- お役立ち記事
- 工場の効率を最大化するバッテリー残量表示の革新技術導入法
月間76,176名の
製造業ご担当者様が閲覧しています*
*2025年3月31日現在のGoogle Analyticsのデータより
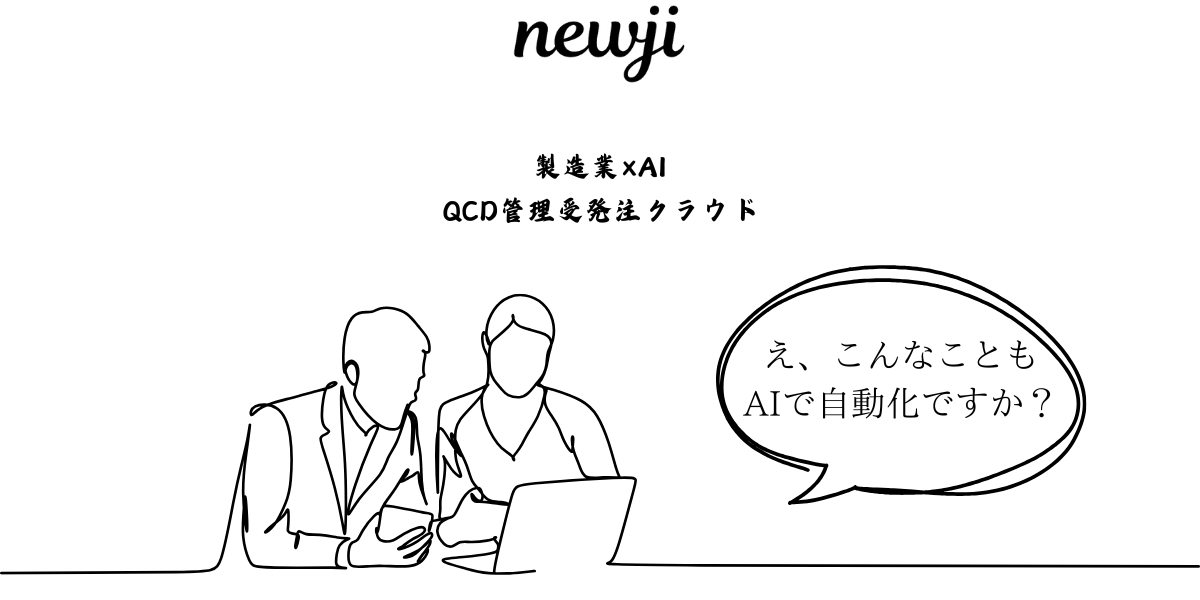
工場の効率を最大化するバッテリー残量表示の革新技術導入法
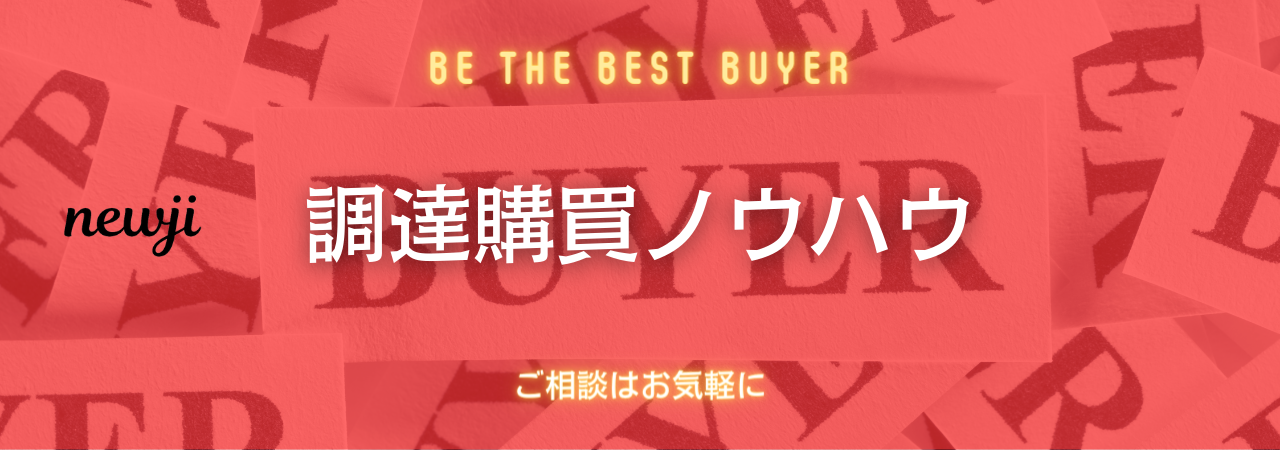
目次
はじめに
工場の効率化は、製造業における競争力維持の鍵となります。その中でも、バッテリー残量表示技術の革新は、生産ラインの稼働率向上やコスト削減に大きく寄与します。本記事では、最新のバッテリー残量表示技術の導入方法と、その効果を最大化するための実践的なアプローチについて解説します。
バッテリー残量表示技術の重要性
バッテリー駆動の機器や設備が増加する現代の工場において、バッテリー残量の正確な表示は欠かせません。適切なバッテリーマネジメントは、機器のダウンタイムを防ぎ、メンテナンスコストの削減につながります。また、リアルタイムでの残量管理は、製造プロセスの最適化にも寄与します。
現場での課題とニーズ
多くの工場では、バッテリー残量の管理が手動や断片的なシステムに依存しているため、情報の遅延や誤差が発生しやすい状況です。これにより、予期せぬ機器停止や生産遅延が発生し、全体の生産効率が低下します。現場の管理職からは、信頼性の高いリアルタイム表示システムへのニーズが高まっています。
最新のバッテリー残量表示技術
近年の技術革新により、バッテリー残量表示システムは大きく進化しています。特に注目すべきは、IoT(モノのインターネット)とAI(人工知能)を活用した高度なシステムです。
IoTによるリアルタイムモニタリング
IoT技術を導入することで、バッテリーの状態をリアルタイムで監視できます。センサーがバッテリーの電圧や温度を常時モニタリングし、データをクラウドに送信する仕組みです。これにより、管理者は常に最新のバッテリーステータスを把握でき、迅速な対応が可能となります。
AIを活用した予測分析
AI技術を活用することで、バッテリーの寿命や性能低下を予測することが可能です。過去のデータを基に、バッテリーの劣化パターンを分析し、メンテナンスのタイミングや交換時期を最適化します。これにより、計画的なメンテナンスが実現し、突発的なトラブルを未然に防ぐことができます。
革新技術の導入方法
バッテリー残量表示の革新技術を導入するには、以下のステップが重要です。
現状分析とニーズの明確化
まず、現行のバッテリーマネジメントシステムを評価し、現状の課題や改善点を明確にします。具体的なニーズを洗い出し、導入する技術の要件を定めます。
適切な技術とサプライヤーの選定
市場には多くのバッテリー管理システムが存在します。機能性、コスト、サポート体制などを比較検討し、自社のニーズに最適な技術と信頼できるサプライヤーを選定します。公開されている市況データや成功事例を参考にすることが有効です。
統合と従業員教育
新しいシステムを既存の生産ラインに統合する際には、シームレスな連携が求められます。導入後は、従業員に対する適切な教育とトレーニングを実施し、システムの効果を最大限に引き出します。
導入による効果とデータ分析
革新技術を導入することで、工場全体の効率が大幅に向上します。
