- お役立ち記事
- 圧延技術の進化:製造業のコスト削減と効率向上への道
月間77,185名の
製造業ご担当者様が閲覧しています*
*2025年2月28日現在のGoogle Analyticsのデータより
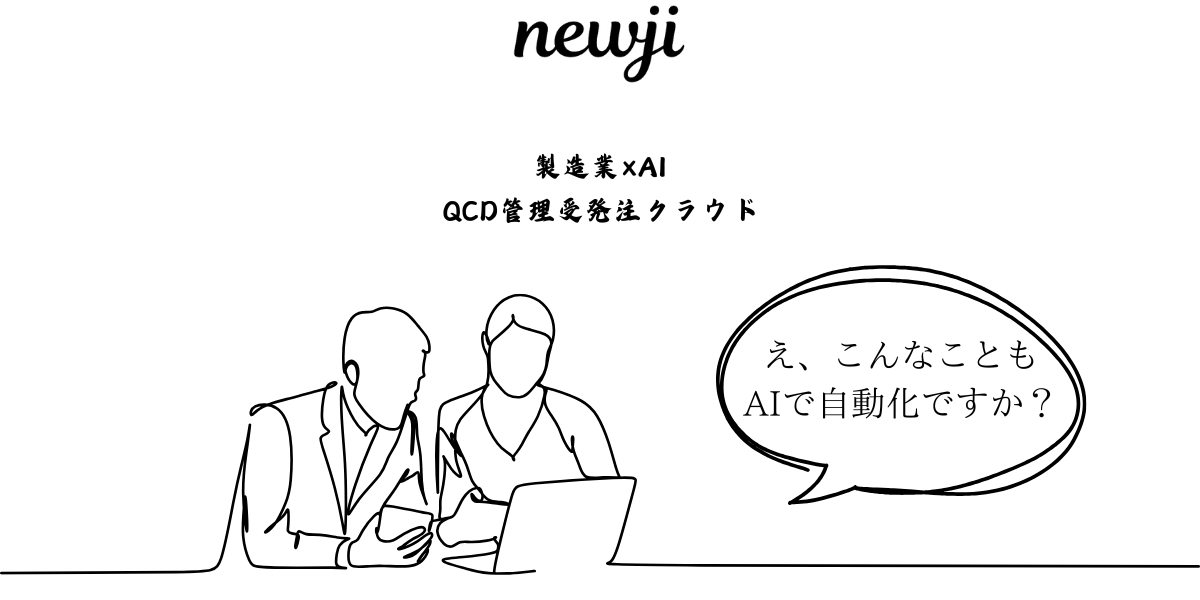
圧延技術の進化:製造業のコスト削減と効率向上への道
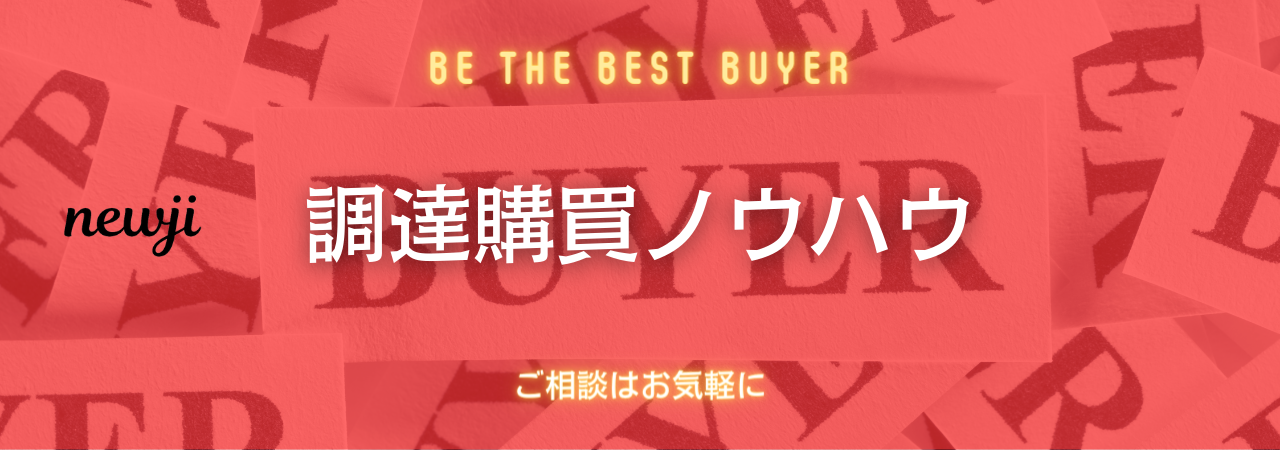
目次
導入
製造業において、圧延技術は材料の品質向上や生産効率の最適化において不可欠な役割を果たしています。長年にわたり進化を遂げてきた圧延技術は、コスト削減と効率向上の両面で製造現場に多大な貢献をしています。本記事では、圧延技術の基礎からその進化、具体的なメリット・デメリット、さらにはサプライヤーとの交渉術や市場動向、成功事例に至るまで、実践的な視点で詳しく解説します。製造業の調達購買部門に携わる方々にとって、圧延技術の理解と活用は、競争力の維持・向上に直結する重要な要素となります。
圧延技術の基礎
圧延の基本原理
圧延とは、材料をローラーの間を通すことで塑性変形させ、所望の形状や厚さに加工する製造プロセスです。主に金属材料に適用され、高温または常温で行われます。高温圧延では材料の延性が増し、大量生産が可能となります。一方、冷間圧延は材料の強度や表面品質を向上させる効果があります。圧延は延伸加工の一種であり、材料の内部組織を均一化し、物理的特性を向上させることが目的です。
圧延の種類
圧延には主に以下の種類があります。
1. **熱間圧延**: 材料を再結晶温度以上で加工する方法。高温により材料の塑性が向上し、大量生産に適しています。鋼板やアルミニウム板の製造に広く用いられます。
2. **冷間圧延**: 材料を室温または低温で加工する方法。高い寸法精度や表面品質を達成でき、材料の強度を向上させることができます。
3. **ロールド圧延**: 複数のローラーを用いて材料を連続的に加工する方法。均一な厚さや形状を実現するために使用されます。
4. **ホットロール圧延とコールドロール圧延**: 加工温度や目的に応じて、ホットロール圧延とコールドロール圧延が使い分けられます。
圧延技術の進化
冷間圧延から熱間圧延への進化
初期の圧延技術は低温での加工が主流でしたが、材料の延性や生産性の向上を求めて熱間圧延が開発されました。熱間圧延により、材料の塑性が向上し、より大きな変形を加えることが可能となりました。また、高温での加工は材料内部の応力を緩和し、後工程での冷間加工の効率を高める効果もあります。これにより、製造工程全体の効率化とコスト削減が実現されました。
自動化とデジタル制御の導入
近年の圧延技術の進化には、自動化とデジタル制御の導入が大きく寄与しています。自動化により、生産ラインの安定性と生産性が向上し、人為的なミスを減少させることができます。デジタル制御システムは、圧延プロセスをリアルタイムで監視・調整し、材料の品質を一貫して維持することを可能にしました。また、IoT技術の活用により、設備の稼働状況や生産データの収集・分析が容易になり、予防保全や生産計画の最適化にも貢献しています。
新素材の開発と適用
