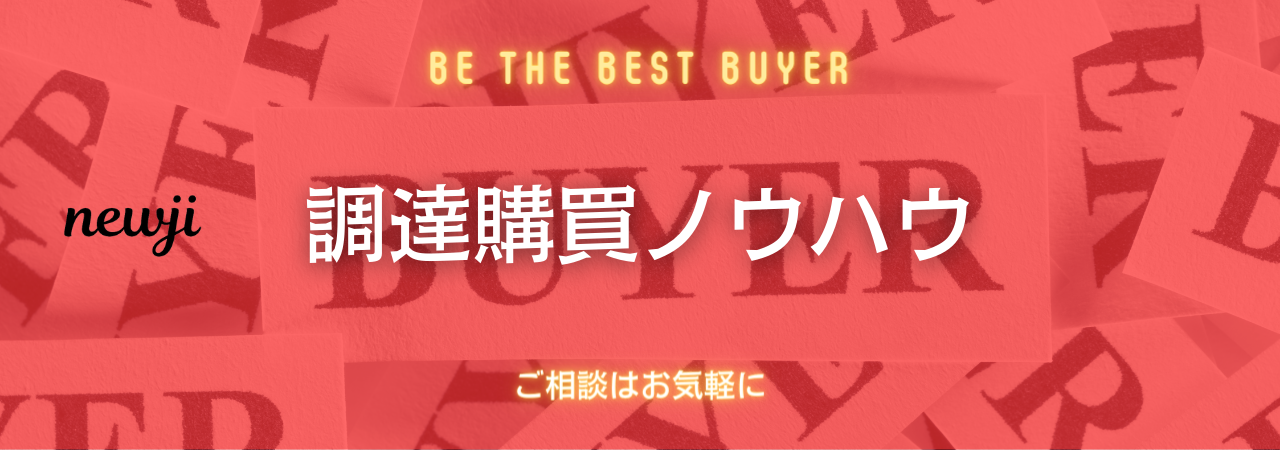
目次
カンバンとピッキングリストの違い
生産管理や物流管理において、カンバンとピッキングリストは非常に重要な役割を果たします。
しかし、これらの用語や概念の違いを明確に理解していない人も少なくありません。
ここでは、カンバンとピッキングリストの違いについて、現場目線から詳しく解説していきます。
カンバン方式とは
カンバン方式は、トヨタ自動車が開発し世界中に広まった生産管理手法の一つです。
カンバンとは日本語で「看板」という意味ですが、この手法では「物の流れを視覚化する」ために使用します。
具体的には、各工程や物品に対応するカード(カンバン)を用いて、生産の流れを管理します。
カンバン方式の基本的な考え方は、「必要なものを、必要な時に、必要な量だけ」生産することで効率を最大化する点にあります。
カンバンの利点
カンバン方式には以下のような利点があります。
1. **在庫削減**
カンバン方式では、過剰生産や在庫の無駄を防ぐことができます。
これにより、効率的な資源利用が可能となり、コスト削減につながります。
2. **柔軟な生産対応**
需要の変動に迅速に対応できるため、急な受注変更や製品バリエーションが多い場合でも柔軟に対応できます。
3. **ミスの削減**
カンバンを用いることで、生産現場における指示が明確になり、ヒューマンエラーを減少させる効果があります。
カンバンの種類
カンバンには以下のような種類があります。
1. **プル型カンバン**
次の工程が先の工程に生産要求を出す形で、材料や部品を引き取る方式です。
2. **プッシュ型カンバン**
先の工程が次の工程に材料や部品を供給する形で、生産要求を出す方式です。
3. **スルーカンバン**
一つのカンバンで複数の工程を管理する特殊なカンバンです。
ピッキングリストとは
ピッキングリストは、製品や部品を組み立てるために必要な材料や部品のリストです。
主に倉庫や物流センターで用いられ、製品を特定の注文や生産計画に基づいて集める際に使用されます。
ピッキングリストの利点
ピッキングリストには以下のような利点があります。
1. **効率的な材料収集**
必要な部品や材料をスムーズに収集するためのガイドとなり、時間と労力を大幅に削減します。
2. **ミスの低減**
明確な指示が記載されているため、誤った部品や材料を選び出すリスクが減少します。
3. **在庫管理の効率化**
どの部品がどれだけ必要かが明確になるため、在庫管理が容易になります。
ピッキングリストの種類
ピッキングリストには以下のような種類があります。
1. **トランザクション型ピッキングリスト**
各注文番号ごとにリストを作成し、特定の注文に合わせた部品や材料を収集します。
2. **バッチ型ピッキングリスト**
複数の注文を一括して処理するために、まとめてリスト化する方式です。
3. **ゾーン型ピッキングリスト**
倉庫や物流センターを複数のゾーンに分け、各ゾーンごとにリストを作成する方式です。
カンバンとピッキングリストの比較
カンバンとピッキングリストはどちらも生産管理や物流管理において重要な役割を果たしますが、その性質や用途は異なります。
以下でそれぞれの特徴を比較してみましょう。
使用目的の違い
– **カンバン**
カンバンは主に、生産の各工程における流れとタイミングを管理するために使用されます。
効率的な生産を実現し、過剰生産や在庫を削減することが目的です。
– **ピッキングリスト**
ピッキングリストは、製品や部品を集めるためのガイドとして使用されます。
特定の注文に基づいて部品や材料を効率的に収集することが目的です。
視覚化の違い
– **カンバン**
カンバンは視覚的な管理ツールであり、現場の作業員が一目で状況を把握できる点が特徴です。
– **ピッキングリスト**
ピッキングリストは、リスト形式の文書や電子データ形式で提供されることが一般的です。
導入の難易度の違い
– **カンバン**
カンバン方式の導入には、現場の作業フローの理解と適切なカンバン設定が必要です。
また、全体の生産システムとの連携が求められます。
– **ピッキングリスト**
