- お役立ち記事
- 使いやすく効果的なホンダのなぜなぜ分析のポイントと展開の仕方
月間76,176名の
製造業ご担当者様が閲覧しています*
*2025年3月31日現在のGoogle Analyticsのデータより
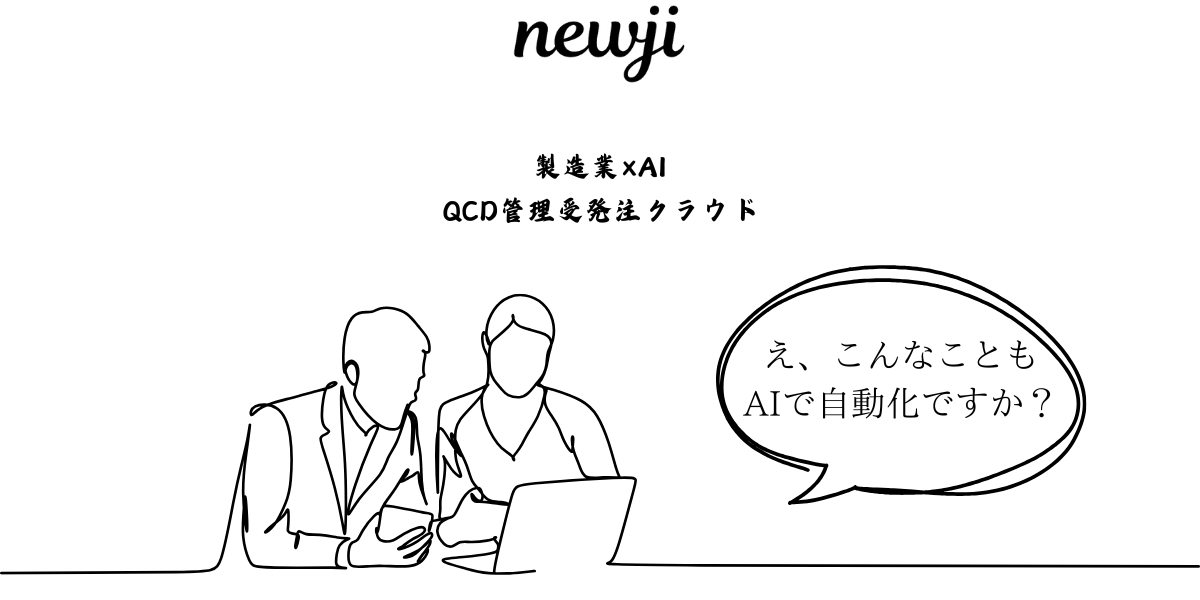
使いやすく効果的なホンダのなぜなぜ分析のポイントと展開の仕方
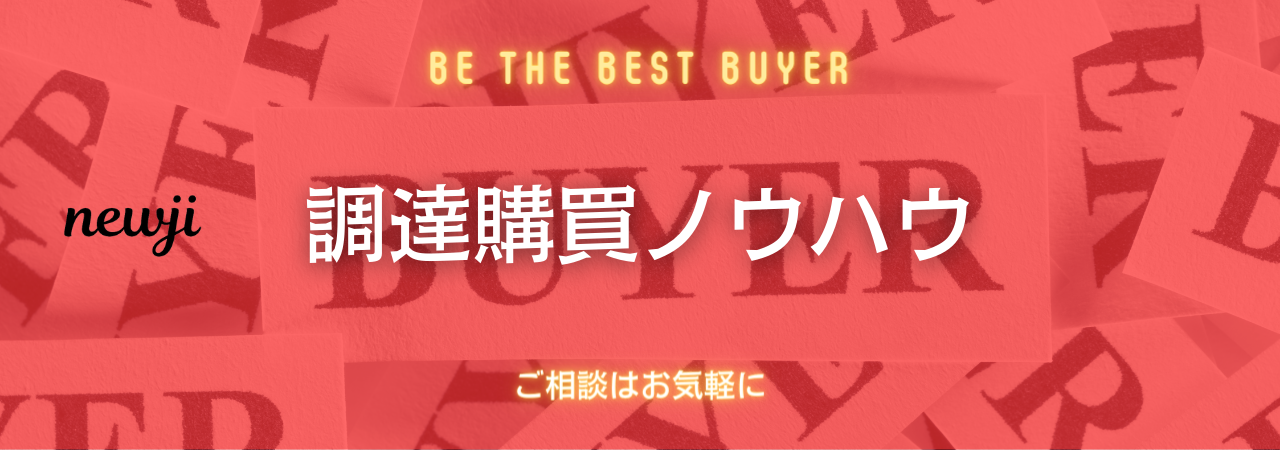
目次
ホンダのなぜなぜ分析とは?
