- お役立ち記事
- QC7つ道具を活用した製造業の調達購買改革: 効率化と品質向上のための実践ガイド
QC7つ道具を活用した製造業の調達購買改革: 効率化と品質向上のための実践ガイド
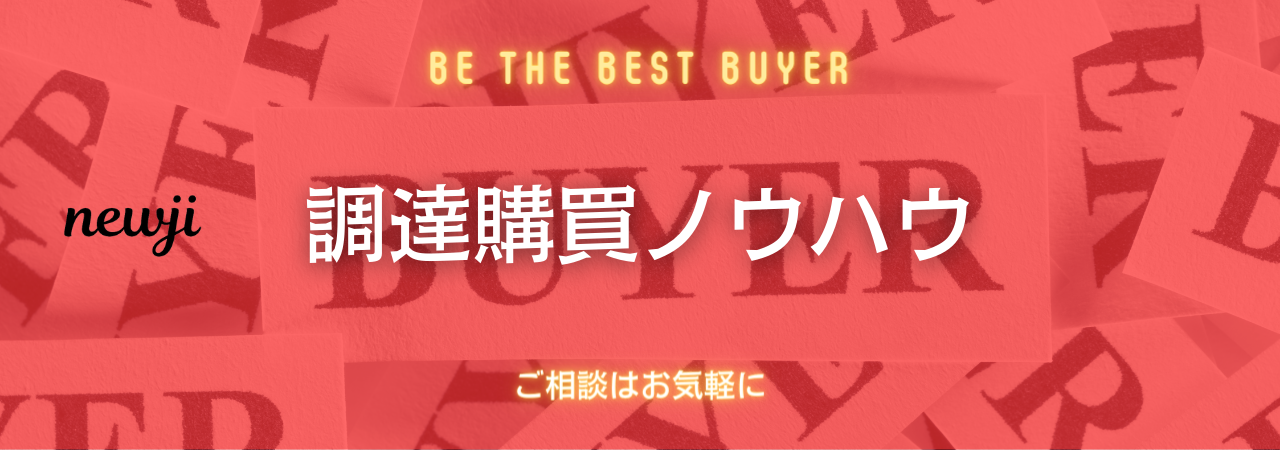
目次
はじめに
製造業において、調達購買部門はコスト管理や供給の安定性を確保するために非常に重要な役割を果たしています。
しかし、品質向上や効率化といった側面については、まだまだ改善の余地があることが多いです。
特にQC7つ道具を活用することで、これらの課題に対して体系立てたアプローチを取ることが可能となります。
本記事では、具体的な方法論や成功事例を交えながら、QC7つ道具を活用した調達購買改革の実践ガイドを提供します。
QC7つ道具とは
QC7つ道具は、品質管理における基本的な手法を指します。
これらの手法は、データを体系的に収集し、分析し、問題を特定するために使用されます。
具体的には以下の7つのツールがあります。
1. パレート図
パレート図は、問題を優先順位順に整列させるためのツールです。
80/20の法則に基づき、全体の80%の問題が20%の根本原因に起因することを示します。
2. ヒストグラム
ヒストグラムは、データの分布を視覚化するためのツールです。
データのばらつきや偏りを確認し、異常値の原因を特定するのに役立ちます。
3. 管理図
管理図は、プロセスが規定範囲内で安定しているかを監視するためのツールです。
特に品質の変動をリアルタイムで把握することで、問題の早期発見が可能となります。
4. 特性要因図(魚の骨図)
特性要因図は、問題の根本原因を体系的に分析するためのツールです。
複雑な問題を可視化し、原因を分類することで、効果的な対策を講じることができます。
5. チェックシート
チェックシートは、データ収集を簡素化するためのツールです。
記録されたデータを分析することで、頻発する問題や傾向を明確にすることができます。
6. 散布図
散布図は、二つの変数間の関係性を視覚化するためのツールです。
相関関係を確認し、原因と結果を特定するのに役立ちます。
7. 層別
層別は、データを異なるカテゴリに分けることで、問題の特定と解決を図るためのツールです。
たとえば、製品のロットや製造ラインごとにデータを分けて分析することで、特定のラインにのみ発生する問題を抽出できます。
QC7つ道具を活用した調達購買改革のステップ
これからは、QC7つ道具をどのように調達購買の現場で活用して効率化と品質向上を実現するか、その具体的なステップを解説します。
1. 問題の特定と優先順位付け (パレート図)
調達購買の問題は多数ありますが、すべてを一度に解決するのは現実的ではありません。
まずはパレート図を使って、最も影響が大きい問題を特定し、優先順位を付けます。
たとえば、サプライヤーからの納期遅延が生産計画に直結する場合、その問題を最優先課題として取り組むべきです。
2. データの収集と分布の確認 (ヒストグラム)
次に、優先度が高い問題に対してデータを収集し、ヒストグラムを作成します。
これにより、納期遅延の頻度や発生状況を視覚化できます。
データの分布を確認することで、異常値やパターンを特定できます。
3. プロセスの安定性チェック (管理図)
集めたデータを基に、管理図を作成してプロセスの安定性を監視します。
たとえば、特定の月に納期遅延が集中している場合、その月の特性を詳しく調査します。
これにより、プロセスにどんな変動があるのかを把握します。
4. 根本原因の分析 (特性要因図)
特性要因図を用いて、納期遅延の根本原因を詳細に分析します。
サプライヤーの生産能力や物流問題、内部の発注ミスなど、考えられる要因をすべて洗い出し、分類します。
これにより、問題の構造が見えてきます。
5. データ収集の効率化 (チェックシート)
特性要因図で明らかにした要因に基づき、今後のデータ収集を効率化するためにチェックシートを導入します。
