- お役立ち記事
- 品質問題未然防止のための品質機能展開(QFD)の有効活用と効率的なFMEA・DRBFMの応用
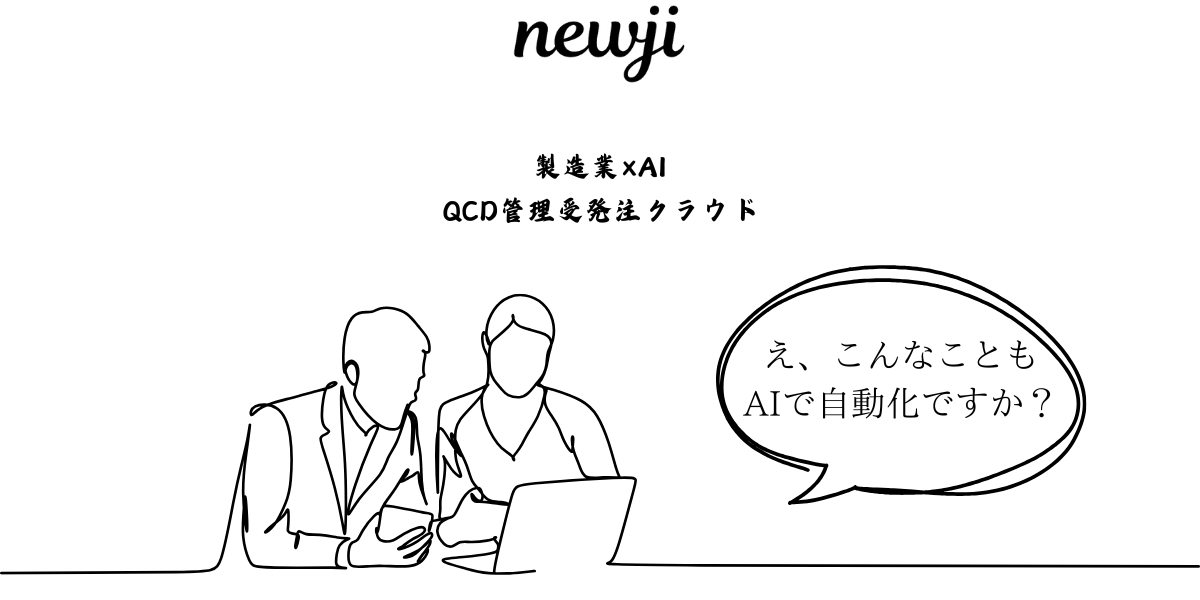
品質問題未然防止のための品質機能展開(QFD)の有効活用と効率的なFMEA・DRBFMの応用
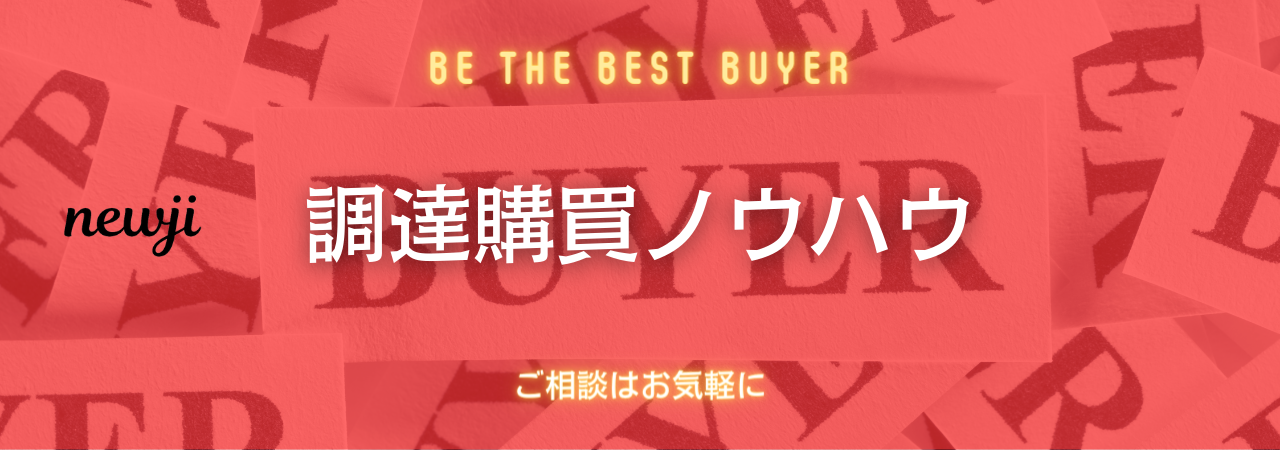
目次
品質機能展開(QFD)の基本とその重要性
品質機能展開(QFD)は、顧客の要求を製品の設計や製造工程に適切に反映させるための手法です。
QFDは1980年代にアメリカにもたらされ、日本の製造業界で多く活用されてきました。
特に、自動車産業など精密さが求められる産業で非常に有効です。
QFDを活用することで、顧客のニーズを正確に把握し、これを製品品質に反映させることが可能になります。
製造業の現場では、顧客から得た要求や市場調査を元に、設計者や生産者が具体的な製品特性に落とし込む作業が求められます。
この過程では、部門間の情報の行き違いや認識のズレが発生しやすく、結果として製品クオリティの低下やトラブルの原因となることがあります。
こうした問題を未然に防ぐために、早い段階でQFDを導入することが重要です。
QFDの実行プロセスの概要
QFDは、主として以下のプロセスで実行されます。
1. 顧客要求の明確化: 顧客が求める機能や特性を詳細に確認します。
2. これら要求を技術的特性に変換: 要求を具現化するための技術的要件を定義します。
3. 技術的特性の優先順位付け: どの特性を重視するか、必要な技術の重要性を評価します。
4. 必要なリソースや設備の確認: 技術特性を実現するために必要な要件、リソースを確認・整備します。
このプロセスを経ることで、顧客要求から一貫した製品仕様が形成され、効率的な製造工程が組立てられます。
FMEAとその重要性
FMEA(Failure Mode and Effects Analysis、故障モード影響解析)は不良や故障を事前に予測し、問題が起こる前に対策を立てるための手法です。
FMEAを活用することによって製品開発におけるリスクを大幅に軽減できるため、製造業において非常に重要なプロセスの一つです。
FMEAは、まず製品の設計や製造過程における潜在的な故障モードを特定します。
次に、その影響を評価し、発生頻度や影響の大きさに基づいてリスクを評価します。
最終的に、優先的に対策すべき問題点を明確にし、対策を講じます。
FMEAのステップ
1. 対象製品やシステムの分割: システム全体を理解し、解析しやすいようにサブシステムやコンポーネントに分割します。
2. 故障モードの特定: 各コンポーネントの故障モードを可能性に基づいてリストアップします。
3. 故障の影響分析: 各故障モードがシステム全体に与える影響を評価します。
4. リスクの評価と優先順位付け: 発生確率や影響度に基づいてリスクレベルを高・中・低に分類し、優先順位を付けます。
5. 軽減策の策定と実施: 重大な影響を及ぼす故障モードに対して、軽減策を講じ、実行します。
FMEAを実施する際、部門横断的なチームを編成し、多角的な視点から問題点を洗い出すことが効果的です。
DRBFMによる問題発見と改善
DRBFM(Design Review Based on Failure Modes、故障モードに基づく設計レビュー)は、すでに確立された設計上の変更がもたらすリスクを評価する手法です。
