- お役立ち記事
- システム設計の実践・例とそのポイント
システム設計の実践・例とそのポイント
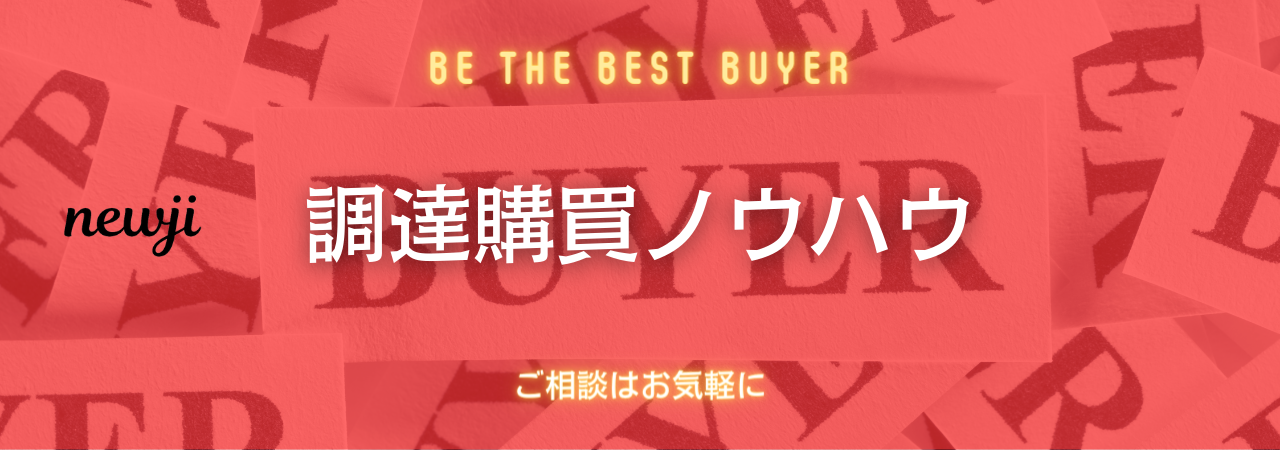
目次
はじめに
システム設計は、製造業において効率的な生産ラインを構築し、品質向上とコスト削減を実現する重要な要素です。
過去の成功体験に囚われず、ラテラルシンキングを活用して新たな発想を持ち込み、現代のニーズに応えるシステムを構築することが求められています。
この記事では、システム設計の実践的なアプローチや例を紹介し、その設計ポイントについても詳しく解説します。
システム設計の基本概念
システム設計には、製造現場の要件把握、システムの構造設計、機能設計、運用設計など多岐にわたるプロセスが含まれます。
まず、システム設計の目的を明確にし、経営戦略と整合させることが重要です。
要件定義
要件定義はシステム設計の最初のステップであり、関係者のニーズや目標を明確にするフェーズです。
製造業の現場では、品質向上や生産性の向上、コスト削減のために必要な要件を明確にしなければなりません。
現場の作業員やエンジニアの声をしっかりとヒアリングし、現実的な解決策を見つけることが求められます。
構造設計と機能設計
構造設計では、システムの全体像を把握し、どのようなシステムを構築するかを検討します。
製造ラインの自動化には、各ステージでの効率性と融通性を考慮に入れることが不可欠です。
機能設計では、具体的な機能を洗い出し、どのように実現するかを詳細に設計します。
例えば、リードタイム短縮を目指してデータフローを改善することが考えられます。
運用設計
運用設計は、システムが日常的にどのように使用されるかを決定するフェーズです。
特に製造業では、システムのダウンタイムを最小限に抑えるための保守管理やトレーニング計画を立てることが重要です。
また、変更管理手続きや障害対応プロセスも整える必要があります。
実践例:製造業におけるシステム設計
次に、具体的な製造業の現場におけるシステム設計の実践例を紹介します。
これらの事例を通じて、どのようにして問題を解決し、生産性を向上させたかを見てみましょう。
事例1:生産ラインの自動化
ある製造工場では、複数の人手作業を必要とする工程がボトルネックとなり、生産性向上の阻害要因となっていました。
この問題を解決するために、システム設計チームは自動化システムの導入を決定しました。
自動化の目的は、作業プロセスを標準化し、品質の一貫性を高めることでした。
自動化システムの設計においては、現場の設備レイアウトの再評価から始め、効率的なマテリアルフローを確立しました。
ロボティクスとコンベアシステムを組み合わせて、移動と加工の自動化を実現し、人的エラーを低減することに成功しました。
事例2:在庫管理システムの最適化
別の工場では、在庫管理の不備により、原材料の過剰在庫や欠品が頻発していました。
ここでは、精密なデータ分析に基づく在庫管理システムの設計が行われました。
システムはリアルタイムでの在庫状況をモニタリングし、需要予測アルゴリズムを組み合わせて、適正な在庫レベルを保持することを可能にしました。
このプロジェクトの成功の鍵は、製造工程と需要予測のデータを統合し、意思決定に役立てたことです。
これにより、コスト削減と生産効率の向上を同時に実現しました。
事例3:品質保証プロセスの強化
ある部品メーカーでは、品質不良品の発生率が高く、顧客クレームが増加していました。
システム設計の範囲では、品質管理プロセスの全面的な見直しが必要とされました。
