- お役立ち記事
- 製造業における標準器選定のポイントと調達戦略
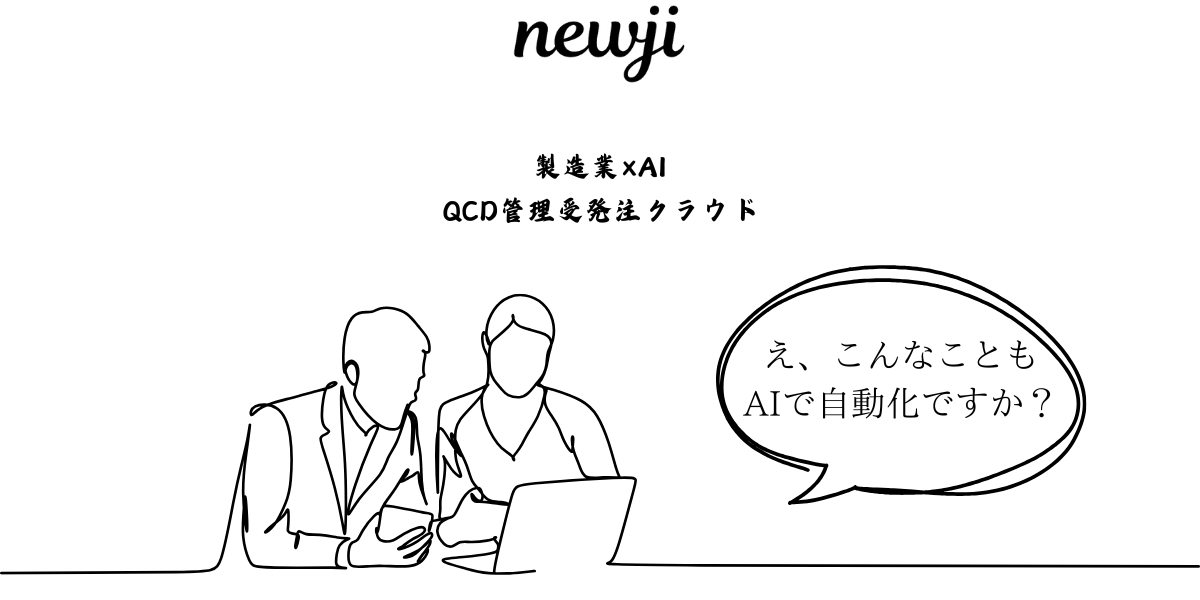
製造業における標準器選定のポイントと調達戦略
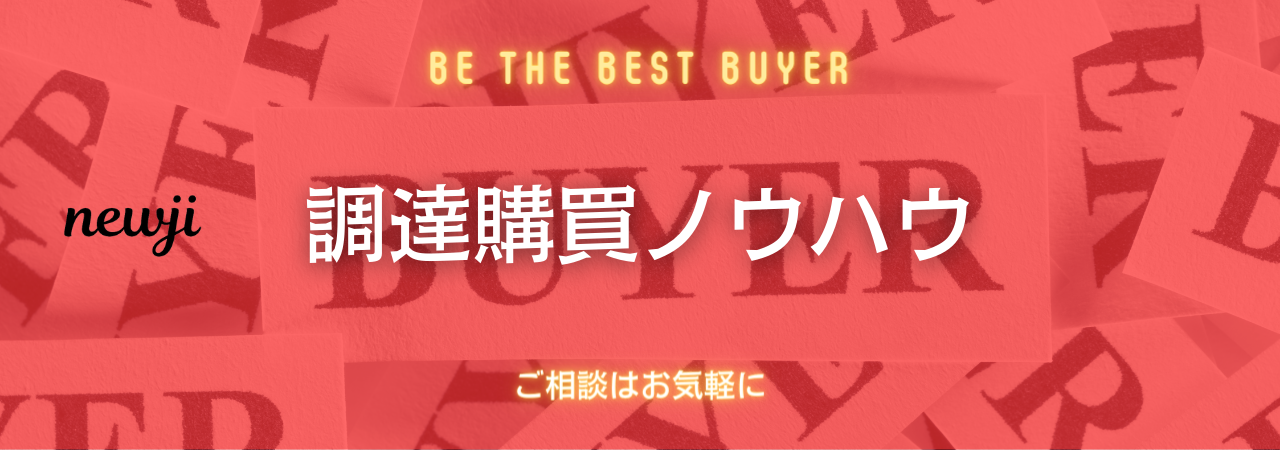
目次
製造業における標準器選定のポイントと調達戦略
製造業において、標準器の選定は製品品質や生産効率を左右する重要な要素です。適切な標準器を選ぶことで、製造プロセスの安定化やコスト削減が実現でき、競争力の向上に繋がります。本記事では、製造業における標準器選定のポイントと、それを支える効果的な調達戦略について詳しく解説します。
標準器選定のポイント
技術的要件の明確化
標準器を選定する際、まず最初に行うべきは技術的要件の明確化です。製品の仕様や製造プロセスに必要な精度、耐久性、操作性などを詳細に把握することが重要です。技術部門と調達部門が連携し、必要な性能基準を確立することで、選定プロセスの基盤が整います。
サプライヤーの選定基準
信頼できるサプライヤーを選定することは、標準器の品質と供給の安定性を確保するために欠かせません。サプライヤー選定時には、以下の基準を考慮します。
– **実績と信頼性**: 長期間にわたり安定した供給実績を持つサプライヤーを選ぶことで、トラブル発生時にも迅速な対応が期待できます。
– **技術力とサポート体制**: 最新技術に対応できるサプライヤーは、将来的な製品開発にも柔軟に対応できます。また、アフターサービスの充実度も重要な評価ポイントです。
– **価格競争力**: 高品質でありながらコストパフォーマンスに優れた製品を提供できるサプライヤーを選ぶことが、全体のコスト削減に寄与します。
コストパフォーマンスの評価
標準器の選定においては、単に価格だけでなく、総合的なコストパフォーマンスを評価することが重要です。初期投資だけでなく、長期的な維持費や運用コストも考慮に入れることで、真のコストメリットを見極めることができます。例えば、メンテナンスが容易な標準器は、長期的にはコスト削減につながる可能性があります。
品質保証と認証の確認
標準器の品質を保証するためには、関連する認証や規格に準拠しているかを確認することが必要です。ISO認証や業界標準に準拠した製品は、一定の品質基準を満たしていることが期待できます。また、サプライヤーが提供する品質保証書やテストレポートなどを確認し、品質管理体制が確立されているかを評価します。
サポート体制とアフターサービス
製造現場では、標準器の故障やトラブルが発生することがあります。その際、迅速かつ適切なサポートを提供できるサプライヤーを選定することが重要です。アフターサービスの充実度やサポート体制の具体的な内容を事前に確認することで、万一の際にも安心して利用することができます。
データに基づく分析
市場データの活用方法
標準器選定において、最新の市場データを活用することは非常に有効です。市場動向や価格変動、技術革新の状況を把握することで、最適なタイミングでの調達や適切な製品選定が可能になります。例えば、特定の標準器の需要が増加している場合、早期にサプライヤーを確保することで価格上昇を回避することができます。
過去の調達実績の分析
過去の調達実績を分析することで、調達プロセスの改善点や成功要因を明らかにすることができます。例えば、過去に問題が発生したサプライヤーとの取引履歴を見直し、品質や納期に関するデータを基に再評価を行うことができます。また、成功した調達事例を分析し、優れたサプライヤーの特徴や効果的な交渉方法を抽出することで、今後の調達活動に活かすことができます。
リスク評価と管理方法
