- お役立ち記事
- FMEA・FTAの実施手順のその事例
月間77,185名の
製造業ご担当者様が閲覧しています*
*2025年2月28日現在のGoogle Analyticsのデータより
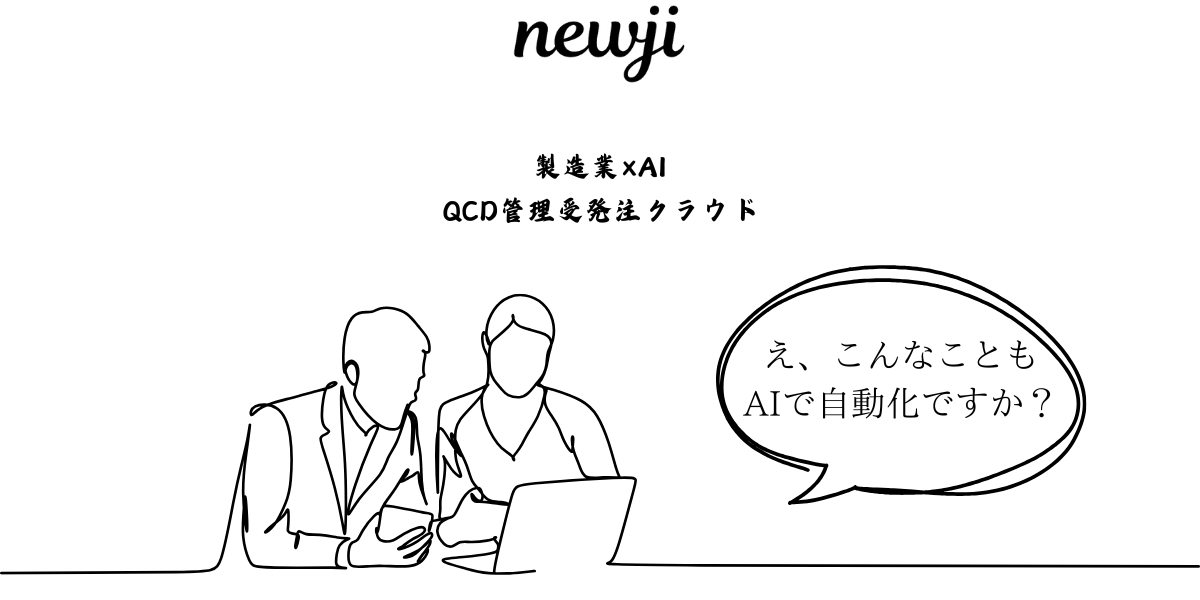
FMEA・FTAの実施手順のその事例
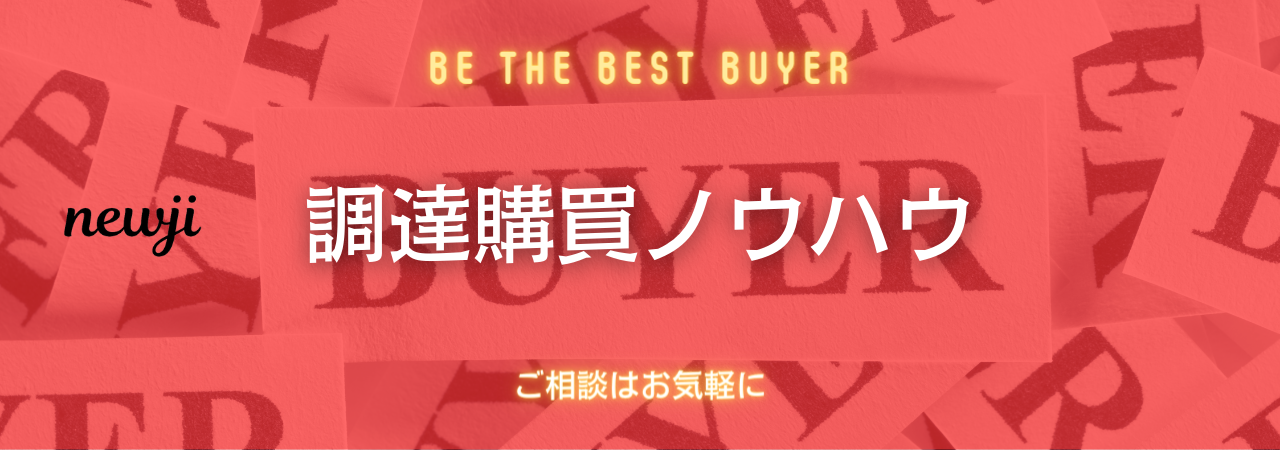
目次
FMEAとFTAの基礎知識
FMEA(Failure Mode and Effects Analysis、故障モード影響解析)とFTA(Fault Tree Analysis、フォルトツリー解析)は、製造業における品質管理やリスクマネジメントで広く用いられる手法です。
いずれも不具合や故障の原因を特定し、製品の信頼性を向上させるための重要なアプローチとして位置付けられています。
FMEAは製品の設計段階から製造プロセスに至るまでの様々な段階で、発生し得る故障モードとその影響を分析し、対応策を講じることでリスクを軽減する手法です。
一方、FTAは特定の故障イベントを起点に、その原因となる基本的な故障をトップダウン式に解析する手法です。
このように、FMEAは発生する可能性のある故障を網羅的に洗い出し、FTAは特定の故障原因を深堀りして分析する相補的な手法として機能します。
FMEAの実施手順と事例
FMEAの実施手順
FMEAを効果的に実施するためには、以下のステップを順次進める必要があります。
1. チームの編成と計画の立案:マルチファンクショナルなチームを編成し、プロジェクトの目標やスコープを明確にします。
2. システムやプロセスの理解:製品やプロセスの構造、動作、使用条件を理解し、解析する範囲を定義します。
3. 故障モードの特定:製品やプロセス内で発生し得る全ての故障モードをリストアップします。
4. 故障モードの影響評価:各故障モードが製品やプロセスに与える影響を識別し、評価します。
5. 根本原因の特定:特定された故障モードの原因を分析し、それがどのようにして発生するのかを明確にします。
6. リスク優先順位の決定:影響度、発生頻度、検出力に基づいてリスクを優先的に評価し、対応策を検討します。
7. 改善策の検討と実施:リスクを低減するための具体的な対策を検討し、実施します。
8. 結果のレビューとフォローアップ:実施した対策の効果を評価し、必要に応じてさらなる改善を行います。
FMEAの事例
例えば、自動車メーカーでのFMEAの事例を考えてみましょう。
新型車のブレーキシステムにおいて、FMEAを行ったとします。
1. 故障モードの特定:ブレーキペダルの反応が鈍い、ブレーキパッドの異常摩耗、ブレーキフルードの漏れなど。