運用効率の向上
リアルタイムでのバッテリー残量管理により、機器のダウンタイムが減少します。具体的な事例では、ある製造業メーカーではダウンタイムを20%削減し、生産性が15%向上しました(出典:製造業協会2023年報告書)。
コスト削減とROI
バッテリーの寿命延長や計画的なメンテナンスにより、運用コストが削減されます。導入費用に対しても、通常1年以内に投資回収が可能であり、長期的なコストメリットが期待できます。
サプライヤーとの交渉術
効果的な交渉は、コスト削減と高品質な技術導入の鍵となります。
強固なサプライヤー関係の構築
信頼関係を築くことで、長期的な協力関係が可能となります。定期的なコミュニケーションやフィードバックを通じて、双方にとって有益な関係を維持します。
市場データを活用した交渉術
公開されている市況データや業界レポートを基に、価格や条件について根拠のある交渉を行います。例えば、バッテリー市場の供給状況や技術トレンドを理解することで、より有利な条件を引き出すことができます(出典:市場調査会社XYZ報告書2023年)。
成功事例の紹介
実際に革新技術を導入し、成功を収めた企業の事例を紹介します。
事例1: 企業Aの導入と成果
企業Aでは、IoTベースのバッテリーマネジメントシステムを導入しました。その結果、バッテリーの故障率が30%減少し、メンテナンスコストが25%削減されました。
事例2: 企業Bの効率化達成
企業BはAIを活用した予測分析システムを導入し、製造ラインの稼働率を向上させました。具体的には、予測精度が80%に達し、突発的なダウンタイムが大幅に減少しました。
まとめ
バッテリー残量表示の革新技術は、工場の効率化に不可欠な要素です。最新のIoTやAI技術を活用し、適切なシステムを導入することで、運用効率の向上やコスト削減が実現できます。成功事例を参考にしながら、効果的な導入方法とサプライヤーとの交渉術を駆使し、自社の製造プロセスを最適化していきましょう。
資料ダウンロード
QCD管理受発注クラウド「newji」は、受発注部門で必要なQCD管理全てを備えた、現場特化型兼クラウド型の今世紀最高の受発注管理システムとなります。
ユーザー登録
受発注業務の効率化だけでなく、システムを導入することで、コスト削減や製品・資材のステータス可視化のほか、属人化していた受発注情報の共有化による内部不正防止や統制にも役立ちます。
NEWJI DX
製造業に特化したデジタルトランスフォーメーション(DX)の実現を目指す請負開発型のコンサルティングサービスです。AI、iPaaS、および先端の技術を駆使して、製造プロセスの効率化、業務効率化、チームワーク強化、コスト削減、品質向上を実現します。このサービスは、製造業の課題を深く理解し、それに対する最適なデジタルソリューションを提供することで、企業が持続的な成長とイノベーションを達成できるようサポートします。
製造業ニュース解説
製造業、主に購買・調達部門にお勤めの方々に向けた情報を配信しております。
新任の方やベテランの方、管理職を対象とした幅広いコンテンツをご用意しております。
お問い合わせ
コストダウンが利益に直結する術だと理解していても、なかなか前に進めることができない状況。そんな時は、newjiのコストダウン自動化機能で大きく利益貢献しよう!
(β版非公開)