- お役立ち記事
- 無駄な動作を排除するための現場レイアウト最適化術
月間76,176名の
製造業ご担当者様が閲覧しています*
*2025年3月31日現在のGoogle Analyticsのデータより
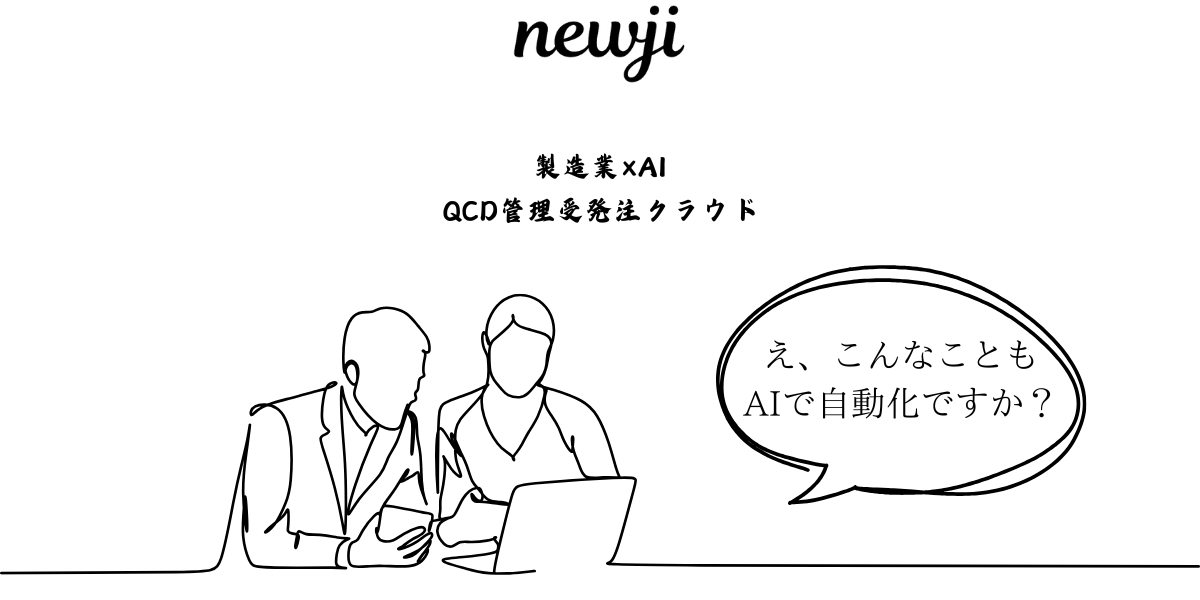
無駄な動作を排除するための現場レイアウト最適化術

目次
無駄な動作を排除するための現場レイアウト最適化術
製造現場において、生産効率を最大化するためには無駄な動作を排除することが不可欠です。
そのためには、現場レイアウトの最適化が鍵となります。
この記事では、現場目線で実践的な内容と最新の技術動向を交え、効果的な現場レイアウト最適化術を紹介します。
現場レイアウトの基本原則
現場レイアウトの最適化を始めるにあたり、以下の基本原則を押さえておくことが重要です。
1. 物流の最短化
物流の最短化は、生産効率を高めるための基本中の基本です。
材料、部品、製品が無駄なく最短距離で移動できるようにレイアウトを設計することが求められます。
そのためには、物流の流れを可視化し、ボトルネックを特定して改善することが重要です。
2. 作業エリアの統合
関連する作業エリアをまとめることで、作業者の移動距離を短縮し、無駄な動作を防ぐことができます。
例えば、組立作業と検査作業を隣接させることで、部品の移動時間を削減し、作業の効率を高めることができます。
3. フレキシビリティの確保
生産現場は常に変化するため、フレキシビリティを持たせたレイアウトが求められます。
移動式の道具や設備、柔軟に配置を変更できる作業台などを使用することで、迅速な対応が可能になります。
無駄な動作を排除する具体的な方法
次に、具体的な方法をいくつか紹介します。
これらの方法を実践することで、無駄な動作を効果的に排除し、生産効率を向上させることができます。
1. 作業標準の見直し
作業標準は、生産効率の向上に欠かせない要素です。
定期的に見直しを行い、無駄な動作や手順を洗い出して改善することが求められます。
作業者からのフィードバックを基に、実際の作業に即した標準を作成することが大切です。
2. 作業エリアの5S活動
5S活動(整理、整頓、清掃、清潔、しつけ)は、無駄な動作を排除するための基本的なアプローチです。
作業エリアを整理・整頓し、作業者が必要な道具や材料を無駄なく取り出せるようにすることで、生産効率を向上させることができます。
3. 自動化の導入
最新の技術動向を取り入れることで、無駄な動作をさらに排除することができます。
例えば、AGV(自律搬送車)やドローンを活用して材料の搬送を自動化することができます。
また、ロボットアームを導入し、反復作業を自動化することで、作業者の負担を軽減し、効率を高めることができます。
4. 作業者の動線設計
作業者の動線を最適化するためには、動線を分析し、効率的なルートを設計することが必要です。
例えば、ピッキング作業を行う際には、最短ルートで部品を取得できるように部品の配置を工夫することが効果的です。
5. カイゼン活動の推進
カイゼン活動は、無駄な動作を排除するための継続的な取り組みです。
現場の作業者からの提案を積極的に取り入れ、小さな改善を積み重ねることで、大きな効果を生むことができます。
定期的にミーティングを開催し、改善点を議論することで、全員がカイゼン意識を持つことが重要です。
最新技術を活用したレイアウト最適化
近年、製造現場においても最新技術の導入が進んでいます。
これらの技術を活用することで、無駄な動作を排除し、さらに効率的なレイアウトを実現することができます。
1. IoTの活用
IoT(Internet of Things)を活用することで、現場の状況をリアルタイムで把握し、データに基づいた改善が可能になります。
例えば、センサーを設置して作業者の動線をトラッキングし、無駄な動きが多いポイントを特定して改善することができます。