材料科学の進展に伴い、新素材の開発とそれに伴う圧延技術の適用が進んでいます。高強度鋼や軽量合金など、性能向上を目的とした新素材は、圧延プロセスの最適化を必要とします。これにより、特定の材料特性を最大限に引き出すための圧延条件や加工方法が研究され、実用化が進んでいます。また、環境に配慮した素材の開発も進み、持続可能な製造プロセスの構築に寄与しています。
製造業におけるコスト削減への影響
エネルギー効率の向上
圧延技術の進化により、エネルギー効率が大幅に向上しました。精密な温度制御や最適な圧延速度の設定により、エネルギー消費を最小限に抑えつつ、高品質な製品を生産することが可能となります。また、最新の圧延設備はエネルギー回収システムを搭載しており、加工中に発生する廃熱を再利用することで、全体のエネルギー使用量を削減しています。
材料の最適化と廃棄物削減
圧延技術の高度化により、材料の無駄を減少させることが可能となりました。精密な圧延プロセスにより、材料の切断や加工時のロスが最小化され、原材料の使用効率が向上します。また、廃棄物のリサイクルが容易になり、環境負荷の低減にも寄与しています。これにより、製造コストの削減とともに、持続可能な生産体制の構築が可能となります。
生産速度の向上によるコスト削減
自動化とデジタル制御の導入により、生産速度が飛躍的に向上しました。高速で安定した圧延プロセスは、大量生産を可能にし、製品1単位あたりの生産コストを大幅に削減します。また、生産ラインの稼働率が向上し、設備の有効利用が促進されることで、資本投資の効率化も実現します。これにより、競争力の強化とともに、コスト面での優位性を確保することができます。
効率向上への寄与
生産ラインの自動化
圧延工程の自動化は、生産ライン全体の効率を飛躍的に向上させます。自動化システムは、材料の供給や製品の取り出しを迅速かつ正確に行い、人手による作業のばらつきを排除します。これにより、生産のリードタイムが短縮され、製品の納期遵守率が向上します。また、自動化により労働コストの削減とともに、労働環境の改善が図られます。
品質管理の強化
最新の圧延技術では、リアルタイムでの品質管理が可能となっています。センサーやカメラを用いたモニタリングにより、製品の寸法や表面状態を常時監視し、異常が検知された場合には即座にフィードバックされます。これにより、不良品の発生を未然に防ぎ、品質の一貫性を維持することができます。また、データの蓄積と解析により、品質向上のための継続的な改善活動が可能となります。
サプライチェーンの最適化
圧延技術の進化に伴い、サプライチェーン全体の最適化が進んでいます。デジタルツインやリアルタイムデータの活用により、材料の調達から製品の出荷までのプロセス全体を一元管理することが可能となります。これにより、在庫の最適化や納期の短縮が実現し、サプライチェーン全体の効率が向上します。また、需要予測の精度が向上することで、過剰在庫や欠品のリスクを低減することができます。
メリットとデメリット
圧延技術のメリット
圧延技術の主なメリットは以下の通りです。
1. **高精度な加工**: 精密な寸法管理が可能であり、製品の一貫性が保たれます。
