- お役立ち記事
- トータルプロダクティブメンテナンス(TPM)の実践方法
月間76,176名の
製造業ご担当者様が閲覧しています*
*2025年3月31日現在のGoogle Analyticsのデータより
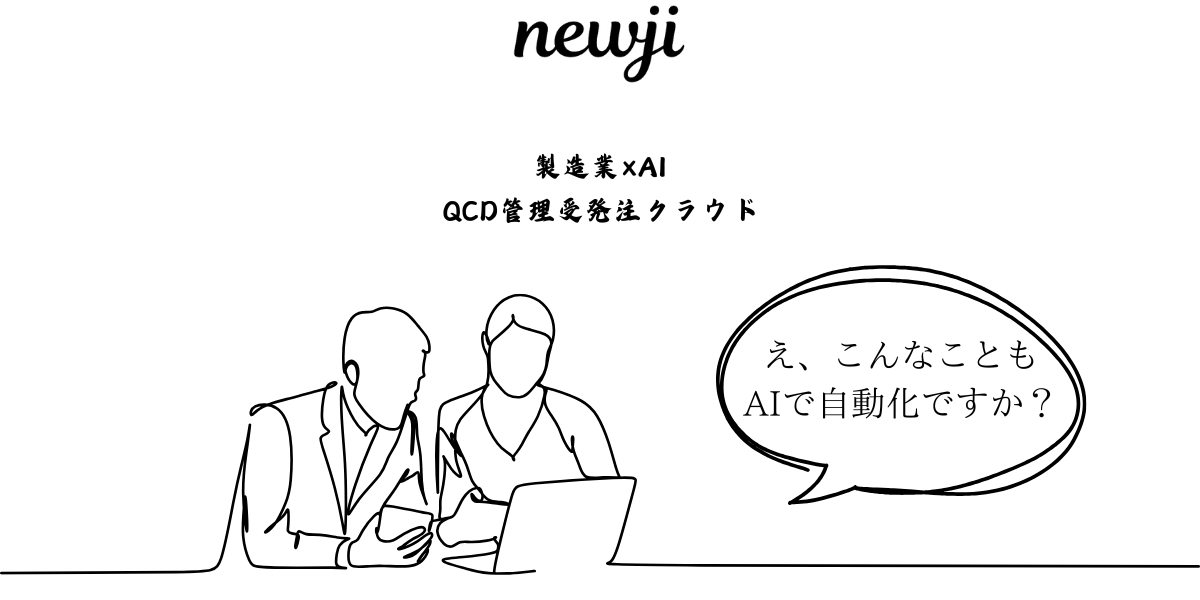
トータルプロダクティブメンテナンス(TPM)の実践方法
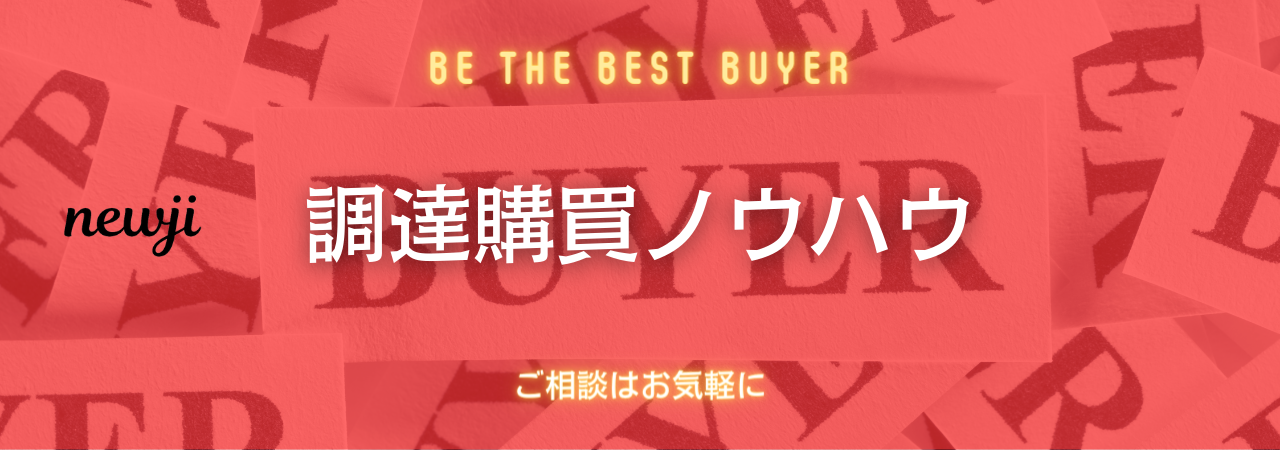
目次
トータルプロダクティブメンテナンス(TPM)とは
トータルプロダクティブメンテナンス(TPM)は、全員参加の生産保全を目指す管理手法です。
このアプローチは、生産性の向上と設備故障の削減を目的として、現場のオペレーターから管理職、さらには経営層までが一丸となって取り組むことが求められます。
TPMの根幹には、「予防保全」「改善保全」「初期管理」「教育訓練」などがあります。
TPMの効果と必要性
TPMを導入することで得られる効果は多岐にわたります。
まず第一に、設備の故障が減少し、結果として生産ラインの稼働率が向上します。
また、設備のメンテナンスが計画的に行われるため、予期せぬトラブルを未然に防ぐことができます。
さらに、従業員のスキル向上や現場の改善が進むことで、全体的な業務効率が上がります。
企業がTPMを導入する必要性としては、競争力の強化が挙げられます。
グローバルな市場で競争が激化している現代、製品の品質や生産コストの面で他社との差異が生じてきます。
TPMを導入し、設備の最適な運用や効率的な生産を実現することで、競争優位を確立することができます。
TPMの基本的な実践ステップ
TPMを効果的に実践するためには、以下のステップを順に踏むことが重要です。
1. 初期整備
まずは初期整備から始めます。
これは設備を最適な状態に保つための最初のステップで、故障の原因となるゴミや油漏れなどを取り除きます。
また、部品の交換や調整も行い、設備の初期性能を回復させます。
2. 予防保全
次に予防保全を実施します。
これは設備が故障する前に定期的なメンテナンスを行い、トラブルを未然に防ぐ手法です。
具体的には、定期点検や消耗部品の交換などがあります。
このステップでは、設備のデータを収集し、予測分析を行うことで、故障リスクを低減させることが重要です。
3. 改善保全
改善保全は、既存の設備をさらに改善していくための取り組みです。
現場での小さな問題や不便さを解消し、生産性を向上させることを目指します。
具体的には、作業手順の見直しや部品の配置変更などが挙げられます。
改善提案を受け入れる文化を育むことが、成功の鍵となります。
4. 初期管理
新しい設備やシステムを導入する際には、初期管理が不可欠です。