調達におけるリスク評価は、予期せぬトラブルを未然に防ぐために不可欠です。標準器の供給リスク、品質リスク、価格変動リスクなどを評価し、それぞれに対する適切な管理方法を策定します。例えば、複数のサプライヤーからの調達を検討することで、特定のサプライヤーに依存するリスクを低減することができます。また、契約時にリスク分担の条項を盛り込むことも有効です。
調達戦略の構築
長期的な調達計画の策定
効果的な調達戦略を構築するためには、長期的な調達計画が必要です。これにより、需要予測に基づいた適切な在庫管理やサプライヤーとの継続的な関係構築が可能になります。例えば、年間の需要量を予測し、それに基づいてサプライヤーと定期的な注文スケジュールを設定することで、供給の安定性を確保することができます。
サプライヤーとのパートナーシップ構築
単なる取引関係にとどまらず、サプライヤーとパートナーシップを構築することで、双方にとってメリットのある関係を築くことができます。共同開発や技術協力、情報共有などを通じて、サプライヤーとの信頼関係を強化し、製品開発や市場対応力を向上させることが可能です。長期的な視点での協力関係は、競争力の維持・向上に寄与します。
グローバル調達の活用
グローバルな視点での調達を活用することで、コスト削減や技術革新の促進が期待できます。海外の優れたサプライヤーからの調達は、製品の品質向上や新技術の導入に繋がります。しかし、言語や文化の違い、物流面での課題なども存在するため、リスク管理が重要です。現地代理店の活用や現地スタッフの配置など、適切な対応策を講じることが求められます。
サステナビリティを考慮した調達戦略
近年、環境問題への関心が高まる中、サステナビリティを考慮した調達戦略が重要となっています。環境負荷の低い材料や製品の選定、エネルギー効率の高い標準器の導入などを推進することで、企業の社会的責任を果たすと同時に、ブランドイメージの向上にも繋がります。また、サプライチェーン全体での環境管理を強化することで、持続可能な製造プロセスの実現が可能となります。
サプライヤーとの折衝術
効果的なコミュニケーションの方法
サプライヤーとの円滑なコミュニケーションは、効果的な折衝の基盤となります。定期的なミーティングや進捗報告の共有を通じて、双方のニーズや課題を把握し、迅速に対応することが重要です。また、オープンで透明性の高いコミュニケーションを心がけることで、信頼関係の構築が促進されます。
交渉戦略とテクニック
交渉においては、双方にとってウィンウィンの結果を目指すことが重要です。以下の戦略とテクニックを活用することで、効果的な交渉を実現できます。
– **準備と情報収集**: 事前に相手のニーズや市場動向を調査し、交渉の基盤を固めます。
– **BATNAの設定**: 代替案(Best Alternative to a Negotiated Agreement)を明確にすることで、交渉の際の立場を強化します。
– **柔軟性の確保**: 固定観念にとらわれず、互いに譲歩できるポイントを見つけることが成功の鍵です。
契約管理とフォローアップ
交渉後の契約管理も重要です。契約内容が適切に履行されているかを定期的にチェックし、問題が発生した際には迅速に対応する体制を整えます。また、フォローアップを通じて、サプライヤーとの関係を継続的に強化することが求められます。これにより、長期的な協力関係の維持が可能になります。
成功事例の紹介
具体的な企業の事例
ここでは、実際に効果的な標準器選定と調達戦略を導入し、成功を収めた企業の事例を紹介します。
**A社の取り組み**
A社は、自動車部品の製造において、標準器の選定プロセスを見直しました。技術部門と調達部門が共同で技術的要件を再評価し、複数のサプライヤーからの提案を比較検討しました。その結果、コストパフォーマンスに優れたサプライヤーと長期契約を締結し、年間で製造コストを15%削減することに成功しました。
