- お役立ち記事
- 工程FMEAの手順
工程FMEAの手順
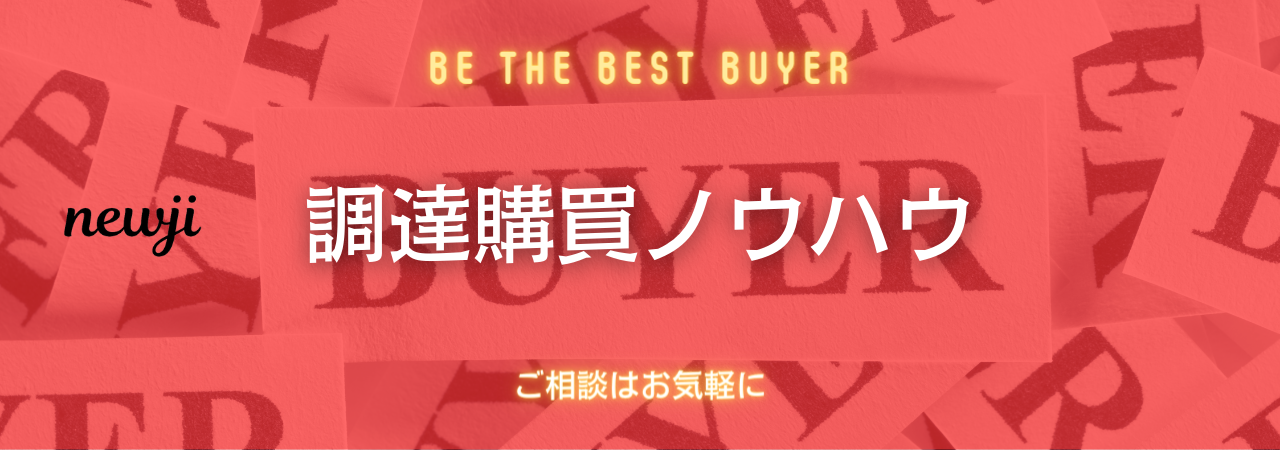
目次
工程FMEAの基本概要
工程FMEA(Failure Mode and Effects Analysis)は、製造工程における潜在的な欠陥モードを特定し、これらが製品やプロセスに及ぼす影響を評価する手法です。
これは品質改善のための重要なツールであり、問題発生を未然に防ぐためのプロアクティブなアプローチとして広く活用されています。
製造業において、工程FMEAは生産ラインの効率化や品質の向上に寄与し、結果として企業の競争力を高める役割を担います。
製品の製造工程で問題が発生した場合、その遡及的な対応には多大なコストと時間が掛かるため、工程FMEAを用いた予防策が重要です。
工程FMEAの実施ステップ
工程FMEAの実施にはいくつかのステップがあります。
これらのステップを順に踏むことで、体系的な欠陥モードの特定と改善策の策定が可能です。
1. プロセスの理解と範囲の定義
最初に行うべきは、対象とするプロセスの完全な理解と、FMEAの範囲を明確に定義することです。
これは、各工程がどのように機能し、どのように繋がっているかを理解するためです。
製造ライン全体を視野に入れ、どの部分に焦点を当てるかを決定します。
2. チームの編成
FMEAはチームアプローチの手法であり、多様な役割を持った専門家のチームで進めるのが有効です。
設計、製造、品質管理、保全などの異なる部門からメンバーを選出し、各視点からのインプットを引き出します。
3. 工程フロー図の作成
工程フロー図は、製品が製造される過程を視覚的に示すツールです。
この図を基に、各ステージにおける欠陥モードを特定します。
工程フロー図は、プロセスの流れを理解するための基盤となります。
4. 潜在的な欠陥モードの特定
全ての工程を順に辿り、どのような欠陥モードが考えられるかを洗い出します。
欠陥モードとは、製品やプロセスが正常に機能しない状態を指します。
各モードについて、どのような問題が発生し得るかを考えます。
5. 影響の評価
各欠陥モードが製品や消費者に与える影響を評価します。
また、影響の深刻度を数値で表すことにより、どの問題が優先的に対策を講じるべきかを判断します。
影響評価には、FMEAシートが使用されます。
6. 発生頻度と検出率の評価
次に、それぞれの欠陥モードの発生頻度と、現行のシステムでの検出率を評価します。
発生頻度は、その欠陥がどれくらいの頻度で起こる可能性があるかを示し、検出率は現実的にどれくらいの確率でそれを発見できるかを表します。
7. リスク優先度数(RPN)の計算
上記のステップで得られた影響、発生頻度、検出率の評価結果を元に、リスク優先度数(RPN: Risk Priority Number)を計算します。
RPNは、各欠陥モードの相対的なリスクを数値化し、優先順位付けに使用されます。
工程FMEAの管理と改善策の実施
工程FMEAの初期評価が完了したら、次に行うべきは管理と改善策の実施です。
ここで得られる情報は、具体的な行動計画として策定され、プロセスの改善に活用されます。
1. 改善策の策定
計算されたRPNに基づき、優先度の高い欠陥モードに対して適切な改善策を策定します。
これには、欠陥原因の除去、新しい検出手法の導入、発生頻度を低下させるための設計変更などが含まれます。
2. 改善策の実施とモニタリング
策定済みの改善策を現場で実行し、その効果をモニタリングします。
