- お役立ち記事
- 試作から量産までの流れ
月間76,176名の
製造業ご担当者様が閲覧しています*
*2025年3月31日現在のGoogle Analyticsのデータより
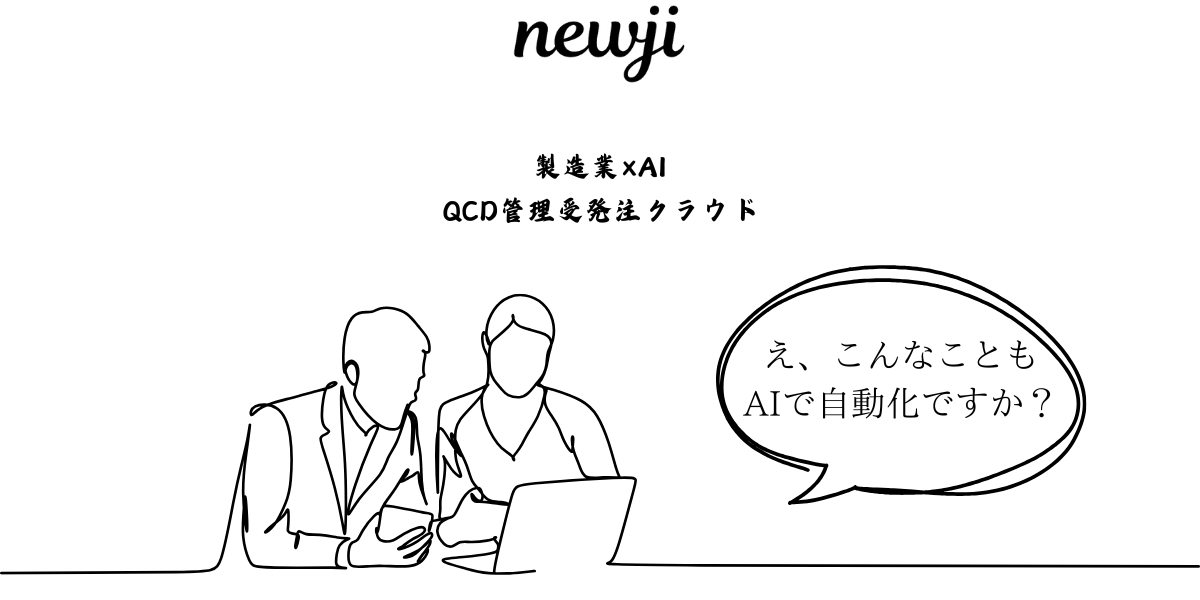
試作から量産までの流れ
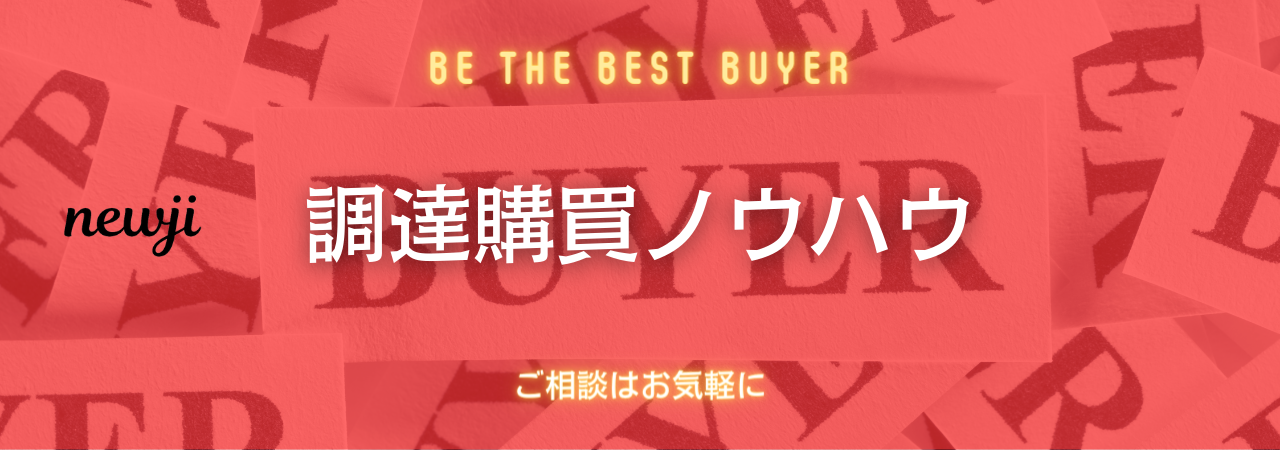
目次
はじめに
製造業における新製品の開発は、試作から量産までの一連のプロセスを経て行われます。
この流れを理解することは生産管理や品質管理の観点から非常に重要です。
新製品開発の成功には、各ステップの詳細な知識と専門的なスキルが求められます。
この記事では、試作から量産までの流れを具体的に解説し、製造業の現場で役立つ実践的な情報と最新の技術動向を紹介します。
試作フェーズ
試作の目標と重要性
試作フェーズでは、新製品の基本的なデザインや機能を現実の形として具現化します。
この段階は、製品の実現可能性を評価するための重要なプロセスです。
試作品を製造することで、設計上の不具合や改良点を見つけることができます。
試作の種類
試作には主に以下の2つの種類があります。
- 概念実証試作:基本的な機能やデザインの確認を目的としたもの。
- 量産前試作:量産で使用する素材や製造方法を確認するためのもの。
最新技術の導入
試作フェーズにおいては、3Dプリンティングなどの最新技術が大いに役立ちます。
これにより、迅速かつ低コストで試作品を作成することができ、設計の確認や修正が容易になります。
設計フェーズ
詳細設計とシミュレーション
試作フェーズで得たフィードバックを基に、詳細な設計を行います。
この段階では、CADソフトウェアを利用して精密な設計図を作成し、製品の各部品や素材の選定を行います。
シミュレーション技術を用いて、製品がどのように機能するかを事前に予測することも重要です。
設計レビュー
詳細設計が完了したら、設計レビューを行います。
ここでは、多くの専門家が集まり、設計の妥当性や製造可能性を評価します。
このステップでの確認作業は、後のステップでのトラブルを未然に防ぐために欠かせません。
試作評価フェーズ
評価基準の設定
試作評価フェーズでは、製品が設計通りに動作するかを確認します。
評価基準には以下の項目が含まれます。
- 機能性
- 耐久性
- 安全性
- コスト
テストとフィードバック
実際に試作品を使用して各種テストを行い、評価基準に基づくデータを収集します。
テストの結果を基に、必要な改良を行います。
フィードバックを迅速に反映することで、製品の完成度を高めることができます。
リスク管理
リスクアセスメント
試作評価が終わった段階で、リスクアセスメントを行います。
これには、製造プロセスにおける潜在的なリスクを特定し、それに対する対策を検討する作業が含まれます。
フェールセーフ設計
リスクアセスメントを基に、フェールセーフ設計を導入します。
これは、製品や製造プロセスにおいて問題が発生した際の被害を最小限に抑えるための設計手法です。
量産準備フェーズ
設備と人員の配置
量産を開始する前に、必要な設備および人員の配置を確認します。
量産に適した設備が整っていることを確認し、担当する人員が適切なトレーニングを受けているかを確認します。
