- お役立ち記事
- 品質管理部門に不可欠なAPQPプロセスの実践的ガイドライン
月間77,185名の
製造業ご担当者様が閲覧しています*
*2025年2月28日現在のGoogle Analyticsのデータより
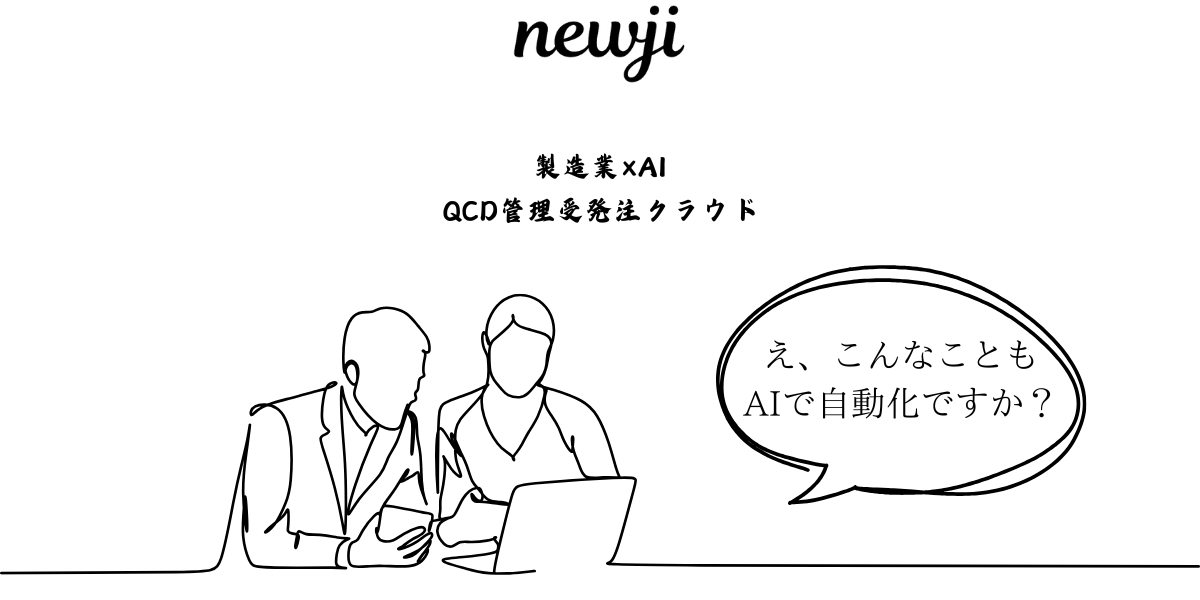
品質管理部門に不可欠なAPQPプロセスの実践的ガイドライン
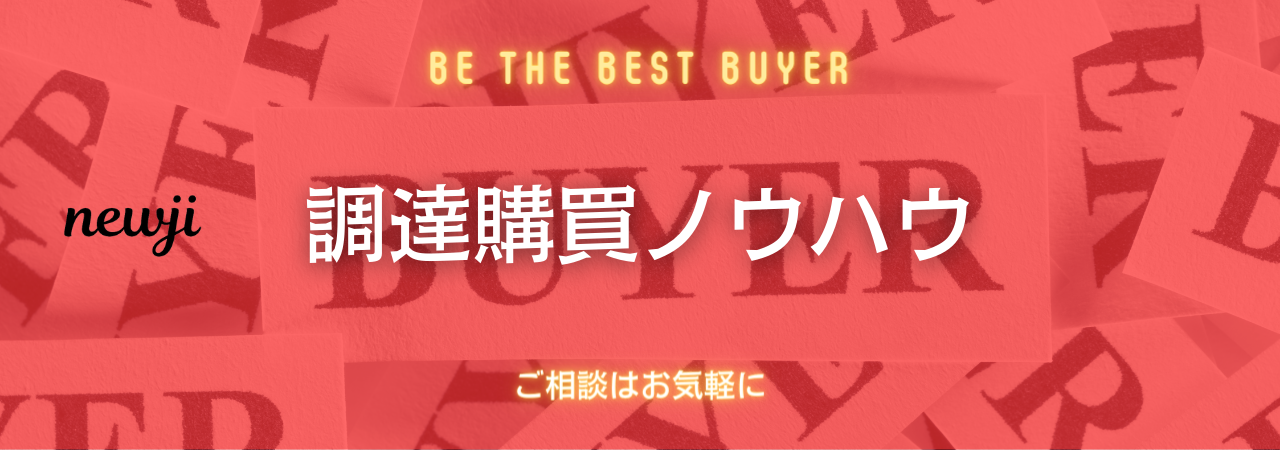
目次
品質管理部門におけるAPQPプロセスの重要性
製造業において品質管理は顧客満足を達成し、競争力を維持するための重要な要素です。
その中でもAPQP(Advanced Product Quality Planning)は、品質を保証するための計画的かつ体系的なアプローチを提供します。
このプロセスは製品の設計から市場投入までの過程で品質を保証するための枠組みであり、特に自動車業界で広く採用されています。
APQPの目的は製品設計、製造プロセスの一貫性を確保し、顧客の要求を満たす製品を提供することです。
また、潜在的な問題を事前に発見し、修正を行うことで、製品の市場投入までの時間を短縮し、コストを削減することも目的としています。
APQPプロセスの主要ステージ
APQPプロセスは大きく分けて5つのステージに分類されます。
これらのステージは、計画および定義、製品設計および開発プロセス、プロセス設計および開発、製品およびプロセスの検証、フィードバック、評価と相互修正、に分かれます。
計画および定義
この段階では製品やプロジェクトの要求事項を定義し、その目標を明確に設定します。
顧客のニーズの理解が最優先課題で、これに基づいて品質目標や仕様が策定されます。
また、製品のライフサイクル全体を見据えたリスク評価も行われます。
市場調査や競合分析も含まれ、製品の基本的な枠組みを決定する重要なフェーズです。
製品設計および開発プロセス
ここでは具体的な製品設計が行われます。
設計仕様書が作成され、それに基づいて設計プロトタイプやサンプルが作られます。
設計の各段階でレビューやテストを行い、設計が要求を満たしているかを確認します。
ここで注意が必要なのは、DFMEA(Design Failure Mode and Effects Analysis)などを活用することによって欠陥予測を行えるところです。
問題があれば早期に対応策を講じることが求められます。
プロセス設計および開発
製造プロセスの設計に重点を置くステージです。
工程図や制御計画を作成し、新たなプロセスを立ち上げるための具体的な手段を固めます。
製造能力、資材の管理、設備の要件、流通の効率化など、包括的なプロセス全体の設計とその実行が求められます。
PFMEA(Process Failure Mode and Effects Analysis)の適用により、製造過程における欠陥リスクを評価し、リスク軽減策を講じます。
製品およびプロセスの検証
設計とプロセスが計画通りに機能するかを検証するフェーズです。
試作やパイロット的に製造を行い、実際の製品が仕様を満たすか、プロセスが意図した性能を発揮するかを確認します。
この段階では、各種テストや評価を行い、問題がないかを徹底的に洗い出します。
PPAP(Production Part Approval Process)を通じて、顧客への納品許可を得られるよう準備を行います。
フィードバック、評価と相互修正
APQPプロセスの最後の段階は、得られたフィードバックを基に、製品やプロセスの評価を行い、必要に応じて改善を実施します。
