- お役立ち記事
- FMEA、DRBFMによる不具合発生防止
月間76,176名の
製造業ご担当者様が閲覧しています*
*2025年3月31日現在のGoogle Analyticsのデータより
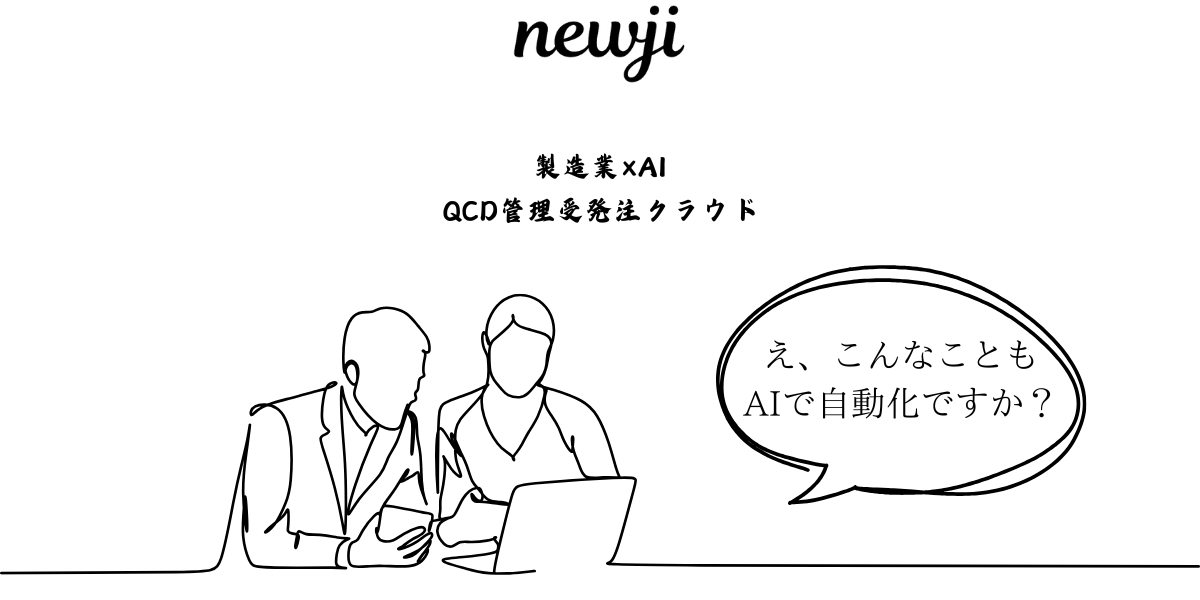
FMEA、DRBFMによる不具合発生防止
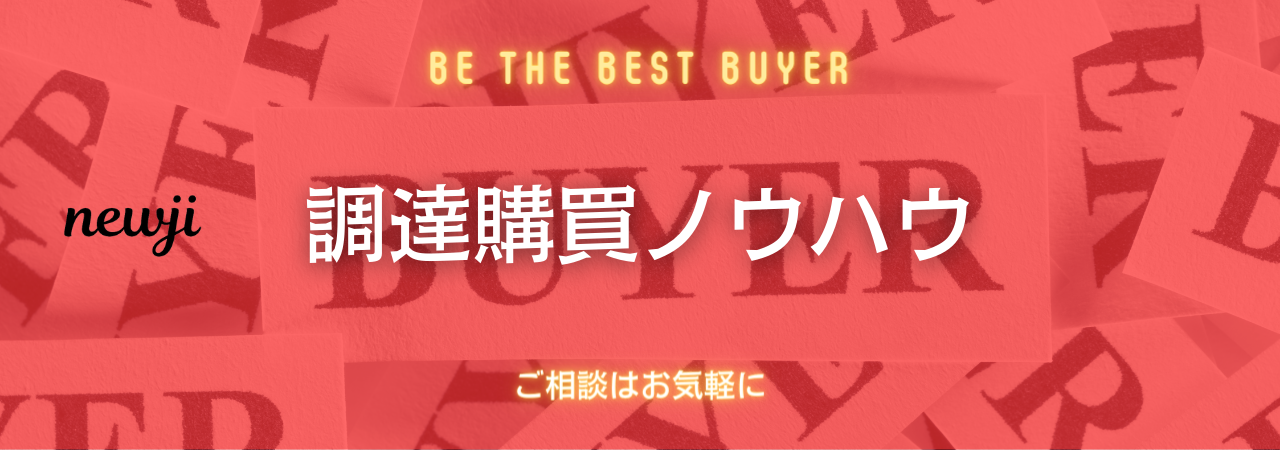
目次
はじめに
製造業における品質管理は、年々その重要性を増しています。
顧客のニーズが多様化する中、製品の不具合を事前に防止することは企業の競争力強化の鍵です。
そこで注目されるのがFMEA(故障モード影響解析)やDRBFM(設計レビューによる故障モードの防止)の手法です。
本記事では、これら手法がどのように不具合を未然に防ぎ、製品品質の向上を支えるのかを解説します。
さらに製造業の現場でそれぞれの手法を実践する際のポイントについて詳しく述べていきます。
FMEAとは何か
FMEAの基本概念
FMEAは、「Failure Mode and Effects Analysis」の略であり、日本語では「故障モード影響解析」と訳されます。
この手法は製品やプロセスの潜在的な故障モードを特定し、その影響を評価し、リスクを軽減するための対策を講じることを目的としています。
FMEAは航空宇宙、医療機器、自動車産業など、安全性が極めて重視される分野で特に活用されている手法です。
FMEAの実施プロセス
1. **故障モードの特定**:製品またはプロセスの各部位や工程について、どのような不具合が発生し得るかを網羅的に洗い出します。
2. **影響の評価**:特定した故障モードが製品に及ぼす影響を評価します。
その影響の重大性、発生確率、検出の難易度を定量的に分析します。
3. **リスク優先度数(RPN)の計算**:重大性、発生確率、検出の難易度を掛け合わせた数値で、どこに最もリスクが集中しているかを明確にします。
4. **優先順位の設定**:RPNの値に基づき、対応すべき優先順位を設定します。
5. **具体的対策の検討と実施**:リスクを低減するための具体的な対策を検討し、実施に移します。
DRBFMとは何か
DRBFMの基本概念
DRBFMは、「Design Review Based on Failure Mode」の略です。
日本語では「設計レビューによる故障モードの防止」と呼ばれます。
この手法はトヨタ自動車によって開発され、設計変更や新規設計時に特に注意を払うべき手法として広く知られています。
DRBFMはFMEAを補完し、設計の履歴や技術的変更を細かく吟味することで、不具合の発生を防ぎます。
