- お役立ち記事
- 試作段階での故障解析技術と改善事例
月間76,176名の
製造業ご担当者様が閲覧しています*
*2025年3月31日現在のGoogle Analyticsのデータより
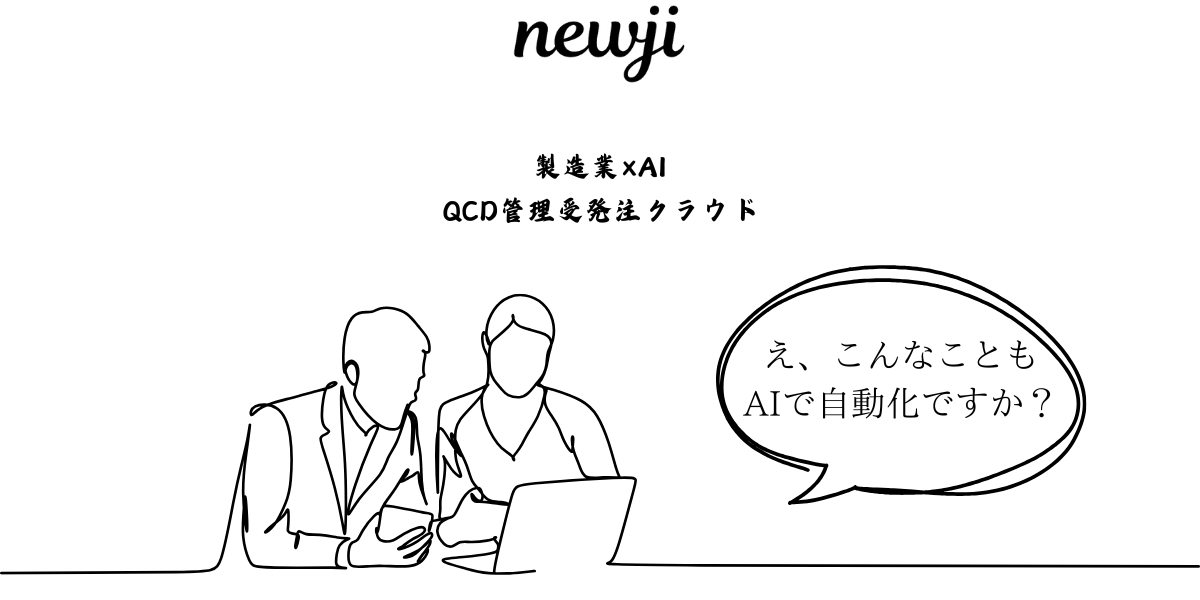
試作段階での故障解析技術と改善事例
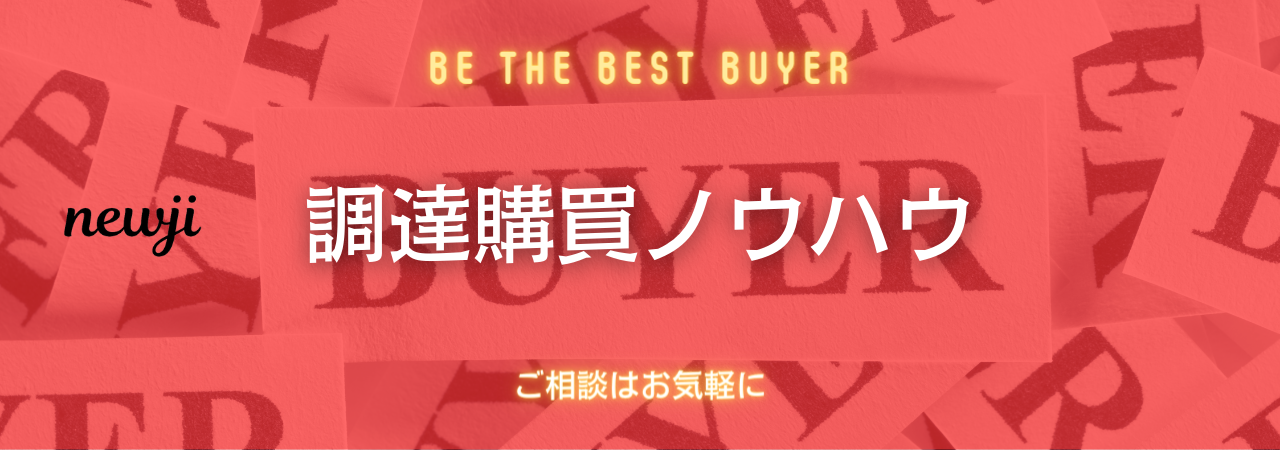
目次
試作段階における故障解析の重要性
製造業において、製品の試作段階は非常に重要な過程です。
最終製品が期待通りの性能を発揮するためには、この段階での故障解析が欠かせません。
不具合の早期発見や原因追及を行い、設計や製造プロセスにフィードバックを与えることで、量産時の不具合を未然に防ぐことができます。
試作段階での故障解析は、製品の品質向上だけでなく、コスト削減や開発期間の短縮にも寄与します。
初期段階での改良が可能となるため、量産フェーズでの大規模なリコールや修正を避けることができ、顧客満足度を高める要因となります。
故障解析技術の基本とそのアプローチ
故障解析は、物理的な視点とデータ的な視点の両方からアプローチすることが求められる複雑なプロセスです。
以下に、基本的な解析技術とその手法を紹介します。
物理的解析
物理的な解析では、肉眼や顕微鏡を使用して、製品に発生した故障箇所を直接観察します。
目視検査や断面解析は、製品の形状や素材の欠陥を識別するために重要です。
さらに、高度な技術として、X線解析や電子顕微鏡を使用して内部構造を詳細に観察することもあります。
データ解析
データ解析では、生産過程や試験結果などの定量的データを分析して故障の原因を特定します。
統計的手法を用いることで、故障のパターンや発生頻度を把握し、潜在的な問題を浮き彫りにすることが可能です。
多変量解析や機械学習を活用することで、より精度の高い予測モデルを構築することができます。
シミュレーション解析
コンピュータシミュレーションを用いることで、製品の動作を仮想的に再現し、潜在的な故障箇所を予測します。
特に、CAE(Computer Aided Engineering)を活用したシミュレーションでは、構造解析や流体解析、熱解析などが行われ、複数のパラメータを一度に検証できる利点があります。
故障解析における人材とチームの役割
故障解析を成功させるためには、適切な人材の確保とチーム形成が不可欠です。
以下のような役割を持った専門家がチームに揃うことで、解析の精度と効率は向上します。
機械設計エンジニア
製品の設計理解とモジュールの構造的特性に精通しているため、物理的な故障箇所の特定に役立ちます。
また、設計変更の必要性についても具体的なフィードバックを提供できます。
材料技術者
材料技術者は、製品に使用されている素材の特性や挙動を分析する専門家です。
素材の欠陥や特性に起因する故障を識別し、改善策を提案します。
品質管理エキスパート
品質管理エキスパートは、生産ラインでの不具合検出や品質基準の維持に責任を持ちます。
データ解析を行い、製造過程での不適切な要素を特定することで、故障を未然に防ぎます。
データサイエンティスト
データサイエンティストは、解析対象のデータを統計的手法や機械学習を用いて解析します。
大量のデータから本質的な問題を抽出し、故障原因を数学的に裏付けることが求められます。
成功事例から学ぶ改善ポイント
これまでに数多くの試作段階での故障解析が成功を収めており、これらの事例から得られる知見は大変貴重です。
以下に、一部の成功事例を紹介し、そこから得られた改善ポイントを考察します。
ケーススタディ1: 新素材の採用による故障回避
ある電子機器メーカーでは、新素材を採用することで製品の寿命が著しく改善されました。