2. **生産性の向上**: 自動化と高速圧延により、短時間で大量生産が可能です。
3. **材料コストの削減**: 材料の無駄を減らし、効率的な使用が促進されます。
4. **品質の向上**: 表面品質や内部構造の均一化が実現され、不良品の発生が減少します。
5. **エネルギー効率**: 最新の技術により、エネルギー消費を抑えつつ高品質な製品を生産できます。
圧延技術のデメリット
一方で、圧延技術には以下のようなデメリットも存在します。
1. **初期投資の高さ**: 最新の圧延設備は高額であり、初期投資が大きくなります。
2. **メンテナンスコスト**: 高度な設備は維持管理にコストがかかる場合があります。
3. **技術習得の必要性**: 複雑な圧延プロセスを最適化するためには、専門的な知識や技術が必要です。
4. **材料の制約**: 圧延に適さない材料や特定の合金は加工が困難な場合があります。
5. **設備の柔軟性**: 特定の製品に特化した設備は、製品ラインの変更に対して柔軟性が低いことがあります。
サプライヤーとの交渉術
信頼関係の構築
サプライヤーとの良好な関係は、圧延プロセスの安定と品質の維持に不可欠です。定期的なコミュニケーションや共同の品質改善活動を通じて、信頼関係を築くことが重要です。信頼関係が構築されることで、緊急時の対応や柔軟な納期調整が可能となり、製造現場の安定運営に寄与します。
価格交渉の戦略
価格交渉では、長期的なパートナーシップを前提とした戦略が有効です。大量購入による割引や定期的な発注量の確保を申し出ることで、価格の優位性を獲得することができます。また、市場動向や原材料価格の変動に関する情報を積極的に共有し、双方にとって公正な価格設定を目指すことが重要です。適切な交渉準備とデータ分析により、効果的な価格交渉を実現できます。
長期的なパートナーシップの構築
単発的な取引ではなく、長期的な視点でのパートナーシップを構築することが、圧延プロセスの安定と継続的な改善に繋がります。共同での技術開発や品質管理活動の推進により、サプライヤーと共同で製品の品質向上やコスト削減を図ることが可能です。また、相互に信頼し合う関係性が、トラブル発生時の迅速な対応や柔軟な調整を可能にします。
市況の影響と対応策
原材料価格の変動
世界的な経済状況や需要の変動により、原材料価格は常に変動しています。圧延プロセスにおいては、鉄鋼やアルミニウムなどの主要材料の価格変動が製造コストに直結します。これに対応するためには、長期的な供給契約の締結や先物取引の活用、複数のサプライヤーとの関係構築が有効です。また、代替材料の検討や材料の再利用などもコスト管理の一環として重要です。
市場需要の変化
市場の需要が変動する中で、柔軟な生産体制の構築が求められます。圧延設備の柔軟性を高めるためには、モジュール化された生産ラインや多品種少量生産に対応可能な設備投資が必要です。需要予測の精度を向上させるために、データ分析やAI技術を活用し、需要変動に迅速に対応できる体制を整えることが重要です。
技術革新への対応