2. 影響評価:ブレーキペダルの反応遅れは制動距離の延長につながり、重大な交通事故のリスクを伴う。
3. 根本原因の特定:例えば、ブレーキホースの品質不良や製造プロセスでの圧力テスト不備など。
4. リスク優先順位の決定:安全に直結する問題として優先順位を高く設定し、即座に改良プロジェクトを立ち上げる。
5. 改善策の検討と実施:高品質のホースメーカーの選定、製造プロセスにおける自動圧力テスト装置の導入など。
このようにして、FMEAを通じて製品の品質と安全性を向上させることができます。
FTAの実施手順と事例
FTAの実施手順
FTAを効果的に実施するためには、以下のステップを順次進める必要があります。
1. トップイベントの特定:解析の対象となる重大な故障イベントを選定します。
2. フォルトツリーの作成:トップイベントに至るまでの原因を階層的に図式化します。
3. 論理ゲートの適用:論理演算(AND/OR)を用いて、各階層のイベントとその因果関係を明示します。
4. 基本イベントの特定:トップイベントに至るもっとも根本的な故障原因を特定します。
5. 定量的解析:故障確率や頻度を算出し、リスクを定量的に評価します。
6. 改善策の検討と実施:フォルトツリー分析から得られた情報を基に、リスク低減策を検討し実施します。
7. 結果のレビューとフォローアップ:改善策の効果を検証し、必要なフィードバックを行います。
FTAの事例
例えば、航空機エンジンの火災事故を想定したFTAを考えてみましょう。
1. トップイベントの特定:エンジン火災の発生。
2. フォルトツリーの作成:燃料漏れ、電気系統のショート、過熱などの諸要因を階層的に示したツリーダイアグラムを作成。
3. 論理ゲートの適用:燃料漏れと電気系統ショートが同時に発生した場合に限り、火災リスクが上昇する(ANDゲート)など。
4. 基本イベントの特定:具体的には、燃料ホースの亀裂や高温部品の接近による配線被覆の劣化など。
5. 定量的解析:各要因の発生確率を集計し、総合的な火災発生確率を評価。
6. 改善策の検討と実施:熱遮断装置の追加設置、燃料ホースの材質変更など具体的な対策を検討し、実行に移す。
このように、FTAによって特定の問題に対する原因を詳細に解析し、しっかりとした対策を講じることが可能になります。
FMEAとFTAの統合的アプローチ
FMEAとFTAの手法は、それぞれ異なる切り口からリスクを分析しますが、統合的に活用することで、製品やプロセスの安全性や信頼性をさらに高めることができます。
