- お役立ち記事
- 試作工程での品質異常の迅速な原因究明手法
月間77,185名の
製造業ご担当者様が閲覧しています*
*2025年2月28日現在のGoogle Analyticsのデータより
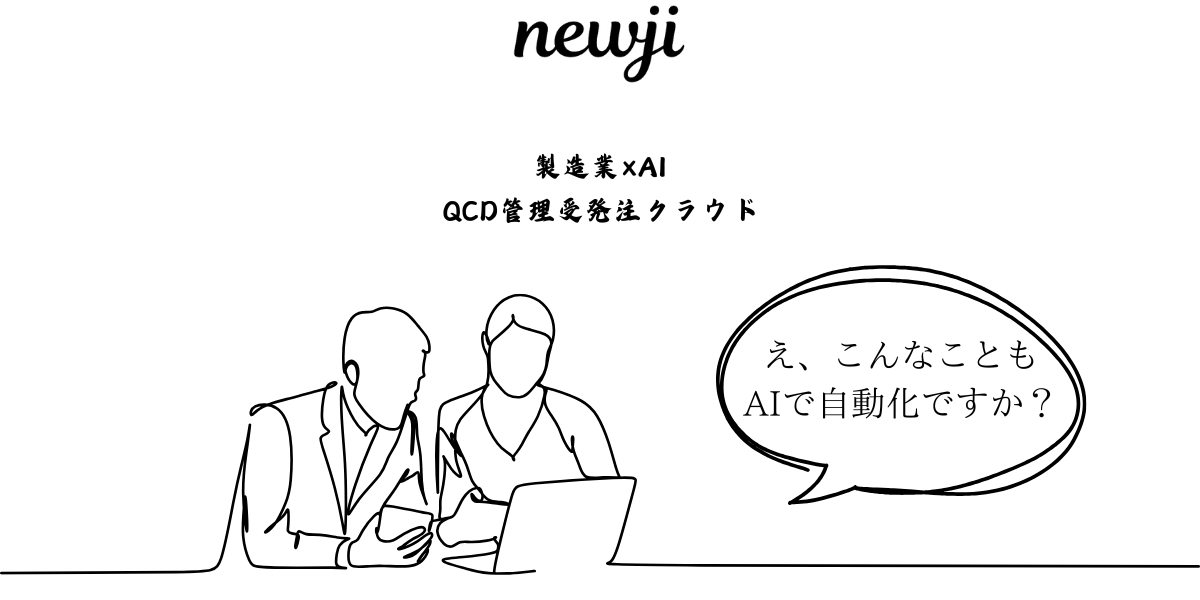
試作工程での品質異常の迅速な原因究明手法
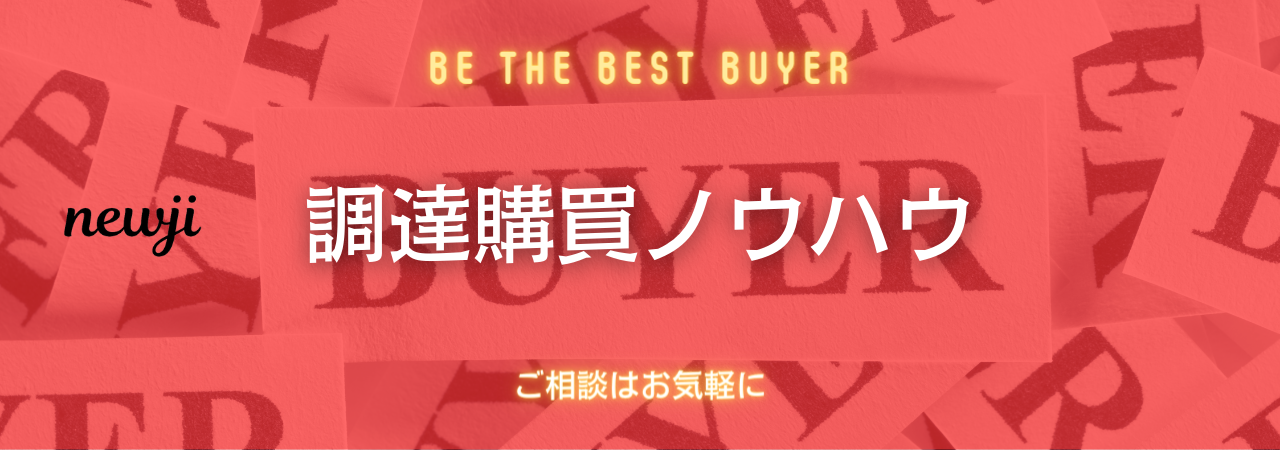
目次
はじめに
製造業では、製品の品質が最も重要な要素とされます。
試作工程での品質異常は、製品の市場投入を遅らせるだけでなく、企業の信頼を損ねるリスクもあります。
品質異常の迅速な原因究明は、製造ラインの効率を保ち、製品の信頼性を確保するために不可欠です。
本記事では、試作工程での品質異常を迅速に解決するための効果的な手法を紹介します。
品質異常の兆候を見逃さないために
製造業において、品質異常が発生する兆候を早期に見つけることが重要です。
品質異常の初期兆候を見逃さず、迅速に対応するためのポイントをいくつか挙げます。
データ収集と分析の重要性
データの収集と分析は、品質管理の中核を成します。
異常が発生する前に、製造プロセスの各段階で得られるデータを詳細に分析し、異常が進行していないかを監視します。
データが大規模であればあるほど、分析により異常の予兆を発見できる可能性が高まります。
現場目線での観察とフィードバック
現場作業員が異常を発見することは少なくありません。
彼らの経験や直感は、しばしば初期兆候の発見に役立ちます。
工場長や品質管理者は、現場の声をしっかりと拾い上げる環境を整え、報告された問題に迅速に対応することが求められます。
定期的な品質会議の実施
異常の早期発見を促進するために、定期的な品質会議を実施します。
この場で、各担当者が最新の状況を報告し、異常の兆候やそれに対する対策を共有することが重要です。
チーム全体で状況を把握し、迅速な対応につなげます。
品質異常が発生した際の迅速な対応
品質異常が発生した際の迅速な対応は、損失を最小限に抑えるために重要です。
異常が見つかった場合のステップを以下に示します。
異常発生の段階的切り分け
まずは、異常が発生しているプロセスを段階的に切り分けます。
どの工程で異常が発生したのか、どの部品が原因かを迅速に特定することが重要です。
このためには、製造工程を体系的に理解し、関与する要因を洗い出す能力が求められます。
原因追究の手法
原因追究には、いくつかの手法があります。
代表的なものとして、5W1H法やなぜなぜ分析があります。
5W1H法では、「いつ、どこで、誰が、何を、なぜ、どのように」と問いかけ、状況を詳細に分析します。
