- お役立ち記事
- 設計FMEAによる品質トラブル未然防止の実践
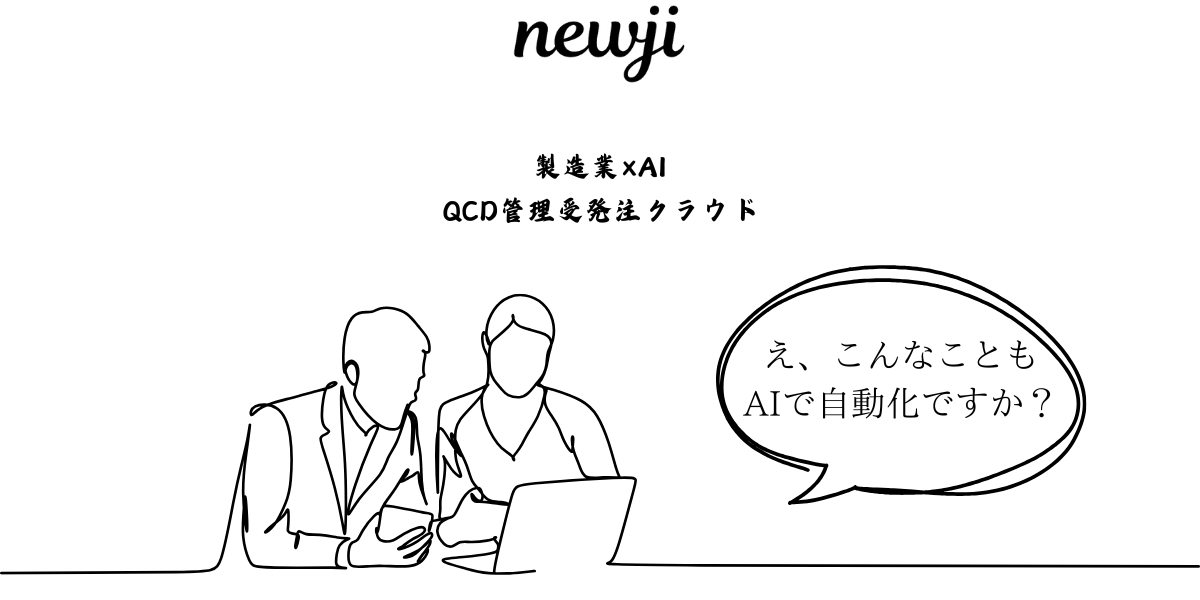
設計FMEAによる品質トラブル未然防止の実践
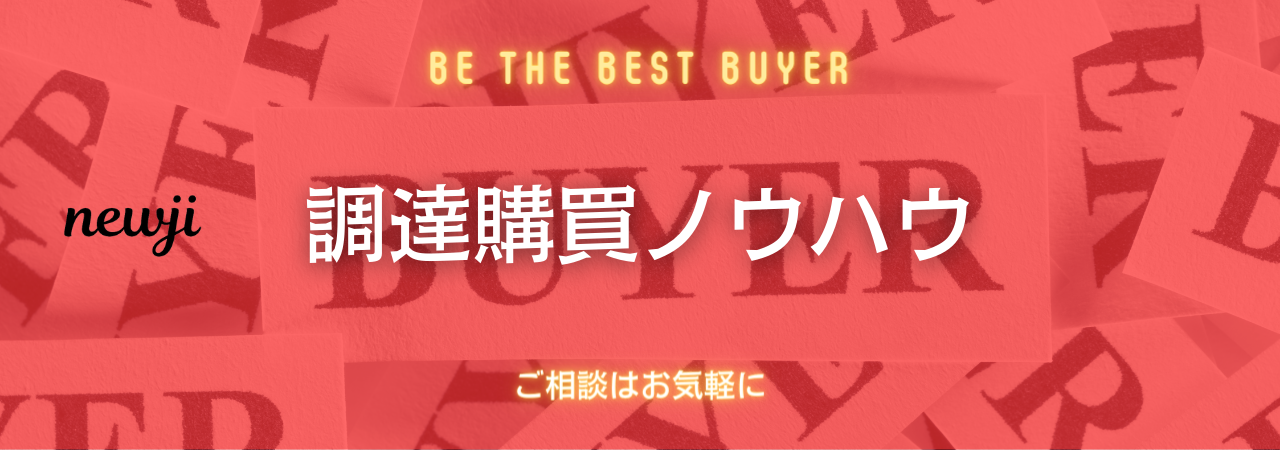
目次
設計FMEAとは?
