- お役立ち記事
- 「製造業のベストプラクティス:コストダウンの実践ノウハウ大全」
月間76,176名の
製造業ご担当者様が閲覧しています*
*2025年3月31日現在のGoogle Analyticsのデータより
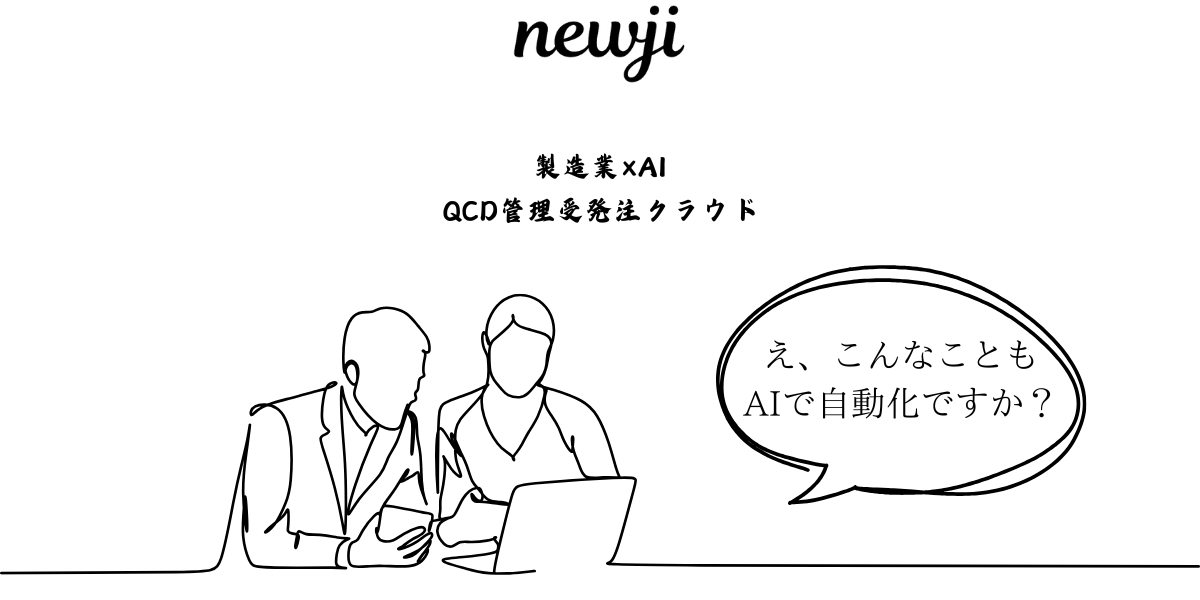
「製造業のベストプラクティス:コストダウンの実践ノウハウ大全」
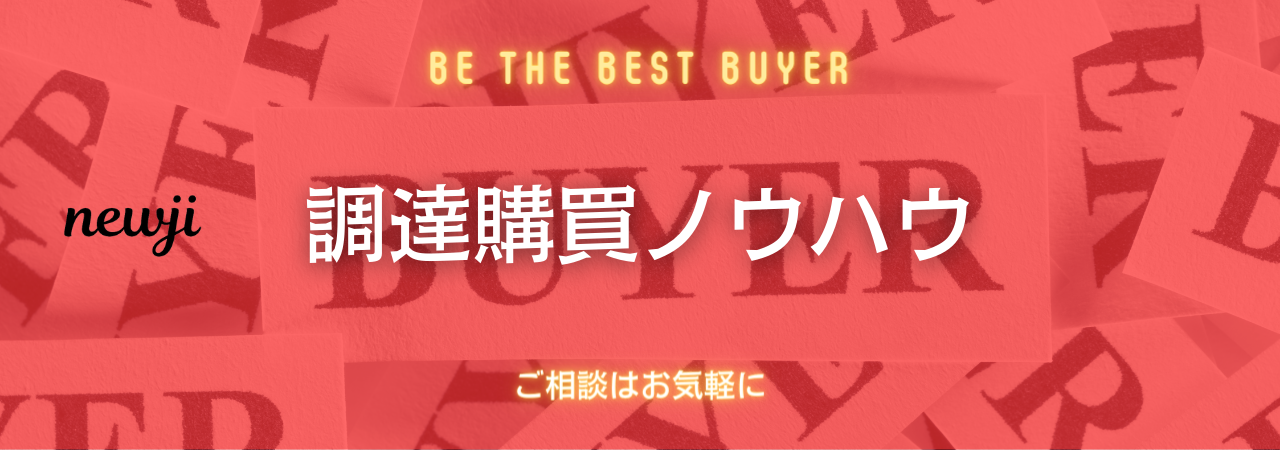
目次
はじめに:コストダウンの重要性
コストダウンは、製造業において企業競争力を高めるために欠かせない戦略の一つです。
特に、調達購買部門におけるコストダウンは、直接的に原価削減につながり、利益率を効果的に向上させる鍵となります。
本記事では、調達購買現場における実践的なコストダウンノウハウを紹介し、具体的な成功事例や数値データを交えながら、その効果的な手法を解説します。
コストダウンの基本戦略
調達購買におけるコストダウンを成功させるには、いくつかの基本的な戦略があります。
以下に、代表的な戦略を紹介します。
1. サプライヤーの適正評価と選定
サプライヤーの選定は、コストダウンの第一歩です。
適正な評価を行うためには、品質、価格、納期、技術力、安定供給能力などの要素を総合的に考慮する必要があります。
以下の評価項目を基にサプライヤーの選定を行いましょう。
– 価格評価:競合他社と比較した価格の優位性
– 品質評価:過去の納品実績および品質管理体制
– 納期評価:納期遵守率およびリードタイムの短さ
– 技術評価:技術開発能力および技術支援体制
– 供給評価:実績ベースでの供給能力および安定性
2. 価格交渉力の強化
価格交渉は、コストダウンを実現するための重要なスキルです。
交渉を成功させるためには、以下のポイントを押さえておくことが重要です。
– 市況データの活用:原材料の相場価格や市場動向を把握し、交渉に活用します。
– コストブレークダウン:製品の構成要素や製造コストを分析し、具体的なコスト削減目標を設定します。
– ロングテール戦略:少量多品種の取引では、サプライヤーにとっても利益が出やすいためメイン商品の価格交渉を優位に進められることがあります。
3. サプライチェーンの最適化
サプライチェーン全体の効率化もコストダウンに直結します。
以下の手法を駆使して、サプライチェーン全体を最適化しましょう。
– ジャストインタイム(JIT):必要な物を必要なときに必要な量だけ調達することで、在庫削減を図ります。
– サプライヤーとのコラボレーション:サプライヤーと情報共有を行い、共通の目標を設定します。
– サプライチェーン全体の可視化:ITツールを活用して、供給網のリアルタイム監視を行い、問題発生時に迅速な対応を行います。
4. 継続的な見直しと改善
コストダウンは、一度の施策で完了するものではありません。