このステップでは、新しい設備の運用開始前に、詳細なマニュアルを作成し、適切なトレーニングを実施します。
また、新しい設備が最適に機能するようにするための管理方法を確立します。
5. 教育訓練
TPMを成功させるためには、従業員のスキルアップが重要です。
教育訓練を通じて、設備の操作方法やメンテナンス手順を習得させます。
また、TPMの理念や重要性を理解させることも大切です。
この教育訓練を定期的に行うことで、従業員の意識改革とスキルの向上が図られます。
6. 小集団活動
小集団活動とは、現場の従業員が少人数で集まり、改善活動を行うことです。
これにより、現場に最も近い従業員が、自分たちの手で職場の改善を進めることができます。
小集団活動は、現場の改善意識を高めると同時に、コミュニケーションの活性化も図ることができます。
7. 安全・環境管理
安全と環境の管理もTPMの重要な要素です。
労働災害の防止や環境負荷の低減を目指すことで、持続可能な生産活動を実現します。
具体的な取り組みとしては、安全点検の実施やエネルギー消費の削減などが挙げられます。
最新の技術動向とTPMの連携
最新の技術動向もTPMの実践には欠かせません。
特に、IoT(インターネット・オブ・シングズ)やAI(人工知能)の導入が進んでいます。
IoTの活用
IoT技術を活用することで、設備の状態をリアルタイムで監視・管理することが可能です。
センサーを設置し、設備の稼働状態や温度、振動などのデータを取得します。
これにより、故障の予兆を早期に察知し、計画的な保全活動を実施することができます。
また、データをクラウド上で一元管理することで、リモートでの監視や分析も可能となります。
AIの導入
AIを活用することで、設備データの解析がさらに高度化します。
過去の故障データや運転履歴をAIが分析し、故障の予測や最適なメンテナンス時期の提案を行います。
これにより、人間の判断だけでは見逃しがちな微細なサインを見極め、予防保全の精度を高めることができます。
ロボティクスの利用
ロボティクス技術の導入も効果的です。
メンテナンス作業をロボットに任せることで、人手不足の解消や作業の効率化が図れます。
例えば、点検ロボットや清掃ロボットを導入することで、設備の状態を定期的に確認し、清潔さを保つことが容易になります。
TPM実践の成功事例
最後に、TPMを実践して成功した事例をいくつか紹介します。
ケース1: 自動車メーカーの事例
ある大手自動車メーカーでは、TPMの導入により、生産ラインのダウンタイムが大幅に削減されました。
オペレーターによる自主保全活動が活発化し、小さな異常や異音を早期に発見できるようになりました。
また、小集団活動による改善提案が多く出され、作業効率が向上しました。