設計FMEA(Failure Mode and Effects Analysis)は、製品設計の段階で潜在的な故障モードやその影響を特定し、評価し、防止・軽減策を講じるためのアプローチです。
これにより、設計段階での品質トラブルを未然に防ぐことができます。
FMEAは製造業の品質管理において重要な役割を果たし、その起源は航空宇宙産業にありますが、現在では自動車業界をはじめ、多くの分野で活用されています。
設計FMEAの目的
設計FMEAの主な目的は、製品設計の欠陥を早期に発見し、顧客の要求や期待に応じた品質を確保することです。
具体的には次のような目的があります。
潜在的欠陥の特定
設計段階で潜在的な欠陥を特定し、リスクを評価します。
この段階で問題を発見して対策を講じることで、後々の修正工数やコストを大幅に削減することができます。
リスクの軽減
特定されたリスクについて、予防措置や修正を講じることで、故障の発生を防ぎます。
これにより製品の信頼性向上を図ります。
設計の改善
FMEAの結果から得られた知見を活かし、設計の改善を進めます。
継続的な改善が行われることで、次回以降のプロジェクトにおいても効果的な設計が可能になります。
顧客満足度の向上
高品質で信頼性のある製品を提供することで、顧客満足度の向上につながります。
結果として、ブランド価値を高め、競争優位性を確保できます。
設計FMEAのプロセス
設計FMEAは標準化されたプロセスを持ち、多くの場合以下のステップで進行します。
1. システムを理解し、目的を設定
最初に、対象となるシステムや製品を理解し、FMEAの目的を明確にします。
具体的には、どの範囲を分析するのか、どのような品質目標を設定するのかを決定します。
2. 構造解析
対象システムの構造を詳細に解析し、その組み立て要素や機能を明確化します。
構造解析により、どの部分にリスクが潜む可能性があるのかを絞り込みます。
3. 機能解析
各要素の機能や、システム全体の動作を解析します。
これにより、製品が正常に動作するために必要な条件を把握します。
4. 故障モードの特定
各機能に対して、どのような故障モードが考えられるのかを特定します。
この段階で、過去の事例や統計データを活用し、多角的な視点でリスクを洗い出します。
5. 効果と原因の分析
特定した欠陥モードが実際に発生した場合、それがどのようにシステム全体に影響を与えるかを分析します。
また、その欠陥が発生する可能性のある原因も併せて考察します。
6. リスクの評価
欠陥の発生頻度、深刻度、検出可能性を評価し、優先順位をつけます。
この評価に基づいて、緊急度の高いものから対策を講じていきます。
7. 改善策の設定と実施
優先度の高いリスクに対して、具体的な改善策を設定し実施します。
改善策が実装された後は、その効果を検証し、必要であれば更なる改善を行います。
設計FMEAを活用した品質トラブル未然防止のポイント
設計FMEAを効果的に活用するためには、いくつかのポイントを押さえておく必要があります。
早期の段階で実施すること
設計FMEAは、できるだけ早い段階で始めることが重要です。
製品開発の初期段階であればあるほど、設計変更が容易で、コストも抑えることができます。
関連部門との連携
FMEAは設計部門だけでなく、生産管理、品質管理、調達部門など、関連する部門との連携が不可欠です。
多様な視点を取り入れることで、より網羅的にリスクを把握し、対策を講じることができます。
データの活用
過去の故障データや改善事例をしっかり活用することが求められます。
データに基づいた分析は、直感や経験に頼るよりも信頼性が高く、効果的なリスク軽減策につながります。
継続的な改善を意識すること
設計FMEAは一度実施して終わりではなく、継続的に見直し、改善を続けることがポイントです。
特に設計変更が加わる場合には、その都度FMEAを見直し、新しいリスクが発生していないかを確認します。
設計FMEAの現場での課題とその対処法
設計FMEAは有用なツールである一方、実施に際しては現場でいくつかの課題が生じることがあります。
ここでは一般的な課題とその対処法について解説します。
リソース不足
FMEAの実施には多くの時間と人材を要しますが、実際にはリソースが不足していることがあります。
対策としては、プロジェクトの初期段階でリソースを明確に計画し、必要に応じて外部パートナーや自動化ツールの活用を検討することです。
関係者の認識不足
特に新しいチームメンバーや他の部門の関係者が、FMEAの意義や方法を十分に理解していない場合があります。
定期的な研修やワークショップを通じて、FMEAの重要性と具体的な進め方を共有し、理解を深めることが重要です。
情報の共有不足
FMEAのプロセスは多くの情報を必要としますが、情報の一元管理ができていない場合、情報の断片化につながります。
対策としては、共有プラットフォームを活用した情報管理体制を整え、必要な情報を迅速にアクセスできるようにすることです。
結果のフォローアップ不足
FMEAの結果に基づく改善策が実施されない、または十分に効果が検証されないこともあります。
これを防ぐには、改善策の実施状況を定期的にフォローアップし、結果を評価するプロセスを確立することが必要です。
まとめ
設計FMEAは、製品開発プロセスにおける品質トラブルの未然防止に大きく寄与するツールです。
その目的、プロセス、活用法を理解し、現場での課題をクリアすることで、製品の信頼性向上と顧客満足度の向上を実現することが可能です。
製造業の発展において、FMEAを適切に活用することは、継続的な品質改善と製品の競争力強化に直結すると言えます。
技術革新が進む中でも、しっかりとした基礎を持ちながら、柔軟かつ迅速に対応できるFMEAを目指し、製品開発に活用していきましょう。
資料ダウンロード
QCD調達購買管理クラウド「newji」は、調達購買部門で必要なQCD管理全てを備えた、現場特化型兼クラウド型の今世紀最高の購買管理システムとなります。
ユーザー登録
調達購買業務の効率化だけでなく、システムを導入することで、コスト削減や製品・資材のステータス可視化のほか、属人化していた購買情報の共有化による内部不正防止や統制にも役立ちます。
NEWJI DX
製造業に特化したデジタルトランスフォーメーション(DX)の実現を目指す請負開発型のコンサルティングサービスです。AI、iPaaS、および先端の技術を駆使して、製造プロセスの効率化、業務効率化、チームワーク強化、コスト削減、品質向上を実現します。このサービスは、製造業の課題を深く理解し、それに対する最適なデジタルソリューションを提供することで、企業が持続的な成長とイノベーションを達成できるようサポートします。
オンライン講座
製造業、主に購買・調達部門にお勤めの方々に向けた情報を配信しております。
新任の方やベテランの方、管理職を対象とした幅広いコンテンツをご用意しております。
お問い合わせ
コストダウンが利益に直結する術だと理解していても、なかなか前に進めることができない状況。そんな時は、newjiのコストダウン自動化機能で大きく利益貢献しよう!
(Β版非公開)