ホンダのなぜなぜ分析は、「なぜ」問題が発生したのかを繰り返し問い続けることで、問題の根本原因を特定し改善策を見出すプロセスです。
この分析方法は1970年代、トヨタ自動車で発展した「5 Whys」としても知られていますが、ホンダでは独自の視点や改善手法を加味して実践されています。
この手法は製造現場での問題解決において、高い効果を発揮しています。
問題が発生した際、その表面上の原因だけで解決しようとするのではなく、なぜその原因が発生したのかを深掘りすることで、再発防止のための最適な対策を講じることができます。
なぜなぜ分析の基本的な進め方
ホンダのなぜなぜ分析を効果的に進めるためには、以下のステップを踏む必要があります。
この手順をしっかり押さえることで、より深い問題解決が可能となります。
1. 問題を特定する
まず最初に行うべきことは、問題の明確化です。
たとえば、不良品の発生という問題があれば、その不良品が具体的にどのような状態で発生したのかを詳細に記録します。
可能であれば、発生した状況を詳細に把握しておくと対応策を考える際のヒントになります。
2. 初回の「なぜ」を問う
次に、その問題が「なぜ」発生したかを問いかけます。
この「なぜ」を具体的に考えることが、後のステップで繰り返す「なぜ」の基礎になります。
例としては、「なぜ不良品が発生したのか?」といったように具体的な問いを立てます。
3. 回答から次の「なぜ」を見つけ出す
初回の「なぜ」に対し回答が出たら、その回答に対して再度「なぜ」を問い続けます。
これにより、問題をどんどん深掘りしていきます。
例えば、「なぜ不良品が発生したのか?」という問いに対して「原因部品の品質が悪いから」という回答が得られた場合、次に「なぜ原因部品の品質が悪いのか?」とさらに問いを進めます。
4. 十分な深さまで掘り下げる
このプロセスを、問題の核までたどり着くまで繰り返します。
通常、「なぜ」を5回繰り返すことが標準とされていますが、問題の複雑さによってはそれ以上必要な場合もあります。
肝心なのは、納得のいく根本原因が見つかるまで問い続けることです。
5. 改善策の立案と実行
根本原因が特定されたら、その原因を解消するための具体的な改善策を立案し実行します。
改善策は、再発防止だけでなく、プロセス全体の効率向上にもつながることが多いです。
ホンダ式なぜなぜ分析の特徴
ホンダのなぜなぜ分析には、その独自の重要な特徴がいくつかあります。
これを理解して活用することで、より効果的な問題解決が可能になります。
従業員全員参加の文化
ホンダでは、なぜなぜ分析は特定の専門家だけが行うものではなく、製造現場で働くすべての従業員が積極的に参加することが求められています。
これにより、現場での多角的な視点と専門知識を生かした分析が可能になり、改善策も実行に移しやすくなります。
柔軟なアプローチ
ホンダのなぜなぜ分析は、その状況や問題の性質に応じて、柔軟にアプローチを変えることが許されています。
これは、すべての問題が同じ原因を持つわけではないという理解に基づいています。
ホンダではこの柔軟性を大事にし、標準的なテンプレートにとらわれず状況に応じた解決方法を優先します。
継続的な改善文化の醸成
ホンダでは、長期的な視点に立ち、継続的な改善を進めることが重視されます。
問題解決の結果をすぐに確認し、必要に応じてさらに深掘りしていくことで、より本質的な改善を達成しようとする姿勢が強調されています。
なぜなぜ分析を効果的に展開するためのポイント
なぜなぜ分析を効果的に展開するには、いくつかのポイントを押さえておく必要があります。
このポイントを意識することで、より良い結果を導き出すことができます。
正確なデータの収集
問題解決の第一歩は、正確なデータの収集です。
現場での問題の状況がどのようであったかを、できる限り詳細に記録することが必要です。
