- お役立ち記事
- フレームワーク活用による業務効率・業務品質向上とその実践
月間76,176名の
製造業ご担当者様が閲覧しています*
*2025年3月31日現在のGoogle Analyticsのデータより
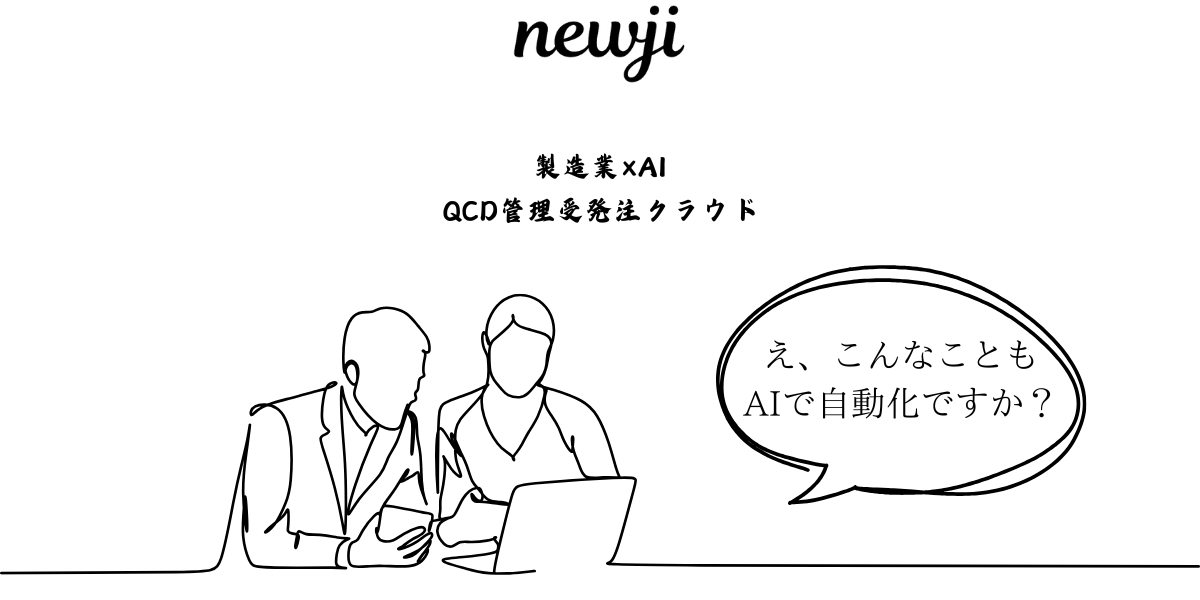
フレームワーク活用による業務効率・業務品質向上とその実践
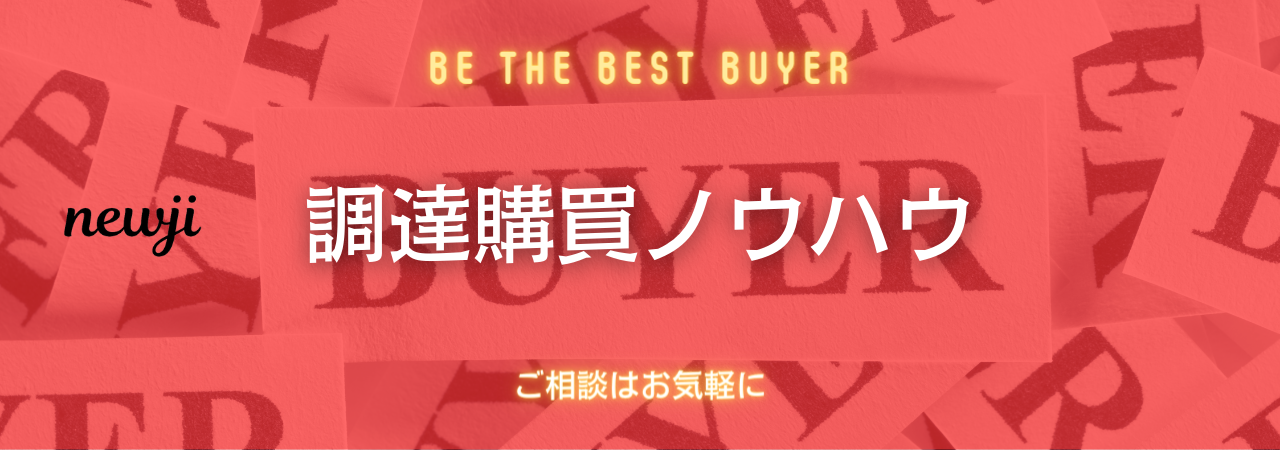
目次
はじめに
製造業における業務効率の向上と品質の改善は、企業の競争力を維持するために欠かせない要素です。
特に、このような成果を短期間で達成するためには、体系的なアプローチが求められます。
そこで、多くの場合で役立つのが「フレームワーク」の活用です。
フレームワークは、さまざまな場面で意思決定を簡素化し、効率的かつ効果的に活動を進めるための基盤を提供します。
この記事では、フレームワークの具体的な種類とその活用について解説し、実践的な手法を紹介します。
業務効率と品質向上におけるフレームワークの役割
業務効率と品質の向上におけるフレームワークの主な役割は、複雑な作業の簡素化、最適化された手順の提供、そしてチーム全体のコミュニケーションの改善です。
とりわけアナログ業界では、情報の整理と共有が難しいことが多いため、フレームワークによる明確なガイドラインが業務の透明性を高めます。
以下に、製造業で活用される代表的なフレームワークをいくつか紹介します。
PDCAサイクル
製造業では、改善を継続的に行うことが重視されます。
PDCAサイクルは、Plan(計画)、Do(実行)、Check(確認)、Act(改善)の4つのステップからなり、プロセスを継続的に改善する手法として非常に有効です。
このサイクルを回し続けることで、業務プロセスが徐々に洗練されていくのです。
5S活動
5S活動は整理、整頓、清掃、清潔、しつけという5つの日本語の頭文字を取った改善活動です。
職場環境を整えることで、作業効率や従業員の安全性を向上させます。
意外と侮られがちな活動ですが、整った職場は品質管理においても基礎的な重要性を持ちます。
Lean Manufacturing(リーン生産方式)
Lean Manufacturingは主に無駄を排除し、価値を最大化することに焦点を当てた経営手法です。
製造ラインでのムダの削減や、効率的な工程の設計、標準作業の設定などを通じて、効率的な生産を実現します。
具体的なフレームワーク活用例
それでは、これらのフレームワークが現場でどのように実際に役立てられるのか、具体例を通じて見ていきましょう。
生産ラインの効率化
例えば、ある部品工場での生産ラインにおける業務効率化を図るケースを考えます。
ここで使用されるフレームワークはLean Manufacturingと5S活動です。
まず、Lean Manufacturingの「ムダの排除」を念頭に置き、生産工程を分解し、各ステップの無駄を洗い出します。
次に、5S活動を導入し、作業場所の整理整頓を徹底させます。
これにより、工具や部品の出し入れが円滑になり、作業者の動線も短縮されました。
品質管理の向上
次に、品質管理の向上におけるPDCAサイクルの活用例を考えます。
ある部品の品質にばらつきがあるという問題に直面した場合、このサイクルを用いることで問題解決が図れます。
まず、品質向上のための計画(Plan)を立て、試験的に新たな検査工程を実行(Do)します。
その結果を検証して(Check)、得られたデータに基づき工程の修正や方法の改善(Act)を行います。