効果的なフィードバックメカニズムを組み込み、実施後の状況を継続的に評価します。
3. 再評価と更新
改善策の効果を評価後、必要に応じてFMEAをアップデートします。
製造プロセスや市場条件の変化に応じ、定期的な再評価を行うことが重要です。
工程FMEAの成功事例
製造業の現場では、工程FMEAの実施により多くの成功事例が生まれています。
1. 自動車部品メーカーの場合
ある自動車部品メーカーでは、工程FMEAを導入することで、製造工程での不良品発生率を30%削減しました。
特に、欠陥モードの早期発見と適切な品質管理手法の導入が成功要因として挙げられます。
2. 電機機器メーカーの場合
電機機器メーカーでは、エレクトロニクス製品の製造工程においてFMEAを活用し、不良率を大幅に低減。
RPN分析による改善策の優先づけを実施し、工程上でのトラブルを未然に防止することができました。
工程FMEAの導入に向けた課題
しかし、工程FMEAを成功裡に導入するためには、いくつかの課題を克服する必要があります。
1. 初期導入コスト
工程FMEAの導入には、プロセスの詳細な分析や専門知識が必要であり、初期コストがかかります。
これは、特に中小企業にとって大きな課題となることがあります。
2. チームワークの確保
効果的なFMEAを行うには、異なる部門からの協力が不可欠です。
しかし、部門間のコミュニケーション不足や連携不足が、工程FMEAの実施を妨げる要因となる場合があります。
3. 継続的な管理と改善
FMEAは静的な手法ではなく、動的に管理し続ける必要があります。
動的な市場環境や工場環境の変化に対応するために、継続的なデータ更新とレビューを行わなければなりません。
今後の展望
工程FMEAは、今後さらに重要性を増すでしょう。
特に、製造のデジタル化が進む現代において、FMEAのプロセスをデジタルツールと連携させることで、さらなる効率化が期待されます。
AIやIoT技術を組み合わせることで、FMEAの結果をより正確に、よりリアルタイムに反映し、問題発生前の予測能力を高めることができるでしょう。
工程FMEAはこれからも、品質向上とコスト削減の手段として進化し続けます。
資料ダウンロード
QCD調達購買管理クラウド「newji」は、調達購買部門で必要なQCD管理全てを備えた、現場特化型兼クラウド型の今世紀最高の購買管理システムとなります。
ユーザー登録
調達購買業務の効率化だけでなく、システムを導入することで、コスト削減や製品・資材のステータス可視化のほか、属人化していた購買情報の共有化による内部不正防止や統制にも役立ちます。
NEWJI DX
製造業に特化したデジタルトランスフォーメーション(DX)の実現を目指す請負開発型のコンサルティングサービスです。AI、iPaaS、および先端の技術を駆使して、製造プロセスの効率化、業務効率化、チームワーク強化、コスト削減、品質向上を実現します。このサービスは、製造業の課題を深く理解し、それに対する最適なデジタルソリューションを提供することで、企業が持続的な成長とイノベーションを達成できるようサポートします。
オンライン講座
製造業、主に購買・調達部門にお勤めの方々に向けた情報を配信しております。
新任の方やベテランの方、管理職を対象とした幅広いコンテンツをご用意しております。
お問い合わせ
コストダウンが利益に直結する術だと理解していても、なかなか前に進めることができない状況。そんな時は、newjiのコストダウン自動化機能で大きく利益貢献しよう!
(Β版非公開)