DRBFMの実施プロセス
1. **変更箇所の特定と詳細分析**:設計における変更点、及びその周辺領域を徹底的に洗い出し、それらが製品性能に及ぼす影響を分析します。
2. **仮説立案と議論**:変更箇所に関する様々な仮説を立て、どのような事象が起き得るのかをあらゆる観点から議論します。
3. **懸念事項の抽出と対策検討**:議論から生まれた懸念事項について、その影響を抑えるための具体的な対策を検討します。
4. **対策の実施と評価**:決定した対策を実行し、その効果を評価しフィードバックします。
FMEAとDRBFMの比較と相互補完性
FMEAとDRBFMは、いずれも不具合発生の未然防止を目指す手法ですが、それぞれ異なる特徴があります。
FMEAは包括的に製品やサービスの全ての故障モードを洗い出すアプローチに対し、DRBFMは設計変更や新規設計時に特化したアプローチです。
これらはお互いの弱点を補う形で共存することができます。
FMEAを実施することで、全体のリスクの把握と大まかな対策の方針を立てた後、詳細にDRBFMを行うことで、設計変更時のリスクを更に細かく分析できます。
これにより、通常の品質管理プロセスでは見過ごされがちな「見えざるリスク」にも目を光らせ、より堅牢な製品開発を実現します。
製造現場でのFMEAとDRBFMの活用方法
現場でのFMEA活用のポイント
製造現場でFMEAを効果的に活用するためには、次のようなポイントに注力することが重要です。
– **クロスファンクショナルチームの編成**:部署間で異なる視点が集まることで、より多くのリスク要因を洗い出すことができます。
– **データの蓄積と活用**:過去のデータを基に故障モードを特定しやすくなるため、データの蓄積と分析は欠かせません。
– **継続的な見直し**:製品ライフサイクルのいかなる時点でもリスクは変化し得るため、定期的な見直しを行い、FMEAの内容を最新の状態に保つ必要があります。
現場でのDRBFM活用のポイント
DRBFMを現場で有効に活用するためのポイントは以下の通りです。
– **設計変更を重視**:設計変更時には必ずDRBFMを実施し、潜在的なリスクを未然に防ぐプロセスを習慣化します。
– **自由な討論の場を確保**:様々な視点を持つ人々を巻き込み、自由な意見交換の機会を作ることで、見えにくいリスクを抽出しやすくします。
– **予防措置の徹底**:DRBFMで特定されたリスクに対する対策は、効果が確認されるまで継続的にフォローアップを行うことが重要です。
現場の課題と成功事例