これを繰り返すことで、品質の安定化が図られます。
アナログ業界におけるフレームワーク活用の課題
伝統的なアナログ製造業の中には、フレームワークの導入が必ずしも簡単でない場合があります。
特にフレームワークの本質を理解し、それを実行に移すことがしばしば難しく感じられることもあるでしょう。
組織文化の壁
例えば、昭和から続く古い作業慣行や文化がある企業では、新しい手法の導入に抵抗を示すことがあります。
そのため、フレームワークを定着させるには、その価値を全員が理解し、共通認識として持つための教育が不可欠です。
ツールの選定と導入
また、アナログ業界ではデジタルツールの導入をためらうケースが見られます。
しかし、最近はフレームワークを支援するためのソフトウェアやアプリケーションが多く存在します。
これらを適切に組み合わせることで、より効率的にフレームワークを活用できます。
フレームワークを活用するための成功要因
フレームワークを効果的に導入するための鍵は、従業員の理解と協力、適切なツールの選定、そして持続可能なプロセスへの整備です。
従業員の巻き込み
まず、フレームワークの価値を組織全体で共有し、各メンバーがそのメリットを理解しているかが重要です。
動機付けを行い、従業員が自発的に取り組む環境を整えることが成功への第一歩です。
試行錯誤と調整
次に、初めから100%完璧なフレームワークの実行を期待するのではなく、試行錯誤を重ねることが重要です。
PDCAサイクルを回すように、自社に最適化されたフレームワークを構築し、調整し続ける姿勢が必要です。
結果の可視化と評価
最終的に、フレームワークを利用した成果を数値やデータで可視化し、それを評価することが欠かせません。
モチベーションを維持し、さらなる改善へのきっかけとなります。
まとめ
フレームワークを活用することは、業務効率と品質の向上を実現するための有効な手段です。
特に製造業界においては、日常的に改善を行い、業務を最適化し続けることが成長の鍵となります。
アナログ文化が色濃く残る業界であっても、適切な方法でフレームワークを導入し運用していくことで、持続的な成長を遂げることが可能です。
ぜひこれを機に、フレームワークの活用を検討し、貴社の成長に役立ててください。
資料ダウンロード
QCD管理受発注クラウド「newji」は、受発注部門で必要なQCD管理全てを備えた、現場特化型兼クラウド型の今世紀最高の受発注管理システムとなります。
ユーザー登録
受発注業務の効率化だけでなく、システムを導入することで、コスト削減や製品・資材のステータス可視化のほか、属人化していた受発注情報の共有化による内部不正防止や統制にも役立ちます。
NEWJI DX
製造業に特化したデジタルトランスフォーメーション(DX)の実現を目指す請負開発型のコンサルティングサービスです。AI、iPaaS、および先端の技術を駆使して、製造プロセスの効率化、業務効率化、チームワーク強化、コスト削減、品質向上を実現します。このサービスは、製造業の課題を深く理解し、それに対する最適なデジタルソリューションを提供することで、企業が持続的な成長とイノベーションを達成できるようサポートします。
製造業ニュース解説
製造業、主に購買・調達部門にお勤めの方々に向けた情報を配信しております。
新任の方やベテランの方、管理職を対象とした幅広いコンテンツをご用意しております。
お問い合わせ
コストダウンが利益に直結する術だと理解していても、なかなか前に進めることができない状況。そんな時は、newjiのコストダウン自動化機能で大きく利益貢献しよう!
(β版非公開)