- お役立ち記事
- DRとFMEA
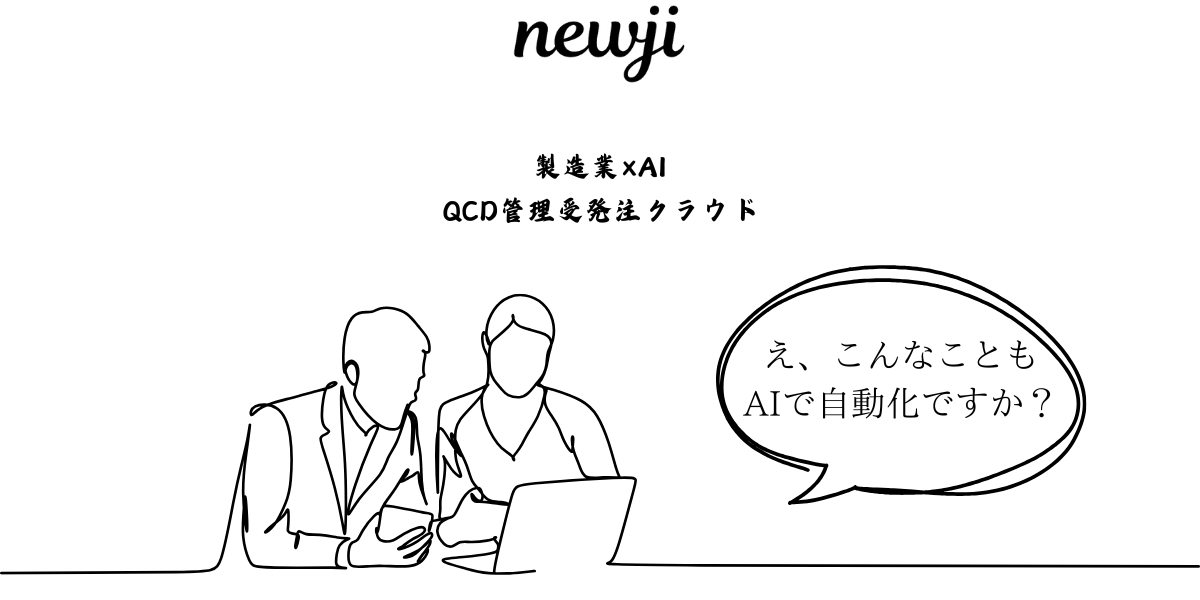
DRとFMEA
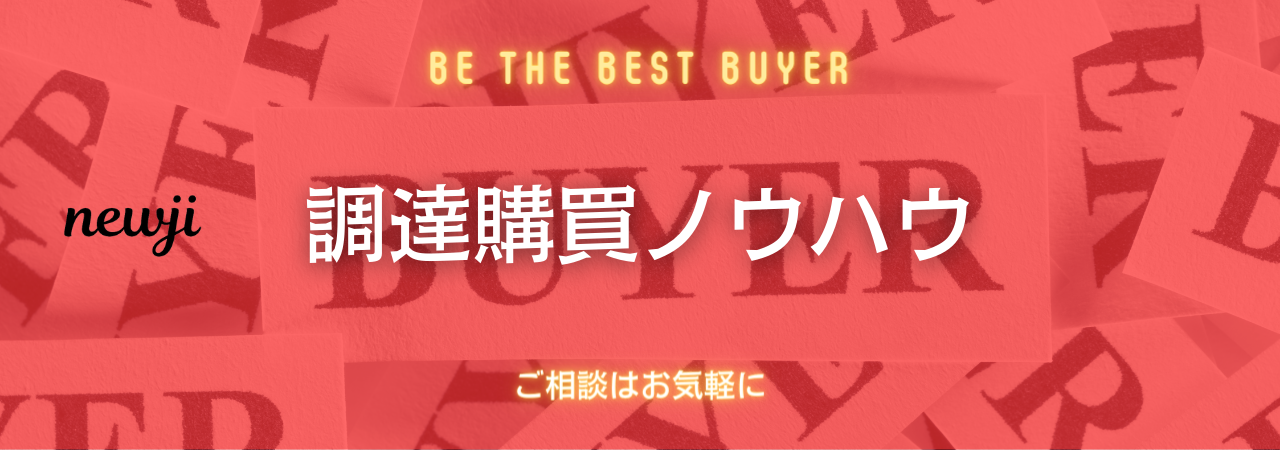
目次
DR(デザインレビュー)とは
デザインレビュー(Design Review、以下DR)は、製品開発プロセスの各段階で設計や仕様を評価し、意図した品質や性能を確保するための重要な工程です。
開発チームや利害関係者が集まり、設計の健全性、リスク、改善点を議論し、課題を解決する機会です。
DRの目的は、設計上の問題を早期に検出し、修正することであり、これにより製品の信頼性や市場投入までの時間を短縮します。
設計段階でのミスは、後々の製造段階での大きな問題やコストにつながるため、DRはことさら重要です。
DRのプロセス
DRは、設計ステージごとに異なる焦点を持つ複数のレビューを含むことが一般的です。
開発ライフサイクルの各ステージで行われ、要求仕様、コンセプト設計、詳細設計などが対象となります。
各DRは、以下のプロセスを経て進められます。
1. **準備**:レビューチームの編成、資料の準備、検討課題の明確化。
2. **実施**:設計者からのプレゼンテーション、参加者からの質疑応答、問題及びリスクの洗い出し。
3. **フォローアップ**:抽出した課題の対応策の検討、実行計画の立案、次回レビューへの準備。
DRを成功させる要素
DRを効果的に行うためには、以下のポイントが重要です。
– **多様な視点**:異なる専門分野のエキスパートを参加させ、幅広い視点で設計を評価する。
– **明確な目的**:各DRの目的を明確にし、全員が共有することで、レビューの焦点を明確にする。
– **オープンなコミュニケーション**:ミーティング内で自由に意見を述べられる環境を作り、潜在的な問題を隠さず洗い出す。
– **フォローアップ体制**:問題点の洗い出しだけでなく、その後のフォローアップが機能する体制を整える。
FMEA(故障モード影響解析)とは
FMEA(Failure Mode and Effect Analysis)は、製品やプロセスの故障モードを特定し、それが結果に与える影響を評価する手法です。
リスクの高い故障モードを特定し、優先順位をつけて対策を講じることで、品質と信頼性を向上させます。
FMEAは製造業界のみならず、多くの産業で採用されており、特に自動車業界での規格であるISO 26262に基づいた開発に欠かせない手法となっています。
FMEAのプロセス
FMEAは通常、次のようなステップで行われます。
