- お役立ち記事
- DCS(Distributed Control System)を導入して製造業のプロセス制御を最適化する方法
月間76,176名の
製造業ご担当者様が閲覧しています*
*2025年3月31日現在のGoogle Analyticsのデータより
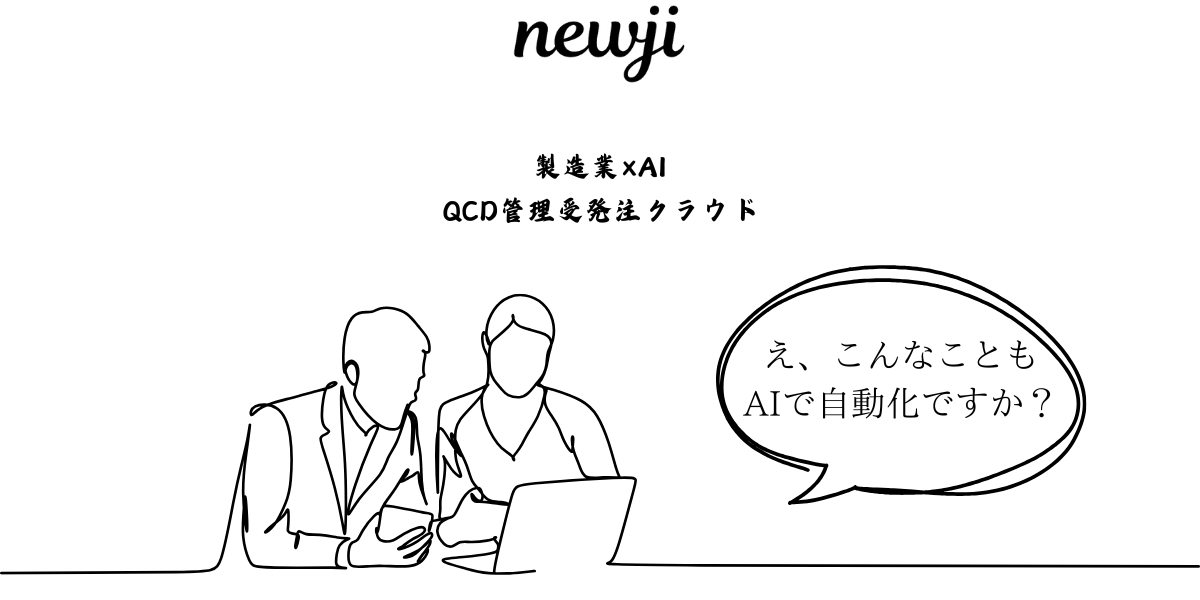
DCS(Distributed Control System)を導入して製造業のプロセス制御を最適化する方法
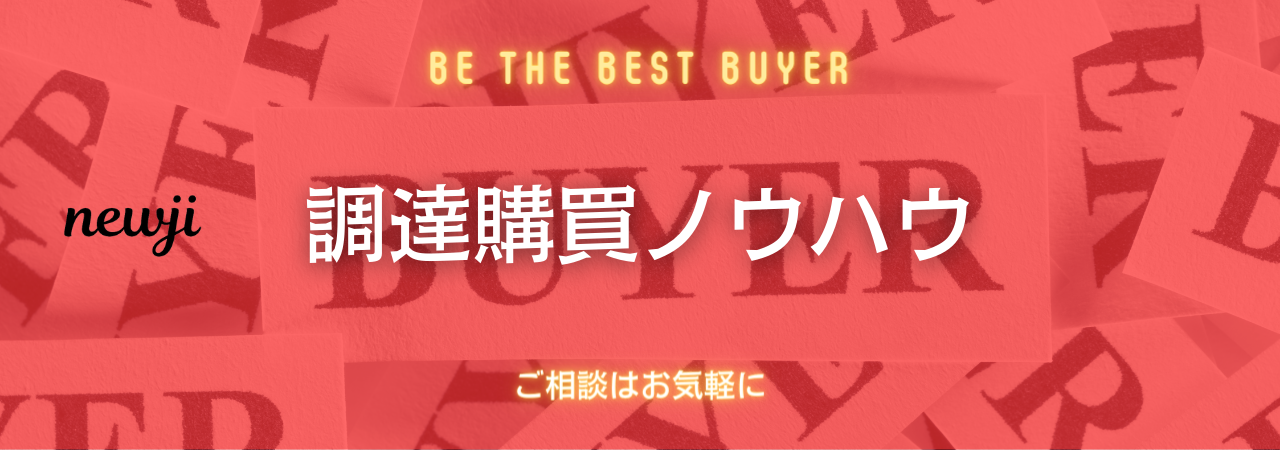
目次
DCS(Distributed Control System)とは何か?