技術の進化に遅れをとらないためには、継続的な技術投資と社員のスキルアップが不可欠です。最新の圧延技術や設備の導入だけでなく、現場スタッフへの教育・研修を通じて、新技術の理解と活用能力を高めることが重要です。また、技術革新の動向を継続的にモニタリングし、自社の圧延プロセスに適用可能な新技術を積極的に取り入れる姿勢が求められます。
成功事例の紹介
国内企業の成功事例
日本国内の大手製鉄企業では、先進的な圧延技術の導入により、製品の品質向上と生産コストの削減に成功しています。例えば、最新のデジタル制御システムを導入することで、温度管理や圧延速度の最適化を実現し、高品質な鋼板の安定供給を可能にしました。また、圧延プロセスの自動化により、労働コストの削減と生産性の向上を達成しています。これにより、国内外の競争力を強化し、持続的な成長を遂げています。
海外企業の成功事例
海外においても、圧延技術の進化を活用して成功を収めている企業が多く存在します。例えば、欧州の自動車部品メーカーでは、最新の冷間圧延技術を採用することで、軽量かつ高強度な部品を効率的に生産しています。これにより、燃費性能の向上と製品の品質保証を同時に実現しています。また、北米の建材メーカーでは、熱間圧延技術の高度化により、大規模な建材の一貫生産が可能となり、生産コストの大幅な削減と市場シェアの拡大に成功しています。
まとめ
圧延技術は製造業において、コスト削減と効率向上を実現するための重要な要素です。技術の進化により、エネルギー効率の向上や生産ラインの自動化、品質管理の強化が可能となり、持続的な競争力の維持が実現されています。また、サプライヤーとの信頼関係の構築や市場動向への柔軟な対応も、圧延プロセスの最適化には欠かせません。成功事例からも分かるように、最新の圧延技術を適切に導入し活用することで、製造業の発展と持続可能な成長に大きく寄与することができます。今後も技術革新とともに、圧延技術は製造業のコスト削減と効率向上に向けて、さらなる進化を遂げていくことでしょう。
資料ダウンロード
QCD管理受発注クラウド「newji」は、受発注部門で必要なQCD管理全てを備えた、現場特化型兼クラウド型の今世紀最高の受発注管理システムとなります。
ユーザー登録
受発注業務の効率化だけでなく、システムを導入することで、コスト削減や製品・資材のステータス可視化のほか、属人化していた受発注情報の共有化による内部不正防止や統制にも役立ちます。
NEWJI DX
製造業に特化したデジタルトランスフォーメーション(DX)の実現を目指す請負開発型のコンサルティングサービスです。AI、iPaaS、および先端の技術を駆使して、製造プロセスの効率化、業務効率化、チームワーク強化、コスト削減、品質向上を実現します。このサービスは、製造業の課題を深く理解し、それに対する最適なデジタルソリューションを提供することで、企業が持続的な成長とイノベーションを達成できるようサポートします。
製造業ニュース解説
製造業、主に購買・調達部門にお勤めの方々に向けた情報を配信しております。
新任の方やベテランの方、管理職を対象とした幅広いコンテンツをご用意しております。
お問い合わせ
コストダウンが利益に直結する術だと理解していても、なかなか前に進めることができない状況。そんな時は、newjiのコストダウン自動化機能で大きく利益貢献しよう!
(β版非公開)