- お役立ち記事
- FMEA、DRBFMによる不具合発生防止
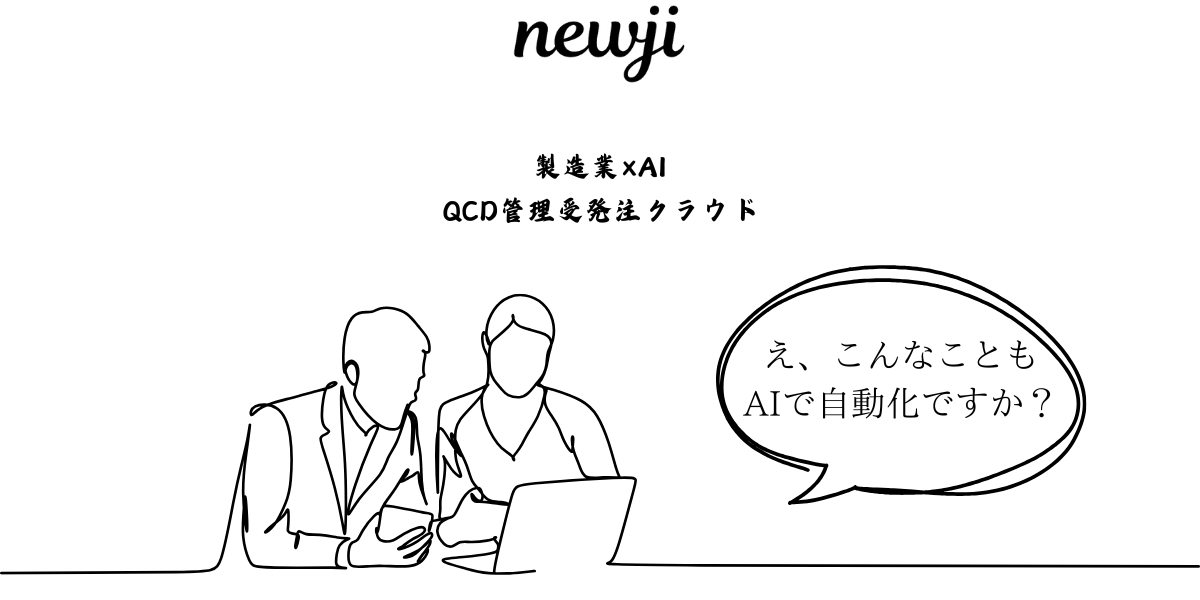
FMEA、DRBFMによる不具合発生防止
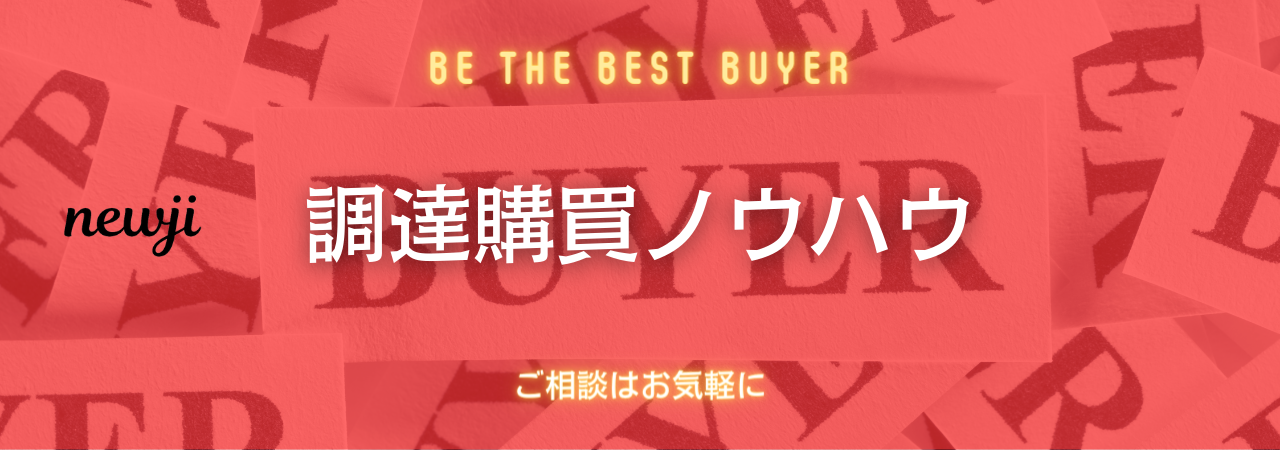
目次
FMEAとDRBFMとは何か?