ケース2: 食品工場の事例
食品工場でもTPMが大いに効果を発揮しています。
特に、衛生管理の徹底が求められる業界では、設備の清掃や点検が非常に重要です。
TPMの実践により、従業員一人一人が衛生管理に対する意識を持ち、設備の状態を常に監視するようになりました。
その結果、異物混入のリスクが低減し、顧客からの信頼も向上しました。
ケース3: 製薬企業の事例
製薬企業でも、TPMの実践により、生産ラインの安定稼働が実現しました。
この企業では、IoTとAIを駆使して設備データをリアルタイムで監視し、故障予測を実施しています。
そのため、トラブル発生前に適切な対応ができるようになり、生産の中断が減少しました。
また、従業員の教育訓練プログラムが充実し、スキルの向上も図られました。
まとめ
トータルプロダクティブメンテナンス(TPM)は、全員参加型の管理手法として、設備の最適化と生産性向上を目指すものです。
初期整備や予防保全、改善保全などの基本ステップを踏み、教育訓練や小集団活動を通じて現場の改善意識を高めることが重要です。
さらに、IoTやAI、ロボティクスなどの最新技術を活用することで、TPMの効果を最大限に引き出すことができます。
多くの企業がTPMを実践し、成功を収めていることから、その実効性は確かなものです。
製造業の発展と競争力の向上のために、TPMを導入し、持続可能な生産活動を実現しましょう。
資料ダウンロード
QCD管理受発注クラウド「newji」は、受発注部門で必要なQCD管理全てを備えた、現場特化型兼クラウド型の今世紀最高の受発注管理システムとなります。
ユーザー登録
受発注業務の効率化だけでなく、システムを導入することで、コスト削減や製品・資材のステータス可視化のほか、属人化していた受発注情報の共有化による内部不正防止や統制にも役立ちます。
NEWJI DX
製造業に特化したデジタルトランスフォーメーション(DX)の実現を目指す請負開発型のコンサルティングサービスです。AI、iPaaS、および先端の技術を駆使して、製造プロセスの効率化、業務効率化、チームワーク強化、コスト削減、品質向上を実現します。このサービスは、製造業の課題を深く理解し、それに対する最適なデジタルソリューションを提供することで、企業が持続的な成長とイノベーションを達成できるようサポートします。
製造業ニュース解説
製造業、主に購買・調達部門にお勤めの方々に向けた情報を配信しております。
新任の方やベテランの方、管理職を対象とした幅広いコンテンツをご用意しております。
お問い合わせ
コストダウンが利益に直結する術だと理解していても、なかなか前に進めることができない状況。そんな時は、newjiのコストダウン自動化機能で大きく利益貢献しよう!
(β版非公開)