- お役立ち記事
- フォールトツリー分析(FTA)と原因結果分析(FMEA)の違い
月間76,176名の
製造業ご担当者様が閲覧しています*
*2025年3月31日現在のGoogle Analyticsのデータより
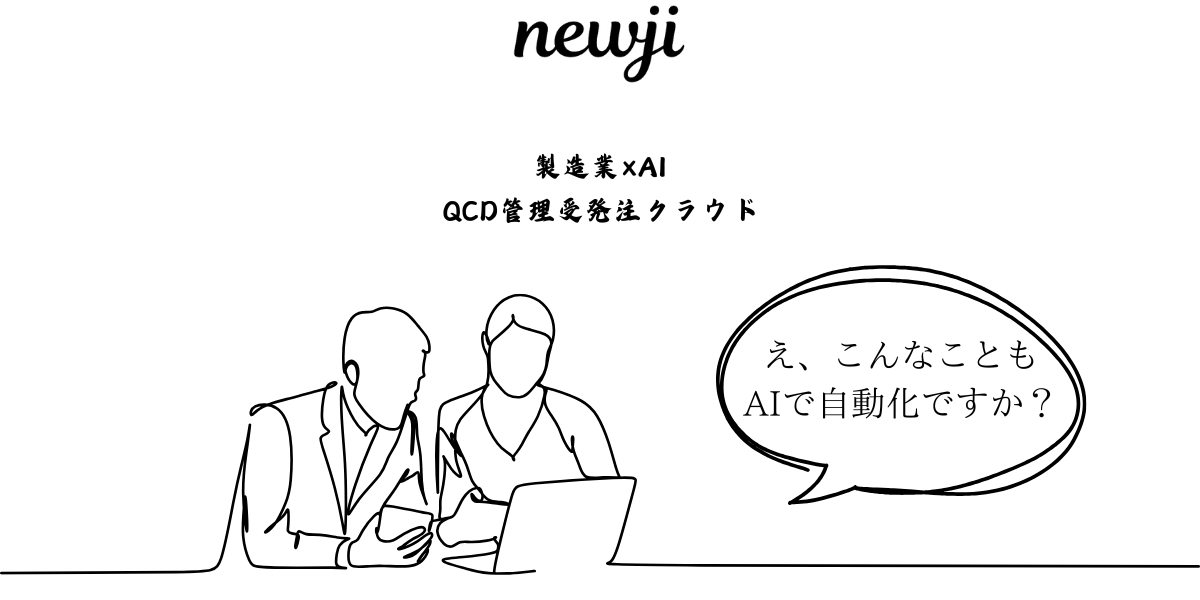
フォールトツリー分析(FTA)と原因結果分析(FMEA)の違い
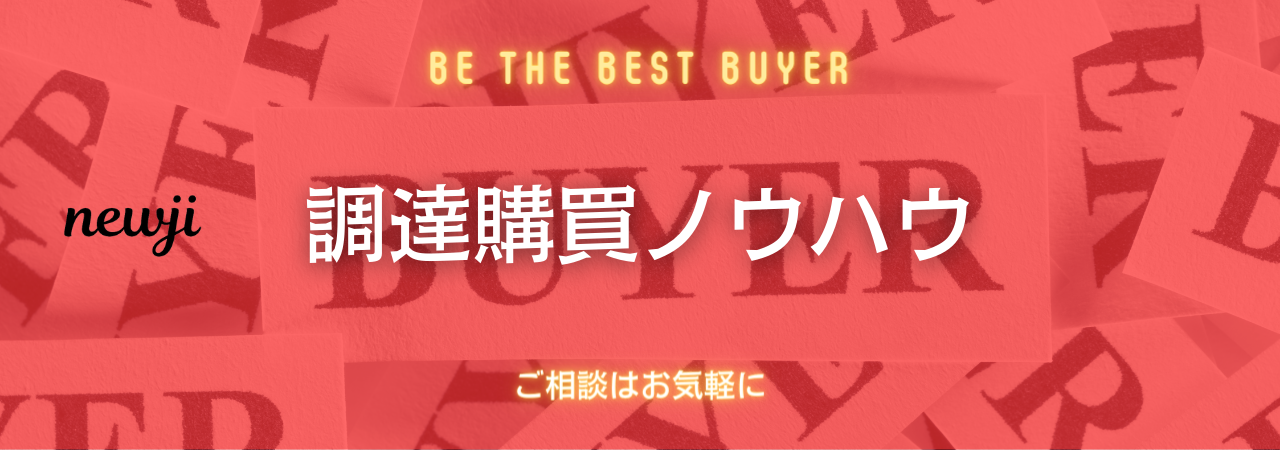
目次
フォールトツリー分析(FTA)と原因結果分析(FMEA)とは?
製造業における品質管理やリスク管理の一環として、フォールトツリー分析(FTA)と原因結果分析(FMEA)は非常に重要なツールです。
これらの手法は、製品やプロセスにおける潜在的な欠陥や故障の原因を特定し、その影響を予測するために使用されます。
では、それぞれの手法とは具体的にどのようなもので、どのような違いがあるのでしょうか?
フォールトツリー分析(FTA)とは?
