- お役立ち記事
- Evolution of 3D Printing Technology Revolutionizing Manufacturing
Evolution of 3D Printing Technology Revolutionizing Manufacturing
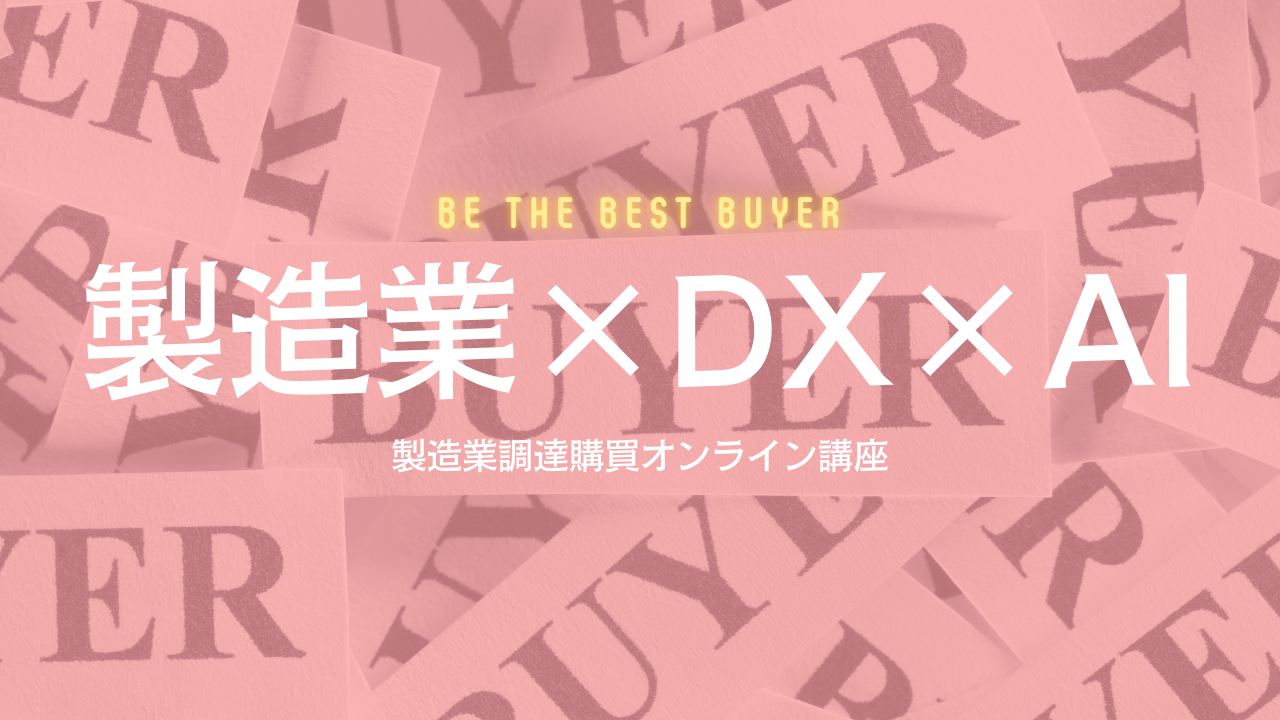
3D printing technology, also known as additive manufacturing, has come a long way since its origins in the 1980s. What started as a novelty method for creating plastic prototypes has evolved into a revolutionary technique for manufacturing complex products. Over the past few decades, 3D printing has progressed significantly, allowing industries to design and produce goods in new, more efficient ways.
The first 3D printers were large and expensive machines that worked slowly. They were mainly used by engineers and designers to print plastic models of prototypes before committing to costly tooling or manufacturing processes. In the late 1980s and early 1990s, some of the earliest pioneers in 3D printing technology developed stereolithography, which worked by curing liquid resin into solid layers with an ultraviolet laser. This was one of the first commercially successful additive manufacturing methods.