なぜなぜ分析では、問題の根本原因を明らかにするために5回以上「なぜ」を問うことを推奨します。
これらの手法を組み合わせて、より正確に問題の元を特定します。
仮説検証と効果測定
原因を特定したら仮説を立て、それに基づいた対策を実行します。
対策が有効であることを確認できるまで、効果の測定と改善を繰り返すことが必要です。
例えば、改善前後で製品の品質や生産効率のデータを比較し、対策へのフィードバックを入手します。
デジタルツールの活用
製造業がデジタル化する中で、デジタルツールは品質管理に大きな役割を果たします。
効率的で精度の高い原因究明が可能なデジタルツールの導入が進んでいます。
IoTとセンサーデータの活用
IoT技術の進歩により、センサーデータをリアルタイムに収集し分析することが可能になりました。
例えば、機械の稼働状況や温度、振動などのデータを監視し、異常を感知した際にアラートを出すシステムを導入します。
このようなリアルタイムのモニタリングにより、問題が発生する前に予防措置を取ることが可能となります。
AIによる予測分析
AIを活用した予測分析は、製造プロセスの異常検知に役立ちます。
AIは大量の過去データからパターンを学習し、異常が発生しそうな段階を自動で予測することができます。
これにより、事前にアクションを取ることができ、製品の品質を維持しつつコスト削減が可能になります。
クラウドシステムによる情報共有
クラウドシステムを利用することで、関係者全員が必要なタイミングで情報を共有する環境を整えます。
これにより、手作業やコミュニケーションの無駄を減らし、原因究明をより迅速に行うことができます。
デジタルツールは業務効率化だけでなく、異常発見までの時間を短縮し、迅速な対応を可能にします。
改善した事例から学ぶこと
現場の試行錯誤から学ぶことは多いです。
過去の実際のケーススタディから、どのようにして品質異常を解決したかを学びましょう。
中小企業A社の取り組み
中小企業A社では、製品の一部に頻繁に発生していた不良を、データ集計と現場の知見をもとに特定しました。
現場の作業者が立ち上げた改善提案がきっかけで、工程の相互チェック体制を強化することに成功しました。
これにより不良発生率が大幅に減少した事例です。
学びとして、従業員からのフィードバックとデータの両方を活用する重要性が挙げられます。
大手メーカーB社の改善プロジェクト
大手メーカーB社では、AIを利用した機械学習モデルを導入し、異常検知を自動化しました。
過去データを基に確率的な予測を行い、異常発生の予兆を捉えるシステムを構築しました。
