- お役立ち記事
- トヨタ生産方式で定義する「要因」と「原因」の違い
トヨタ生産方式で定義する「要因」と「原因」の違い
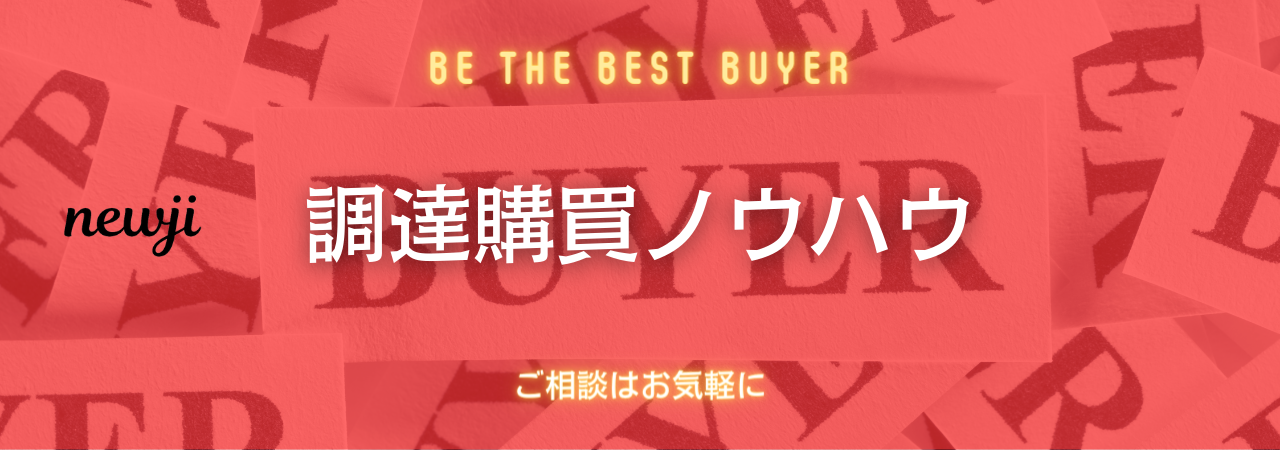
目次
はじめに
トヨタ生産方式は、製造業界における最も効率的で効果的な生産システムとして広く認知されています。
その中で重要な概念の一つが「要因」と「原因」の違いです。
この二つの概念を正しく理解し応用することは、問題解決能力の向上に繋がります。
この記事では、製造業の現場で役立つように「要因」と「原因」の違いを解説し、その重要性や実際の応用例について詳しく説明します。
「要因」と「原因」の基本的な違い
まず、「要因」と「原因」の基本的な違いについて説明しましょう。
「要因」は、その状況を形作る様々な条件や要素を指します。
一方、「原因」は特定の出来事や結果に直接的に影響を与える単一または複数の事象を意味します。
製造業の現場では、問題が発生した際に、表面的な理由だけでなく深層にある「要因」を探り出すことが重要です。
例として見る「要因」と「原因」
例えば、製品不良率が高いという問題があるとします。
「原因」は、検査工程でのチェックミスかもしれませんが、「要因」としては不十分な教育、設備の老朽化、工場の作業環境など、多くの背景が存在することがあります。
現場では、表面的な「原因」だけでなく「要因」にまで目を向けて改善に繋げることが大切です。
トヨタ生産方式の「真因分析(ルートコーズ・アナリシス)」の意義
要因と原因を区別することは、問題解決の根幹に関わる重要な概念です。
トヨタ生産方式では、「真因分析」を用いて、問題の本質に迫ります。
特に「なぜなぜ分析」は、問題を深掘りするために非常に効果的です。
これは「なぜ」を5回繰り返すことで、表面的な原因を超えた要因を模索する手法です。
「なぜなぜ分析」の進め方
「なぜなぜ分析」は、簡単なプロセスですが、効果的な問題解決において非常に強力です。
例として、不良品が多い場合の分析を考えましょう。
1. なぜ不良品が多いのか?