量産試作(PPAP)
量産に先立ち、量産試作(PPAP: Production Part Approval Process)を行います。
これは、実際の量産と同じ条件下で試作品を製造し、品質や性能を最終確認するプロセスです。
量産フェーズ
初期生産
量産フェーズに入ると、まず初期生産を行います。
これは小規模なロットで製品を製造し、最終的な品質確認と製造プロセスの微調整を行うためのものです。
フルスケール生産
初期生産で問題がないことを確認したら、いよいよフルスケールの生産を開始します。
この段階では、生産速度や効率を最大化するための最適化が行われます。
品質管理と連続改善
品質管理の重要性
量産フェーズにおいても、品質管理は非常に重要です。
製品の一定の品質を維持するためには、各製造ステップにおける品質チェックを欠かさず行う必要があります。
連続改善(KAIZEN)
製品の品質向上や製造コストの削減を目指して、連続改善(KAIZEN)活動を促進します。
オペレーターやエンジニアの意見を積極的に取り入れ、現場の問題解決を図ります。
最終検査と出荷
最終検査の実施
フルスケール生産が完了した製品は、最終検査を受ける必要があります。
この段階では、ランダムサンプリングや全数検査を行い、製品が所定の品質基準を満たしているかを確認します。
出荷とフィードバック
最終検査をパスした製品は、出荷準備を行います。
出荷後も顧客からのフィードバックを受け取り、将来的な製品改良に役立てることが求められます。
まとめ
試作から量産までの流れは、多岐にわたるステップと綿密なプロセスが絡み合っています。
各フェーズにおける詳細な計画と実施、最新技術の導入、品質管理の徹底が新製品開発の成功に欠かせません。
この記事で紹介した基本的な流れや最新の技術動向を参考に、皆様の製造現場でのプロジェクトを成功に導いてください。
資料ダウンロード
QCD管理受発注クラウド「newji」は、受発注部門で必要なQCD管理全てを備えた、現場特化型兼クラウド型の今世紀最高の受発注管理システムとなります。
ユーザー登録
受発注業務の効率化だけでなく、システムを導入することで、コスト削減や製品・資材のステータス可視化のほか、属人化していた受発注情報の共有化による内部不正防止や統制にも役立ちます。
NEWJI DX
製造業に特化したデジタルトランスフォーメーション(DX)の実現を目指す請負開発型のコンサルティングサービスです。AI、iPaaS、および先端の技術を駆使して、製造プロセスの効率化、業務効率化、チームワーク強化、コスト削減、品質向上を実現します。このサービスは、製造業の課題を深く理解し、それに対する最適なデジタルソリューションを提供することで、企業が持続的な成長とイノベーションを達成できるようサポートします。
製造業ニュース解説
製造業、主に購買・調達部門にお勤めの方々に向けた情報を配信しております。
新任の方やベテランの方、管理職を対象とした幅広いコンテンツをご用意しております。
お問い合わせ
コストダウンが利益に直結する術だと理解していても、なかなか前に進めることができない状況。そんな時は、newjiのコストダウン自動化機能で大きく利益貢献しよう!
(β版非公開)