統計的プロセスコントロール(SPC)を導入し、リアルタイムで品質データを収集・分析するシステムを構築しました。
新しいシステムは、現場作業員が素早く問題を発見し、是正措置を講じるためのツールを提供しました。
その結果、不良品の発生頻度が大幅に削減され、顧客満足度の向上につながりました。
システム設計の成功に向けたポイント
これらの事例から示唆されるように、システム設計の成功にはいくつかの重要なポイントがあります。
では、それらのポイントを具体的に見ていきましょう。
関係者の連携とコミュニケーション
システム設計は複数のステークホルダーを巻き込んだプロジェクトです。
現場の作業員、エンジニア、管理層との間で緊密なコミュニケーションを保ち、意見の収集と調整を行うことが重要です。
特に、設計の初期段階での関与によって、後々の問題を未然に防ぐことができます。
柔軟性と拡張性を考慮
システム設計には、将来の成長や環境の変化に対応できる柔軟性と拡張性が求められます。
これにより、新しい技術や市場のニーズに対して迅速に対応でき、生産システムとしての有効性を長期間維持することができます。
データ駆動型アプローチ
現代の製造業においては、データ駆動型アプローチが常識となっています。
システム設計には、積極的にデータ分析を組み込み、詳細なインサイトに基づいて意思決定を行うことが求められます。
データ駆動型の設計は、より高い精度と効率をもたらします。
継続的な改善と検証
システム設計がうまくいったからといって、そこで止まってしまってはいけません。
常に改善の機会を探り、運用段階での効果を検証し続けることが重要です。
PDCAサイクルを導入し、持続可能な改善活動を推進する文化を醸成することで、継続的な成功を収めることができます。
まとめ
システム設計は、製造業の未来を切り開くための重要なプロセスです。
現場の問題を的確に把握し、新たな視点で解決策を考えることで、業務の効率化と品質向上が可能になります。
この記事で紹介した実践例と設計のポイントを参考に、皆さんの現場でも革新的なシステム設計に取り組んでください。
製造業に携わる全ての方々にとって、システム設計の成功がさらなる成長と発展に繋がることを願っています。
資料ダウンロード
QCD調達購買管理クラウド「newji」は、調達購買部門で必要なQCD管理全てを備えた、現場特化型兼クラウド型の今世紀最高の購買管理システムとなります。
ユーザー登録
調達購買業務の効率化だけでなく、システムを導入することで、コスト削減や製品・資材のステータス可視化のほか、属人化していた購買情報の共有化による内部不正防止や統制にも役立ちます。
NEWJI DX
製造業に特化したデジタルトランスフォーメーション(DX)の実現を目指す請負開発型のコンサルティングサービスです。AI、iPaaS、および先端の技術を駆使して、製造プロセスの効率化、業務効率化、チームワーク強化、コスト削減、品質向上を実現します。このサービスは、製造業の課題を深く理解し、それに対する最適なデジタルソリューションを提供することで、企業が持続的な成長とイノベーションを達成できるようサポートします。
オンライン講座
製造業、主に購買・調達部門にお勤めの方々に向けた情報を配信しております。
新任の方やベテランの方、管理職を対象とした幅広いコンテンツをご用意しております。
お問い合わせ
コストダウンが利益に直結する術だと理解していても、なかなか前に進めることができない状況。そんな時は、newjiのコストダウン自動化機能で大きく利益貢献しよう!
(Β版非公開)