In the 1990s and 2000s, major technological advances took 3D printing to new levels. Fused deposition modeling 3D printers gained popularity, working by melting and depositing materials layer by layer through an extrusion nozzle. New materials like nylon and carbon fiber entered the fray, expanding the potential applications beyond plastics. Desktop 3D printers also hit the consumer market, making additive manufacturing accessible to schools, makerspaces, and creative professionals. 3D Systems introduced PolyJet technology for multimaterial color 3D printing. Rapid progress was being made.
The 2010s brought 3D printing into the mainstream. Higher quality desktop machines dropped substantially in price, under $1,000 for basic models. Major companies like 3D Systems, Stratasys, and MakerBot led the consumer 3D printing revolution as the technology spread virally online. Desktop 3D scanning allowed digital files to be created from physical objects. Complex metal and elastomer additive manufacturing processes were developed for industries. The possibilities seemed limitless.
Today, 3D printing is a diverse field that continues pushing boundaries. Selective laser sintering can print industrial-grade parts in metals like titanium and tool steel. Multi-jet fusion uses droplets of different photopolymers to create vivid, strong final products. New print heads offer nanoscale resolution. Bioprinting techniques are generating living human tissue and bringing organ transplants closer to reality. Advanced robots print entire structures without assembly. Car companies are 3D printing jigs, jet engines, and even complete vehicles. The International Space Station now has an onboard 3D printer for in-space manufacturing.
Across industries, 3D printing is revolutionizing traditional manufacturing in countless ways. It allows virtual designs to be realized physically faster and more cost-effectively than ever before. Complex geometries that were previously impossible to produce can now be readily 3D printed with moving internal structures. Mass customization becomes a reality as printing one item is as simple as producing millions. Designs can be optimized for weight reductions, strengthening, and efficient material usage. Supply chains gain flexibility and resilience.
On the consumer side, the “Maker Movement” takes advantage of desktop 3D printers to empower creativity. Hobbyists, students, and entrepreneurs design and print toys, replacement parts, works of art, musical instruments, prosthetics, and more. 3D scanning and printing help preserve cultural heritage artifacts. With open-source sharing of digital 3D models, communities globally collaborate on projects online. Education embraces 3D printing to bring subjects to life for students in tactile, hands-on ways.
Looking ahead, researchers foresee 3D printing transforming entire industries within the next decade. Automotive, aerospace, medical, architecture and more will adopt additive manufacturing for large-scale production. Future printers may print fully functional devices filled with electrical components. Scientists are working on 4D printing that produces objects able to change shapes and properties over time. Even nuclear fusion and space elevators may leverage 3D printing technologies one day. By embracing constant forward progress, the future of 3D printing promises to revolutionize how products are designed, made, distributed and used worldwide for generations to come.
資料ダウンロード
QCD調達購買管理クラウド「newji」は、調達購買部門で必要なQCD管理全てを備えた、現場特化型兼クラウド型の今世紀最高の購買管理システムとなります。
ユーザー登録
調達購買業務の効率化だけでなく、システムを導入することで、コスト削減や製品・資材のステータス可視化のほか、属人化していた購買情報の共有化による内部不正防止や統制にも役立ちます。
NEWJI DX
製造業に特化したデジタルトランスフォーメーション(DX)の実現を目指す請負開発型のコンサルティングサービスです。AI、iPaaS、および先端の技術を駆使して、製造プロセスの効率化、業務効率化、チームワーク強化、コスト削減、品質向上を実現します。このサービスは、製造業の課題を深く理解し、それに対する最適なデジタルソリューションを提供することで、企業が持続的な成長とイノベーションを達成できるようサポートします。
オンライン講座
製造業、主に購買・調達部門にお勤めの方々に向けた情報を配信しております。
新任の方やベテランの方、管理職を対象とした幅広いコンテンツをご用意しております。
お問い合わせ
コストダウンが利益に直結する術だと理解していても、なかなか前に進めることができない状況。そんな時は、newjiのコストダウン自動化機能で大きく利益貢献しよう!
(Β版非公開)