DCS(Distributed Control System)は、分散型制御システムの略で、産業用プロセス制御において中心的な役割を果たします。
これは、複数の制御装置が分散配置され、それぞれが独自の制御機能を持つシステムのことを指します。
一般的には、プロセスプラント、化学工場、製造ラインなど、複雑な制御が必要な環境で利用されます。
DCSは、各制御装置が分散して配置されているため、システム全体の信頼性が向上し、一箇所の故障が全体に及ぼす影響を最小限に抑えることができます。
また、システム全体を統括する中央監視システムが存在し、リアルタイムでのデータ収集と解析が可能です。
DCSの主な機能と利点
リアルタイム制御とモニタリング
DCSの最大の強みは、リアルタイムでプロセスを制御し、モニタリングできる点にあります。
これにより、製造現場の状況を瞬時に把握し、迅速な対応が可能となります。
具体例として、化学反応の進行をリアルタイムで監視し、必要に応じて反応条件を調整することで、最適な生産効率を維持することが挙げられます。
安全性の向上
DCSには、安全性を高めるための機能が多数搭載されています。
例えば、異常が発生した場合に即座にアラートを発する機能や、自動的に安全な状態に移行するセーフティ機能などです。
これにより、人為的なミスや機械の故障に対する対策が強化されます。
柔軟性の向上
DCSは、システム全体の柔軟性を高める設計がされています。
例えば、新しい機器や制御ロジックを追加する際も、システム全体への影響を最小限に抑えながら対応できます。
これにより、生産ラインの変更や追加が容易になり、急速に変化する市場ニーズに迅速に対応することが可能です。
データ解析と予測保全
DCSは、大量のデータを収集し、そのデータを解析することで、予測保全や異常検知にも役立ちます。
機器の稼働状況や過去のデータを基に、メンテナンス時期を予測し、適切なタイミングで保全作業を行うことで、機器のダウンタイムを最小限に抑えることができます。
DCSの導入手順
DCSを導入する際には、以下の手順を踏むことが一般的です。
1. 現状分析と要件定義
まず、現在の製造プロセスの現状を詳細に分析し、DCSに求める要件を定義します。
これには、現行の制御システムの課題点や改善点を洗い出し、新たなシステムに求める機能や性能を明確にすることが含まれます。
2. システム設計
次に、要件定義に基づいてDCSのシステム設計を行います。
システムアーキテクチャの設計、ハードウェアおよびソフトウェアの選定、ネットワークの構成などを検討します。
信頼性や拡張性を考慮し、将来的な変更や追加も考慮した設計を行うことが重要です。
3. システム導入
システム設計が完了したら、実際にDCSを導入します。
設備の搬入、設置、結線、ソフトウェアのインストールなどを行います。
この段階では、現場の運用に影響を与えないよう、適切な計画を立てて作業を進めることが求められます。
4. テストと検証
システム導入が完了したら、次にテストと検証を行います。
実際の運用条件でシステムが正しく動作するか、予期せぬトラブルが発生しないかを確認します。
必要に応じて微調整を行い、最適な動作を実現します。
5. 運用開始とフィードバック
最後に、DCSの運用を開始します。
運用開始後も、継続的にデータを収集し、システムが最適な状態で稼働し続けるようにメンテナンスを行います。
また、現場からのフィードバックを取り入れ、必要に応じてシステムの改善を行うことが重要です。
DCSの最新技術動向
DCSの技術も日々進化しています。
最新の技術動向を把握し、常に最適なシステムを導入することが求められます。
IoTとDCSの融合
IoT(Internet of Things)の進化により、DCSも大きな変革を迎えています。