ピッキングリストの導入は比較的簡単で、リストを生成するソフトウェアやシステムの導入だけで対応可能です。
最新の技術動向
これまで紹介したカンバンとピッキングリストも、最新の技術動向により大きく進化しています。
以下でその一部を紹介します。
デジタルカンバン
デジタルカンバンは、従来の紙ベースのカンバンを電子化し、リアルタイムで生産状況を管理するシステムです。
これにより、以下のようなメリットがあります。
– **リアルタイムモニタリング**
生産ラインの状態をリアルタイムで監視し、即座に対応できます。
– **データ分析の容易化**
生産データを蓄積し、分析することで、より効率的な生産計画が立てられます。
– **柔軟な変更対応**
生産計画の変更やイレギュラー対応が迅速に行えます。
自動化ピッキングシステム
ピッキングリストをベースにした自動化ピッキングシステムは、倉庫や物流センターでの作業効率を大幅に向上させる技術です。
具体的なメリットは以下の通りです。
– **作業効率の向上**
ロボットや自動化装置を使用することで、ピッキング作業が迅速かつ正確に行われます。
– **コスト削減**
人力の作業が減少し、労働コストが削減されます。
– **エラーの減少**
自動化によりピッキングミスが減少し、精度が向上します。
導入事例と効果
最後に、カンバンとピッキングリストの実際の導入事例とその効果について触れます。
カンバン方式導入事例
ある自動車部品メーカーでは、カンバン方式を導入し、以下のような効果を得ました。
– **在庫の削減**
従来の在庫が50%減少し、余剰コストが大幅に削減されました。
– **生産効率の向上**
生産ラインの稼働率が向上し、製品の納期遵守率が改善しました。
– **ヒューマンエラーの減少**
カンバン方式により、現場での誤操作や誤出荷が減少しました。
ピッキングリスト導入事例
ある大手物流企業では、ピッキングリストを活用した自動化ピッキングシステムを導入し、以下のような成果を上げました。
– **作業時間の短縮**
ピッキング作業の時間が従来の半分以下に短縮されました。
– **正確性の向上**
ピッキングミスが90%以上減少し、クレーム対応が大幅に減少しました。
– **コスト削減**
自動化により労働コストが削減され、運営コストが改善しました。
まとめ
カンバンとピッキングリストは、それぞれ異なる目的と特徴を持つ重要な生産管理および物流管理ツールです。
カンバン方式は生産フローの視覚化と効率的な生産管理、在庫削減に効果的です。
一方、ピッキングリストは正確な部品収集と作業効率の向上に役立ちます。
最新の技術動向を取り入れることで、これらのツールの効果はさらに向上します。
現場での実際の導入事例を参考にして、自社の生産管理や物流管理を最適化するために、これらのツールを上手に活用していくことが重要です。
資料ダウンロード
QCD管理受発注クラウド「newji」は、受発注部門で必要なQCD管理全てを備えた、現場特化型兼クラウド型の今世紀最高の受発注管理システムとなります。
ユーザー登録
受発注業務の効率化だけでなく、システムを導入することで、コスト削減や製品・資材のステータス可視化のほか、属人化していた受発注情報の共有化による内部不正防止や統制にも役立ちます。
NEWJI DX
製造業に特化したデジタルトランスフォーメーション(DX)の実現を目指す請負開発型のコンサルティングサービスです。AI、iPaaS、および先端の技術を駆使して、製造プロセスの効率化、業務効率化、チームワーク強化、コスト削減、品質向上を実現します。このサービスは、製造業の課題を深く理解し、それに対する最適なデジタルソリューションを提供することで、企業が持続的な成長とイノベーションを達成できるようサポートします。
製造業ニュース解説
製造業、主に購買・調達部門にお勤めの方々に向けた情報を配信しております。
新任の方やベテランの方、管理職を対象とした幅広いコンテンツをご用意しております。
お問い合わせ
コストダウンが利益に直結する術だと理解していても、なかなか前に進めることができない状況。そんな時は、newjiのコストダウン自動化機能で大きく利益貢献しよう!
(β版非公開)