- お役立ち記事
- PDCAとOODAの違い
月間76,176名の
製造業ご担当者様が閲覧しています*
*2025年3月31日現在のGoogle Analyticsのデータより
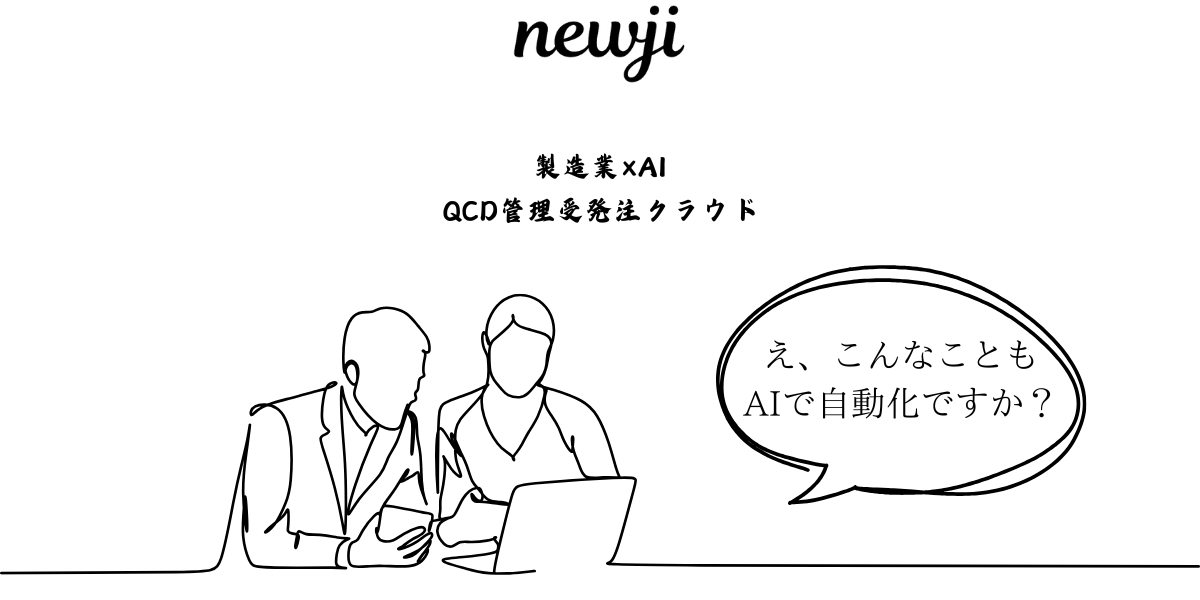
PDCAとOODAの違い
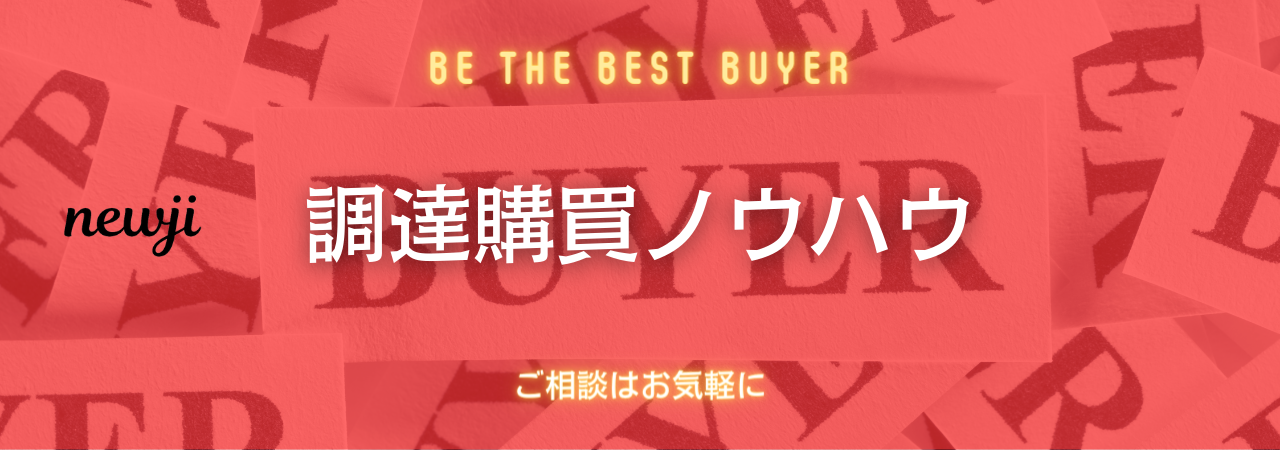
目次
PDCAとは何か
PDCAサイクルは、Plan(計画)、Do(実行)、Check(確認)、Act(改善)という4つのステップからなる品質管理と業務改善の手法です。
この手法は、1950年代にエドワーズ・デミング博士によって広められ、製造業を中心に多くの企業で採用されています。
Plan:計画を立てる
まず、目標を設定し、その目標を達成するための具体的な計画を立てます。
このステップでは、現状の問題点を把握し、改善策を考えます。
例えば、新製品の生産ラインを設計する場合、この段階で設備、人員、コストなどを詳細に検討します。
Do:計画を実行する
次に、計画を実行に移します。
このステップでは、立てた計画通りに作業を進め、実際に問題解決や目標達成に向けたアクションを行います。
例えば、新しい生産ラインを実際に運用し、計画通りの生産が可能かを確認します。
Check:結果を確認する
実行した結果を確認するステップです。
計画通りに進んだか、成果が上がったかを評価し、データや実績を分析します。
例えば、生産ラインの効率や品質を確認し、問題点があればそれを明らかにします。
Act:改善策を講じる
最後に、確認した結果をもとに改善策を講じます。
このステップでは、良かった点を維持しつつ、問題点を改善します。
例えば、効率が低かった部分を改善し、次のサイクルで再度チェックします。
OODAとは何か
OODAループは、Observe(観察)、Orient(方向付け)、Decide(決定)、Act(行動)の4つのステップからなる意思決定のフレームワークです。
元々はアメリカ空軍のジョン・ボイド大佐によって開発され、高速で変化する状況に迅速に対応するための手法として広まりました。
Observe:観察する
まず、現状を詳細に観察します。
このステップでは、環境や状況の変化を迅速にとらえ、必要な情報を収集します。
例えば、市場の動向や競合企業の戦略などを観察します。
Orient:方向付けする
次に、収集した情報をもとに、自分自身や組織の位置づけを明確にします。
このステップでは、情報を分析し、今後の方向性を定めます。
例えば、強みや弱みをはっきりさせ、次に何をすべきかを考えます。
Decide:決定する
次に、最良の行動を決定するステップです。
観察と方向付けに基づいて、最も適切なアクションを選びます。
例えば、新しい製品を市場に投入するか否かを決定します。
Act:行動する
最後に、決定したアクションを実行します。
このステップでは、迅速に行動に移り、結果を再度観察します。
例えば、新しい製品の市場投入を実際に行い、その反応を観察します。
PDCAとOODAの違い
PDCAとOODAは、どちらも問題解決や業務改善のためのフレームワークですが、アプローチや適用するシチュエーションが異なります。
アプローチの違い
PDCAは循環型で、計画に基づいた段階的な改善を目指します。
一方、OODAは状況に応じた迅速な意思決定を重視します。
そのため、PDCAは安定した環境での長期的な改善に適しており、OODAは変化が激しい環境での迅速な対応に向いています。
適用するシチュエーションの違い
PDCAは、生産管理や品質管理など、穏やかで計画的な環境に適しています。