複数のセンサーやデバイスがインターネットに接続され、リアルタイムでデータを収集・解析することが可能になっています。
これにより、プロセス制御の精度がさらに向上し、予測保全や異常検知も高度化しています。
人工知能(AI)の活用
AI技術の発展により、DCSにおいてもAIを活用した制御が注目されています。
AIは、大量のデータを解析し、最適な制御パラメータを自動的に調整することで、効率的な生産を実現します。
また、異常検知の精度も向上させることができます。
クラウドベースのDCS
クラウド技術の進化に伴い、クラウドベースのDCSも増えています。
クラウドベースのDCSは、初期投資を抑え、柔軟かつスケーラブルなシステムを構築することが可能です。
また、リモートアクセスが容易であり、場所を選ばずにシステムの監視・管理ができます。
DCS導入の成功事例
具体的な事例を通じて、DCS導入の成功ポイントを紹介します。
化学工場での導入事例
ある化学工場では、プロセスの一部を自動化するためにDCSを導入しました。
導入前は人為的なミスや機器の故障が頻発していたため、生産効率が低下していました。
しかし、DCS導入後は、リアルタイムでの監視と自動制御が可能となり、生産効率が30%向上し、故障の発生率も大幅に減少しました。
食品工場での導入事例
ある食品工場では、複雑な製造プロセスを最適化するためにDCSを導入しました。
導入前は手作業による調整が多く、生産のばらつきが問題となっていました。
DCS導入後は、プロセス全体を自動で制御することで、一貫性のある高品質な製品を安定して生産できるようになりました。
まとめ
DCS(Distributed Control System)は、分散型の制御システムであり、製造業のプロセス制御を最適化するための強力なツールです。
リアルタイムでの制御とモニタリング、安全性の向上、柔軟性の向上、データ解析と予測保全など、多くの利点があります。
DCSを導入する際には、現状分析と要件定義、システム設計、システム導入、テストと検証、運用開始とフィードバックという手順を踏むことが重要です。
また、IoTやAI、クラウド技術の進化により、DCSの技術も日々進化しており、最新の技術動向を把握することが求められます。
具体的な導入事例を参考にしながら、自社の製造プロセスに最適なDCSを導入し、生産効率や品質の向上を目指しましょう。
資料ダウンロード
QCD管理受発注クラウド「newji」は、受発注部門で必要なQCD管理全てを備えた、現場特化型兼クラウド型の今世紀最高の受発注管理システムとなります。
ユーザー登録
受発注業務の効率化だけでなく、システムを導入することで、コスト削減や製品・資材のステータス可視化のほか、属人化していた受発注情報の共有化による内部不正防止や統制にも役立ちます。
NEWJI DX
製造業に特化したデジタルトランスフォーメーション(DX)の実現を目指す請負開発型のコンサルティングサービスです。AI、iPaaS、および先端の技術を駆使して、製造プロセスの効率化、業務効率化、チームワーク強化、コスト削減、品質向上を実現します。このサービスは、製造業の課題を深く理解し、それに対する最適なデジタルソリューションを提供することで、企業が持続的な成長とイノベーションを達成できるようサポートします。
製造業ニュース解説
製造業、主に購買・調達部門にお勤めの方々に向けた情報を配信しております。
新任の方やベテランの方、管理職を対象とした幅広いコンテンツをご用意しております。
お問い合わせ
コストダウンが利益に直結する術だと理解していても、なかなか前に進めることができない状況。そんな時は、newjiのコストダウン自動化機能で大きく利益貢献しよう!
(β版非公開)