- お役立ち記事
- トヨタ生産方式で定義する「要因」と「原因」の違い
トヨタ生産方式で定義する「要因」と「原因」の違い
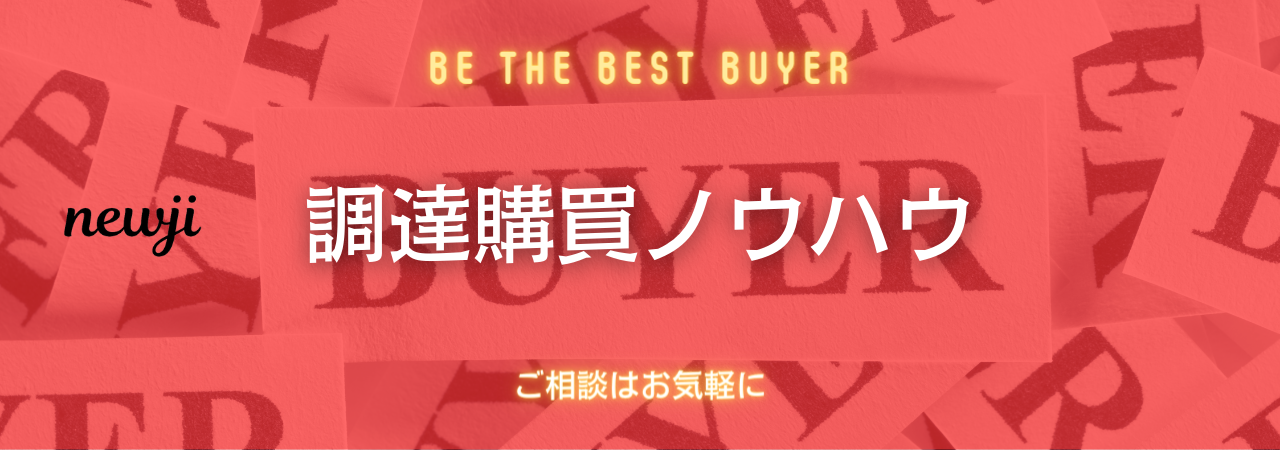
目次
はじめに
製造業において「トヨタ生産方式」は効率的で高品質な生産を実現するための重要なフレームワークとして知られています。
その中で特に注目すべきは、「要因」と「原因」の違いに関する理解です。
この二つの概念を正しく理解し、現場で適切に活用することが、問題解決力を飛躍的に高める鍵となります。
この記事では、「要因」と「原因」の違いを詳しく解説し、どのように現場で活用できるかを具体的に探っていきます。
「要因」と「原因」とは何か
トヨタ生産方式では、「要因」と「原因」は極めて重要な概念です。
「要因」とは、結果や現象を生み出す要素のことを指します。
一方、「原因」は、特定の現象を直接的に引き起こしたものを意味します。
言い換えれば、「原因」は一つの出来事を特定するのに対し、「要因」は多様な出来事や背景を含んでいます。
「要因」の具体的な理解
「要因」は、問題や現象を取り巻く複数の条件や背景を指します。
例えば、製造ラインでの不良品発生を考えたとき、その不良品発生の「要因」には、作業手順、設備の状態、材料の品質、作業員のスキルなど様々な要因が含まれます。
ここで重要なのは、これら複数の「要因」が絡み合って結果として不良品が生じるという点です。
「原因」の具体的な理解
一方で、「原因」は具体的なトリガーを見出します。
先の不良品発生の場合、たとえば「操作ミス」が「原因」と特定されることがあります。
この場合、操作ミスそのものが直接的な不良品発生のきっかけとなっているので、「原因」とされます。
「要因」と「原因」の違いをどう活用するか
それでは、実際の現場でこれらの概念をどのように活用すべきでしょうか。
以下に具体的なアプローチをご紹介します。
問題解決への応用
まず重要なのは、「要因」と「原因」を区別して分析することです。
「要因」を把握することで、問題が発生する背景を総合的に理解できます。
その上で、「原因」を特定することで直接対策を講じることが可能になります。
これは、表面的な問題だけではなく、根本的な改善を目指すために欠かせません。
改善活動の実践
改善活動においては、まず「要因」を洗い出すためのデータ収集と分析が必要となります。
次にそのデータに基づいて、「原因」を見極め対策を検討します。
このプロセスを繰り返すことにより、より効率的で効果的な改善活動が実現できます。
「要因」と「原因」を区別するための手法
現場で「要因」と「原因」を明確にするために、いくつかの具体的な手法があります。
なぜなぜ分析
「なぜなぜ分析」は、現場で非常に有効な手法です。
問題が起きた時に「なぜ?」を繰り返し問うことで、表面的な原因だけでなく、根本的な問題を探し出すことができます。
このプロセスは、深く掘り下げて考える力を養い、「要因」と「原因」をしっかり区別する習慣をつけます。
特性要因図の活用
