- お役立ち記事
- 実験計画法の活用方法
月間77,185名の
製造業ご担当者様が閲覧しています*
*2025年2月28日現在のGoogle Analyticsのデータより
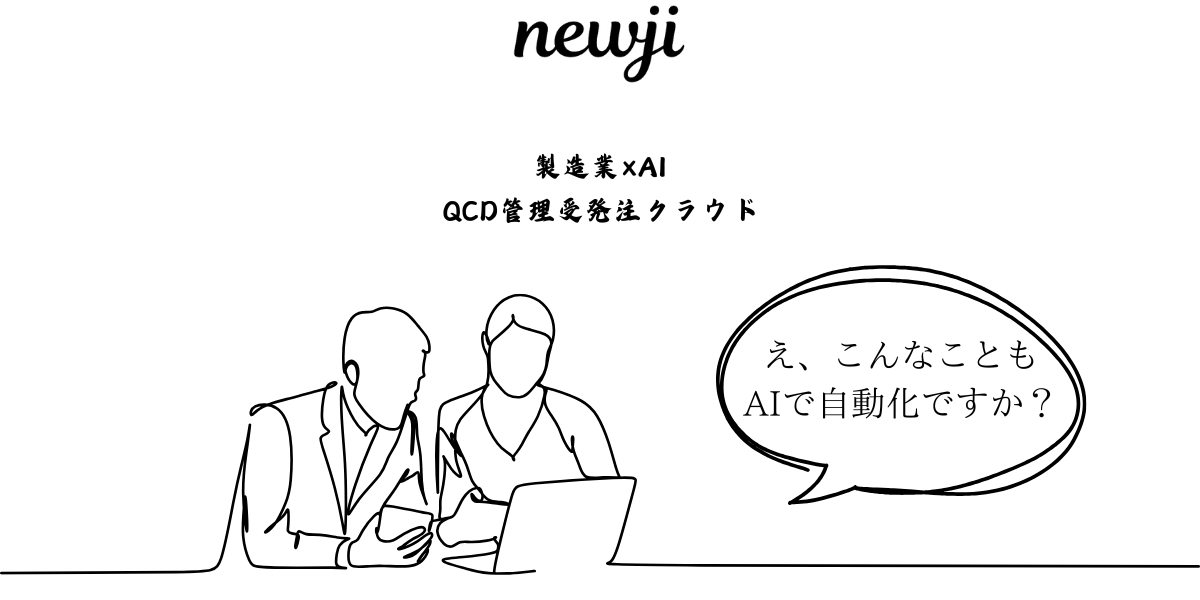
実験計画法の活用方法
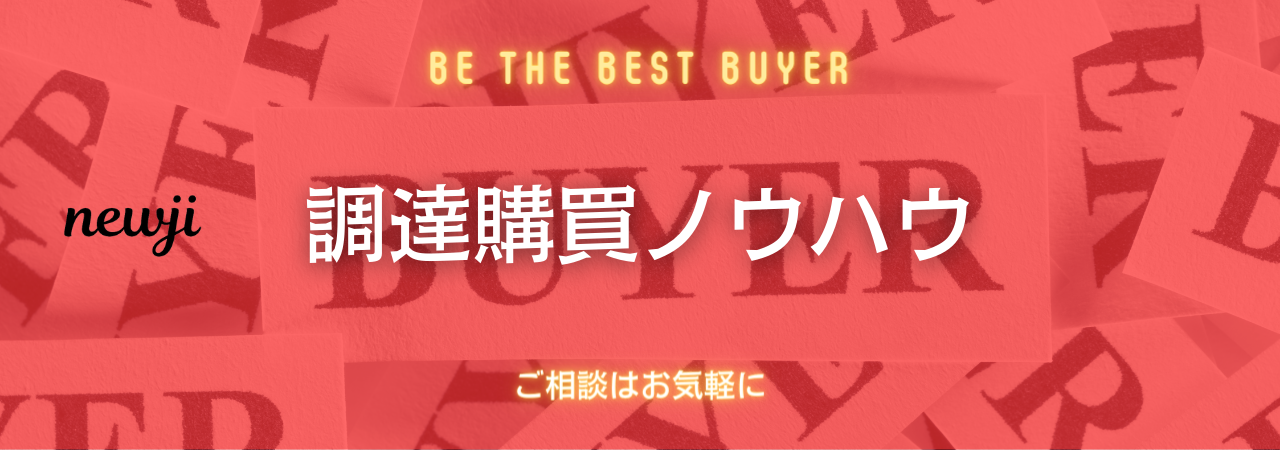
目次
はじめに
実験計画法は、製造業におけるプロセス改善や製品開発において非常に重要な役割を果たす手法です。
多くの製造業者が日常的に直面する品質問題や生産性の課題を解決するための有効な手段として、この方法を適切に活用することが求められています。
本記事では、実験計画法の基本的な概念から、現場での具体的な活用方法までを詳しく解説し、実際の製造プロセスにおけるメリットを考察します。
実験計画法とは
定義と目的
実験計画法(Design of Experiments: DOE)は、実験を効率的に設計し、データを効果的に分析するための手法です。
その目的は、実験の結果を最大限に活用し、少ない試行で有意義な結論を引き出すことにあります。
つまり、品質改善や製品開発のために必要な情報を最小限のコストで得ることができるのです。
製造業における重要性
製造業では、新製品の開発、生産プロセスの最適化、品質管理の強化など、多岐にわたる目的で実験計画法が活用されています。
たとえば、製品の仕様変更による影響を検証するために、複数の因子を組み合わせて結果を予測することができます。
これにより、製造段階でのトラブルを未然に防ぎ、コスト削減や効率向上を実現します。
実験計画法の基本的な概念
因子と水準
実験計画法では、調査対象となる要素を「因子」と呼び、その因子が取りうる値を「水準」と呼びます。
たとえば、色や温度、圧力といった要因があるとすれば、それぞれの因子が複数の水準(例えば、温度50℃、60℃、70℃)を持つことになります。
直交配列と交互作用
直交配列は、実験計画法のなかでよく利用される方法で、少ない実験回数で複数の因子を包括的に調査することを可能にします。
これにより、因子間の交互作用(因子同士の相互の影響)を見抜くだけでなく、それぞれの因子が与える影響を明確にすることができます。
具体的な活用方法
品質改善への応用
実験計画法は、製品の品質改善における強力なツールです。
例えば、製品の欠陥を削減するために、製造工程での温度や圧力、加工時間などの因子を組み合わせて実験を行うことで、最適な製造条件を突き止めることができます。
この手法を使うことで、品質のバラつきを減少させ、顧客満足度の向上を図ることが可能です。
生産工程の最適化
製造プロセスの効率を高めるためには、実験計画法を活用して生産工程そのものを最適化することが重要です。
たとえば、製造ラインにおけるボトルネックの原因を特定し、その改善策を試行する際に実験計画法を使用することで、リソースの無駄を排除し、全体の生産性を向上させることができます。
新製品開発のための検証
新製品開発においては、さまざまな試行錯誤が求められますが、実験計画法を用いることで、効率的かつ効果的に探索を進めることができます。
デザインパラメーターや素材の選定、製造条件の設定など、製品の開発段階から試験を行い、想定と異なる問題が生じた場合の迅速な対策立案が可能です。