まず、FMEAを用いて広範囲にわたるリスクを洗い出し、次にFTAを通じて特定の重大な故障原因を深掘りしてその詳細な理解に努めるという流れが効果的です。
このプロセスにより、製造業における潜在的なリスクを漏れなく発見し、かつ効率的に対策を講じることが可能です。
また、デジタルツールやシミュレーション技術の進化により、FMEAとFTAをより高度かつ迅速に実施できるようになってきています。
このため、担当者はこれらのテクノロジーを活用しながらリスク管理を推進することが求められます。
組織内での一貫したリスク管理体制の構築も重要であり、FMEAとFTAの各手法を体系的に統合することで、企業全体の品質向上に貢献することが期待されます。
まとめ
FMEAとFTAは、製造業における品質向上とリスク管理には欠かせない手法です。
各々の手法はその目的やアプローチが異なるものの、相互に補完することでより包括的な改善策を導くことができます。
現場での活用においては、チームを組織し協力しながら詳細な解析を行うことが成功の鍵となります。
また、デジタル技術の導入によって、これらのプロセスを円滑に進め、かつ深い分析が行えるようになるでしょう。
製造業の現場では、これらの手法を積極的に採用し、製品の信頼性向上と顧客満足度の向上に努めていくことが求められます。
これにより、企業の競争力を高めるだけでなく、社会的信頼を築くことにも寄与するといえます。
資料ダウンロード
QCD管理受発注クラウド「newji」は、受発注部門で必要なQCD管理全てを備えた、現場特化型兼クラウド型の今世紀最高の受発注管理システムとなります。
ユーザー登録
受発注業務の効率化だけでなく、システムを導入することで、コスト削減や製品・資材のステータス可視化のほか、属人化していた受発注情報の共有化による内部不正防止や統制にも役立ちます。
NEWJI DX
製造業に特化したデジタルトランスフォーメーション(DX)の実現を目指す請負開発型のコンサルティングサービスです。AI、iPaaS、および先端の技術を駆使して、製造プロセスの効率化、業務効率化、チームワーク強化、コスト削減、品質向上を実現します。このサービスは、製造業の課題を深く理解し、それに対する最適なデジタルソリューションを提供することで、企業が持続的な成長とイノベーションを達成できるようサポートします。
製造業ニュース解説
製造業、主に購買・調達部門にお勤めの方々に向けた情報を配信しております。
新任の方やベテランの方、管理職を対象とした幅広いコンテンツをご用意しております。
お問い合わせ
コストダウンが利益に直結する術だと理解していても、なかなか前に進めることができない状況。そんな時は、newjiのコストダウン自動化機能で大きく利益貢献しよう!
(β版非公開)