結果として、工程の停止時間を削減し、製品回収コストを大幅に抑えることに成功しました。
このケースから、自動化と先進技術の導入による予防措置の有効性がわかります。
稼働中のプロジェクトで異常を防ぐためのポイント
品質異常を未然に防ぐ取り組みも重要です。
稼働中のプロジェクトで役立つ具体的なアプローチを紹介します。
標準化と柔軟なプロセス
各工程の作業を標準化し、異常を検知しやすくします。
加えて、柔軟なプロセス設計を行い、万が一異常が発見された場合でも迅速に対策を講じることができる体制を整えます。
トレーニングと教育の充実
従業員のスキルアップを図るため、定期的なトレーニングと教育を行います。
最新の技術や手法の習得を促進し、現場での問題解決能力を高めます。
知識と技術の普及により、異常を未然に防げる体制を築きます。
まとめ
試作工程での品質異常の迅速な原因究明は、製造業における競争力を維持するための重要な課題です。
データ分析や現場のフィードバック、デジタルツールの活用など、多面的なアプローチでしっかりと対策を講じましょう。
過去の成功事例や業界全体のベストプラクティスを参考にしながら、常に品質向上に向けた努力を怠らないことが重要です。
今後も継続的に改善し続け、製造業の発展に貢献しましょう。
資料ダウンロード
QCD管理受発注クラウド「newji」は、受発注部門で必要なQCD管理全てを備えた、現場特化型兼クラウド型の今世紀最高の受発注管理システムとなります。
ユーザー登録
受発注業務の効率化だけでなく、システムを導入することで、コスト削減や製品・資材のステータス可視化のほか、属人化していた受発注情報の共有化による内部不正防止や統制にも役立ちます。
NEWJI DX
製造業に特化したデジタルトランスフォーメーション(DX)の実現を目指す請負開発型のコンサルティングサービスです。AI、iPaaS、および先端の技術を駆使して、製造プロセスの効率化、業務効率化、チームワーク強化、コスト削減、品質向上を実現します。このサービスは、製造業の課題を深く理解し、それに対する最適なデジタルソリューションを提供することで、企業が持続的な成長とイノベーションを達成できるようサポートします。
製造業ニュース解説
製造業、主に購買・調達部門にお勤めの方々に向けた情報を配信しております。
新任の方やベテランの方、管理職を対象とした幅広いコンテンツをご用意しております。
お問い合わせ
コストダウンが利益に直結する術だと理解していても、なかなか前に進めることができない状況。そんな時は、newjiのコストダウン自動化機能で大きく利益貢献しよう!
(β版非公開)