- お役立ち記事
- 品質機能展開QFDの有効活用とFMEA・DRBFMの未然防止活動と効率化への応用
月間77,185名の
製造業ご担当者様が閲覧しています*
*2025年2月28日現在のGoogle Analyticsのデータより
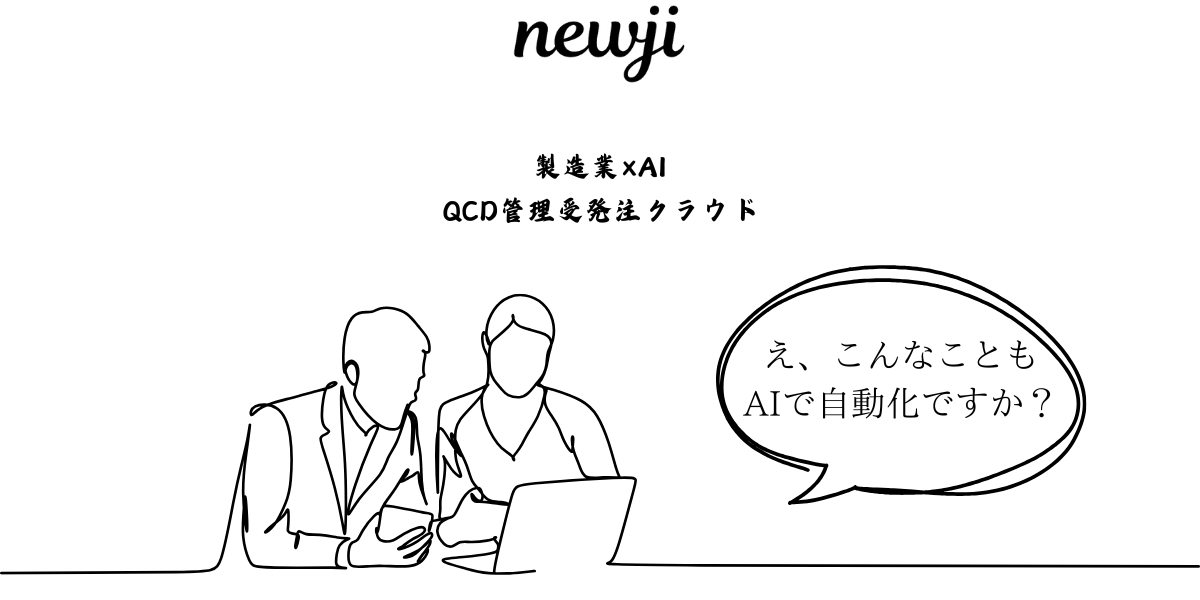
品質機能展開QFDの有効活用とFMEA・DRBFMの未然防止活動と効率化への応用
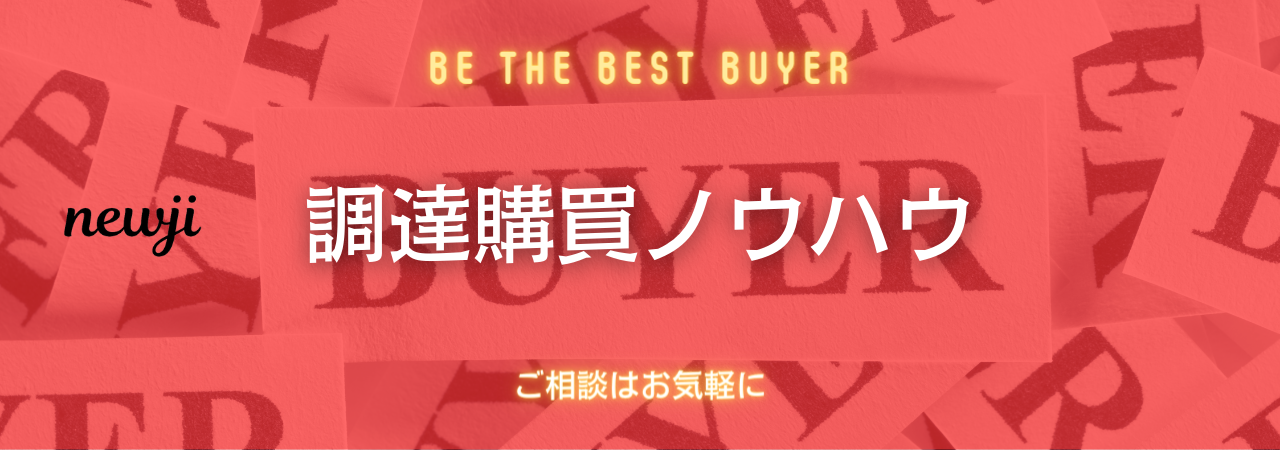
目次
品質機能展開(QFD)とは
品質機能展開(QFD)は、製品開発において顧客の要求を効果的に取り込み、最終製品に反映するための手法です。
主に顧客のニーズを技術的な仕様に変換し、製品設計に反映させるプロセスを体系化しています。
そのため、特に初期段階での誤解や見落としを防ぐために極めて重要です。
QFDは「お客様が何を求めているのか」という基本的な問いに対して継続的に答えるために、製品のコンセプトや仕様を様々な部門や工程にわたって調整する役割を果たします。
QFDの具体的なプロセス
QFDは、顧客要求を抜き出し、これを設計特徴に翻訳する過程で四つの主なフェーズに分かれます。
「製品計画」、「製品設計」、「プロセス設計」、そして「製造プロセス制御」です。それぞれのフェーズで、要求事項を関連部門と協力して検討・評価していくことが求められます。
家系図のように関連性を見える化し、「何を重視すべきか」「どのように実現するか」という判断がしやすくなります。
失敗モード影響解析(FMEA)の役割
FMEAは、製品やプロセスの潜在的な障害や不具合を洗い出し、その影響を考慮して未然に防ぐための手法です。
これにより問題発生を抑え込み、品質と信頼性を維持することができます。
FMEAでは具体的に、発生しうる失敗モードを特定し、その影響を定量的に評価します。
さらに、原因を探求し、それを防ぐための改良策を立案します。
FMEAは、特に製品のライフサイクル全体を通じて適用可能であり、プロジェクトの初期段階で効果的に導入することで、コスト削減や品質向上に寄与します。
FMEAの実施ステップ
まず、対象とするシステムや部品を詳細に分析し、失敗モードをリストアップします。
次に、失敗モードごとに「重大度」、「発生頻度」、「検出能力」を定量化し、これに基づいて優先度を決定します。
その結果に基づき、改良策を具体的に実施し、その効果をモニタリングします。
これを繰り返すことで、製品やプロセスの信頼性を高めることができます。
Design Review Based on Failure Mode (DRBFM)の重要性
DRBFMは、製品設計において変更が加えられる際に、その変更が引き起こす可能性のある失敗や不具合を事前に検討するための手法です。
これは、従来のFMEAのプロアクティブさを一段と推し進めた手法と言えます。
DRBFMは、特に既存製品に設計変更を加える場合に非常に有効で、予期せぬ問題発生を防ぎます。
DRBFMの流れ
DRBFMは、「設計の意図を明確にする」、「変更が及ぼす影響を分析する」、「失敗モードを想定し対応策を考える」というプロセスを基本とします。
設計者と多部門チームが参加し、より具体的な設計意図の理解と変更の影響評価を行います。
このプロセスを通じて、全社的に変更がどのように利用者や市場に影響を与えるかを深く検討し、実行可能な解決策を導き出します。
QFD、FMEA、DRBFMの相乗効果
QFDとFMEA、DRBFMはそれぞれが独立した手法ですが、組み合わせることでより一層効果的に品質保証活動を遂行できます。