昭和から抜け出せないアナログ業界への適用
現状と課題
多くの製造業者が依然として昭和時代の方式を採用している現状がある中、新たな手法への移行には大小様々な障害があります。
その一つに、長年の慣習による心理的・文化的な抵抗があり、従業員のスキル向上に関する教育不足が浮き彫りになります。
効率的な業務遂行のために、実験計画法の導入は業界の革新に寄与します。
デジタルトランスフォーメーションと統合
アナログ業界においても、デジタルトランスフォーメーション(DX)と実験計画法を組み合わせることで、従来の業務効率を飛躍的に高めることができます。
デジタルツールを活用してデータ収集と分析を自動化することで、人間の介入を最小限に抑え、実験の結果をリアルタイムで可視化することが可能になります。
実験計画法を実践するためのステップ
目的と仮説の設定
まずは明確な実験の目的と仮説を設定することが重要です。
改善したいプロセスや新たに開発する製品の具体的な目標を設計し、何を達成すべきかを明確に定義します。
因子と水準の選定
続いて、考慮する因子とその水準を選定します。
この段階で、すべての可能性を網羅するわけではなく、本当に効果のある因子に絞り込むことが重要です。
実験の設計と実施
直交配列を活用して最適な実験設計を行います。
設計が完了したら、次は実際の実験を行い、データを収集していきます。
データ分析と結果の検証
収集したデータを分析し、仮説や目的が達成されたかを検証します。
もし結果が予想と異なる場合は、その原因を解明し、さらなる改善策を講じる必要があります。
結論と今後の展望
実験計画法は、製造業における品質改善や生産効率向上において非常に強力なツールであり、特に現場の課題解決に大きく貢献します。
昭和的なアナログ手法から脱却し、新しい技術と連携してこの手法を導入することは、製造業界全体の競争力を高める一助となります。
今後も不断に進化する技術を取り込みながら、実験計画法を活用して製造プロセスの最適化を図ることが求められています。
資料ダウンロード
QCD管理受発注クラウド「newji」は、受発注部門で必要なQCD管理全てを備えた、現場特化型兼クラウド型の今世紀最高の受発注管理システムとなります。
ユーザー登録
受発注業務の効率化だけでなく、システムを導入することで、コスト削減や製品・資材のステータス可視化のほか、属人化していた受発注情報の共有化による内部不正防止や統制にも役立ちます。
NEWJI DX
製造業に特化したデジタルトランスフォーメーション(DX)の実現を目指す請負開発型のコンサルティングサービスです。AI、iPaaS、および先端の技術を駆使して、製造プロセスの効率化、業務効率化、チームワーク強化、コスト削減、品質向上を実現します。このサービスは、製造業の課題を深く理解し、それに対する最適なデジタルソリューションを提供することで、企業が持続的な成長とイノベーションを達成できるようサポートします。
製造業ニュース解説
製造業、主に購買・調達部門にお勤めの方々に向けた情報を配信しております。
新任の方やベテランの方、管理職を対象とした幅広いコンテンツをご用意しております。
お問い合わせ
コストダウンが利益に直結する術だと理解していても、なかなか前に進めることができない状況。そんな時は、newjiのコストダウン自動化機能で大きく利益貢献しよう!
(β版非公開)