**B社の戦略**
B社は、グローバル市場での競争力強化を目指し、海外の先進的なサプライヤーとのパートナーシップを構築しました。現地の技術を積極的に取り入れ、製品の品質向上に繋げるとともに、調達コストの削減を実現しました。また、サステナビリティを重視した調達戦略を導入し、環境負荷の低減にも成功しています。
調達戦略の導入による成果
標準器選定と調達戦略の見直しにより、多くの企業が以下のような成果を達成しています。
– **コスト削減**: 効果的なサプライヤー選定と交渉により、調達コストの大幅な削減が可能となります。
– **品質向上**: 高品質な標準器の導入により、製品の品質向上と不良品の減少が実現できます。
– **生産効率の向上**: 適切な標準器の選定により、製造プロセスの安定化と生産効率の向上が図れます。
– **リスク管理の強化**: 多角的な調達戦略の導入により、供給リスクの低減や市場変動への対応力が向上します。
ベストプラクティスの共有
成功事例から抽出したベストプラクティスを共有することで、他の企業も同様の成果を達成することが可能です。以下は、特に有効とされるベストプラクティスです。
– **クロスファンクショナルチームの活用**: 技術部門と調達部門が連携することで、より的確な標準器選定が可能となります。
– **データドリブンな意思決定**: 市場データや過去の実績データを基に意思決定を行うことで、客観的かつ効果的な調達が実現します。
– **継続的な改善プロセスの導入**: 調達プロセスを定期的に見直し、改善を続けることで、常に最適な調達戦略を維持することができます。
まとめ
製造業における標準器の選定と調達戦略は、企業の競争力を左右する重要な要素です。技術的要件の明確化、信頼できるサプライヤーの選定、コストパフォーマンスの評価、品質保証の確認など、各段階で慎重な判断が求められます。また、データに基づく分析やリスク管理、長期的な調達計画の策定、サプライヤーとのパートナーシップ構築など、包括的な調達戦略の構築が成功の鍵となります。
さらに、サプライヤーとの効果的なコミュニケーションや交渉術の活用、契約管理とフォローアップの徹底により、安定した調達体制を維持することが可能です。成功事例に学ぶベストプラクティスを導入し、持続可能な調達戦略を実現することで、製造業の発展に貢献することができます。
今後の製造業においては、技術革新や市場変動に柔軟に対応できる調達体制が求められます。標準器選定のポイントを押さえた上で、効果的な調達戦略を構築し、企業の競争力を一層高めていくことが重要です。
資料ダウンロード
QCD調達購買管理クラウド「newji」は、調達購買部門で必要なQCD管理全てを備えた、現場特化型兼クラウド型の今世紀最高の購買管理システムとなります。
ユーザー登録
調達購買業務の効率化だけでなく、システムを導入することで、コスト削減や製品・資材のステータス可視化のほか、属人化していた購買情報の共有化による内部不正防止や統制にも役立ちます。
NEWJI DX
製造業に特化したデジタルトランスフォーメーション(DX)の実現を目指す請負開発型のコンサルティングサービスです。AI、iPaaS、および先端の技術を駆使して、製造プロセスの効率化、業務効率化、チームワーク強化、コスト削減、品質向上を実現します。このサービスは、製造業の課題を深く理解し、それに対する最適なデジタルソリューションを提供することで、企業が持続的な成長とイノベーションを達成できるようサポートします。
オンライン講座
製造業、主に購買・調達部門にお勤めの方々に向けた情報を配信しております。
新任の方やベテランの方、管理職を対象とした幅広いコンテンツをご用意しております。
お問い合わせ
コストダウンが利益に直結する術だと理解していても、なかなか前に進めることができない状況。そんな時は、newjiのコストダウン自動化機能で大きく利益貢献しよう!
(Β版非公開)