特性要因図(魚の骨図)は、問題の「要因」を視覚化するためのツールとして有効です。
問題を特性(結果)として、各要因を骨のように配置することで、どの要因がどのように関連しているかが一目でわかります。
図解化することで、全体像を理解しやすくなり、分析がしやすくなります。
昭和から踏み出さないアナログ業界での適用
昭和時代の製造現場では、アナログ的な手法が主流でした。
しかし、現在でもこれらは根強く残っており、その特有の経験が新しい時代の方法と融合することができます。
アナログ的手法とデジタル化の融合
アナログ的手法としては、現場の経験を重視し、視覚的なチェックや手触り、音での確認などがあります。
これらはデジタル化が進んだ今でも、適切に使えば非常に価値のあるものです。
デジタルツールと併用することで、データの正確性と現場の知見を融合し、「要因」と「原因」をより明確にできます。
現場主義の重要性
トヨタ生産方式が強調する現場主義は、構造的な問題を、「行って見て、考え実行する」ことによって即座に見つけ出し、対処していくことを促します。
このアナログ的とも言えるアプローチは、デジタル技術が発達した今日でも大事にされるべきで、現場の声を無視することなく取り入れていくことが求められています。
まとめ
トヨタ生産方式における「要因」と「原因」の理解は、問題を深く分析し、根本的な解決を目指すために重要です。
これらを区別し現場で活用することにより、組織全体の生産性と品質が向上します。
昭和のアナログ的な特徴を、現代のデジタルツールと適切に組み合わせ、より進化した製造業を実現することが一つの鍵となるでしょう。
製造業に関わる皆さんが、これらの技術と知識を実践することで、更なる成長を遂げることを願っています。
資料ダウンロード
QCD調達購買管理クラウド「newji」は、調達購買部門で必要なQCD管理全てを備えた、現場特化型兼クラウド型の今世紀最高の購買管理システムとなります。
ユーザー登録
調達購買業務の効率化だけでなく、システムを導入することで、コスト削減や製品・資材のステータス可視化のほか、属人化していた購買情報の共有化による内部不正防止や統制にも役立ちます。
NEWJI DX
製造業に特化したデジタルトランスフォーメーション(DX)の実現を目指す請負開発型のコンサルティングサービスです。AI、iPaaS、および先端の技術を駆使して、製造プロセスの効率化、業務効率化、チームワーク強化、コスト削減、品質向上を実現します。このサービスは、製造業の課題を深く理解し、それに対する最適なデジタルソリューションを提供することで、企業が持続的な成長とイノベーションを達成できるようサポートします。
オンライン講座
製造業、主に購買・調達部門にお勤めの方々に向けた情報を配信しております。
新任の方やベテランの方、管理職を対象とした幅広いコンテンツをご用意しております。
お問い合わせ
コストダウンが利益に直結する術だと理解していても、なかなか前に進めることができない状況。そんな時は、newjiのコストダウン自動化機能で大きく利益貢献しよう!
(Β版非公開)