1. **システムの理解**:製品やプロセスの構造を理解し、分析対象を明確化する。
2. **故障モードの特定**:過去のデータや経験、理論に基づいて潜在的な故障モードを洗い出す。
3. **影響の評価**:各故障モードがシステムや顧客に与える影響を評価する。
4. **リスクの優先順位付け**:故障の可能性、影響度、検出の難しさを基にリスクを定量化し、優先順位をつける。
5. **対策の実行**:高リスクの故障モードに対して対策を講じ、実行する。
6. **再評価とフォローアップ**:対策後の状況を再度評価し、必要に応じて改善を継続する。
FMEAの成功ポイント
FMEAを効果的に実施するには、以下の要素が重要です。
– **包括的な参加**:設計者、製造者、品質管理者など関連するすべての部門からの参加が重要です。
– **過去のデータの活用**:過去の問題事例や統計データを用いて、潜在的リスクをより正確に予測する。
– **リスク評価の一貫性**:定量的な手法を用いてリスクを評価し、客観性を持たせる。
– **持続的なフォローアップ**:一度の解析で終わらせず、継続的にフォローアップしプロセスを改善する。
DRとFMEAの相関関係
DRとFMEAは、異なるアプローチで製品の品質を向上させますが、互いに補完し合う関係にあります。
– **DRの中でのFMEA活用**:DRのプロセスでFMEAを利用することで、設計段階からリスク管理を取り入れ、より深い議論と具体的な対策が可能になります。
– **プロアクティブな問題解決**:FMEAで発見されたリスクは、DRの中で議論され、事前に対策が立てられることで、製品ライフサイクルの早期段階で問題を回避できます。
– **フィードバックループの確立**:DRでの指摘事項を基にFMEAのリスク評価を更新し、次回の設計プロジェクトにフィードバックすることで、設計手法の継続的改善が図れます。
これらの手法を組み合わせることで、開発期間の短縮、製品の信頼性向上、コスト削減につなげることができます。
伝統的な製造業における課題と解決策
昭和から続く日本の製造業は、保守的な側面を持ちつつも、近年ではデジタル化やグローバル化の影響を受け、変革を迫られています。
デジタル化への移行
多くの製造業では、未だに紙ベースの管理や手動によるプロセスが残っています。
これが故に、情報の共有や確認に時間がかかるケースが見受けられます。
デジタルツールを導入し、DRやFMEAのプロセスでの効率性を向上させることが必要です。
– **デジタルツールの導入**:Cadデータや仕様書をクラウドベースで管理し、必要な情報に迅速にアクセスできる環境を整備する。