これがないと、いくら「なぜ」を問いかけても仮説に基づいた分析になってしまい、真の原因にはたどり着けません。
コミュニケーションの徹底
複数の従業員が関与する問題解決にはコミュニケーションが不可欠です。
現場の声をしっかりと聞き、チーム一丸となって問題に取り組む姿勢が求められます。
コミュニケーションが取れていれば、意見交換もスムーズになり、問題解決のスピードも大幅に向上します。
仮説と検証のバランス
なぜなぜ分析には、仮説と検証が必須です。
問いかけの中で浮かび上がった仮説を検証するために、時には実験やシミュレーションが必要なこともあります。
仮説が正しいかどうかを徹底的に検証し、それに基づく改善策を立案します。
組織全体の協力
問題の解決には、組織全体の協力が必要です。
特に、上層部の理解とサポートがあるとスムーズにプロセスが進みます。
上層部が問題解決に興味を持ち、積極的に関与することで、改善策の実行と定着が早くなります。
なぜなぜ分析から得られる成果
ホンダのなぜなぜ分析を実践することで、どのような成果が得られるのでしょうか。
その具体的な効果について解説します。
品質向上
問題の根本原因を解決することにより、製品の品質が向上します。
不良品の削減やクレームの減少に貢献し、結果として顧客満足度が向上するでしょう。
生産効率の向上
生産過程での改善点が明らかになり、無駄を排除することで生産効率が高まります。
「なぜ」という問いかけを通じて見えてくる細かなプロセスの改善が、全体として大きな成果をもたらすことが多いです。
従業員のモチベーション向上
ホンダのなぜなぜ分析は、従業員が問題解決に積極的に参加することを促します。
このプロセスが従業員のスキル向上やモチベーションの向上へとつながり、職場全体の活気を生むことになります。
組織の知識の蓄積
分析を通じて得られた知識が組織全体に蓄積されます。
この知識の蓄積が将来の問題解決の際に役立ち、継続的な組織の成長を促進します。
まとめ
ホンダのなぜなぜ分析は、製造業において根本的な問題解決を実現するための強力なツールです。
その効果的な展開には、現場の声を大事にし、従業員全員が参加し、柔軟なアプローチをとることが求められます。
また、徹底的な仮説の検証とデータ収集が重要であり、組織全体での問題解決が文化として根付くことで、品質向上や生産効率の改善、従業員のやる気向上といった具体的な成果が実現されます。
このように、なぜなぜ分析は単なる課題解決手法にとどまらず、組織全体の競争力を高める手段として非常に有効です。
資料ダウンロード
QCD管理受発注クラウド「newji」は、受発注部門で必要なQCD管理全てを備えた、現場特化型兼クラウド型の今世紀最高の受発注管理システムとなります。
ユーザー登録
受発注業務の効率化だけでなく、システムを導入することで、コスト削減や製品・資材のステータス可視化のほか、属人化していた受発注情報の共有化による内部不正防止や統制にも役立ちます。
NEWJI DX
製造業に特化したデジタルトランスフォーメーション(DX)の実現を目指す請負開発型のコンサルティングサービスです。AI、iPaaS、および先端の技術を駆使して、製造プロセスの効率化、業務効率化、チームワーク強化、コスト削減、品質向上を実現します。このサービスは、製造業の課題を深く理解し、それに対する最適なデジタルソリューションを提供することで、企業が持続的な成長とイノベーションを達成できるようサポートします。
製造業ニュース解説
製造業、主に購買・調達部門にお勤めの方々に向けた情報を配信しております。
新任の方やベテランの方、管理職を対象とした幅広いコンテンツをご用意しております。
お問い合わせ
コストダウンが利益に直結する術だと理解していても、なかなか前に進めることができない状況。そんな時は、newjiのコストダウン自動化機能で大きく利益貢献しよう!
(β版非公開)