QFDにより、顧客の声を製品設計に反映させつつ、FMEAでのリスク管理、DRBFMでの変更管理を通じ、品質の作り込みと信頼性の高い製品開発を実現します。
これらの手法を組み合わせることで、製品開発のあらゆる段階で潜在的な問題に対する理解が深まり、製品化後のトラブル発生を抑えることができます。
統合的アプローチの事例
例えば、ある新製品の開発において、まずQFDを用いて顧客要求を模索し、製品の要件を抽出します。
次に、FMEAを実施し、開発過程で考えられる全てのリスクに対して評価と対策を立てます。
さらに、設計変更が発生した際にはDRBFMで影響を精査し、予期せぬリスクを徹底的に排除します。
これにより、高品質かつ市場要求に即した製品を効率的に出荷できるのです。
未然防止のための効率化と改善への取り組み
未然防止活動としてのQFD、FMEA、DRBFMは、ただリスクを回避するだけでなく、プロジェクト全体の効率化にも貢献します。
問題を事前に特定し解決策を講じることで、開発工程における無駄を省き、タイムリーな製品供給を可能とします。
デジタルツールの活用
最近では、デジタルツールを活用したこれらのプロセスの効率化が進んでいます。
例えば、専用のソフトウェアを使用することで、QFDの行列やFMEAのリストはより迅速に作成され、関係者との情報共有も効率的に行われます。
このようにデジタル技術を適応させることで、迅速な意思決定とチーム間連携を促進し、手戻りや不要な作業コストを削減します。
現場での実践事例
具体的な現場での例として、デジタルツールによるリアルタイムのデータ収集と分析が挙げられます。
これにより、問題が発生する前に予兆を把握し、事前に対策を講じることが可能となります。
また、デジタル環境を整備することで、新たな問題への即応性を高め、お客様の期待に応える製造プロセスの実現が容易となります。
終わりに
製造業界の発展には、顧客ニーズを深く理解し、製品設計に反映することが不可欠です。
QFD、FMEA、DRBFMの活用とこれに伴う効率化の取り組みは、全体的な製品品質およびビジネスプロセスの改善を可能にします。
未然防止活動の強化により、製品の信頼性と競争力をさらに高め、よりよい製品供給を目指していきましょう。
資料ダウンロード
QCD管理受発注クラウド「newji」は、受発注部門で必要なQCD管理全てを備えた、現場特化型兼クラウド型の今世紀最高の受発注管理システムとなります。
ユーザー登録
受発注業務の効率化だけでなく、システムを導入することで、コスト削減や製品・資材のステータス可視化のほか、属人化していた受発注情報の共有化による内部不正防止や統制にも役立ちます。
NEWJI DX
製造業に特化したデジタルトランスフォーメーション(DX)の実現を目指す請負開発型のコンサルティングサービスです。AI、iPaaS、および先端の技術を駆使して、製造プロセスの効率化、業務効率化、チームワーク強化、コスト削減、品質向上を実現します。このサービスは、製造業の課題を深く理解し、それに対する最適なデジタルソリューションを提供することで、企業が持続的な成長とイノベーションを達成できるようサポートします。
製造業ニュース解説
製造業、主に購買・調達部門にお勤めの方々に向けた情報を配信しております。
新任の方やベテランの方、管理職を対象とした幅広いコンテンツをご用意しております。
お問い合わせ
コストダウンが利益に直結する術だと理解していても、なかなか前に進めることができない状況。そんな時は、newjiのコストダウン自動化機能で大きく利益貢献しよう!
(β版非公開)