製品がリリースされた後も、顧客のフィードバックを活用し、継続的な改善を推進します。
これにより、顧客満足度を向上させ、次の製品開発プロジェクトにも反映させることが可能です。
最新の業界動向とAPQPプロセスの変革
製造業におけるデジタルトランスフォーメーションは、APQPプロセスの効率化と精度向上に寄与しています。
例えば、IoTデバイスやビッグデータ分析技術の進展により、リアルタイムのデータ取得と分析が可能になっています。
これにより、潜在的な問題を早期に発見し、迅速な対応が可能となっています。
また、シミュレーション技術の進化により、製品設計段階からバーチャルプロトタイプを使用して検証を行うことができるようになりました。
これにより、物理的な試作品を作成する前にデザインのフィードバックを得て、設計の最適化を進めることが可能です。
人工知能や機械学習技術の活用も注目されています。
これにより、プロセスの自動化やメンテナンスの予測を実現し、製品の信頼性向上と製造コストの削減にも寄与しています。
APQPプロセスを成功に導くためのポイント
APQPプロセスを成功させるためには、いくつかのポイントを押さえておくことが重要です。
まず、全体の見通しを持ち、製品ライフサイクルの各ステージで必要なリソースを適切に管理します。
また、チームメンバー間での十分なコミュニケーションと調整が重要です、これにより、設計変更やリスク評価に対処するのが容易になります。
次に、顧客との綿密なコミュニケーションを維持し、要件変更や新たなニーズへの迅速な対応をすることが求められます。
ここでのポイントは、顧客のフィードバックを活用し、製品やプロセスの改善に反映させることです。
さらに、継続的な教育とトレーニングを通じて、従業員のスキルアップを図ることも重要です。
技術革新や新しいツールの導入に対して柔軟に対応できる体制を整えましょう。
まとめ
APQPプロセスは製品の品質を計画的に保証するための強力なフレームワークです。
各ステージでの詳細な作業と顧客の期待に応えることを目的としており、適切な実施により市場での成功が可能となります。
最新技術の活用にも注意を払い、変化する業界動向に適応する姿勢を持つことが大切です。
製造業界の発展に寄与し、顧客満足度を向上させるために、APQPプロセスの理解と活用を進めていきましょう。
資料ダウンロード
QCD管理受発注クラウド「newji」は、受発注部門で必要なQCD管理全てを備えた、現場特化型兼クラウド型の今世紀最高の受発注管理システムとなります。
ユーザー登録
受発注業務の効率化だけでなく、システムを導入することで、コスト削減や製品・資材のステータス可視化のほか、属人化していた受発注情報の共有化による内部不正防止や統制にも役立ちます。
NEWJI DX
製造業に特化したデジタルトランスフォーメーション(DX)の実現を目指す請負開発型のコンサルティングサービスです。AI、iPaaS、および先端の技術を駆使して、製造プロセスの効率化、業務効率化、チームワーク強化、コスト削減、品質向上を実現します。このサービスは、製造業の課題を深く理解し、それに対する最適なデジタルソリューションを提供することで、企業が持続的な成長とイノベーションを達成できるようサポートします。
製造業ニュース解説
製造業、主に購買・調達部門にお勤めの方々に向けた情報を配信しております。
新任の方やベテランの方、管理職を対象とした幅広いコンテンツをご用意しております。
お問い合わせ
コストダウンが利益に直結する術だと理解していても、なかなか前に進めることができない状況。そんな時は、newjiのコストダウン自動化機能で大きく利益貢献しよう!
(β版非公開)