製造業の現場でFMEAやDRBFMを取り入れることには、多くの利益がある反面、様々な課題も存在します。
その一つに、チームメンバーの意識改革が挙げられます。
特にアナログの手法に慣れている現場では、新しい手法を取り入れることに抵抗が生じることもあるため、教育と啓発活動が必要です。
ある自動車部品メーカーでは、FMEAのプロセスを導入する際に、初めてプロジェクトチームに参加するスタッフへの教育を強化し、各メンバーが自分の役割を明確に理解できるようにサポートしました。
その結果、設計段階での不具合発見率が飛躍的に向上し、生産段階でのトラブルも減少しました。
まとめ
FMEAやDRBFMは、製造業における不具合発生の未然防止において極めて有効な手法です。
FMEAは潜在的な故障モードを広範囲に渡って洗い出し、全体の品質管理を強化するのに役立ちます。
一方で、DRBFMは設計変更や新規設計時に焦点を当て、詳細なリスク分析を行うための手段として有効です。
これらの手法を適切に組み合わせ、現場での実践に落とし込み、継続的にフィードバックを行うことで、企業は高い品質の製品を市場に出し、競争力を維持し続けることが可能となります。
製造業に携わるすべての人々が、この手法を正しく理解し、実践することが、業界全体の発展に寄与することになるでしょう。
資料ダウンロード
QCD管理受発注クラウド「newji」は、受発注部門で必要なQCD管理全てを備えた、現場特化型兼クラウド型の今世紀最高の受発注管理システムとなります。
ユーザー登録
受発注業務の効率化だけでなく、システムを導入することで、コスト削減や製品・資材のステータス可視化のほか、属人化していた受発注情報の共有化による内部不正防止や統制にも役立ちます。
NEWJI DX
製造業に特化したデジタルトランスフォーメーション(DX)の実現を目指す請負開発型のコンサルティングサービスです。AI、iPaaS、および先端の技術を駆使して、製造プロセスの効率化、業務効率化、チームワーク強化、コスト削減、品質向上を実現します。このサービスは、製造業の課題を深く理解し、それに対する最適なデジタルソリューションを提供することで、企業が持続的な成長とイノベーションを達成できるようサポートします。
製造業ニュース解説
製造業、主に購買・調達部門にお勤めの方々に向けた情報を配信しております。
新任の方やベテランの方、管理職を対象とした幅広いコンテンツをご用意しております。
お問い合わせ
コストダウンが利益に直結する術だと理解していても、なかなか前に進めることができない状況。そんな時は、newjiのコストダウン自動化機能で大きく利益貢献しよう!
(β版非公開)