– **データのリアルタイム共有**:モバイル機器やタブレットを活用して、現場での情報収集や指示を即時に行う体制を構築。
グローバル化への対応
グローバル市場での競争激化は、日本国内市場だけに頼らないビジネス戦略を求めています。
これにより、DRやFMEAのプロセスも国際規格に準拠し、海外のパートナーとも円滑に協働できる体制作りが求められます。
– **国際規格の理解と適用**:ISO/TS 16949やISO 26262など国際的な規格を理解し、製品開発プロセスに取り入れる。
– **異文化理解の促進**:海外拠点とのコミュニケーションスキルを強化し、グローバルチームでのDR/FMEAを可能にする。
まとめ
DRとFMEAは、製造業における品質管理の中核を担うプロセスです。
早期段階での設計上の問題発見とリスク予測は、製品の品質を大きく向上させる鍵となります。
昭和の伝統を持つ日本の製造業も、デジタル化やグローバル化の流れを取り入れることで、自社の競争力を強化し続けることができます。
これからの製造業界において、DRとFMEAという2つの手法の理解と活用は必須であり、その成功の鍵は、文化や従来の慣習を超えた柔軟な考え方にあります。
製造業に関わる全ての方が、これらの方法論を活かし、ますます複雑化する市場環境に対応し続けることを期待します。
資料ダウンロード
QCD調達購買管理クラウド「newji」は、調達購買部門で必要なQCD管理全てを備えた、現場特化型兼クラウド型の今世紀最高の購買管理システムとなります。
ユーザー登録
調達購買業務の効率化だけでなく、システムを導入することで、コスト削減や製品・資材のステータス可視化のほか、属人化していた購買情報の共有化による内部不正防止や統制にも役立ちます。
NEWJI DX
製造業に特化したデジタルトランスフォーメーション(DX)の実現を目指す請負開発型のコンサルティングサービスです。AI、iPaaS、および先端の技術を駆使して、製造プロセスの効率化、業務効率化、チームワーク強化、コスト削減、品質向上を実現します。このサービスは、製造業の課題を深く理解し、それに対する最適なデジタルソリューションを提供することで、企業が持続的な成長とイノベーションを達成できるようサポートします。
オンライン講座
製造業、主に購買・調達部門にお勤めの方々に向けた情報を配信しております。
新任の方やベテランの方、管理職を対象とした幅広いコンテンツをご用意しております。
お問い合わせ
コストダウンが利益に直結する術だと理解していても、なかなか前に進めることができない状況。そんな時は、newjiのコストダウン自動化機能で大きく利益貢献しよう!
(Β版非公開)