フォールトツリー分析(FTA)は、システムやプロセスの障害の原因を図式的に表した手法です。
FTAは、トップダウン方式で問題の根本原因を特定することを目的としています。
FTAの基本的な流れ
1.システムやプロセスのトップレベルの障害(トップイベント)を特定します。
2.トップイベントを引き起こす可能性のある直接の原因(直接イベント)を特定します。
3.直接イベントに至るまでの中間イベントを識別します。
4.これらのイベントを論理ゲート(ANDゲート、ORゲートなど)で結び、全体のフォールトツリーを作成します。
5.フォールトツリーを利用して、原因とその確率を算出し、対応策を検討します。
FTAの特徴
FTAの最大の特徴は、トップダウン方式であることです。
トップレベルの障害からスタートし、その原因を順次遡って特定していきます。
これにより、「なぜ」という視点で問題を深堀りし、根本的な要因を突き止めることができます。
原因結果分析(FMEA)とは?
原因結果分析(FMEA:Failure Mode and Effects Analysis)は、システム、プロセス、設計などの潜在的な故障モードを事前に特定し、その影響とリスクを評価する手法です。
FMEAは、ボトムアップ方式で問題の予防に重きを置きます。
FMEAの基本的な流れ
1.分析対象のシステムやプロセスを細分化します。
2.各部分について、潜在的な故障モード(Failure Mode)を明確にします。
3.故障モードが発生した場合の影響(Effect)を特定します。
4.故障モードの発生原因(Cause)を記録します。
5.それぞれの原因について、発生頻度(Occurrence)、検出可能性(Detection)、重大度(Severity)を評価します。
6.リスク優先数(RPN:Risk Priority Number)を計算し、対策を検討します。
FMEAの特徴
FMEAの特徴は、ボトムアップ方式であることです。
個々の要素から始めて、それが全体に与える影響を考慮することで、潜在的な故障を事前に防止することができます。
FTAとFMEAの違い
FTAとFMEAはともにリスク管理の重要なツールですが、そのアプローチと目的にはいくつかの重要な違いがあります。
アプローチの違い
FTAはトップダウン方式で、トップレベルの障害から始まり、その原因を逐次特定していく手法です。
これに対して、FMEAはボトムアップ方式で、システムやプロセスの個々の部分からスタートし、潜在的な故障モードを事前に特定し、その影響を評価します。
目的の違い
FTAの主な目的は、既に発生した障害の根本原因を特定し、再発防止策を検討することです。
一方、FMEAの目的は、潜在的な故障を事前に発見し、そのリスクを評価し、予防策を講じることです。
使用する場面の違い
FTAは、トラブルシューティングや問題解決の際に特に効果的です。
具体的には、製品が市場に出た後の故障分析や、生産ラインでのトラブル発生時などに活用されます。
一方、FMEAは、新製品の設計段階や新しい生産ラインの計画段階で使用されます。
事前に潜在的な問題を洗い出し、品質や信頼性を向上させるための手法として優れています。
FTAとFMEAの併用
製造業の品質管理やリスク管理をより効果的に行うためには、FTAとFMEAの併用が推奨されます。
これにより、既存の問題の解決策を見つけるだけでなく、将来的な問題の発生を未然に防ぐことができます。
FTAの実施後にFMEAを行う
まずFTAを実施し、既存の問題の根本原因を特定します。
その後、FMEAを行い、新たなリスクや潜在的な故障モードを事前に排除することで、全体的な品質と信頼性を向上させることができます。
FMEAの実施後にFTAを行う
逆に、FMEAを先に実施して潜在的な故障モードとその影響を評価し、それに基づいてシステムやプロセスを最適化します。
その後、実際に問題が発生した場合には、FTAを実施して根本原因を特定し、再発防止策を講じることが可能です。
まとめ
FTAとFMEAは、それぞれ異なるアプローチと目的を持つリスク管理の手法です。
FTAはトップダウン方式で既存の障害を特定し、FMEAはボトムアップ方式で潜在的な故障モードを事前に評価します。
どちらも製造業における品質管理やリスク管理において非常に重要な役割を果たします。
これらの手法を併用することで、既存の問題を解決し、将来的な問題の発生を未然に防ぐことが可能になります。
以上の点を踏まえ、製造業現場での品質管理やリスク管理をさらに改善し、持続可能な発展に貢献していきましょう。
資料ダウンロード
QCD管理受発注クラウド「newji」は、受発注部門で必要なQCD管理全てを備えた、現場特化型兼クラウド型の今世紀最高の受発注管理システムとなります。
ユーザー登録
受発注業務の効率化だけでなく、システムを導入することで、コスト削減や製品・資材のステータス可視化のほか、属人化していた受発注情報の共有化による内部不正防止や統制にも役立ちます。
NEWJI DX
製造業に特化したデジタルトランスフォーメーション(DX)の実現を目指す請負開発型のコンサルティングサービスです。AI、iPaaS、および先端の技術を駆使して、製造プロセスの効率化、業務効率化、チームワーク強化、コスト削減、品質向上を実現します。このサービスは、製造業の課題を深く理解し、それに対する最適なデジタルソリューションを提供することで、企業が持続的な成長とイノベーションを達成できるようサポートします。
製造業ニュース解説
製造業、主に購買・調達部門にお勤めの方々に向けた情報を配信しております。
新任の方やベテランの方、管理職を対象とした幅広いコンテンツをご用意しております。
お問い合わせ
コストダウンが利益に直結する術だと理解していても、なかなか前に進めることができない状況。そんな時は、newjiのコストダウン自動化機能で大きく利益貢献しよう!
(β版非公開)