継続的な見直しと改善が必要です。
定期的に以下の点を見直し、改善を繰り返しましょう。
– コストデータの分析:月次や四半期ごとにコストデータを収集し、トレンドを分析します。
– サプライヤー評価の更新:年次でサプライヤーの評価を更新し、パフォーマンスのフィードバックを行います。
– 仕組みの標準化:効果のあったコストダウン施策を標準化し、全業務に展開します。
実践的なコストダウン手法の紹介
ここでは、実際に多くの企業で導入され、効果を上げているコストダウン手法をいくつか紹介します。
1. コスト分析ツールの導入
コスト分析ツールを導入することで、調達コストの細分化と可視化が実現します。
これにより、優先的に削減すべきコスト要因が明確になり、効果的な施策を講じることができます。
実際の導入事例として、ある大手製造業では、コスト分析ツールを導入した結果、年間で10%の調達コスト削減を達成しました。
(出典:株式会社コストマネジメント “調達コスト管理ツール導入事例”)
2. ベンチマーク分析
ベンチマーク分析は、自社のコスト構造と業界他社のコスト構造を比較する手法です。
これにより、自社の強みや弱点が明確になり、具体的な改善ポイントが見えてきます。
例えば、ある電子部品メーカーは、業界トップ企業とのベンチマーク分析を実施し、自社の間接材コストが他社よりも高いことを発見しました。
その結果、間接材の調達プロセスを見直し、経費を削減することに成功しました。
3. ロングテール戦略の活用
ロングテール戦略とは、少量多品種の商品に対しても十分な利益を上げることができるようにする戦略です。
これにより、サプライヤーとの交渉力を高め、主力商品の価格交渉を有利に進めることが可能になります。
例えば、ある化学製品メーカーでは、年間消費量が少ない特殊化学薬品についても積極的に価格交渉を行いました。
その結果、全体のコスト削減に成功し、年間で5%のコストダウンを実現しました。
4. グローバル調達の推進
グローバル調達は、コストダウンを実現するために有効な手法です。
各国の競争力を活用し、最適なサプライヤーを選定することで、大幅なコスト削減が期待できます。
具体的な成功事例として、ある自動車メーカーでは、アジア地域からの調達を増やし、単価を平均15%削減することに成功しました。
(出典:日経BP “グローバル調達で競争力を高める”)
成功事例とそのデータ分析
次に、実際の企業での成功事例を元に、具体的なデータを用いてその効果を検証し、分析します。
事例1:大手電機メーカーのコストダウン戦略
ある大手電機メーカーは、調達コスト削減のためにベンチマーク分析を実施し、データを基に戦略を策定しました。
– 初期データ:年間調達コスト 500億円
– ベンチマークデータ:競合他社の平均調達コスト 450億円
– ステップ1:サプライヤーの再評価と選定