試作段階での繰り返しテストと材料分析により、従来の素材に存在した微小な亀裂や内部応力が製品の早期故障の原因となっていることを特定しました。
結果として、より適した新素材を採用し、製品寿命を大幅に延ばすことができました。
ケーススタディ2: 生産プロセスの最適化による故障率低減
精密機械メーカーにおいては、生産ラインのプロセスを見直し、40%の故障率低減を達成しました。
具体的には、検査工程の強化とリアルタイムデータの導入により、異常を即座に検出し対策を講じることが可能となりました。
結果的に、出荷後のトラブルが激減し、顧客の信頼を獲得しています。
ケーススタディ3: シミュレーションによる潜在故障の予防
自動車メーカーは、CAEシミュレーションを活用して複雑な構造の耐久性を事前に評価しました。
試作段階での耐久試験とシミュレーション結果を突き合わせることで、量産前に潜在故障を予測し、設計の改善に繋げました。
これにより、製品リリース後のリコールを未然に防ぐことができました。
昭和からの業界動向とデジタルトランスフォーメーションの現状
製造業界は、昭和の頃から続く技術や手法に依存している部分が多く、特にアナログな手法が根強く残っています。
しかし、近年ではデジタルトランスフォーメーション(DX)の流れが加速し、これまでの手法を刷新しつつあります。
例えば、IOT(Internet of Things)やAI(人工知能)の導入により、リアルタイムでのデータ取得や解析が可能になりました。
これにより、従来の故障解析方法に比べて、はるかに迅速かつ正確な原因特定が可能になっています。
また、クラウド技術の進化によって、複数の拠点やシステム間でデータを共有し、解析結果を即座に反映することで、効率的な改善策の導入が促進されています。
これらの進化は、業界全体における大きな革新をもたらし、より迅速で効率的な製品開発が可能となっています。
まとめ: 試作段階における故障解析の未来
試作段階での故障解析は、製造業にとって不可欠な工程であり、今後もその重要性は増していくでしょう。
技術の進化とともに解析手法も進化を遂げていますが、基礎的な物理的解析とデータ解析の融合は変わることなく重要です。
新たな技術の導入や組織の人材育成を通じて、より高精度な故障解析が実現できるよう努めることが、製造業の未来を切り開く鍵となるでしょう。
これからも、日々の改善と新たな取り組みを通じて、より高品質な製品づくりを目指していくことが求められます。
資料ダウンロード
QCD管理受発注クラウド「newji」は、受発注部門で必要なQCD管理全てを備えた、現場特化型兼クラウド型の今世紀最高の受発注管理システムとなります。
ユーザー登録
受発注業務の効率化だけでなく、システムを導入することで、コスト削減や製品・資材のステータス可視化のほか、属人化していた受発注情報の共有化による内部不正防止や統制にも役立ちます。
NEWJI DX
製造業に特化したデジタルトランスフォーメーション(DX)の実現を目指す請負開発型のコンサルティングサービスです。AI、iPaaS、および先端の技術を駆使して、製造プロセスの効率化、業務効率化、チームワーク強化、コスト削減、品質向上を実現します。このサービスは、製造業の課題を深く理解し、それに対する最適なデジタルソリューションを提供することで、企業が持続的な成長とイノベーションを達成できるようサポートします。
製造業ニュース解説
製造業、主に購買・調達部門にお勤めの方々に向けた情報を配信しております。
新任の方やベテランの方、管理職を対象とした幅広いコンテンツをご用意しております。
お問い合わせ
コストダウンが利益に直結する術だと理解していても、なかなか前に進めることができない状況。そんな時は、newjiのコストダウン自動化機能で大きく利益貢献しよう!
(β版非公開)