FMEA(Failure Mode and Effects Analysis)は、日本語では「故障モード影響解析」と呼ばれ、不具合が発生する可能性のある箇所を事前に予測し、その影響を評価し、対策を講じるための手法です。
一方、DRBFM(Design Review Based on Failure Mode)はトヨタ自動車によって開発された手法で、設計変更や新しい製品の開発において、潜在的な不具合を特定し、失敗の可能性を最小限に抑えることを目的としています。
どちらの手法も製造業における品質保証の重要な要素であり、不具合の発生を未然に防ぐために広く実施されています。
FMEAとDRBFMの活用目的
FMEAの主な目的は、製品やプロセスの初期段階で潜在的な故障モードを特定し、その影響を評価することです。
これにより、設計や製造プロセスにおけるリスクを軽減し、製品の信頼性と安全性を向上させることが可能です。
FMEAは工程FMEA(Process FMEA)や設計FMEA(Design FMEA)など、様々なステージで適用できる柔軟性があります。
DRBFMは、特に設計変更が行われる際に、変更によって引き起こされる可能性がある問題を詳細に検討することを目的としています。
設計変更の影響を理解するために、「何が変わったのか、何が変わっていないのか」を議論し、新たに発生するリスクを徹底的に評価し対策を講じます。
FMEAの具体的なプロセス
FMEAの実施プロセスは次のようなステップで進めます。
1. システムの理解
最初に行うのは、製品やプロセスの全体像を把握することです。
製品の使用目的、顧客の要求、運用環境などを洗い出して、どのような機能を果たすべきなのかを明確にします。
2. 潜在的故障モードの洗い出し
各コンポーネントや工程において発生しうる故障モードをリストアップします。
過去のデータや専門家の知識を活用し、あらゆる可能性を考慮に入れます。
3. 故障モードの影響評価
故障モードが実際に発生した場合の影響を定量的かつ定性的に評価します。
これには影響の深刻さ(Severity)、発生頻度(Occurrence)、検出可能性(Detection)などを考慮に入れ、リスク優先度(RPN:Risk Priority Number)を算出します。
4. 改善策の検討と実施
RPNの高い故障モードに対して、優先的に改善策を立案し、実施します。
改善策が効果的であるかどうかを検証し、必要に応じてFMEAを更新します。
5. 結果の文書化とレビュー
FMEAの結果をしっかりと文書化し、関係者間で共有します。
定期的にレビューを行い、最新の状態を維持します。
DRBFMの具体的なプロセス
DRBFMもまた、設計変更を効果的に管理するための体系的なプロセスを持っています。
1. 想定される問題の確認
設計変更が既存の設計にどのように影響を及ぼす可能性があるかを確認します。
変更内容についての詳細なレビューを行い、新たなリスクを洗い出します。
2. 変更箇所の詳細な分析
設計変更の箇所について深く掘り下げ、特に注意が必要な部分を特定します。
これにより、改良する要素を明確にします。
3. チェックリストによる確認
DRBFM特有のチェックリストを利用し、変更箇所およびその影響を体系的に確認します。
チェックリストを用いることで、漏れのない評価を実施します。
4. 意見交換とアイデア出し
変更に関して関連部門と広く意見交換を行い、多角的な視点からアイデアを集めます。
多様な観点からのフィードバックを取り入れることで、より堅牢な対策を打ち出します。
5. 検証とフォローアップ
決定した対策の効果を検証し、必要に応じてさらなる改善を行います。
プロジェクトの進捗を追跡し、問題が発生した際には即座に対応します。
FMEAとDRBFMの違いと補完性
FMEAとDRBFMの違いは、その適用範囲とフォーカスする段階にあります。
FMEAは製品やプロセス全体の潜在的な問題を洗い出し、広範囲に渡ってリスクを管理する手法です。
一方で、DRBFMは設計変更に特化し、その影響を詳細に分析することで、変更による不具合を事前に防ぐ手法です。
両者は異なるフェーズを対象としますが、相互に補完し合う関係です。
FMEAで全体のリスクを管理し、DRBFMで設計変更時のリスクを確実に抑えることで、製品の品質と信頼性を高めることが可能になります。
なぜ不具合発生防止に重要なのか
どちらの手法も、製造業において不具合発生を最小限に抑えるために極めて重要です。
不具合が発生すると、製品の信頼性が損なわれるだけでなく、顧客の満足度の低下や企業の評判にも悪影響を及ぼします。
また、重大な故障が発生した場合には、リコールや修理費用の負担、さらには法的責任が生じる可能性もあります。
FMEAとDRBFMを効果的に活用することで、これらのリスクを事前に予測し、未然に防ぐことが可能になります。
これにより、製品の品質保証体制を強化し、顧客満足度の向上に寄与します。
まとめ
FMEAとDRBFMは製造業における不具合発生防止の鍵となる手法です。
それぞれの手法を理解し、適切に活用することで、製品の信頼性や安全性を高めることができます。
製造業の現場では、これらの手法を効果的に取り入れることで、品質保証体制を強化し、競争力を維持することが求められています。
技術の進化とともに手法そのものも進化しており、最新のトレンドやベストプラクティスを活用し、持続的な品質改善を追求することが、差別化の一因となるでしょう。
資料ダウンロード
QCD調達購買管理クラウド「newji」は、調達購買部門で必要なQCD管理全てを備えた、現場特化型兼クラウド型の今世紀最高の購買管理システムとなります。
ユーザー登録
調達購買業務の効率化だけでなく、システムを導入することで、コスト削減や製品・資材のステータス可視化のほか、属人化していた購買情報の共有化による内部不正防止や統制にも役立ちます。
NEWJI DX
製造業に特化したデジタルトランスフォーメーション(DX)の実現を目指す請負開発型のコンサルティングサービスです。AI、iPaaS、および先端の技術を駆使して、製造プロセスの効率化、業務効率化、チームワーク強化、コスト削減、品質向上を実現します。このサービスは、製造業の課題を深く理解し、それに対する最適なデジタルソリューションを提供することで、企業が持続的な成長とイノベーションを達成できるようサポートします。
オンライン講座
製造業、主に購買・調達部門にお勤めの方々に向けた情報を配信しております。
新任の方やベテランの方、管理職を対象とした幅広いコンテンツをご用意しております。
お問い合わせ
コストダウンが利益に直結する術だと理解していても、なかなか前に進めることができない状況。そんな時は、newjiのコストダウン自動化機能で大きく利益貢献しよう!
(Β版非公開)