トヨタ自動車で開発され、20世紀末から広く製造業界で使われるようになりました。
DRBFMは既にある製品やプロセスに対する小さな変更が与える影響を見逃さないことで、品質を向上させるための戦術として位置づけられています。
DRBFM進行方法
1. 設計の変更点を特定: システムにおいてどの部分が変わるのかを具体的に明示します。
2. 変更による影響を検討: 変更が周辺システムや最終結果にどのような影響を及ぼすかを徹底的に議論します。
3. 代替案の提案と試行: 潜在的な問題に対して、改善策や代替案の策定→試行→評価を繰り返します。
このように設計変更に伴うリスクを最小限に抑えるためのDRBFMは、FMEAと相性が良く、一緒に活用することで問題予測能力が飛躍的に向上します。
QFD、FMEA、DRBFMの統合的活用で品質問題を未然に防ぐ
品質問題を未然に防止するためには、QFD、FMEA、DRBFMを統合的に活用することが望ましい結果をもたらします。
これら3つの手法は互いに補完し合い、それぞれの手法が持つ強みを最大化することで、最終的な製品品質を大幅に向上させることが可能です。
QFDによって顧客要求を具現化し、それを実現するための技術的特性を設計に組み込みます。
次に、FMEAを用いて設計段階でのリスクを予測し、適切な対策を講じます。
最後にDRBFMにより、設計変更や改良案が引き起こす潜在的な問題を洗い出し、設計段階での実装精度を高めます。
これらの過程を丁寧に進めることで、製造業界における品質問題を未然に防ぎ、最終製品のクオリティを高い水準で維持することが可能となります。
その結果、顧客満足度の向上やブランドの信頼性向上に繋がるでしょう。
製造業における競争力を強化し、持続的に成長するために、これらの手法を現場に効果的に取り入れることが求められます。
また、これらの手法を活用するためには、部門横断的なコミュニケーションとコラボレーションが重要です。
製造現場の従業員一人一人が品質意識を持ち、日常業務にこれらの手法を取り入れることで、未然にトラブルを防ぎ、より良い製品を顧客に提供することが可能となります。
これはまた、製造業の持続可能な成長を支える柱ともなり得ます。
資料ダウンロード
QCD調達購買管理クラウド「newji」は、調達購買部門で必要なQCD管理全てを備えた、現場特化型兼クラウド型の今世紀最高の購買管理システムとなります。
ユーザー登録
調達購買業務の効率化だけでなく、システムを導入することで、コスト削減や製品・資材のステータス可視化のほか、属人化していた購買情報の共有化による内部不正防止や統制にも役立ちます。
NEWJI DX
製造業に特化したデジタルトランスフォーメーション(DX)の実現を目指す請負開発型のコンサルティングサービスです。AI、iPaaS、および先端の技術を駆使して、製造プロセスの効率化、業務効率化、チームワーク強化、コスト削減、品質向上を実現します。このサービスは、製造業の課題を深く理解し、それに対する最適なデジタルソリューションを提供することで、企業が持続的な成長とイノベーションを達成できるようサポートします。
オンライン講座
製造業、主に購買・調達部門にお勤めの方々に向けた情報を配信しております。
新任の方やベテランの方、管理職を対象とした幅広いコンテンツをご用意しております。
お問い合わせ
コストダウンが利益に直結する術だと理解していても、なかなか前に進めることができない状況。そんな時は、newjiのコストダウン自動化機能で大きく利益貢献しよう!
(Β版非公開)