一方、OODAは市場変化や競争状況の分析など、高速で変化する環境に適しています。
例えば、新製品の開発や市場投入の際にはOODAが役立ちますが、既存の製造プロセスの改善にはPDCAが有効です。
PDCAとOODAの共通点
PDCAとOODAには共通する点もあります。
どちらの手法も、現状の理解、計画の立案、行動の実行、結果の確認というサイクルを持っています。
また、どちらの手法でも問題点を早期に発見し、迅速に対応することが重要です。
データの重要性
PDCAもOODAも、計画や行動の基盤としてデータを重視します。
具体的なデータに基づいて状況を把握し、適切な行動を取ることが求められます。
そのため、信頼性のあるデータ収集と分析が不可欠です。
継続的な改善
どちらの手法も、一度のサイクルで全てが完了するわけではありません。
継続的な改善と学習を通じて、組織全体のパフォーマンスを向上させることが目指されています。
最新の技術動向とPDCA/OODAの組み合わせ
最新の技術を活用することで、PDCAとOODAの効果をさらに高めることができます。
IoTとデータ解析
IoT(Internet of Things)技術を活用すれば、工場内の設備や生産ラインの状態をリアルタイムで監視することができます。
収集したデータを解析し、PDCAやOODAの各ステップで即座に活用することで、迅速かつ精度の高い意思決定が可能になります。
AIと自動化
人工知能(AI)を用いることで、データ解析やパターン認識を自動化し、より高度な予測や異常検知ができるようになります。
これにより、PDCAのCheckとActのステップや、OODAのObserveとDecideのステップが大幅に効率化されます。
クラウド技術
クラウド技術を活用することで、誰でもどこでもデータにアクセスし、リアルタイムで情報を共有することができます。
これにより、チーム全体での迅速な対応と柔軟な意思決定が実現できます。
まとめ
PDCAとOODAは、いずれも業務改善や意思決定のための有効なフレームワークですが、適用するシチュエーションやアプローチが異なります。
PDCAは計画的な改善に、OODAは迅速な対応に適しています。
最新の技術を活用することで、これらの手法の効果をさらに高めることができます。
製造業の現場でこれらの知識や手法を活かし、継続的な成長と改善を目指しましょう。
資料ダウンロード
QCD管理受発注クラウド「newji」は、受発注部門で必要なQCD管理全てを備えた、現場特化型兼クラウド型の今世紀最高の受発注管理システムとなります。
ユーザー登録
受発注業務の効率化だけでなく、システムを導入することで、コスト削減や製品・資材のステータス可視化のほか、属人化していた受発注情報の共有化による内部不正防止や統制にも役立ちます。
NEWJI DX
製造業に特化したデジタルトランスフォーメーション(DX)の実現を目指す請負開発型のコンサルティングサービスです。AI、iPaaS、および先端の技術を駆使して、製造プロセスの効率化、業務効率化、チームワーク強化、コスト削減、品質向上を実現します。このサービスは、製造業の課題を深く理解し、それに対する最適なデジタルソリューションを提供することで、企業が持続的な成長とイノベーションを達成できるようサポートします。
製造業ニュース解説
製造業、主に購買・調達部門にお勤めの方々に向けた情報を配信しております。
新任の方やベテランの方、管理職を対象とした幅広いコンテンツをご用意しております。
お問い合わせ
コストダウンが利益に直結する術だと理解していても、なかなか前に進めることができない状況。そんな時は、newjiのコストダウン自動化機能で大きく利益貢献しよう!
(β版非公開)