たとえば、毎回の納品時にサプライヤーの出荷時間や輸送ルートを記録します。
このチェックシートを定期的に見直し、必要なデータが漏れなく収集されるように管理します。
6. 関係性の検証 (散布図)
収集したデータを散布図にして、納期遅延とその他の変数(たとえば、天候や交通状況)との関係を確認します。
これにより、納期遅延が単純なミスなのか、それとも他の外部要因により発生しているのかを特定できます。
7. データの層別化 (層別)
最後に、収集したデータを層別し、異なる要因ごとに問題を分析します。
たとえば、新規サプライヤーと既存サプライヤーで納期遅延の発生率を比較し、どちらに多く問題が発生しているかを明確にします。
このステップを踏むことで、より具体的な解決策を講じることができます。
成功事例:サプライヤー管理の改善
ある製造業の調達購買部門では、QC7つ道具を用いて以下のような成功事例がありました。
問題の特定と優先順位付け
パレート図を用いて、最も頻発するサプライヤーの納期遅延が全体の問題の80%を占めていることを特定。
データの収集と分布の確認
ヒストグラムを作成し、納期遅延が特定のサプライヤーに集中していることを可視化。
プロセスの安定性チェック
管理図で、特定期間に遅延が増加する傾向を確認し、この期間の特性を調査。
根本原因の分析
特性要因図を使って、サプライヤーの生産能力不足、物流の混乱、内部発注ミスといった複数の要因を特定。
データ収集の効率化
チェックシートを導入し、毎回の納品時に詳細なデータを収集。
関係性の検証
散布図により、納期遅延とサプライヤーの生産スケジュールの関連を確認。
データの層別化
層別によって、新規サプライヤーに多くの問題が集中していることを明確にし、改善プログラムを導入。
この一連のプロセスを通じて、納期遅延の問題が大幅に削減され、サプライヤー管理の改善が実現しました。
QC7つ道具を用いた調達購買改革のメリットとデメリット
メリット
– 問題の可視化が容易
– データに基づく意思決定が可能
– 改善活動の効果を測定しやすい
– チーム全体での共有とコミュニケーションが円滑に進む
デメリット
– 初期導入の手間とコストがかかる
– データ収集と分析に時間がかかることがある
– 全ての問題がQC7つ道具だけで解決できるとは限らない
– スキルと知識が必要であり、教育が必要
まとめ
QC7つ道具は、製造業の調達購買部門において効率化と品質向上を実現するための強力なツールです。
正確なデータに基づき、体系的に問題を特定し、分析し、解決策を講じることで、調達購買の課題を効果的に解決できます。
本記事で紹介した手法と成功事例を参考に、ぜひ自社の改善活動に取り入れてみてください。
資料ダウンロード
QCD調達購買管理クラウド「newji」は、調達購買部門で必要なQCD管理全てを備えた、現場特化型兼クラウド型の今世紀最高の購買管理システムとなります。
ユーザー登録
調達購買業務の効率化だけでなく、システムを導入することで、コスト削減や製品・資材のステータス可視化のほか、属人化していた購買情報の共有化による内部不正防止や統制にも役立ちます。
NEWJI DX
製造業に特化したデジタルトランスフォーメーション(DX)の実現を目指す請負開発型のコンサルティングサービスです。AI、iPaaS、および先端の技術を駆使して、製造プロセスの効率化、業務効率化、チームワーク強化、コスト削減、品質向上を実現します。このサービスは、製造業の課題を深く理解し、それに対する最適なデジタルソリューションを提供することで、企業が持続的な成長とイノベーションを達成できるようサポートします。
オンライン講座
製造業、主に購買・調達部門にお勤めの方々に向けた情報を配信しております。
新任の方やベテランの方、管理職を対象とした幅広いコンテンツをご用意しております。
お問い合わせ
コストダウンが利益に直結する術だと理解していても、なかなか前に進めることができない状況。そんな時は、newjiのコストダウン自動化機能で大きく利益貢献しよう!
(Β版非公開)