– ステップ2:価格交渉の強化と新技術の導入
これにより、以下の成果を達成しました。
– 調達コスト削減額:年間 10億円(2%削減)
– 納期遵守率:95%から98%に向上
– サプライヤー満足度:80%から85%に向上
事例2:食品メーカーの在庫管理によるコストダウン
ある食品メーカーでは、在庫管理を見直すことで調達コストの削減を目指しました。
– 初期データ:年間在庫費用 80億円
– 現状分析:在庫回転率 4回/年
– ステップ1:ジャストインタイム(JIT)導入
– ステップ2:在庫監視システムの導入
結果として、以下の成果を上げました。
– 在庫費用削減額:年間 20億円(25%減)
– 在庫回転率:4回/年から5回/年に向上
– 生産停止リスク:10%から5%に減少
まとめ:コストダウンの持続的な運用
コストダウンは、一度の取り組みで終わるものではなく、継続的な見直しと改善が求められます。
サプライヤー評価や価格交渉、サプライチェーン最適化の基本戦略を押さえつつ、ベンチマーク分析やグローバル調達などの実践的な手法を導入することで、持続的なコストダウンを実現できます。
また、データ分析を通じて戦略の効果を検証し、成功事例を参考にすることで、より効果的な施策を講じることが可能となります。
製造業におけるコストダウンは、企業の競争力を強化し、利益率を向上させるために欠かせない施策です。
これらのノウハウを活用し、貴社の調達購買活動を一層効率的に行い、持続的な成長を実現しましょう。
資料ダウンロード
QCD管理受発注クラウド「newji」は、受発注部門で必要なQCD管理全てを備えた、現場特化型兼クラウド型の今世紀最高の受発注管理システムとなります。
ユーザー登録
受発注業務の効率化だけでなく、システムを導入することで、コスト削減や製品・資材のステータス可視化のほか、属人化していた受発注情報の共有化による内部不正防止や統制にも役立ちます。
NEWJI DX
製造業に特化したデジタルトランスフォーメーション(DX)の実現を目指す請負開発型のコンサルティングサービスです。AI、iPaaS、および先端の技術を駆使して、製造プロセスの効率化、業務効率化、チームワーク強化、コスト削減、品質向上を実現します。このサービスは、製造業の課題を深く理解し、それに対する最適なデジタルソリューションを提供することで、企業が持続的な成長とイノベーションを達成できるようサポートします。
製造業ニュース解説
製造業、主に購買・調達部門にお勤めの方々に向けた情報を配信しております。
新任の方やベテランの方、管理職を対象とした幅広いコンテンツをご用意しております。
お問い合わせ
コストダウンが利益に直結する術だと理解していても、なかなか前に進めることができない状況。そんな時は、newjiのコストダウン自動化機能で大きく利益貢献しよう!
(β版非公開)