2. デジタルツインの導入
デジタルツインとは、現実の工場を仮想空間上に再現したモデルのことです。
これを活用することで、レイアウト変更のシミュレーションを行い、最適な配置を見つけることができます。
また、仮想空間上で実際の生産を再現し、無駄な動作を事前に検出することも可能です。
3. AIによる予測分析
AI(人工知能)を活用することで、データを元にした予測分析が可能になります。
例えば、過去の生産データを分析し、どの工程で無駄が発生しやすいかを予測することができます。
その結果を基に、事前に対策を講じることで、無駄な動作を未然に防ぐことができます。
事例紹介: 成功したレイアウト最適化の実例
最後に、成功したレイアウト最適化の具体的な事例を紹介します。
これらの事例を参考に、自社の現場にも適用できる改善策を見つけていただければと思います。
事例1: 部品供給エリアの改善
ある自動車部品メーカーでは、部品供給エリアのレイアウトを見直しました。
従来は部品が不規則に配置されていたため、ピッキング作業に多くの時間を要していました。
そこで、部品を使用頻度や重量に基づいて再配置し、短い動線で最適なピッキングルートを確保しました。
その結果、ピッキング作業の効率が向上し、生産リードタイムが大幅に短縮されました。
事例2: AGV導入による自動化
ある電子機器メーカーでは、AGVを導入して材料搬送を自動化しました。
従来は作業者が手動で部品を運搬していたため、人手不足や作業効率の問題がありました。
AGV導入後、搬送業務が自動化されたことで、作業者は本来の業務に集中できるようになり、全体的な生産効率が向上しました。
事例3: デジタルツインを用いたシミュレーション
ある医療機器メーカーでは、新しい生産ラインの設計に際してデジタルツインを活用しました。
仮想空間上でレイアウト変更のシミュレーションを行うことで、最適な配置を見つけることができました。
また、事前に無駄が発生しそうなポイントを特定し、対策を講じることで、実際の稼働開始後もスムーズに生産を行うことができました。
製造現場における無駄な動作の排除は、生産効率の向上に直結します。
現場レイアウトの最適化を通じて、物流の最短化、作業エリアの統合、フレキシビリティの確保などを実践することが重要です。
また、最新技術の活用や具体的な事例から学び、自社の現場にも適用できる改善策を見つけることが大切です。
これにより、無駄な動作を排除し、競争力のある生産現場を実現することができるでしょう。
資料ダウンロード
QCD管理受発注クラウド「newji」は、受発注部門で必要なQCD管理全てを備えた、現場特化型兼クラウド型の今世紀最高の受発注管理システムとなります。
ユーザー登録
受発注業務の効率化だけでなく、システムを導入することで、コスト削減や製品・資材のステータス可視化のほか、属人化していた受発注情報の共有化による内部不正防止や統制にも役立ちます。
NEWJI DX
製造業に特化したデジタルトランスフォーメーション(DX)の実現を目指す請負開発型のコンサルティングサービスです。AI、iPaaS、および先端の技術を駆使して、製造プロセスの効率化、業務効率化、チームワーク強化、コスト削減、品質向上を実現します。このサービスは、製造業の課題を深く理解し、それに対する最適なデジタルソリューションを提供することで、企業が持続的な成長とイノベーションを達成できるようサポートします。
製造業ニュース解説
製造業、主に購買・調達部門にお勤めの方々に向けた情報を配信しております。
新任の方やベテランの方、管理職を対象とした幅広いコンテンツをご用意しております。
お問い合わせ
コストダウンが利益に直結する術だと理解していても、なかなか前に進めることができない状況。そんな時は、newjiのコストダウン自動化機能で大きく利益貢献しよう!
(β版非公開)