– チェック工程でミスが発生しているため。
2. なぜチェック工程でミスが多いのか?
– 作業者が手順を遵守していないため。
3. なぜ手順を遵守していないのか?
– 作業手順が複雑で作業者に理解されていないため。
4. なぜ作業手順が理解されていないのか?
– 十分な教育やトレーニングが行われていないため。
5. なぜ十分な教育やトレーニングが行われていないのか?
– トレーニングプログラムが計画されていないため。
このプロセスを通じて、表層的な原因だけでなく、根本的な要因までを明確にすることができます。
要因と原因の違いを理解することのメリット
要因と原因の違いを理解することで、製造業やサプライチェーン全体にわたる多くのメリットを享受することができます。
以下にその主なメリットを挙げます。
問題解決能力の向上
問題解決において、表面的な原因だけでなく、深層にある要因にアプローチすることにより、持続的な改善を実現できます。
その結果、同じ問題の再発を防ぎ、品質向上を図ることに繋がります。
生産性の向上
要因を把握して生産プロセスを調整することで、リソースの最適化が可能になります。
無駄を減らし、効率的な生産ラインを構築することで、生産性向上に繋がります。
従業員の成長と能力開発
「なぜなぜ分析」などの手法を用いた教育トレーニングは、従業員の問題解決能力を養い、彼らの成長を促進します。
自らの業務改善に関与することでモチベーションも向上します。
製造業の現場における実践例
トヨタ生産方式の考え方を取り入れるには、現場での実践が欠かせません。
いくつかの事例を紹介しましょう。
現場での「要因」と「原因」の特定と改善
ある工場でラインストップが頻発する問題が発生しました。
原因は一見、ラインオペレーターのスキル不足と思われましたが、実際はオペレーターの教育不足が要因でした。
現場では新たな教育プログラムを導入し、さらに自動ライン監視システムを導入することで、ラインストップの頻度を大幅に減少させました。
サプライヤーとの協力による問題解決
品質不良の原因がサプライヤーにある場合、トヨタ生産方式では、単にサプライヤーの変更ではなく協力して問題解決を図ることを重視します。
サプライヤーと共同で原因と要因を分析し、改善策を打ち出すことで、サプライチェーン全体の改善に寄与します。
まとめ
「要因」と「原因」を深く理解し、区別することは、製造業の問題解決能力を高めるために非常に重要です。
トヨタ生産方式を活用したアプローチは、業界全体のプロセス改善、効率化、そして品質向上を実現するための強力なツールとなります。
この知識を活用して、より良い製品作りに寄与できることを願っています。
資料ダウンロード
QCD調達購買管理クラウド「newji」は、調達購買部門で必要なQCD管理全てを備えた、現場特化型兼クラウド型の今世紀最高の購買管理システムとなります。
ユーザー登録
調達購買業務の効率化だけでなく、システムを導入することで、コスト削減や製品・資材のステータス可視化のほか、属人化していた購買情報の共有化による内部不正防止や統制にも役立ちます。
NEWJI DX
製造業に特化したデジタルトランスフォーメーション(DX)の実現を目指す請負開発型のコンサルティングサービスです。AI、iPaaS、および先端の技術を駆使して、製造プロセスの効率化、業務効率化、チームワーク強化、コスト削減、品質向上を実現します。このサービスは、製造業の課題を深く理解し、それに対する最適なデジタルソリューションを提供することで、企業が持続的な成長とイノベーションを達成できるようサポートします。
オンライン講座
製造業、主に購買・調達部門にお勤めの方々に向けた情報を配信しております。
新任の方やベテランの方、管理職を対象とした幅広いコンテンツをご用意しております。
お問い合わせ
コストダウンが利益に直結する術だと理解していても、なかなか前に進めることができない状況。そんな時は、newjiのコストダウン自動化機能で大きく利益貢献しよう!
(Β版非公開)